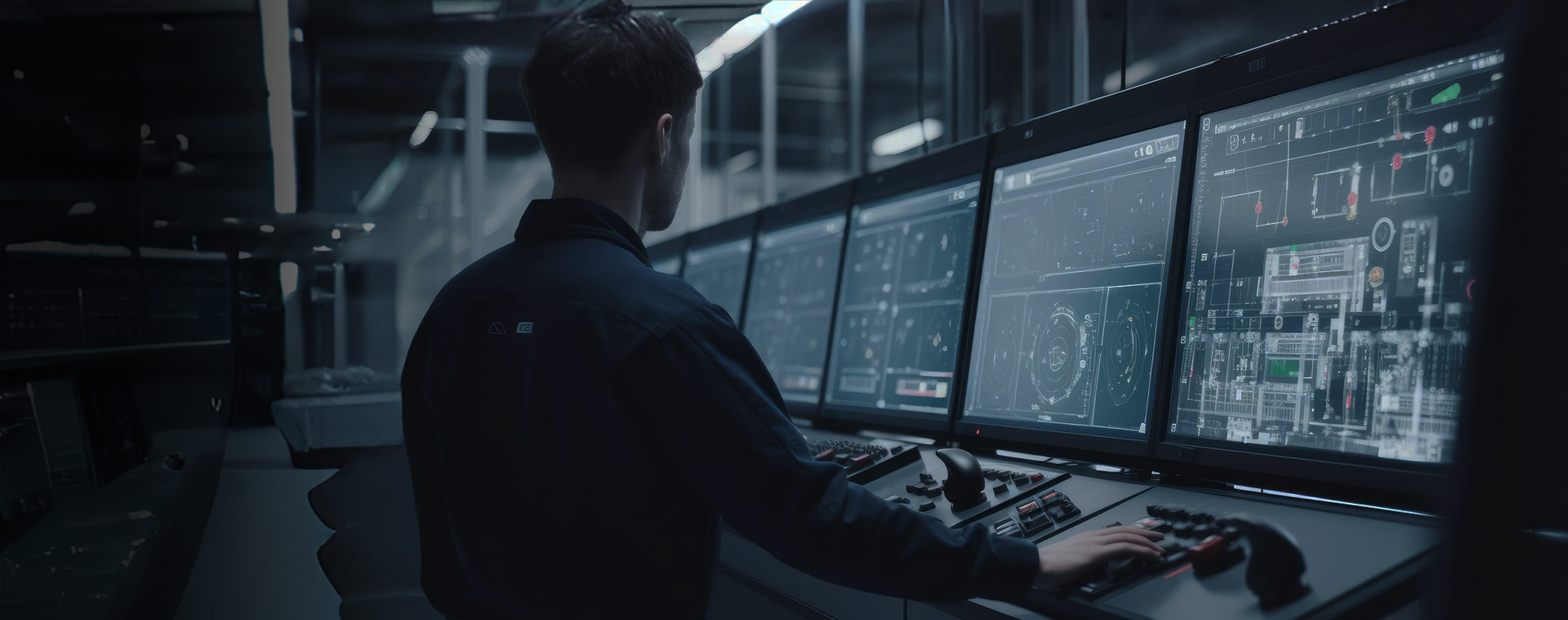
Predictive Maintenance Solutions
Predictive Maintenance Solutions for Industrial Automation
Discover a new level of resilience and productivity on your factory floor with our advanced predictive maintenance (PdM) solutions. Our engineering team revolutionises traditional maintenance practices by employing Edge AI and Industrial IoT to deliver unmatched performance.
We leverage industry-leading platforms such as NVIDIA Jetson and AI solutions from AMD (Xilinx), including Kria and Versal. Employing our services for your predictive maintenance solutions, you can stay ahead of potential machine failures, optimise your maintenance schedules, and obtain other benefits.
Explore the Benefits of Predictive Maintenance for Businesses
Recovered revenue |
Minimised downtime |
Longer equipment life |
Decreased risk exposure |
Enhanced production |
Cost-effective maintenance |
Use Cases of Predictive Maintenance
As a predictive maintenance company, we develop software that optimises equipment performance and reduces unexpected downtime in various industries.
Early detection of defective bearings
Early detection of anomalies in power generation turbines
Recognition of unbalanced fans
Notification of required bearing lubrication
Reporting of loose electrical connections
Alerting to contaminated or replacement-needed oil
Detection of abnormal vibration in manufacturing equipment
Identification of misalignment between rotating equipment
Detection of unusual heat or temperature patterns in power plants
Identification of brake system abnormalities in vehicles
Detection of abnormal sensor readings in medical devices
Industry 4.0 and Predictive Maintenance Software
Advanced analytics on machine data collected from end sensor nodes are at the core of our predictive maintenance software. Through this approach, we extract meaningful insights that accurately forecast machine failures.
Read more about our sensor development services →
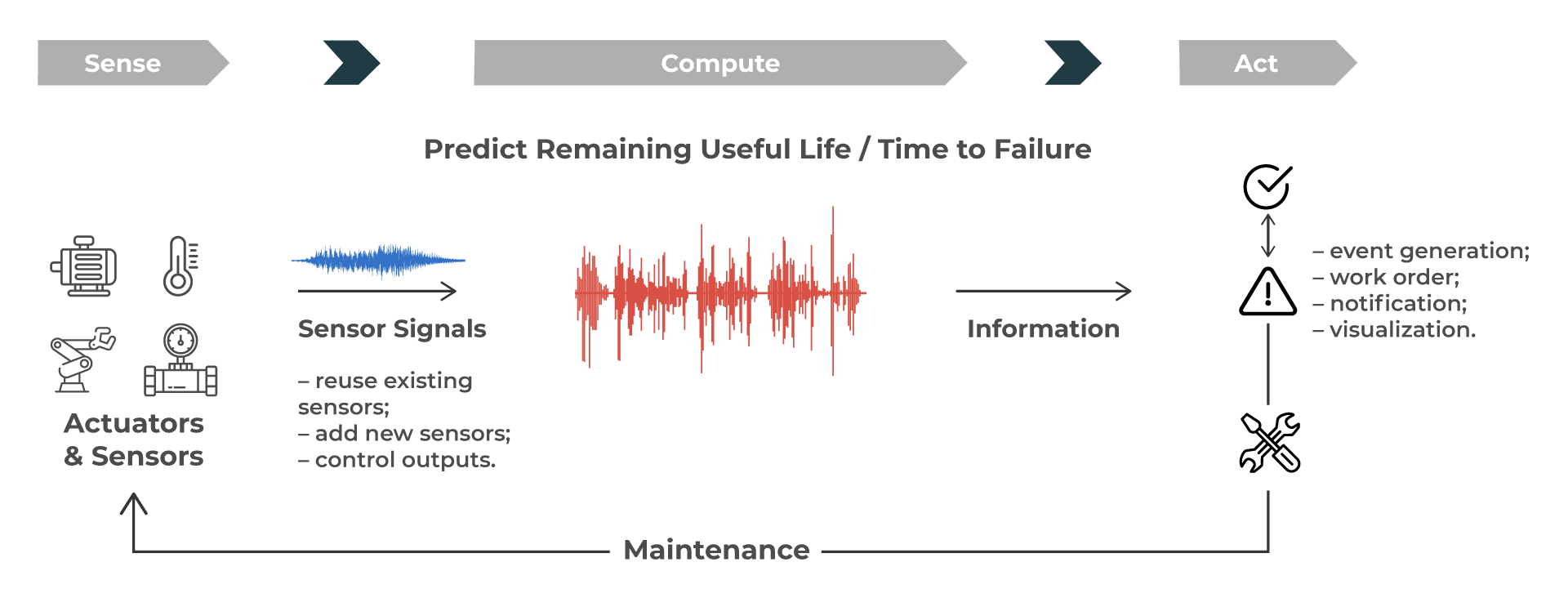
Predictive Maintenance Services We Provide
Our predictive maintenance services help our clients track their assets’ condition over time and identify trends that may indicate potential problems.
