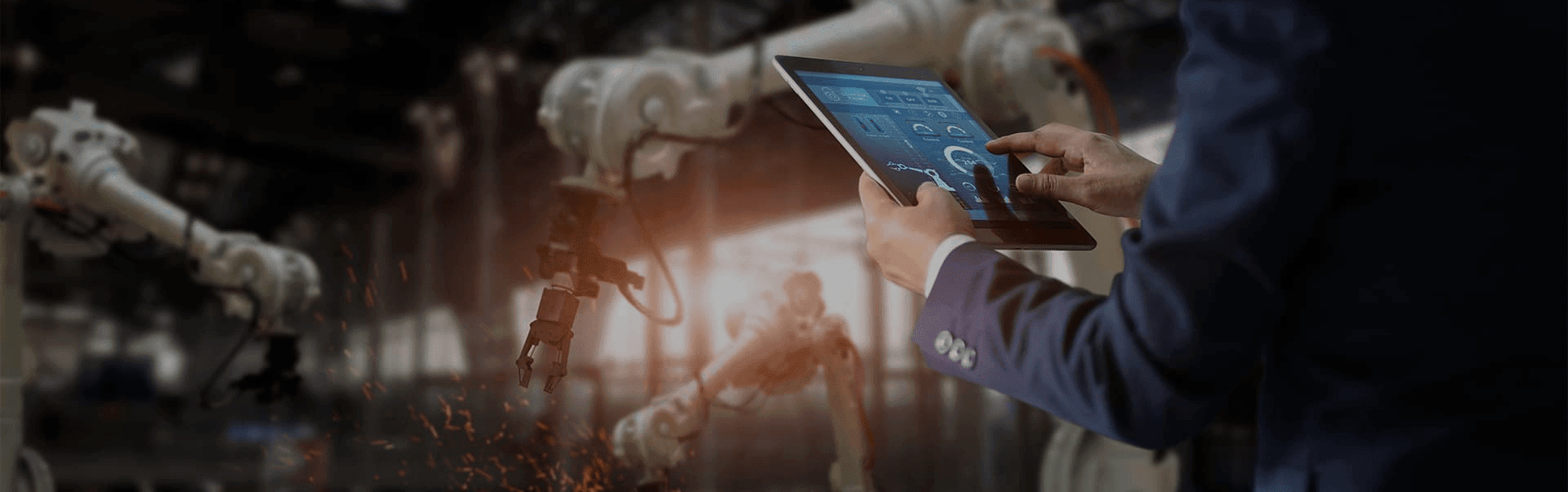
Industrial Solutions
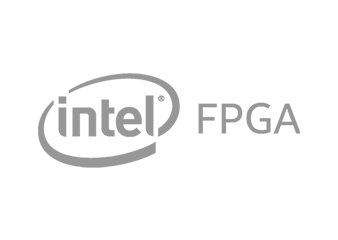
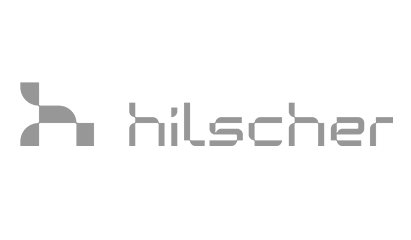
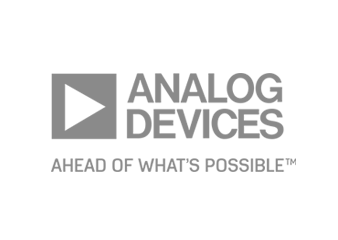
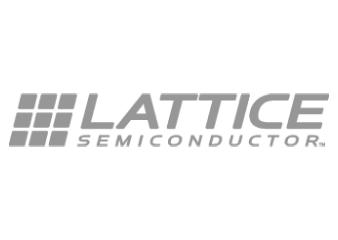
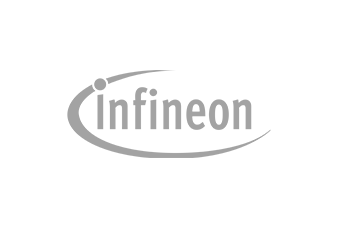
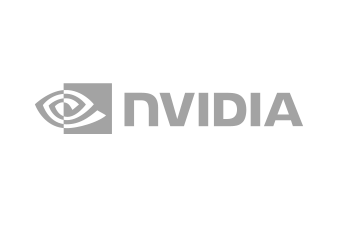
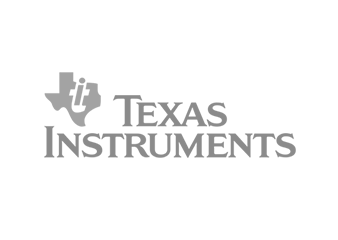

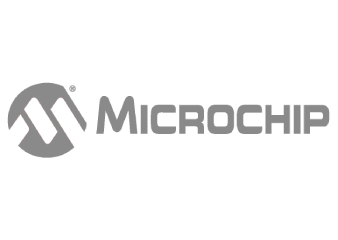
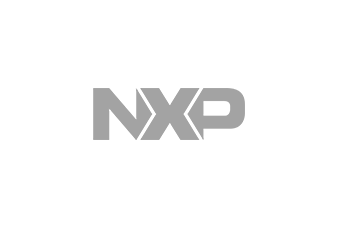
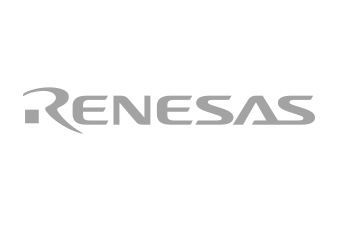
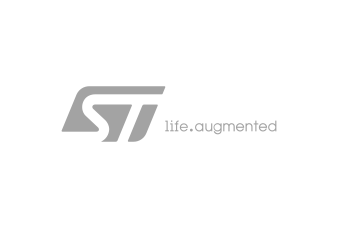
