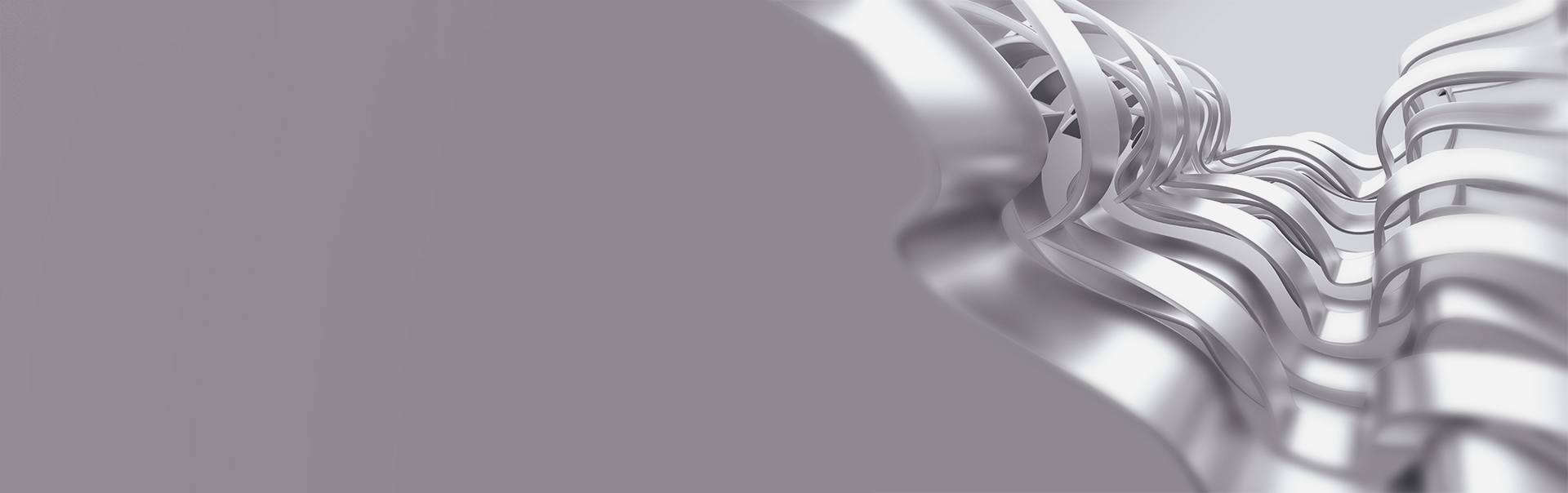
Material
Selection
Electronics Enclosure Materials
Enclosure materials play a crutial role in the manufactoring process, demanding careful selection and expertise in industrial design, management and marketing. We help our clients select the right material for their electronics enclosures, whether it's for prototypes or mass-produced designs.
We know how to combine various materials, including wood, ceramics, composites and additive materials, virtually all plastics, glass, and metals. Our experience in prototyping and production of electronics helps us choose the best material options based on design needs, client preferences and budget.
Materials for prototypes
At the prototyping stage it is not always possible to use materials that have been chosen for mass production. For example, prototyping of plastic electrical enclosures cannot be done with certain types of plastics which are nevertheless successfully used in manufacturing commercial devices. In this case, we use an analog which will reflect the characteristics of your original choice as fully as possible.
Material combinations
Combinations of different materials are often used in enclosure manufacturing. For example, when designing a plastic enclosure box for electronics, several materials may be employed at once: plastic + metal/glass/ceramics/rubber, etc.
In this case, we can provide relevant expert advice on manufacturing, which helps correctly implement jointing locations for selected materials to provide the specified requirements for integrity, flexibility and durability of the finished product, thus matching the designer’s and the customer’s preferences with real production capacities.
Choice of enclosure colour according to RAL and Pantone
We work with international colour management systems — RAL and Pantone — to ensure that the appearance of your case and mass-produced devices is clearly defined and reproduced.
Even if you are located on one continent and your production site on another, standardised colour-matching systems allow everyone involved in the project to see the final look of your device. You only need to find the right code on RAL or Pantone fans or colour charts.