– Leverage cloud-based architectures and microservices to seamlessly integrate existing systems and databases and facilitate real-time data collection, analysis, and visualisation.
– Employ machine learning frameworks to ensure accurate anomaly detection and predictive modelling for proactive maintenance strategies.
AI Software Development
We develop advanced deep-learning models to analyse sensor data, detect patterns, and forecast equipment failures.
With natural language processing and computer vision expertise, we extract valuable insights from unstructured data sources, enhancing your maintenance systems' predictive capabilities.
We create software for embedded devices, integrating with real-time operating systems like FreeRTOS and QNX, enabling seamless integration with hardware components.
Our expertise in communication protocols, such as MQTT and OPC UA, ensures seamless connectivity and data exchange between devices and backend systems.
We utilise industry-standard tools and technologies to design circuit boards, sensor interfaces, and communication modules optimised for data acquisition and processing.
Within our services, we:
Select suitable sensors, microcontrollers, and communication protocols to ensure seamless integration with existing infrastructure.
Adhere to stringent quality standards and conduct thorough testing to deliver robust and reliable hardware components for predictive maintenance systems.
We implement high-performance and low-latency FPGA solutions to accelerate data processing and analysis, enabling real-time anomaly detection and efficient decision-making.
We leverage the latest tools and libraries: Xilinx Vivado | XGBoost | Apache Mahout | Spark Mlib | TheanoAccord.NETAForge.NET
We build robust firmware solutions that ensure seamless communication between hardware components, data acquisition, and analysis.
Our expertise includes low-level programming, device drivers, and firmware optimisation methods, enabling efficient operation and accurate data collection for predictive maintenance functionalities.
Our experts design hardware components and enclosures for predictive maintenance systems.
The enclosures we design can withstand harsh industrial environments thanks to their protection against dust, moisture, shock, and vibration according to IP65, IP67, IP68, and IP69K.
Our manufacturing capabilities include PCB fabrication, assembly, and quality testing, ensuring the efficient production of high-quality predictive maintenance devices.
We adhere to industry standards and regulations to deliver reliable hardware elements for your solutions.
Our Case Studies on Predictive Maintenance
How we used sensors, machine learning (ML), edge computing & cloud computing in our clients' projects.
Maximise the lifespan of industrial pumps
We built an IoT predictive maintenance solution that helps prevent costly breakdowns and downtime, increase efficiency, and extend the pump's lifespan.
It uses sensors to collect data on the pump's performance and machine learning algorithms to identify patterns and anomalies, enabling early detection of potential issues.
Technologies
Vendors: STMicroelectronics.
Programming languages: С/C++.
Industrial networks: IO-Link, OPC Ua.
SDK: AWS, CMSIS RTOS 2, FP-IND-PREDMNT1 (STM32Cube function pack for multi-sensors node with signal processing to enable predictive maintenance).
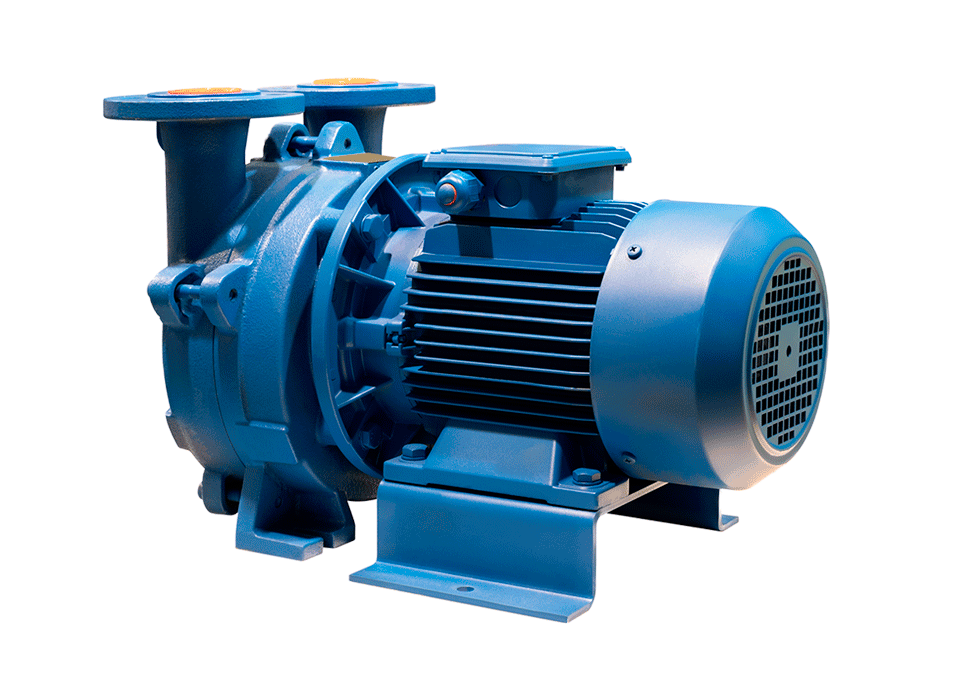
Keep elevators in optimal condition
Using sensors and machine learning algorithms, we have developed a solution that effectively prevents elevator breakdowns, reduces downtime, and enhances user safety.
Potential issues can be identified through real-time monitoring and predictive analytics, allowing for proactive maintenance scheduling and quick emergency response.
Technologies
Vendors: STMicroelectronics, NVIDIA
Programming languages: C, C++, Python.
Industrial networks: IO-Link, Modbus TCP, OPC UA, MQTT.
SDK: Qt, AWS, CMSIS RTOS 2, FP-IND-PREDMNT1, JetPack SDK (Jetson Linux, TensorRT, cuDNN, CUDA, Computer Vision).
