ISO 25119 & Software Development for Functional Safety of Agricultural Machinery
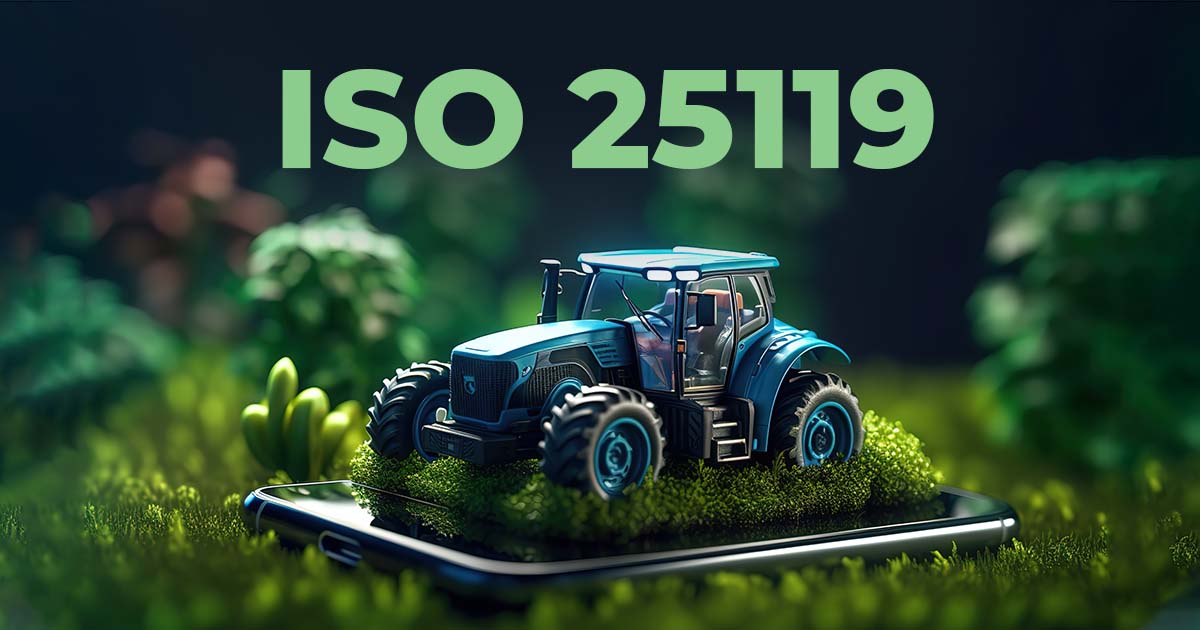
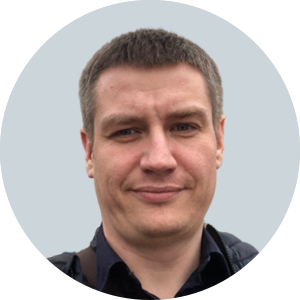
By Alexey Safonov
Head of the Automotive Unit at Promwad
The ISO 25119 standard regulates the development for agricultural transport as an industry-specific implementation of IEC 61508 for functional safety. Let's explore its key requirements and benefits backed by our experience in designing customer solutions for agriculture following ISO 25119 with AgPL b.
In the previous article about ISO 26262, we described the process of developing software for road vehicles. This time, we will focus on ISO 25119 for agricultural machinery. Both standards define the principles of functional safety to be followed in the design of electronic and electrical systems and components, software development, implementation and operation. They also both use the V-model in software development, demonstrating the important interplay between system requirements, system architecture, and the functional and technical safety concepts.
Adherence to ISO 25119 in the development of safety components and systems provides several benefits:
- reduced risks of harm to the environment and people during the operation of machinery;
- the ability to work with global manufacturers requiring compliance with international regulations;
- and reduced risk of product recalls due to functional safety issues.
AgPL: How Safety Levels Are Defined in ISO 25119
ISO 25119 specifies the evaluation of safety levels for electronic systems and components of agricultural machinery according to agricultural performance level (AgPL).
AgPL defines the ability of components to perform safety-related functions in critical situations. ISO 25119 defines five such levels: a, b, c, d, and e, where a is the lowest level of performance and e is the highest one.
