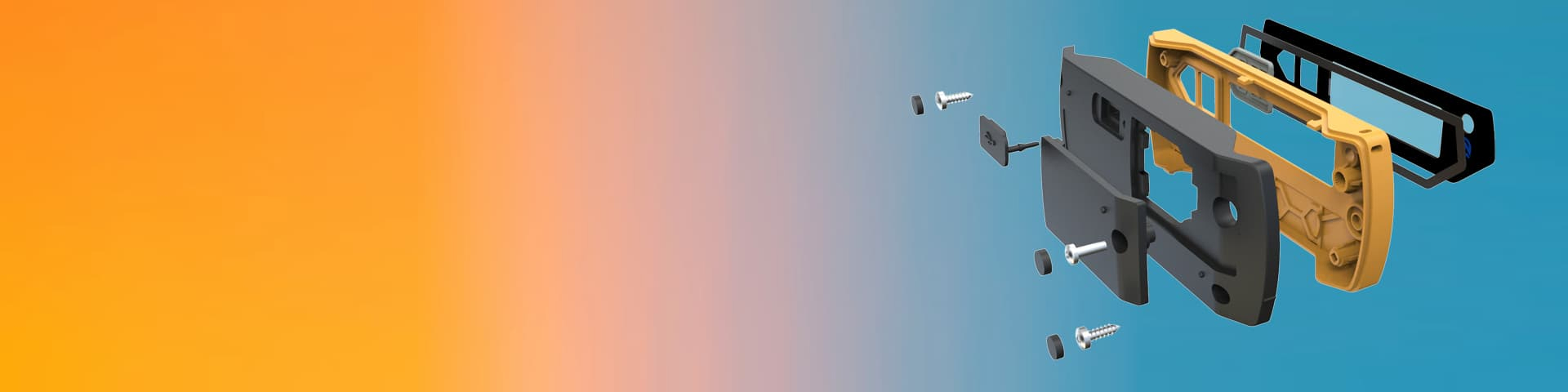
Custom
Enclosures
Custom Enclosure Design for Electronic Devices
- 20 years of experience delivering custom enclosures and mechanical engineering according to the design for manufacturing (DFM) approach.
- A proven track record of successful enclosure design projects, providing both protection and aesthetics.
- End-to-end design services: from enclosure style development to mechanical engineering and manufacturability analysis, we handle it all with our IT infrastructure.
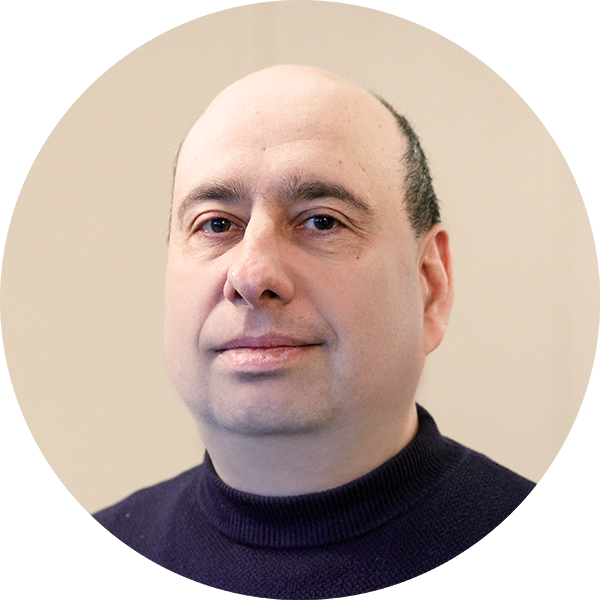
Pavel Moroshek, Head of Embedded Engineering Unit at Promwad
Enhance Your Time-to-Market with Promwad
Finding a design partner is challenging
Stay ahead of the competition with our team
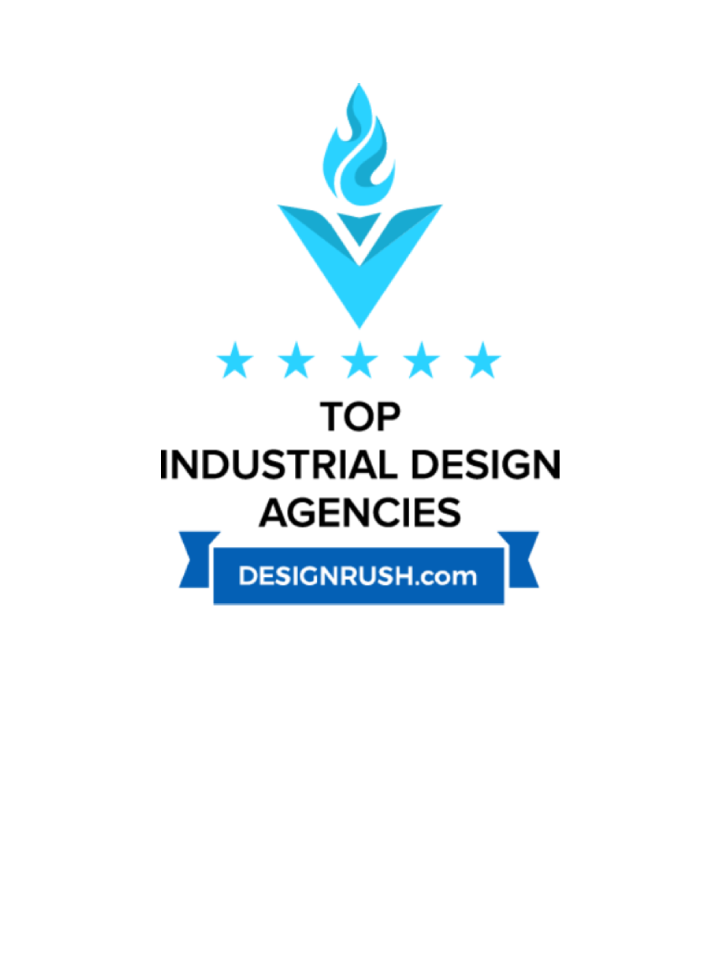
Enclosure Development Project Stages
At Promwad, we carry out the entire process of ​enclosure design, prototyping, and manufacturing.