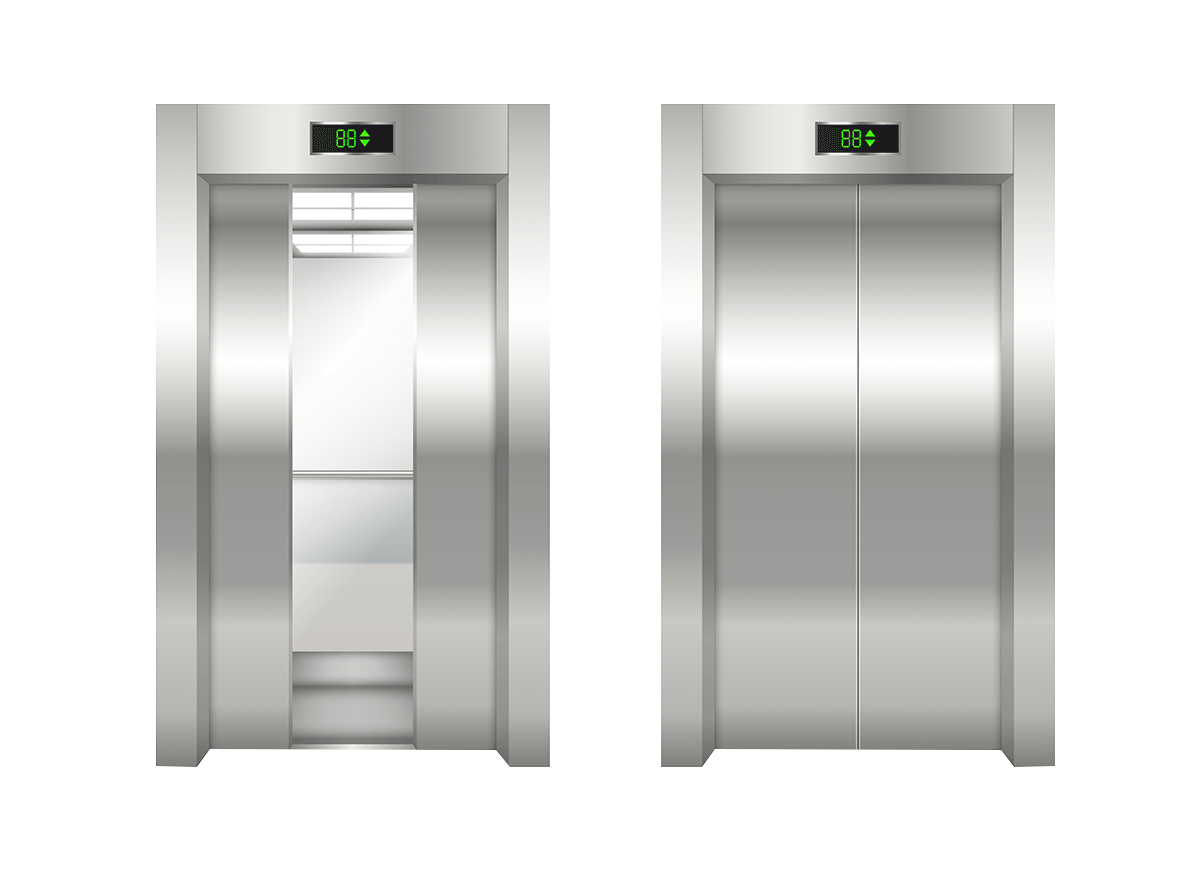
Strengthen patient safety with robust medical equipment
Our predictive maintenance software developed for medical equipment offers increased uptime, reduced maintenance costs, and enhanced patient safety. By monitoring critical components and utilising advanced sensors, potential issues can be detected before they lead to equipment failure.
This approach helps minimise unscheduled maintenance and maximise equipment performance in hospitals and clinics.
Technologies
Vendors: STMicroelectronics, NVIDIA
Programming languages: C, C++, Python.
Industrial networks: Modbus RTU, Modbus TCP, OPC UA, MQTT.
SDK: Qt, AWS, CMSIS RTOS 2, FP-IND-PREDMNT1, JetPack SDK (Jetson Linux, TensorRT, cuDNN, CUDA, computer vision).
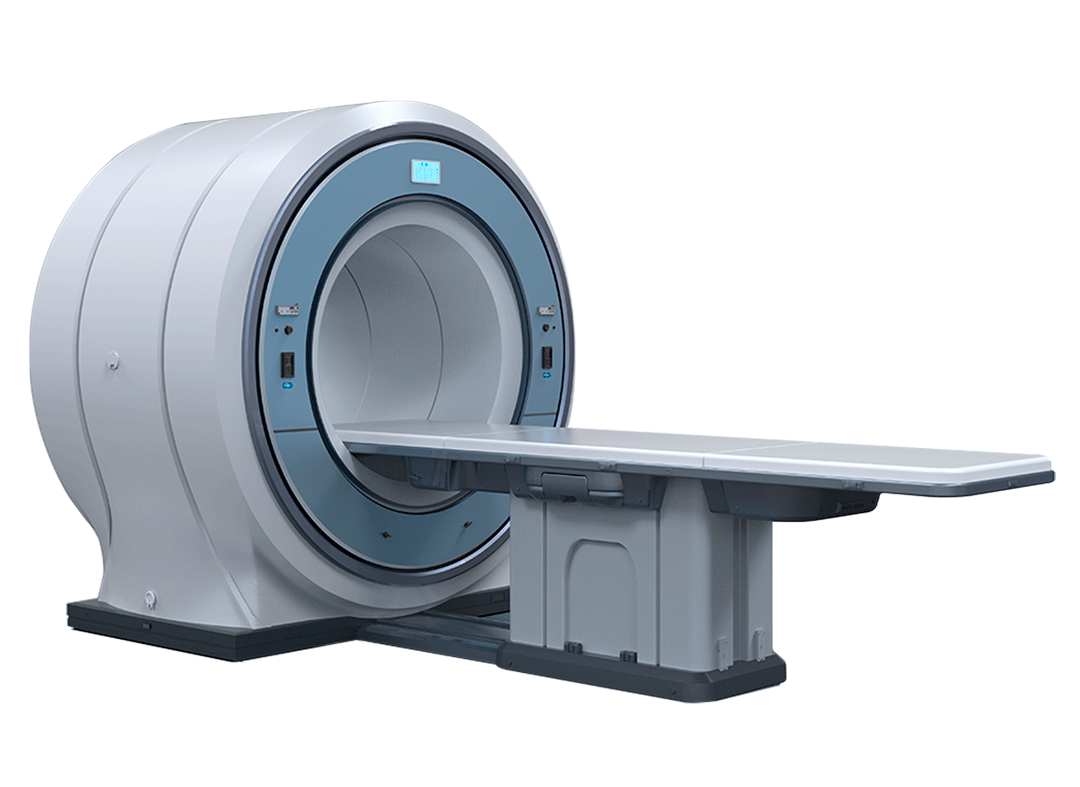
Optimise solar panel efficiency
We designed a solution to increase the effectiveness of solar panels. Our team implemented performance monitoring features and applied advanced analytics, enabling proactive maintenance scheduling to prevent downtime and extend the panels' lifespan.
This solution caters to various markets, including residential, commercial, and utility-scale solar farms.
Technologies
Vendors: STMicroelectronics, NVIDIA
Programming languages: C, C++, Python.