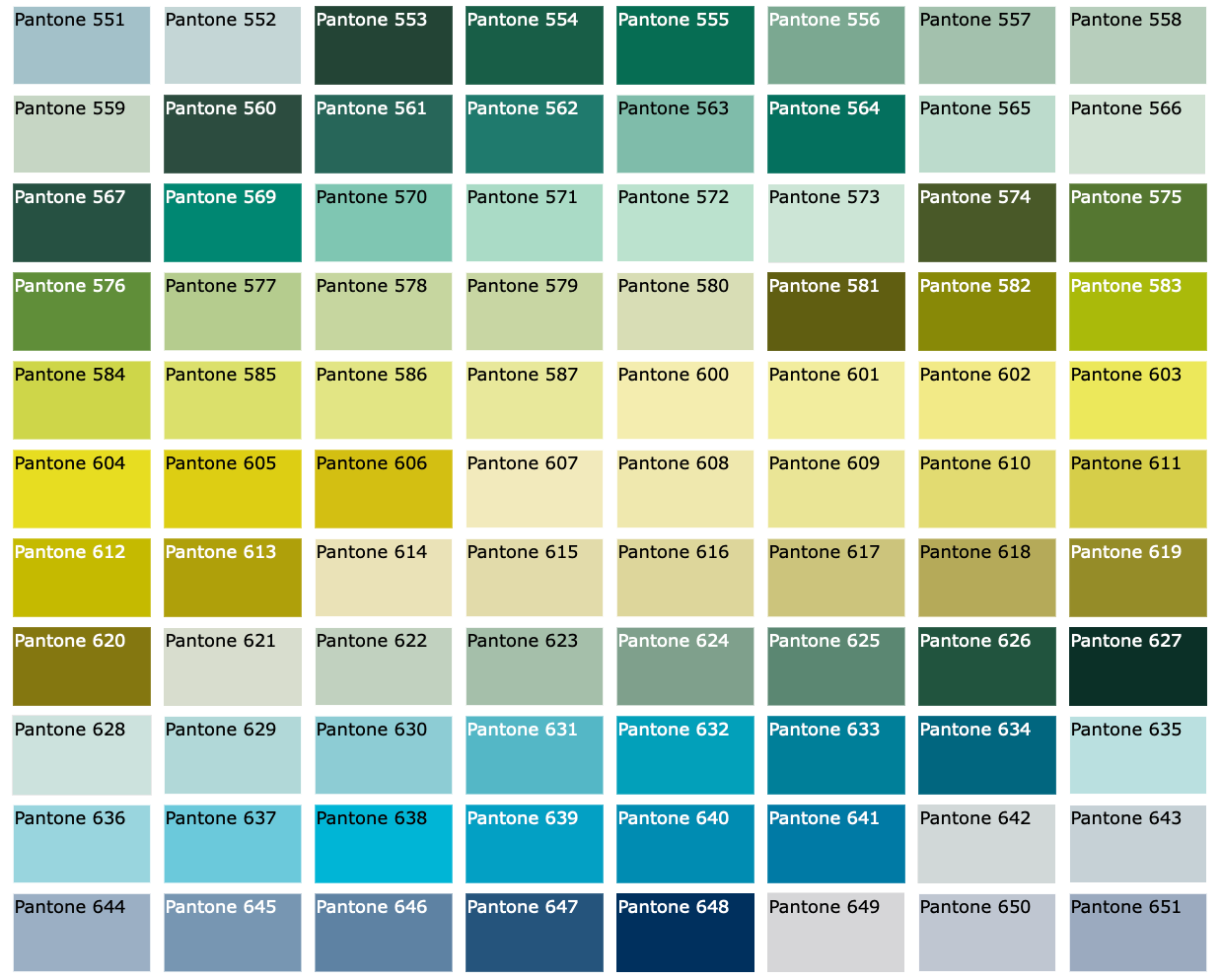
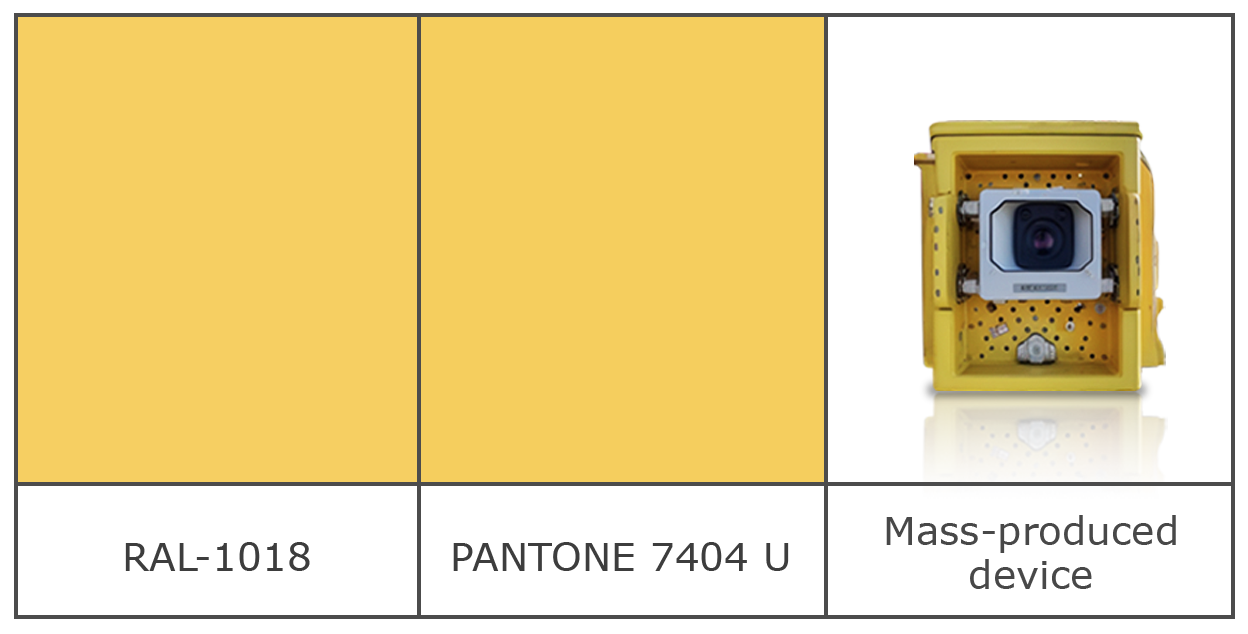
Colour selection and coordination
Together with our clients, we determine the optimum colours, surface textures and degree of gloss when creating photorealistic 3D models of their new devices and reflect this information in the design documentation for production.
What we consider when choosing colours
- Application area of your device
- End user needs
- How often the device will be touched
- Internal components (if the enclosure is transparent)
- Environmental factors
With RAL or Pantone pallets, it is possible to optimise production costs: similar shades may contain varying amounts of pigments, so if a change is allowed in the project, we can choose a more cost-effective one without losing quality.
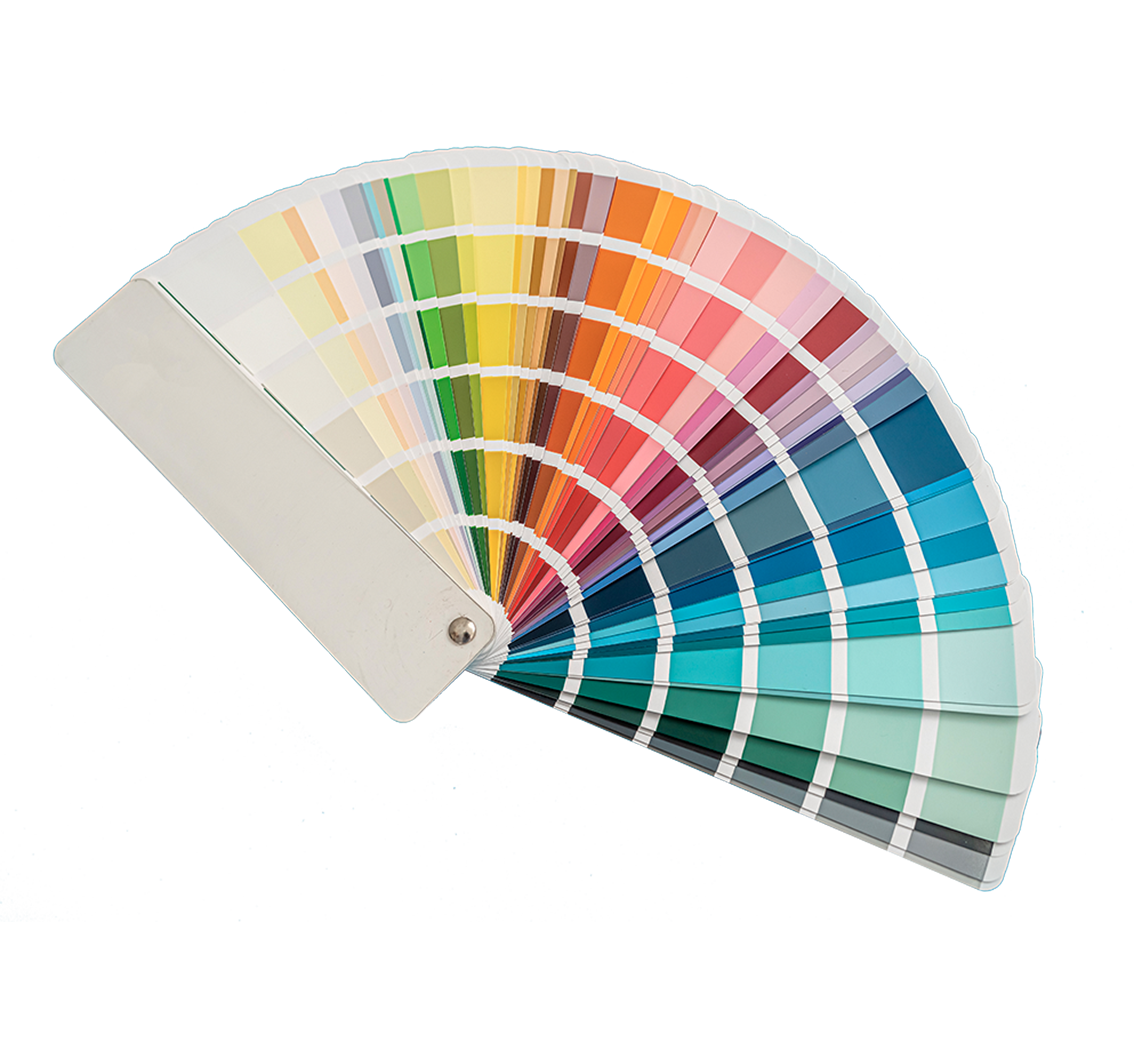
Advantages of RAL and Pantone Colour Management Systems
manufacturers
Case studies on design and production with various colours and materials
Fish finder: industrial & mechanical design
Industrial design and construction of the new generation echo sounders.