1. Requirements
Preliminary research, market survey, pricing factors definition, production requirements implementation
2. Materials
Examination of the customer’s project based on the selected materials
3. Sketches
The first sketches and 2D/3D photorealistic images in a variety of colour and texture solutions
4. 3D modelling
For a more detailed elaboration of the future device, our designers develop a 3D model
5. DFM
Еnclosure prototyping and preparation for mass production in Europe or Asia
6. Production launch
We organise production in the optimal locations worldwide and offer consultations
Result
You get a reliable end device with the required protection against solids, dust, falls, and water with unlimited immersion time to a certain depth.
With our enclosure design services, you control the entire process, from creating the concept to the final ready-to-use device.
Results of Our Enclosure Design Services
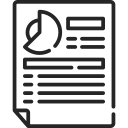
Design documentation
A project file with enclosure design details: costs, components, technologies, and specifications.
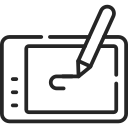
Drawings for enclosure production
Detailed blueprints with dimensions, materials, and assembly instructions necessary for manufacturers.
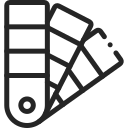
Product
samples
An enclosure prototype for evaluating quality, functionality, and performance before mass production begins.
Why Promwad

Style
We develop custom electronic enclosures following client needs and the latest market trends in terms of both style & development.
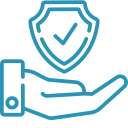
Reliability
Our custom enclosure solutions meet the specified requirements for tightness, flexibility, and strength, all in accordance with IP standards.
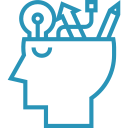
Professionalism
We guarantee the perfect project outcomes based on our vast experience in industrial design, engineering, and production launch.
Our Industrial Design Engineering Tasks
IP rating / Sealing
Protection against drops, splashes, jets, flooding, dust
Vandal-resistant enclosures
Shock and fall protection
Two-component (2K) materials
Protection against corrosion
Components cooling
Thermal simulations to implement ventilation requirements
Injection moulding simulation
Better moulded parts without defects
Shock and drop simulation
Explore Our Completed Projects
We have developed a custom enclosure, taking over the mechanical design and production start-up as well. We provided a high degree of protection against dust and moisture according to the IP67 standard. The robust rubberised device withstands falling from a height of 1.5 m on a hard surface. We also implemented a hermetically sealed sensor connector inside the device and made it easy to assemble and maintain.
What Our Clients Say
"At Kino-mo, we have developed the 3D Holo-Display, an innovative product which makes it possible to project 3-D images in the air. We turned to Promwad with the task of manufacturing new samples"
"Today, our IPTV STB is available at the market and competes on an equal footing with products by the world's leading manufacturers, such as Aminet and Motorola."
Materials for Electronics Enclosures
Thanks to our excellent supply channels, we are ready to work with any materials for your electronic case design:
- Plastics: ABS, ABS+PC, EK, PC, PE, PVC, PMMA, polyamide plastics, and others.
- Woods: different wood species, including composite combinations, such as wood + plastic.
- Metals: production of device enclosure parts from stainless steel, aluminium, and aluminium-magnesium alloys, using various technologies (stamping, moulding, milling, extrusion moulding).
At the customer's request, we can also utilise other materials in industrial processes, including rubber, ceramics, glass, and more.
Sometimes, materials chosen for mass production (e.g., plastics) may not be suitable for the prototyping stage. In such cases, we use an analogue that closely matches the original material's characteristics.
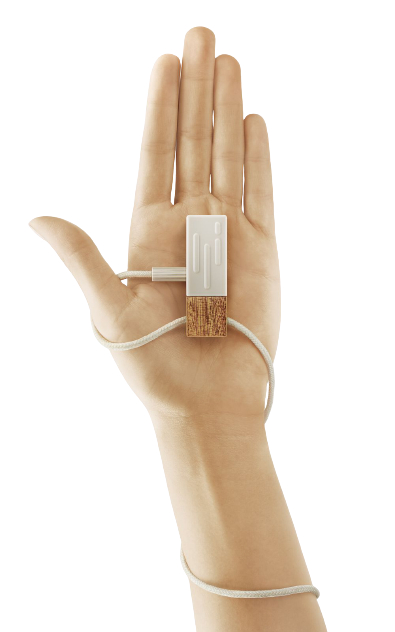
More of Our Case Studies in Custom Enclosure Development
Drop us a line about your custom enclosure design & manufacturing project and get a quote!
We will contact you today or next business day. All submitted information will be kept confidential.