Custom Industrial Automation Solutions: Hardware & Software
Our Expertise
The upper level: SCADA & HMI
HMI panel design
Software development for SCADA (supervisory control and data acquisition): HMI systems, such as Simatic WinCC, to enable the creation of custom SCADA solutions
OPC UA data acquisition server and software development
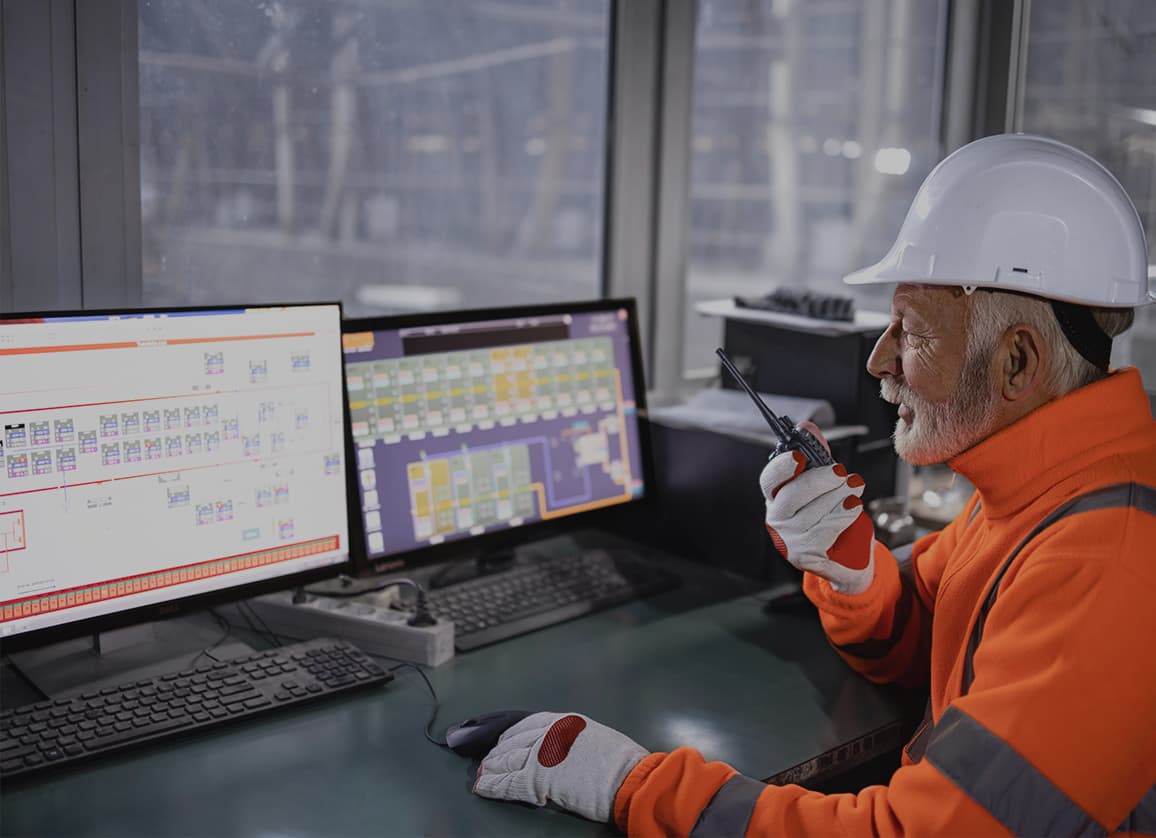
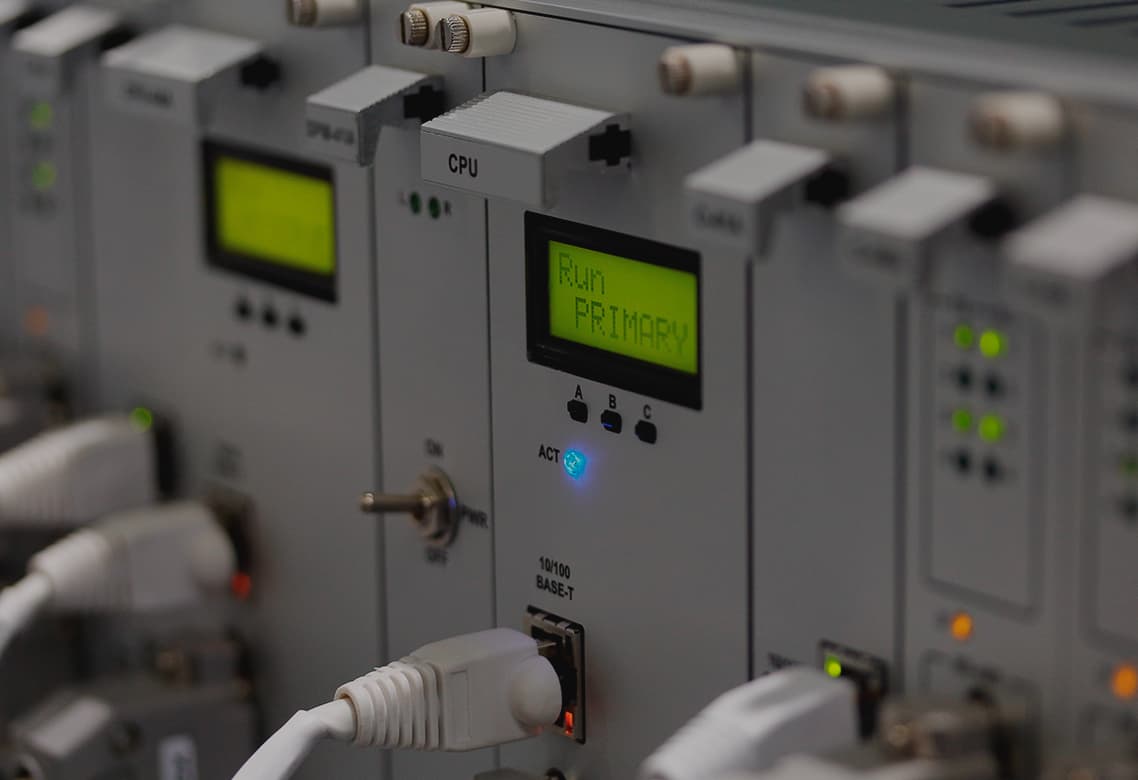
Controller level: automation devices & PLCs
Software and hardware automation engineering
