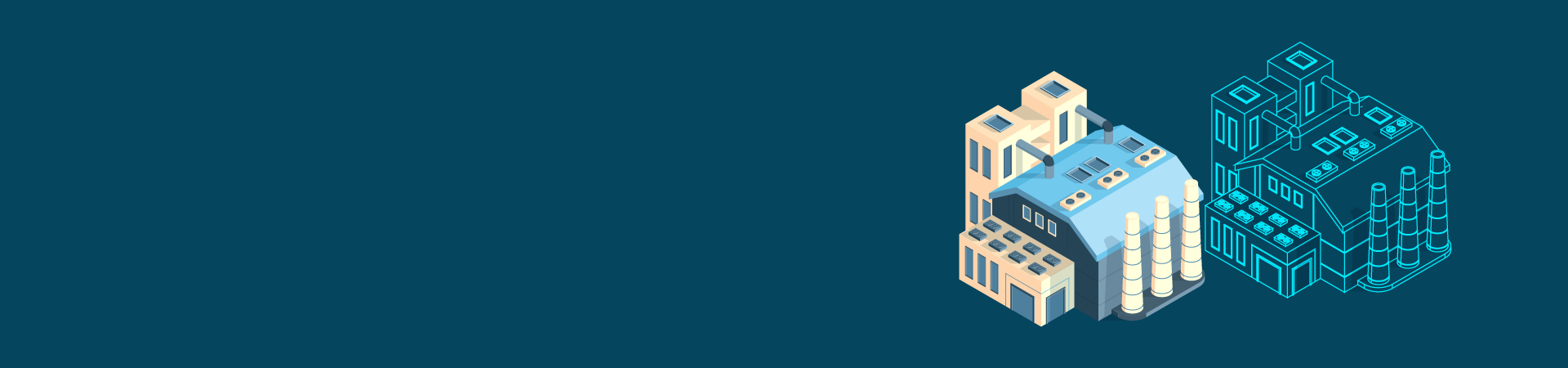
Digital Twins
Custom Digital Twin Design Services
We design digital twins for accurate virtual representations of physical objects or processes. They are updated in real-time and used for simulations, machine learning, and informed decision-making throughout their lifecycle within the Industry 4.0 framework.
Promwad also creates digital twins as intermediaries for communication between assets, including sensors and actuators, to enable the representation of industrial automation services and consumer-oriented IoT applications, including smart home and city systems.
How Does a Digital Twin Work?
As a virtual model, a digital twin mirrors a physical object's characteristics. Consider a pump equipped with sensors that capture vital performance metrics such as energy input and temperature. Digital twin services collect this data and forward it to high-level applications like web/mobile platforms, cloud services, and SCADA systems.
Upon integration into the digital twin infrastructure, this data fuels analysis. Engineers can then run simulations, assess performance, and identify improvement areas without modifying the device. Thus, a digital twin uses real-time data to refine understanding and optimise the physical object.
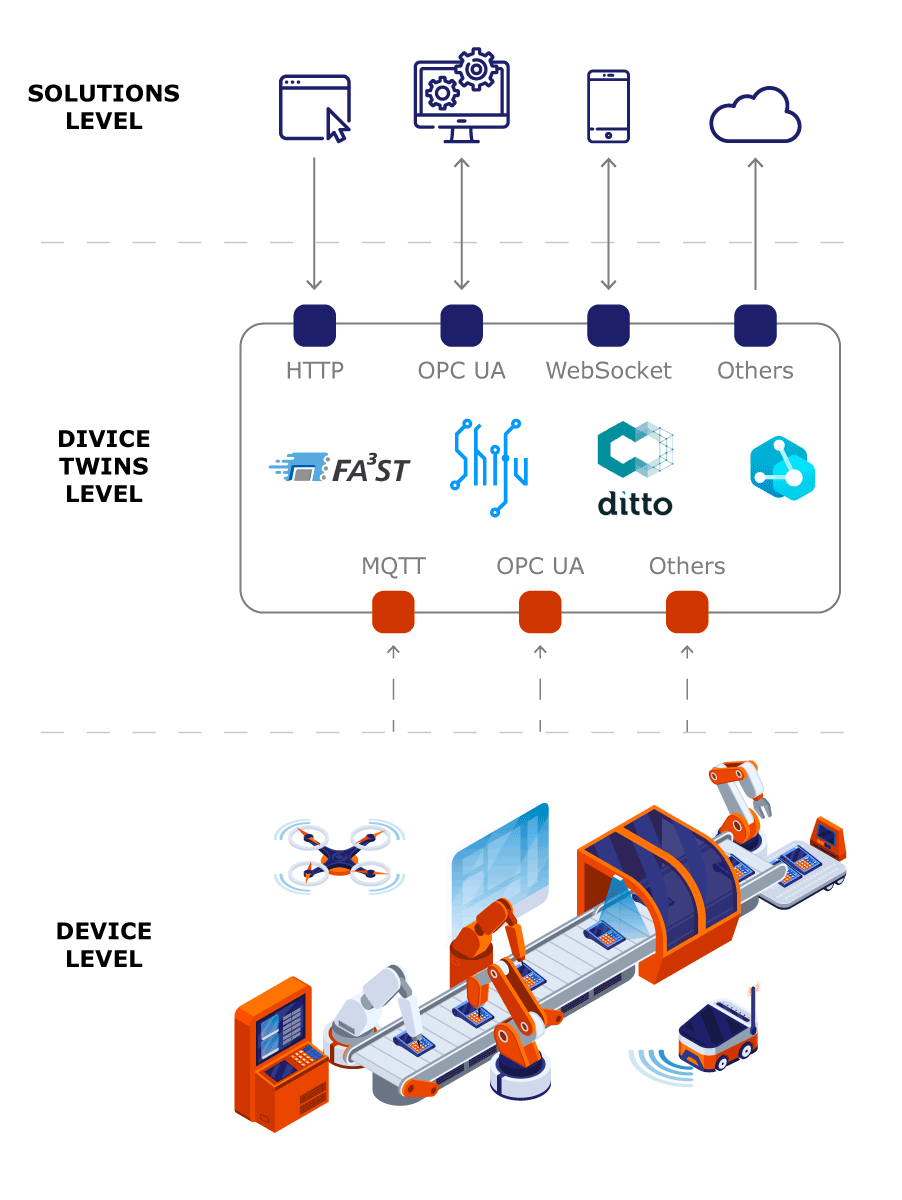
Digital Twins vs. Simulations
Unlike simple simulations, which typically focus on singular processes, digital twin software can execute multiple simulations concurrently, thus offering a more dynamic virtual environment for study.
The 3D digital twin technology enables a two-way flow between the sensors and insight data. This approach offers more significant product and process improvement potential than traditional simulations.
Digital Twins vs. IoT