Industrial networks: IO-Link, Modbus TCP, OPC UA, MQTT.
SDK: Qt, AWS, CMSIS RTOS 2, FP-IND-PREDMNT1, JetPack SDK (Jetson Linux, TensorRT, cuDNN, CUDA, computer vision).
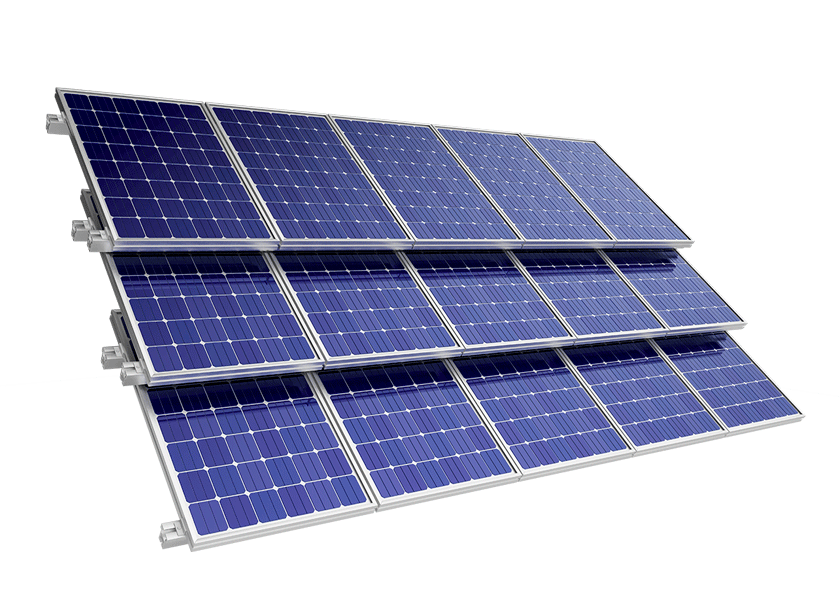
Ensure peak performance of mining equipment
We developed an IoT predictive maintenance solution for the mining industry, focusing on heavy equipment used in mining operations. The system was designed to analyse sensor data to detect early signs of equipment failure.
This proactive approach helps reduce unplanned downtime, optimise maintenance schedules, and improve safety, increasing production efficiency for mining companies.
Technologies
Vendors: STMicroelectronics, NVIDIA
Programming languages: C, C++, Python.
Industrial networks: OPC UA, MQTT, GigE Vision.
SDK: Qt, AWS, CMSIS RTOS 2, FP-IND-PREDMNT1, JetPack SDK (Jetson Linux, TensorRT, cuDNN, CUDA, computer vision).
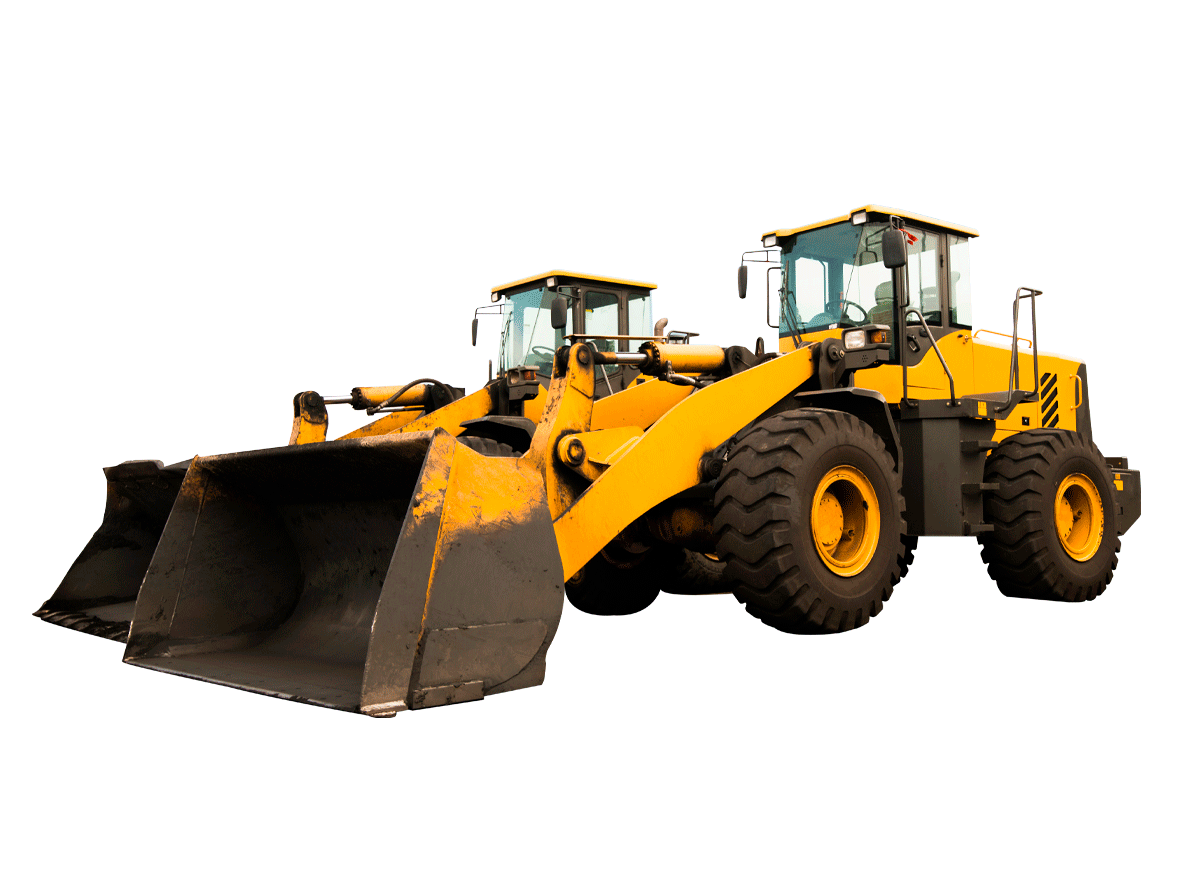
Maximise uptime and efficiency of air compressors
Leveraging data analytics and AI in predictive maintenance, we created a solution for air compressors.
The solution is aimed at helping manufacturers reduce unplanned downtime, optimise maintenance schedules, and improve energy efficiency.
Technologies
Vendors: STMicroelectronics
Industrial networks: IO-Link, OPC UA.
SDK: AWS, CMSIS RTOS 2, FP-IND-PREDMNT1 (STM32Cube function pack for multi-sensors node with signal processing to enable predictive maintenance).