Electronics, enclosure, and firmware development for programmable logic controllers (PLC)
Development of data acquisition (DAQ) systems and distributed control systems (DCS)
Design of interface converters
The lower level: sensors & motor control devices
Turnkey sensor design: enclosure and mechanical design; software development, maths and algorithms for the primary measuring transducer, schematic diagrams and PCB design
Electronics, enclosure, and firmware development for motor control solutions: soft starters, frequency converters (VFD), servo drives, and stepper motor controllers
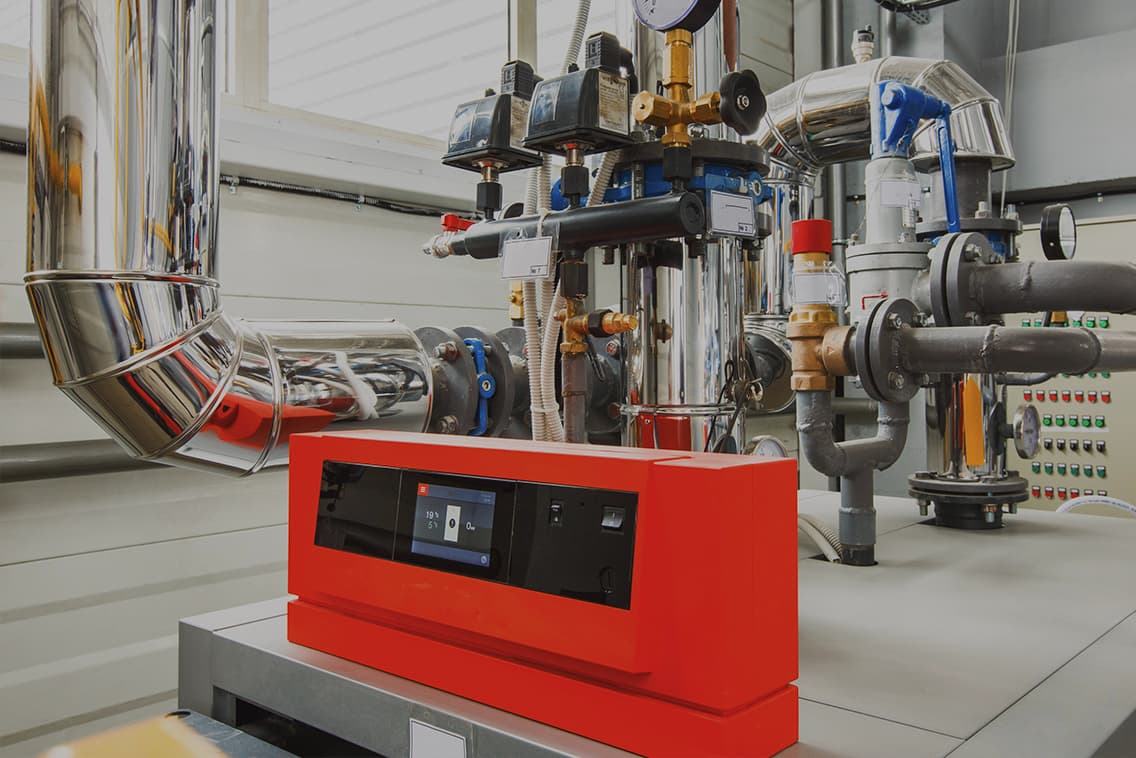
What We Do
Design of hardware and software platforms for motor control systems.
Read more
Secure solutions for real-time data transfer via industrial protocols.
Read more
Custom solutions to optimise maintenance schedules and prevent unplanned downtime.
Read more
PLC, SCADA, MES, and ERP software development for devices and systems manufactured by our clients.
Read more
Custom systems to enhance resource recovery and provide early warnings for equipment failure.