While digital twins and IoT often overlap conceptually, they serve distinct roles. IoT connects devices to the Internet and gathers measurement data, while digital twins organise this data for unified use, enabling the implementation of artificial intelligence, machine learning, and business rules.
In resource management, IoT controls devices, and digital twin software supervises assets, providing broader functionality.
AI Algorithms We Work With
AAS
The Asset Administration Shell
WoT
W3C Web of Things
DTDL
Digital Twin Definition Language
Known Digital Twin Design Standards
Eclipse Ditto
Azure Digital Twins
FA³ST (FAAAST)
Shifu
NVIDIA Omniverse
We use NVIDIA Omniverse Cloud and NVIDIA Omniverse Enterprise to develop custom digital twin solutions. With the power of NVIDIA OVX, we achieve precise, real-time simulations and AI-driven improvements. Thus, we ensure accurate virtual data, physical authenticity, and timely synchronisation for reliable decision-making before production.
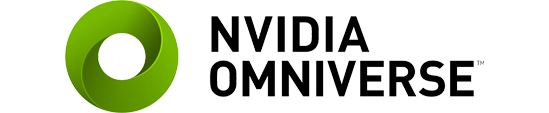
Unity's technology
We use the Unity Industry, a suite of tools, to create digital twins, enabling the real-time iteration of interactive 3D content. Unity's products facilitate the data integration from diverse formats (e.g., BIM, CAD) and systems (e.g., PLM, IIoT) for visualisation.
With technology's industry-leading support for over 20 platforms, including Windows, iOS, and Android, our team ensures comprehensive enhancement of industrial processes for companies of any size.
Enhance Industrial Design with Digital Twins
Early-stage design →
Companies use digital twin software to create virtual prototypes of devices and components, helping to reduce design cycles and prevent costly mistakes.
Performance optimisation →
Manufacturers employ digital twins as a service to evaluate and improve the performance of diverse processes, such as motor efficiency and power usage, under different conditions.