- For the upper part, the “glass” is poured separately and silkscreened. This glass is used as a mortar piece, which is poured over the plastic.
- The resulting plastic part with glass is poured in rubber (TPU), which also forms the elastic buttons, serves as a protective bumper, and is a “gasket” to ensure the tightness of the case when assembled with the bottom part, which is produced in the same way, but without mortgaging parts.
To implement this idea, the optimal serial technology was chosen – a two-component (2k) casting, which uses a special machine with two installed moulds.
Qoobi One, a wireless vacuum tube preamp
To develop the mechanical design of a wireless tube amplifier, Qoobi One, using a ready-made design of our customer.
Non-standard materials were chosen for the production of the case:
- Anodized aluminum with manual polishing for an internal enclosure that cools radio tubes, hiding the device's printed circuit board with a digital-to-analog converter and a chip with Bluetooth 5.0 support.
- Thin quartz glass with engraving for manufacturing of the outer transparent case of the Qoobi One. It looks impressive and reveals the glowing radio tubes.
LED lighting of the device is controlled by a mobile application.
Analysis and consulting
Our projects also involve relevant calculations, computer analysis and simulation of manufacturing processes, which helps optimise enclosure designs, based on the characteristics of the material when it is cast into the mould.
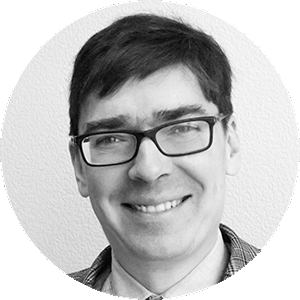
“Promwad industrial designers pay special attention to the selection of materials, suppliers and production specifics. So our customers receive a guaranteed result at the production site - a product free from molding defects (deformations / sink marks / solder seams) and a highly durable enclosure.”
— Ivan Kuten, Managing Director & Tech Advisor at Promwad GmbH
Our Case Studies in Industrial Design
Do you need a quote for the selection of materials for your electronics enclosures?
Drop us a line about your project! We will contact you today or the next business day. All submitted information will be kept confidential.