Read more
Employ IEC 61508 to establish unified network communication across automation devices.
Read more
Our Industrial Automation Engineering Services
Our Tech Stack
Platforms
ARM, RISC-V, MIPS, FPGA/CPLD
Tools & Languages
С, C++, Python, Rust, Qt, JavaScript, Verilog, VHDL, HLS, LLVM
Industrial Interfaces
IEC 60870-5-101/104, IEC 61850, EtherCAT, PROFINET, POWERLINK, EtherNet/IP, Modbus TCP, OPC UA, MQTT, HSR/PRP, HART, IO-Link, PROFIBUS, Modbus RTU, CANopen, RS232, RS485, SNMP, IEC 62056 (DLMS/COSEM)
Vendors
Texas Instruments, Microchip, NXP, STMicroelectronics, Renesas, Infineon, Intel, Xilinx, Lattice, Analog Device, NVidia
OS
Baremetal, Linux (+RT), ROS, RTOS: FreeRTOS, ChibiOS/RT, eCos, CMSIS-RTX, RTEMS, Segger embOS, Mbed OS, TI-RTOS
Build Systems
Buildroot, OpenEmbedded/Yocto Project
HMI/SCADA/Web SCADA/Dashboard Dev
Microcontrollers: TouchGFX, EmWin, uGFX, lvgl | Linux: Qt (QML, Widgets), JavaScript, C++, Rust, WebAssembly
Asymmetric Multiprocessing (Linux + RTOS)
OpenAMP, OpenMCAPI, jailhouse, Xenomai, rpmsg
Our Case Studies in Industrial Automation
Why Promwad
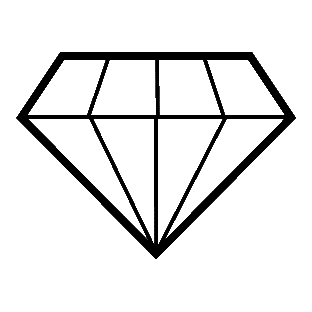
Cost-effective approach
We allocate an engineering team with a tech lead and management to work together with our client’s teams. Therefore, they do not have to bring in their in-house specialists or an expensive external integrator.
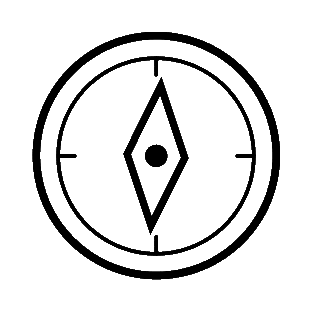
EtherCAT Group member
As a member of the EtherCAT Group, we follow all the established industry standards. Our customers can access the necessary data at any time to improve the efficiency of their machines and equipment.
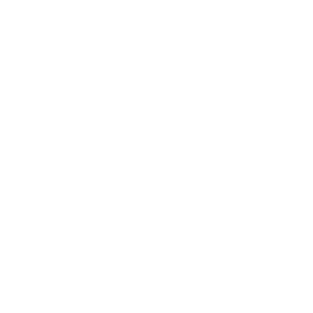
Turnkey product development
At Promwad, we cover all the bases of turnkey product design with a single industrial automation contractor. Also, you can use our cross-industry expertise in the IIoT, telecom, adaptive computing, and automotive industries.