Safety testing →
Digital twins facilitate simulations for safety tests, enhancing device safety features and minimising potential accidents at factories and other large industrial facilities.
Manufacturing optimisation →
Within manufacturing, the technology assists in refining processes such as assembly line layouts and tooling designs, leading to cost reductions and improved efficiency.
Application Areas
Process Manufacturing
Digital twin types
In process manufacturing, digital twins are categorised into distinct levels. Choosing the right type has to be aligned with specific business goals to enhance performance across the required operational levels.
- Component or part twins focus on individual components like equipment parts. Engineers use them to assess durability and efficiency and predict maintenance needs, such as monitoring a product performance.
- Asset or product twins offer a holistic view and enhance the overall efficiency of assets, reduce downtime, and optimise processes, such as heating raw materials in a plant.
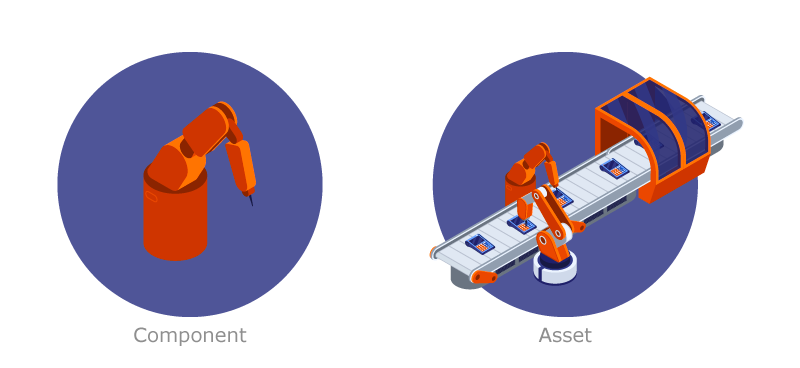
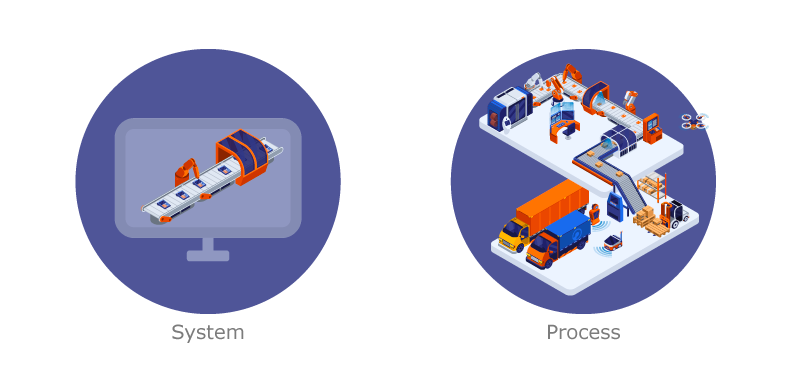
- System or unit twins integrate asset twins to understand inter-asset collaboration. They help plant managers optimise performance, reduce wear and tear, and explore new business opportunities, like streamlining a chemical plant's base product production.
- Process twins encompass entire plant workflows. This software allows managers to analyse system-wide coordination, tweak operational inputs, and monitor crucial metrics, aiding strategic decision-making without disrupting workflows.
Value for process manufacturing
Predictive maintenance
Resource efficiency
Enhanced productivity
Accelerated product development
Strategic planning
Remote training and safety
Power Converter Monitoring
3D digital twin technology enhances power converter monitoring by creating a virtual copy that operates alongside the converter control system.
Power electronic converters operate in heavy loads and harsh environmental conditions, leading to system failures. Potential failure root causes are:
- operation mode beyond the physical capabilities of the components,
- long-term use depreciation.
The digital twin helps to anticipate component wear, ensure timely replacements and adjust equipment control.