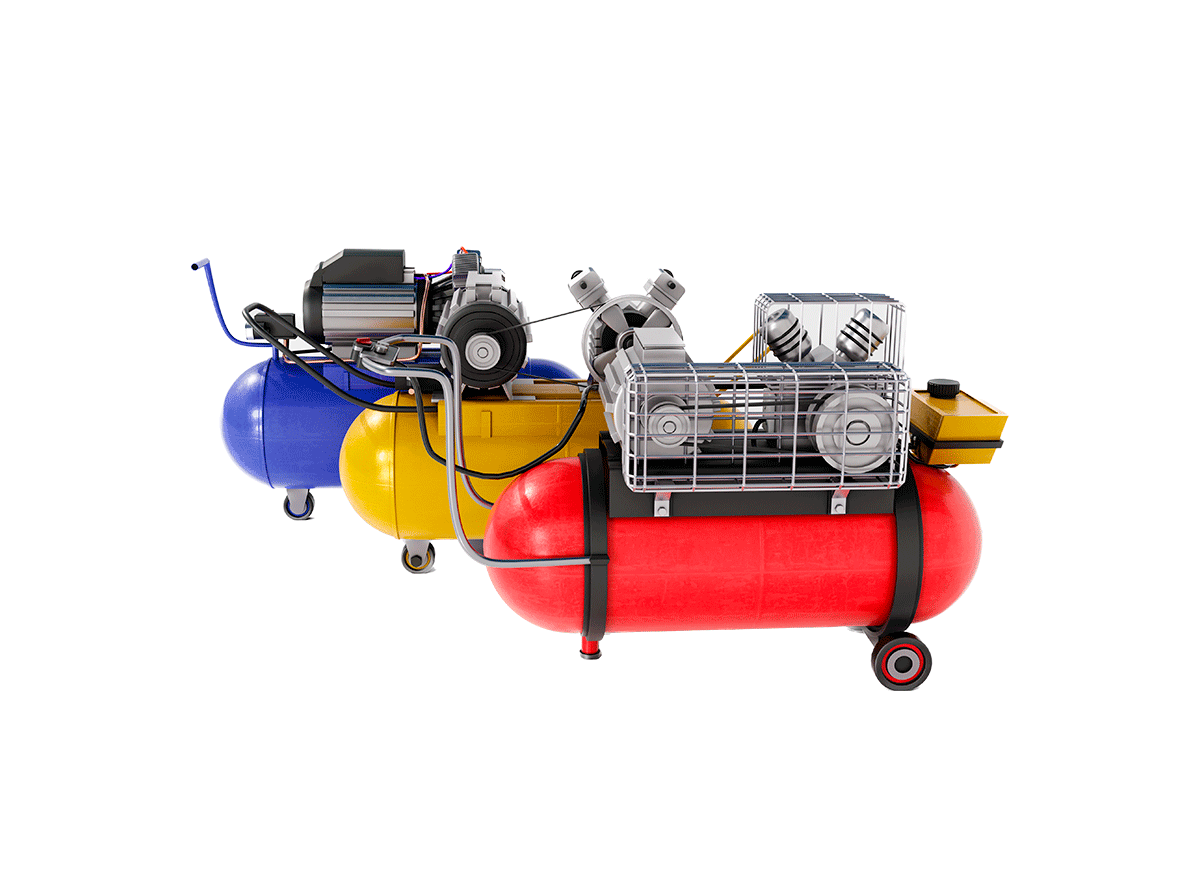
Reduce waste with optimised refrigeration systems
Our team engineered a solution for refrigeration systems that can be applied anywhere in the food and beverage industry. Employing industrial networks, it analyses sensor data and temperature indicators to detect potential equipment failures early on.
This optimises proactive maintenance scheduling, reduces unplanned downtime, and ensures consistent product quality for food and beverage companies.
Technologies
Vendors: STMicroelectronics, NVIDIA
Industrial networks: IO-Link, OPC UA.
SDK: AWS, CMSIS RTOS 2, FP-IND-PREDMNT1 (STM32Cube function pack for multi-sensors node with signal processing to enable predictive maintenance).
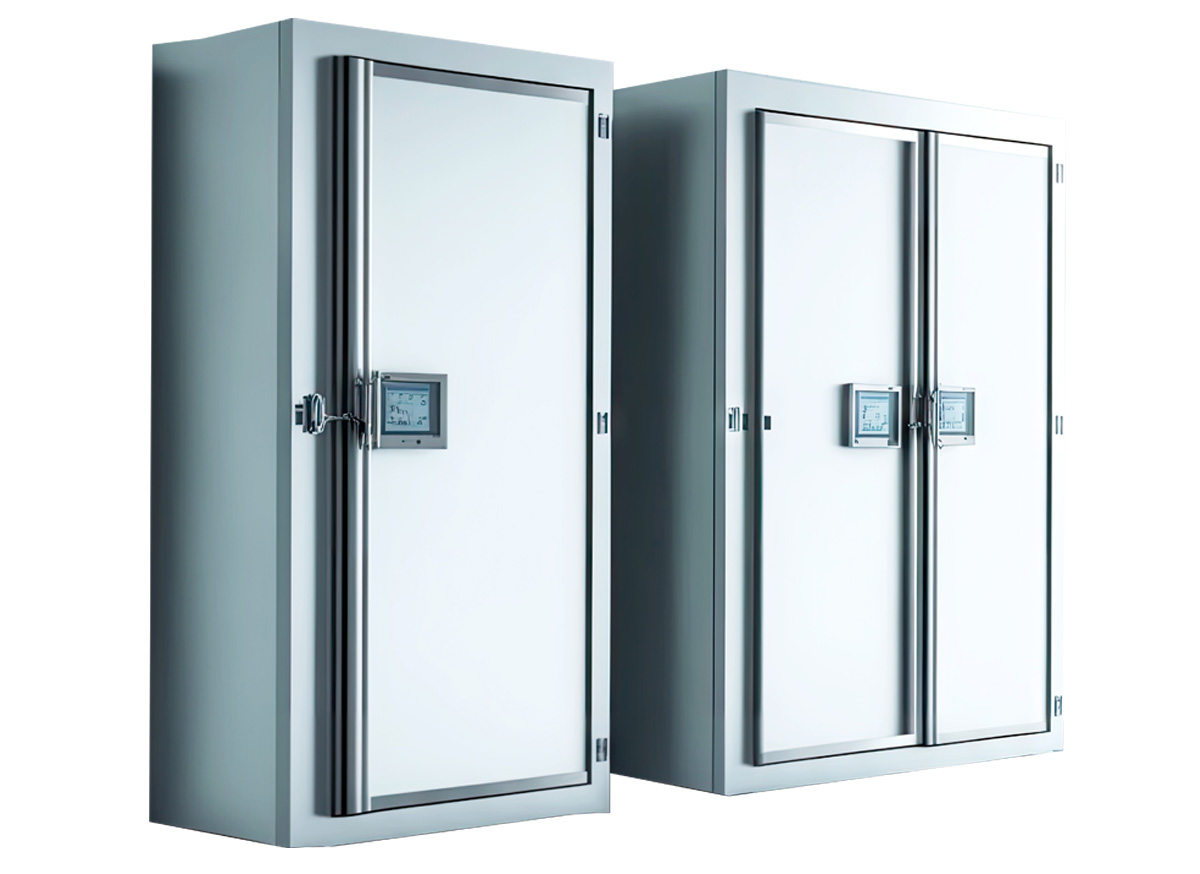
Streamline sensor data acquisition for motor control
In our demo, we leveraged a motor drive TI design for anomaly detection. The system utilises the AM437x IDK running processor SDK RTOS, PRU-ICSS EtherCAT Slave, and PRU-ICSS industrial drives for motor control. The AM437x IDK acts as an EtherCAT slave, communicating with a TwinCAT master on a host machine.