Our Cooperation Models
Flexible approach to suit your current needs
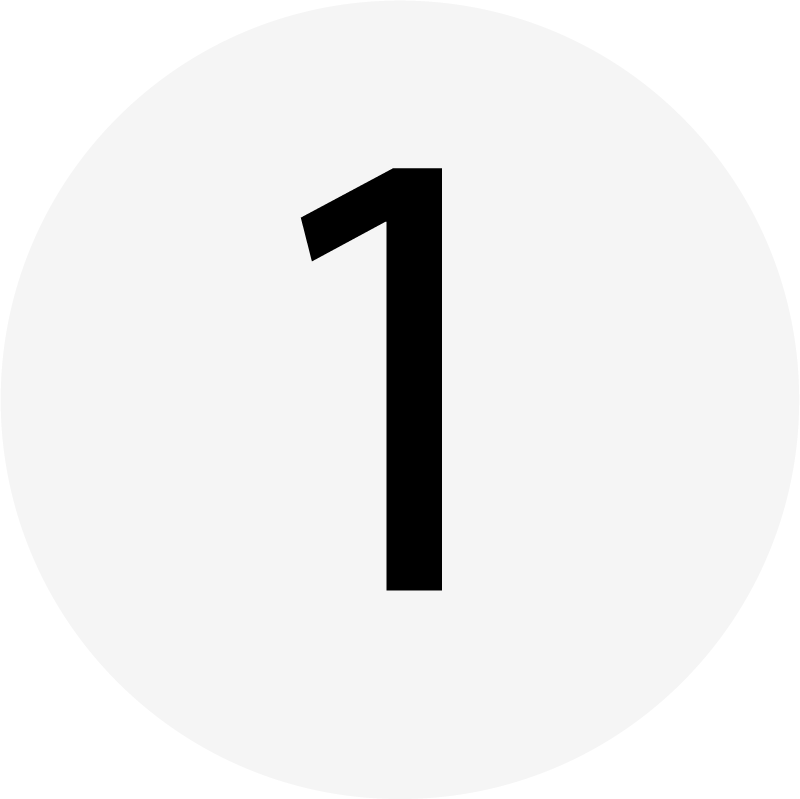
Dedicated Team
We will form a team to fit your specific engineering task. You are free to manage it and provide additional resources.
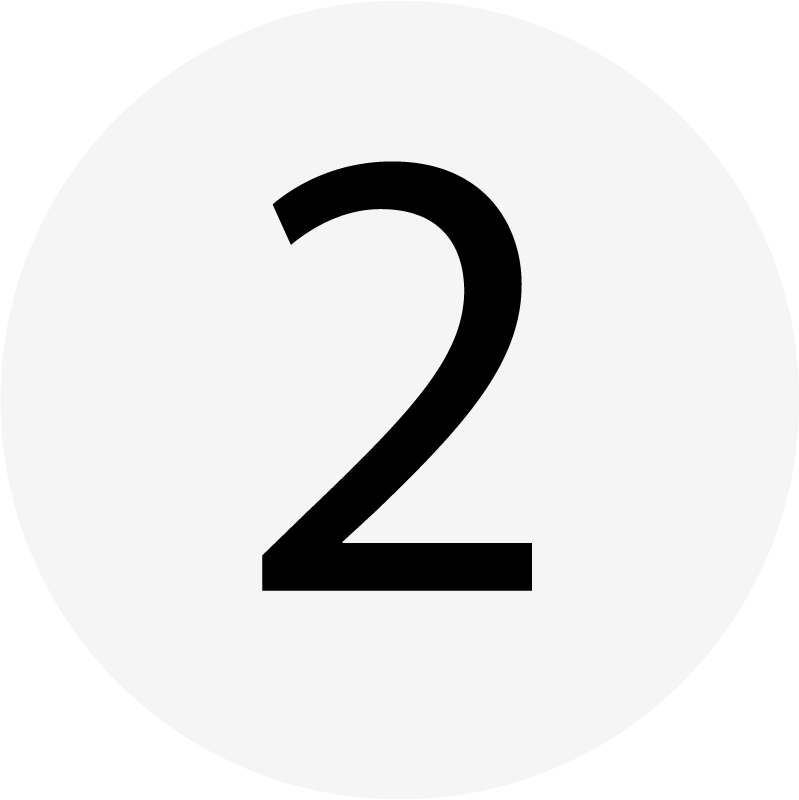
Project-Based
We can join you at any stage or take on the entire project, including our management and risk control.