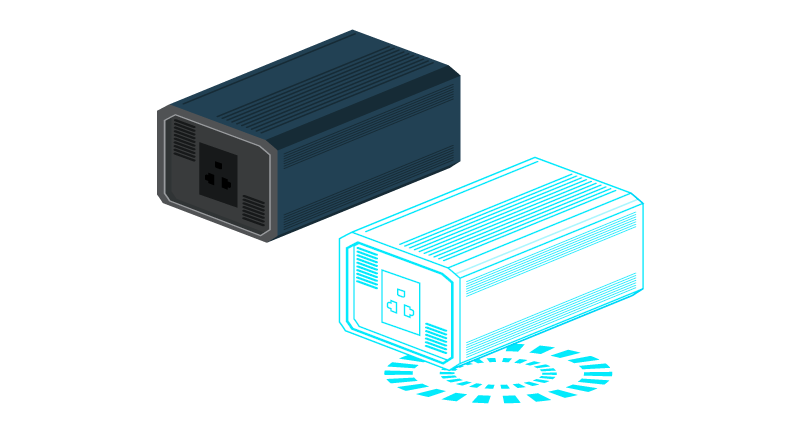
Key components
- Real systemt: The actual physical object or process.
- Digital twin: A virtual replica simulating the actual system's behaviour.
- Sensor feedback: It captures real-world voltage and current signals for the digital model.
- Data analysis: It examines similarities between the real and virtual systems.
- Actions: Interventions based on analytics aimed to optimise system performance.
Automotive Solutions Production
Digital twins enhance automotive production processes by ensuring:
- Virtual production line modelling: Use 3D digital twin technology to simulate the entire production line, from equipment to robots, ensuring seamless interaction.
- Efficient workflow simulation: Mirror various assembly scenarios – from component receipt to final assembly – for optimising processes.
- Virtual testing: Identify equipment compatibility issues and optimise production parameters, establishing quality and productivity.
- Scenario simulations: Simulate equipment failures or emergencies, evaluate system responses, and develop preventive measures.
- Real-time equipment integration: Monitor production equipment, comparing data with virtual models for analysis and adjustment.
- Predictive maintenance: Utilise sensor data to predict equipment conditions, enable timely interventions, reduce breakdowns, and enhance safety.
- Optimised production: Minimise production losses, offer recommendations for process optimisation, and improve delivery time forecasts.
- Condition monitoring: Integrate with automotive systems to predict component behaviours, facilitating proactive maintenance and issue prevention.
Water Supply Systems
Digital twins offer a digital representation of water supply systems, from individual components (e.g., pump or valve) and subsystems (e.g., water treatment plant or another facility) to an entire utility network.
Digital Twin Software Benefits
- Efficient planning and cost reduction: Virtual testing helps select components for water supply systems, decreasing development expenses and time.
- Real-time decision-making: The performance monitoring enables pump efficiency and water quality control for making timely operational decisions to extend asset life.
- Scenario analysis: Simulating various operational scenarios enhances emergency response, improves efficiency, and conserves energy.
- Hydraulic resiliency evaluation: Hydraulic modelling allows simulations of potential disruptions like pipeline failures or power outages.
- Predictive alerts: Continuous updates help predict system issues, triggering alerts for timely intervention by control units or dispatchers.
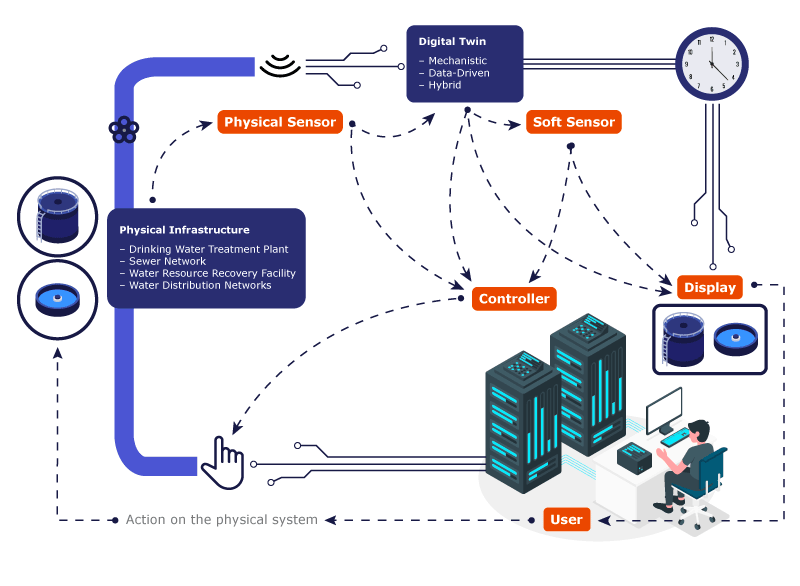
Do you want to enhance equipment reliability with our custom digital twin design services?
Drop us a line about your project! We will contact you today or the next business day. All submitted information will be kept confidential.