To acquire real-time sensor data, we implement high-speed UART with a baud rate of 921600. This enables the transmission of phase current measurements and motor position at a sampling rate of 10 kHz. Continuous data acquisition is achieved using PyAutoGUI, automating TwinCAT control. The motor moves repetitively between positions 1 and 2, ensuring a constant sensor data stream.
Read more about our motor control solutions
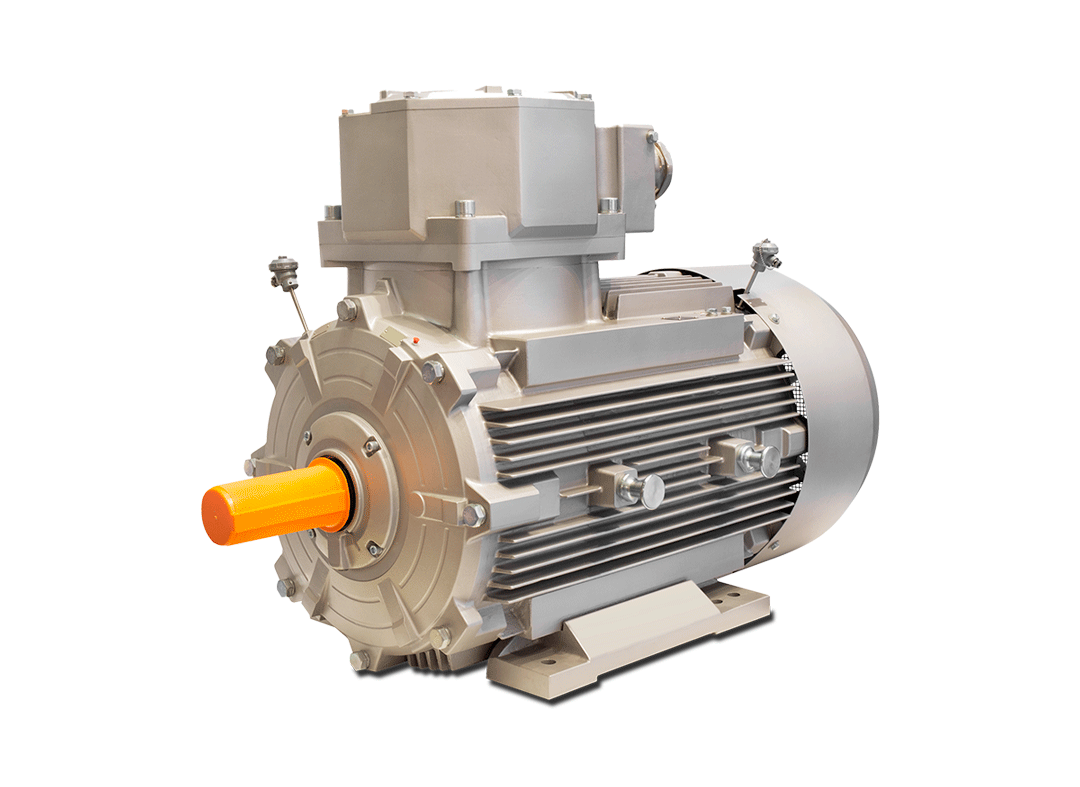
Our Tech Stack
Industrial
Interfaces
EtherCAT, PROFINET, POWERLINK, EtherNet/IP, Modbus TCP, OPC UA, MQTT, HART, IO-Link, PROFIBUS, Modbus RTU, CANopen, RS232, RS485
Cloud Databases,
Warehouses and Storage
AWS: Amazon S3, Amazon Redshift, Amazon DynamoDB, Amazon DocumentDB, Amazon RDS, Amazon ElastiCache
AZURE: Azure Data Lake, Azure Blob Storage, Azure Cosmos DB, Azure Synapse Analytics, Azure Kinect DK, Azure RTOS
GOOGLE CLOUD PLATFORM: Google Cloud SQL, Google Cloud Datastore
Camera Interfaces and Standards
SDI, HD-SDI, 12G-SDI, HDMI, MIPI CSI, MIPI CSI-2, FPD-Link III, Camera Link, USB, GigE, CoaXPress, GigE Vision
Big Data
Azure Cosmos DB, Amazon Redshift, Amazon DynamoDB, MongoDB, Google Cloud Datastore, Apache: Hadoop, Spark, Cassandra, Kafka, Hive, ZooKeeper, HBase
AI
Framework/Toolkits: TensorFlow, (Py)Torch, Keras, Darknet, Colab, Caffe, Amazon Machine Learning, Microsoft CNTK
Embedded SoC/FPGA AI Tools: NVIDIA AI Platform, Lattice senseAI, AMD/Xilinx Versal AI Engine, Renesas e-AI Solution
Cloud AI Platforms: GCP, AWS, Microsoft Azure AI
ML Libraries: XGBoost, Apache Mahout, Spark Mlib, Theano, Accord.NET AForge.NET
Forecasting tools: Facebook Prophet, ThingsBoard Trendz
We Work With
Predictive maintenance software can be implemented across various industries to address diverse business needs and improve operational efficiency.
Building and home automation (HVAC, lighting, appliances, and other systems)
Mechatronics (conveyor and elevator equipment)
Chemicals, incl. petrochemicals
Medicine
Light industry
Textiles
Woodworking
Construction
Mechanical engineering
Industrial machinery
Energy
Mining
Robotics
Why Promwad
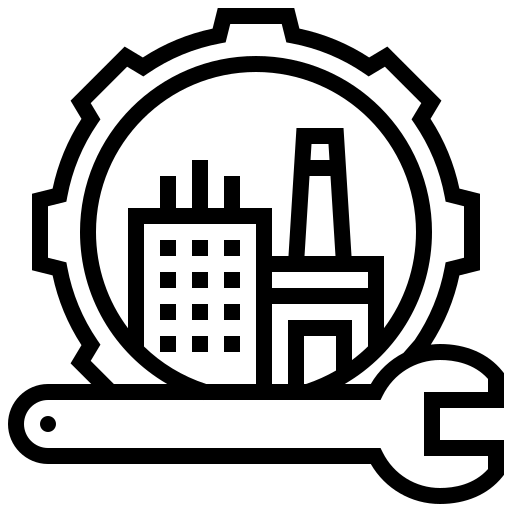
Industrial machinery expertise
We have successfully implemented predictive maintenance solutions for various equipment, including armature, pumps, solar panels, and medical supplies. Now, we can use this industry-specific expertise for your projects.