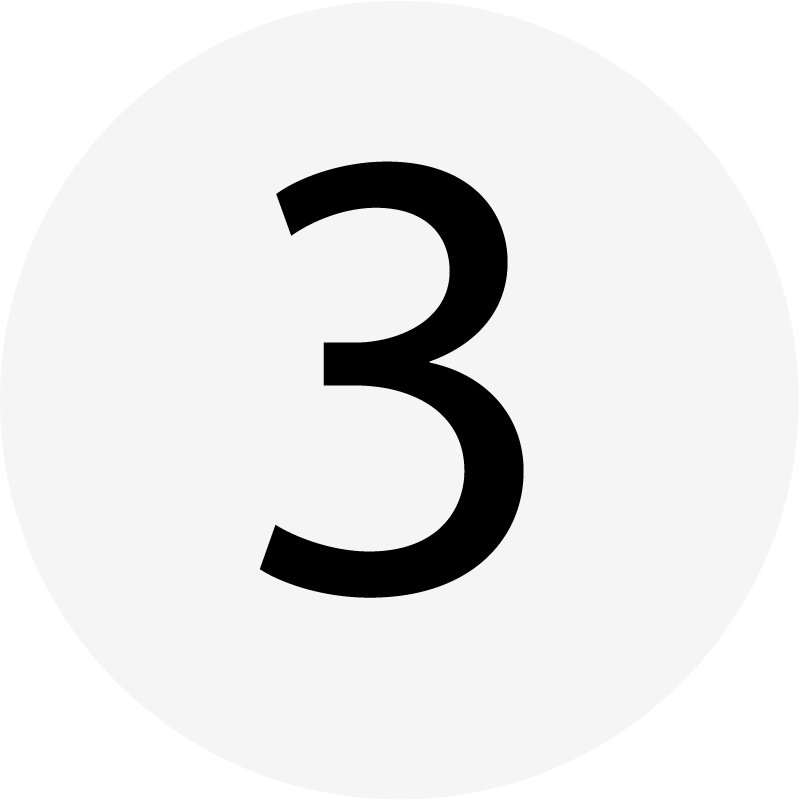
Fixed Price Model
This contract fixes the price so that it does not depend on resources used or time expended by our engineering team.
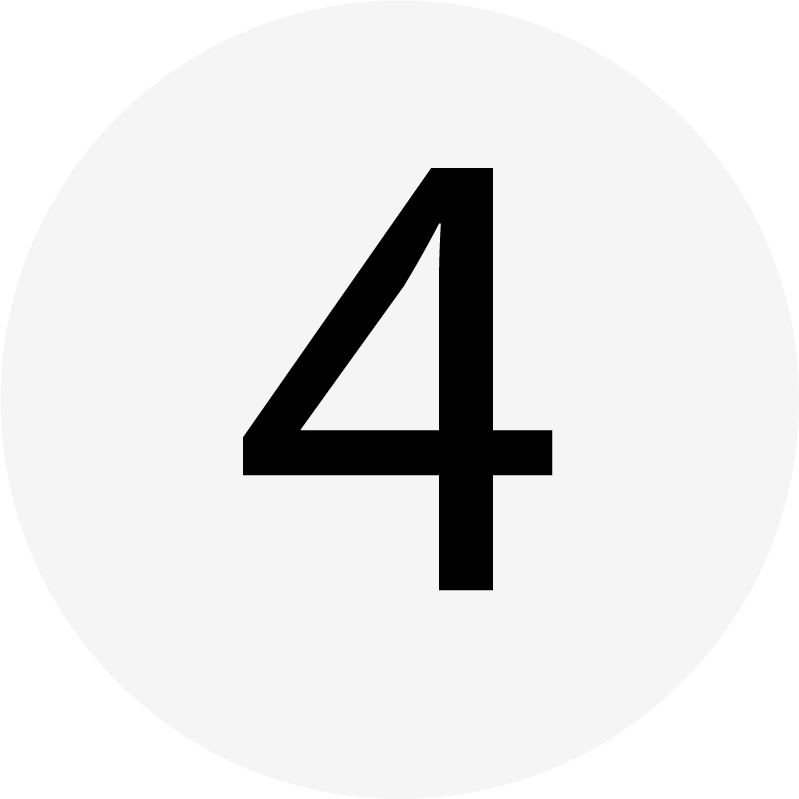
Time and Material
A T&M contract is the best option for your flexible set of tasks that are difficult or impossible to fix and assess in advance.