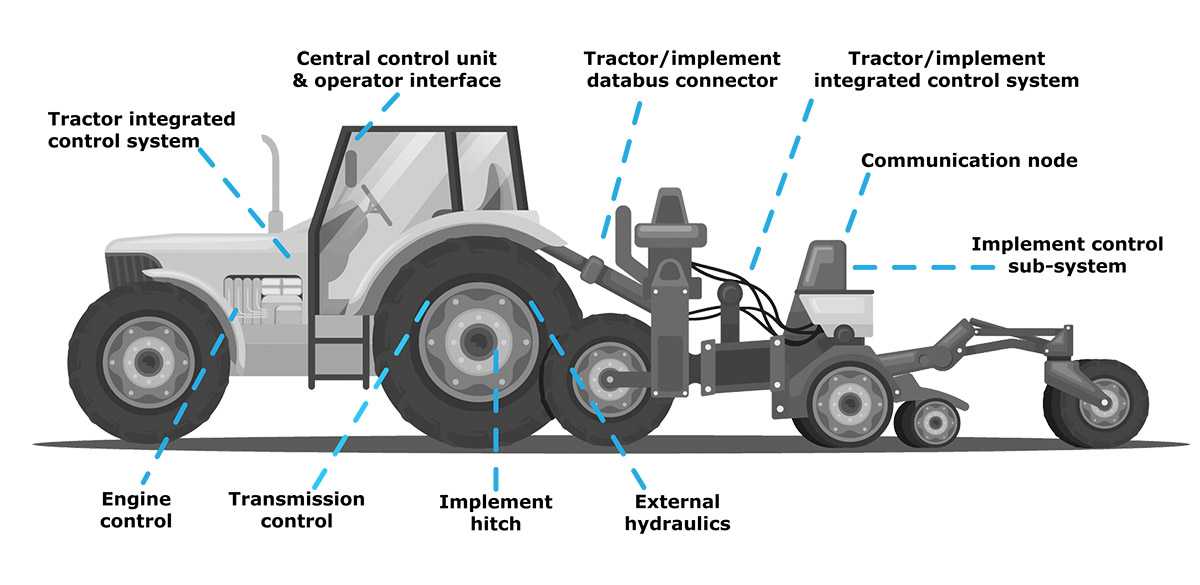
Systems of agricultural machinery that are designed in compliance with AgPL
ISO 25119 software development also uses four software requirement levels (SRL) — B, 1, 2 and 3. The higher the number, the more stringent the safety requirements. Here are examples of safety systems where all components must be designed according to AgPL:
- automatic steering and guidance systems based on sensors, GPS navigation for machinery control;
- collision avoidance systems for detecting obstacles, blind spots or people using radar and LiDAR;
- grain and fertiliser application systems based on sensors and mapping technology;
- implement control systems such as ploughs or seed drills.
Case Study: Integrated Control System Design
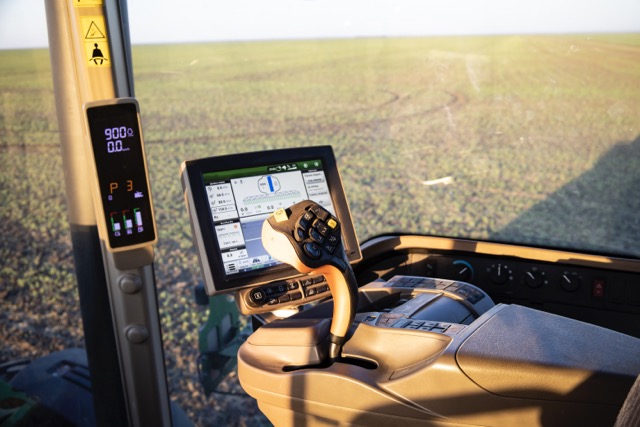
An example of an agricultural machinery cab with an automated control system
On behalf of our customer, a supplier of solutions for agricultural machinery, we developed an integrated control system for gear shifting, rear and front PTO drive, rear axle differential lock, and front drive axle drive. Besides, the system monitors and displays the status of various sensors on the front panel and controls its power circuits for short-circuit and no-load. We have also developed special software to fully monitor the system. Some of the features that our team has implemented:
- front power take-off shaft (PTO);
- rear power take-off shaft;
- gearbox;
- front axle drive;
- rear-axle differential lock.
***
Feel free to contact us if you need any engineering support to develop software or hardware for agricultural machinery that will comply with ISO 25119 and AgPL.