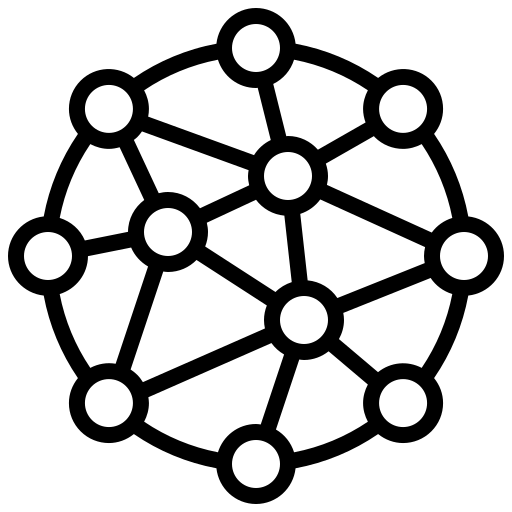
Cutting-edge technologies
We employ data analytics and ML techniques, applying statistical models, time series analysis, anomaly detection algorithms, and predictive modelling to extract valuable insights from sensor data and achieve accurate equipment failure predictions.
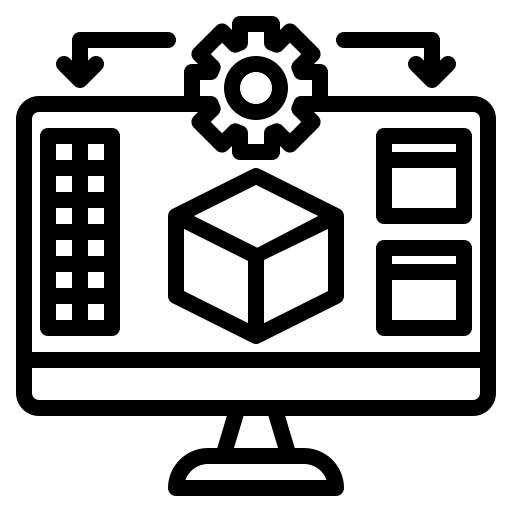
Infrastructure examination
We provide seamless integration with various industrial networks, protocols (OPC UA, Modbus TCP, MQTT), and data acquisition systems, ensuring smooth connectivity and efficient data exchange within your system.
Our Cooperation Models
Flexible approach to suit your current needs
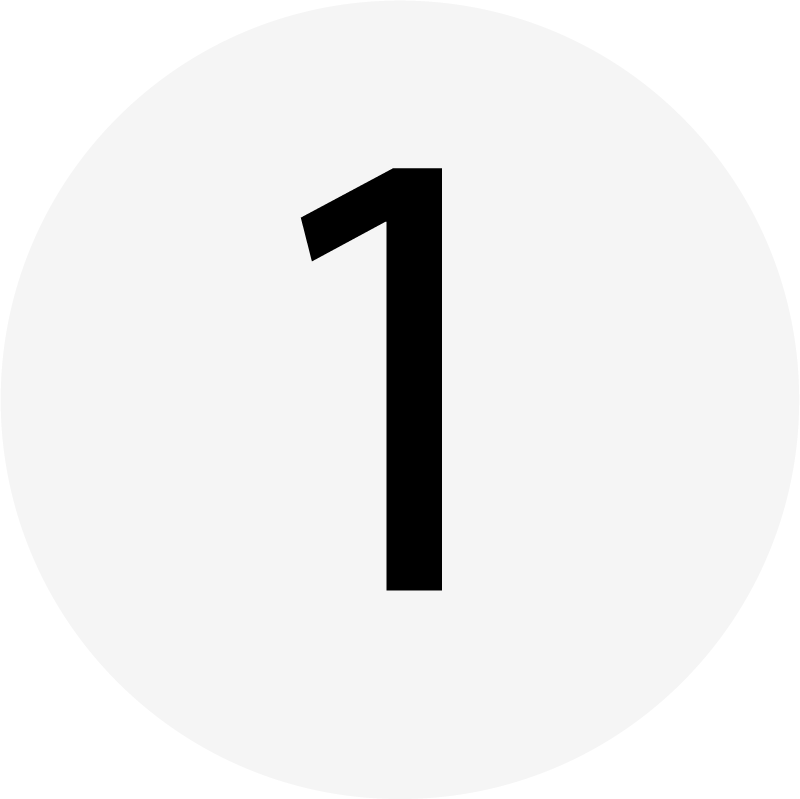
Dedicated Team
We will form a team to fit your specific engineering task. You are free to manage it and provide additional resources.
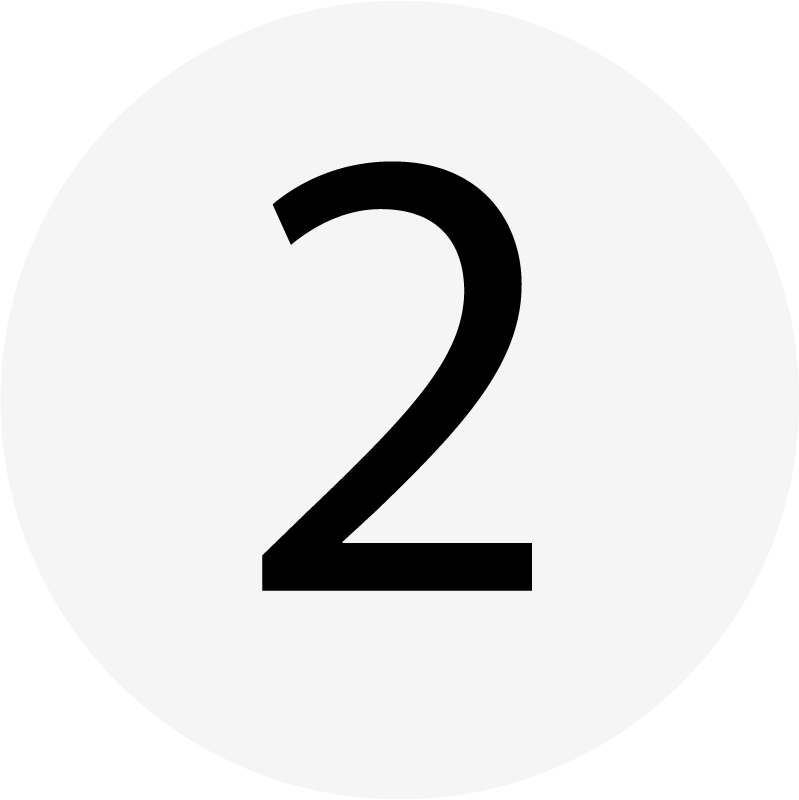
Project-Based
We can join you at any stage or take on the entire project, including our management and risk control.