Drop us a line about your industrial automation or robotics project and get a quote!
We will contact you today or the next business day. All submitted information will be kept confidential.
FAQ
Who are your clients? Who do you develop devices and software for?
We work with startups and mature companies that produce industrial automatics and robotics systems worldwide. Our team helps them solve specific engineering problems within our manufacturing automation consulting and development projects. Here are a few examples of our current and potential customers:
- Manufacturers of drive electronics (frequency converters, servo, and step controllers, soft starters).
- Manufacturers of DCS/PLC/PAC and data acquisition (DAQ) systems.
- Manufacturers of industrial interface converters.
- Power supply companies and those focused on power electronics and systems for power engineering.
- Companies that need customised software development for IA, HMI, SCADA, OPC/OPC UA, ROS, and other technologies.
- Companies working with green energy solutions.
- Telecom companies focused on industrial networks.
- Developers of DAQ/IO systems and safe controllers.
- Companies in predictive maintenance and Edge AI for IA.
- Manufacturers of elevators, conveyors, and crane manufacturers.
- Manufacturers of CNC and batching systems.
- Manufacturers of relay automation (RPA, PA, and more).
- Developers of mobile robots for various applications.
- Manufacturers of air conditioning/cooling systems.
- Companies focused on smart homes and building automation companies.
Even if you don't find yourself on this list, we're still happy to discuss your potential engineering challenges. So don't hesitate to contact us.
What is the difference between the IIoT and the standard approach in industrial automation systems and the power sector?
The standard approach solves certain tasks in the control of industrial processes. IIoT is an autonomous predictive system that is usually not directly included in the production process. With IIoT, processes can be monitored by measuring the metrics needed for predictive maintenance solutions to make faster decisions at the business level. It involves edge processing when data is transmitted to the cloud system, bypassing the transmission level to the PLC and the SCADA system.
Why is real-time networking important for industrial automation, and what technologies and tools do we use to achieve this?
For most systems in industrial automation, time is crucial: they must be well-coordinated and react in real time to external influences at critical moments to guarantee the safety and efficiency of the whole process.
To ensure this parameter, we use safe real-time operating systems, and for supercritical systems, we offer industrial standard FPGA solutions.
What is the lifecycle and temperature grade of components in industrial automation?
The solutions that are created for industrial automation have a long lifecycle of components. In this area, innovations must be considered from many perspectives because, when selecting a new device or embedded system, planning and its integration into the production chain can take years (even decades).
The temperature grade in industrial automation usually ranges from -40 to +85 degrees Celsius. Our developers are guided by these time and temperature frames when selecting components.
What is SIL? How is security defined at the hardware and software levels?
The SIL abbreviation stands for Safety Integrity Level and refers to the certification of software and hardware components to ensure their reliability and security.
SIL certification identifies all process hazards, assesses the risk of failure, and determines that if a failure occurs, the component will "fail safely". For the same process, there can be four safety levels, from SIL 1 to SIL 4 that are determined by calculating the hazard risk reduction factor (RRF).
The SIL level is ensured in terms of software, hardware, and descriptions of possible situations. Each level has an acceptable failure rate: the higher the level, the lower the failure rate.
Why is industrial automation a conservative industry?
Plants are critical facilities. Reliability and resilience are crucial for systems that are implemented in manufacturing because they directly affect people's lives — from industrial injuries to technological disasters. To avoid attacks on industrial facilities, systems must be minimally vulnerable at the device and communication protocol levels.
The new technology takes time to industrialise, and standards take a long time to adopt, so change comes slowly. For example, HMS Networks' research shows that, at the beginning of 2022, the share of wireless protocols was only 7%, and the bulk of data transmission still went through wired networks.
The hardware is changing, but popular networking technologies remain. All industrial protocols are closed as proprietary ones, so engineers have to join the organisation that develops them to find out how a particular standard works. This high entry threshold is due to the high demands placed on the reliability of the systems to be implemented. This is what makes the industrial automation industry so conservative.