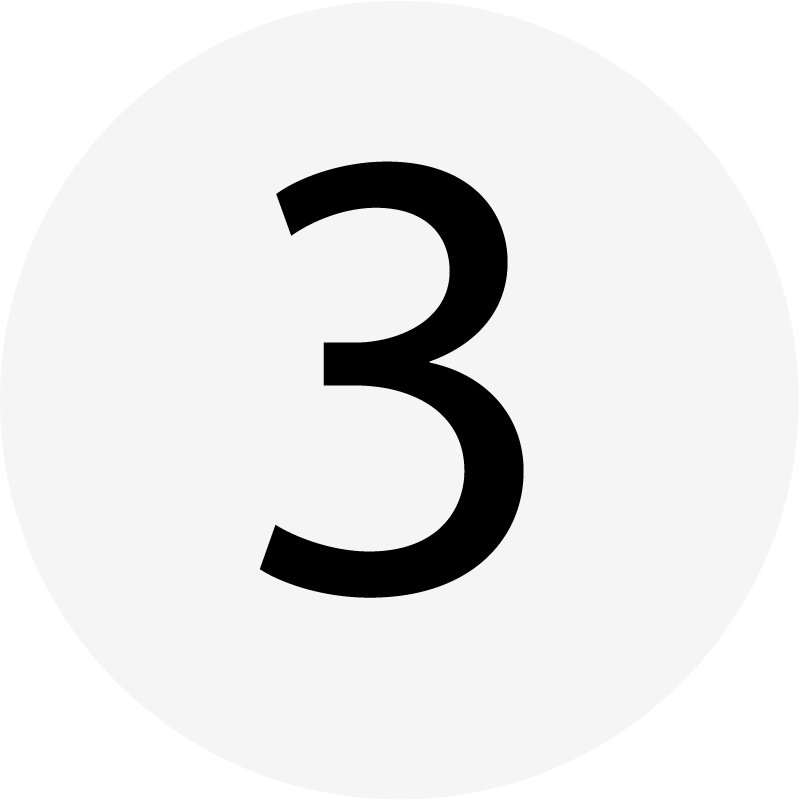
Fixed Price Model
This contract fixes the price so that it does not depend on resources used or time expended by our engineering team.
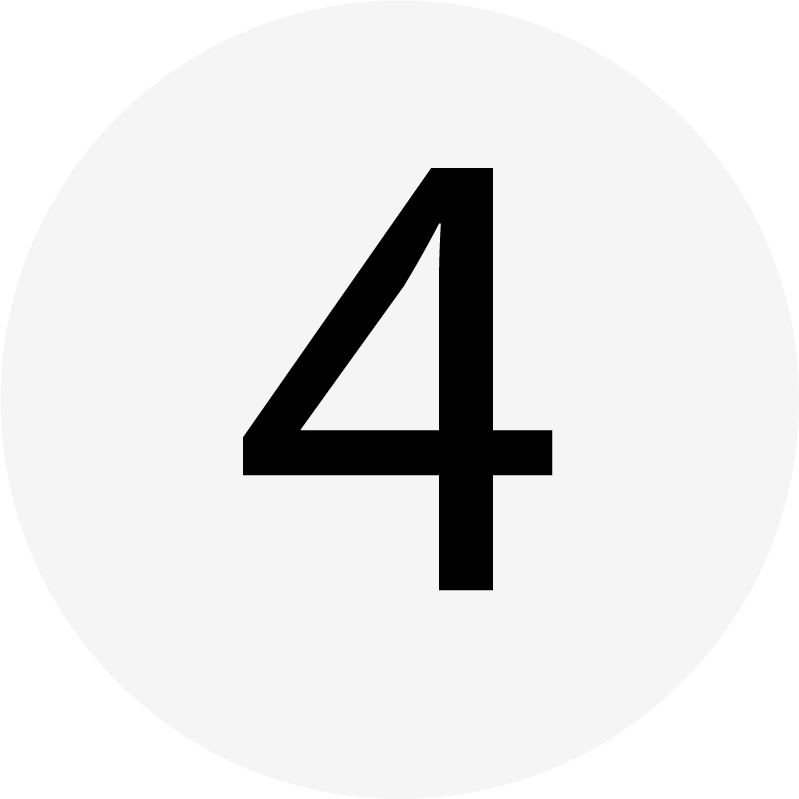
Time and Material
A T&M contract is the best option for your flexible set of tasks that are difficult or impossible to fix and assess in advance.
Do you need a quote for predictive maintenance solution?
Drop us a line about your project! We will contact you today or the next business day. All submitted information will be kept confidential.
FAQ
What types of equipment can benefit from predictive maintenance?
You can upgrade a wide range of devices, including but not limited to:
- Industrial machinery such as pumps, motors, compressors, and turbines.
- Manufacturing equipment like CNC machines, conveyors, and other industrial robotics.
- HVAC systems, including chillers, boilers, and air-handling units.
- Transportation assets like vehicles, aircraft, and trains.
- Power generation equipment such as generators and turbines.
- Medical devices and equipment in healthcare settings.
Can predictive maintenance be integrated with existing maintenance practices?
Yes, it can complement preventive and corrective approaches by providing advanced insights into equipment conditions.
PdM solutions harness the power of predictive analytics, sensor data, and machine learning algorithms to assess equipment conditions in real-time. Additionally, these solutions optimise maintenance schedules, minimise unplanned downtime, and significantly enhance overall equipment reliability by leveraging historical data, advanced algorithms and remote monitoring for predictive maintenance.
What are the benefits of using AI for predictive maintenance in manufacturing?
- Early fault detection: AI algorithms can analyse sensor data in real-time to identify anomalies that may reveal potential equipment failures or performance issues.
- Improved accuracy and precision: AI models can continuously learn and adapt based on historical data, enabling more accurate predictions of equipment conditions and failure probabilities.
- Cost savings and increased efficiency: by identifying maintenance needs in advance, AI-based predictive maintenance avoids unnecessary actions and optimises resource allocation.
- Enhanced equipment lifespan: proactive maintenance enabled by AI-based predictive analytics can extend the lifespan of critical equipment. By addressing issues before they escalate, manufacturers can minimise wear and tear, optimise maintenance interventions, and maximise the lifespan of their assets.
How do predictive and prescriptive maintenance strategies complement each other?
Predictive maintenance predicts potential equipment failures by analysing historical and real-time data to indicate when maintenance should be performed.
On the other hand, prescriptive maintenance takes it further by recommending specific actions to optimise decisions. These strategies consider multiple factors, such as equipment health, operational context, cost factors, and business objectives, to provide actionable recommendations.
By combining these two approaches, organisations can proactively detect potential issues, accurately assess the severity, and make data-driven decisions to optimise maintenance activities and maximise overall equipment performance.
What are some examples of prescriptive maintenance applications?
These applications can be applied in various scenarios, including:
- Optimal scheduling of maintenance tasks based on equipment health, criticality, and operational requirements.
- Recommending specific repair actions or replacement parts based on failure probabilities, cost factors, and availability.
- Providing real-time guidance to technicians, including step-by-step instructions, troubleshooting tips, and safety guidelines.
- Optimising maintenance interventions by considering factors such as weather conditions, production demand, and resource availability.
- Utilising advanced analytics and historical data to identify recurring failures' root causes and suggest long-term corrective actions.
- Analysing operational data to optimise equipment settings and parameters for improved performance and energy efficiency.
- Offering predictive maintenance insights integrated with asset management systems to enable seamless planning, tracking, and reporting of maintenance activities.