Top 7 Predictive Maintenance Trends Driven by IoT Solutions in 2025
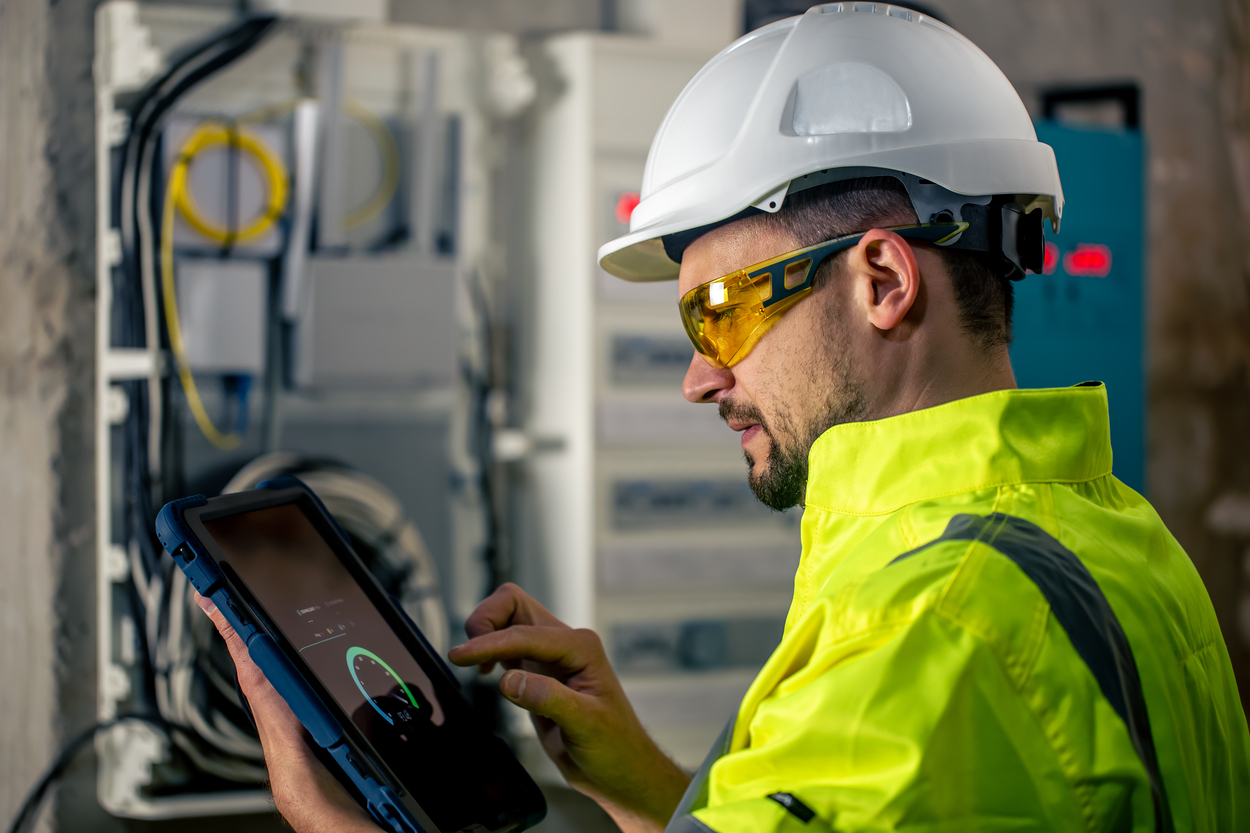
Predictive maintenance, powered by IoT solutions, is transforming how industries manage their assets, significantly reducing downtime and operational costs. By 2025, businesses across multiple sectors will increasingly leverage predictive maintenance strategies enhanced by IoT technologies to proactively address equipment issues, minimize failures, and enhance productivity.
Let's explore the top seven trends in predictive maintenance driven by IoT solutions that will define the next few years.
1. Expansion of IoT Sensors & Real-Time Monitoring
One of the key trends in predictive maintenance is the increased deployment of IoT sensors for real-time equipment monitoring. IoT sensors gather continuous data from various machinery, allowing businesses to proactively predict and address maintenance needs before critical failures occur.
Common IoT sensors for predictive maintenance include:
Sensor Type | Application | Data Collected |
Vibration Sensors | Rotating machinery, motors | Frequency, amplitude |
Temperature Sensors | HVAC systems, engines | Operating temperature |
Acoustic Sensors | Pumps, compressors | Sound frequency analysis |
Humidity Sensors | Electrical equipment, data centers | Moisture levels |
Pressure Sensors | Hydraulic systems, pipelines | Pressure variations |
According to Deloitte, companies adopting sensor-driven predictive maintenance can reduce unplanned downtime by up to 25%.
2. Increased Adoption of Edge Computing
Edge computing allows data processing directly at the point of data collection. For predictive maintenance, this significantly reduces latency, allowing faster decision-making and reducing the burden on cloud infrastructure.
Benefits of edge computing include:
- Real-time analytics: Immediate data processing and anomaly detection.
- Reduced bandwidth: Only relevant data is transmitted, optimizing network usage.
- Enhanced security: Less data sent over external networks means reduced cybersecurity risks.
IDC predicts that by 2025, nearly 50% of enterprise-generated data will be processed at the edge, significantly influencing predictive maintenance strategies.
3. AI and Machine Learning in Predictive Maintenance
Artificial intelligence (AI) and machine learning (ML) will play crucial roles in interpreting vast amounts of IoT sensor data. Advanced algorithms can detect patterns and predict equipment failures before they occur.
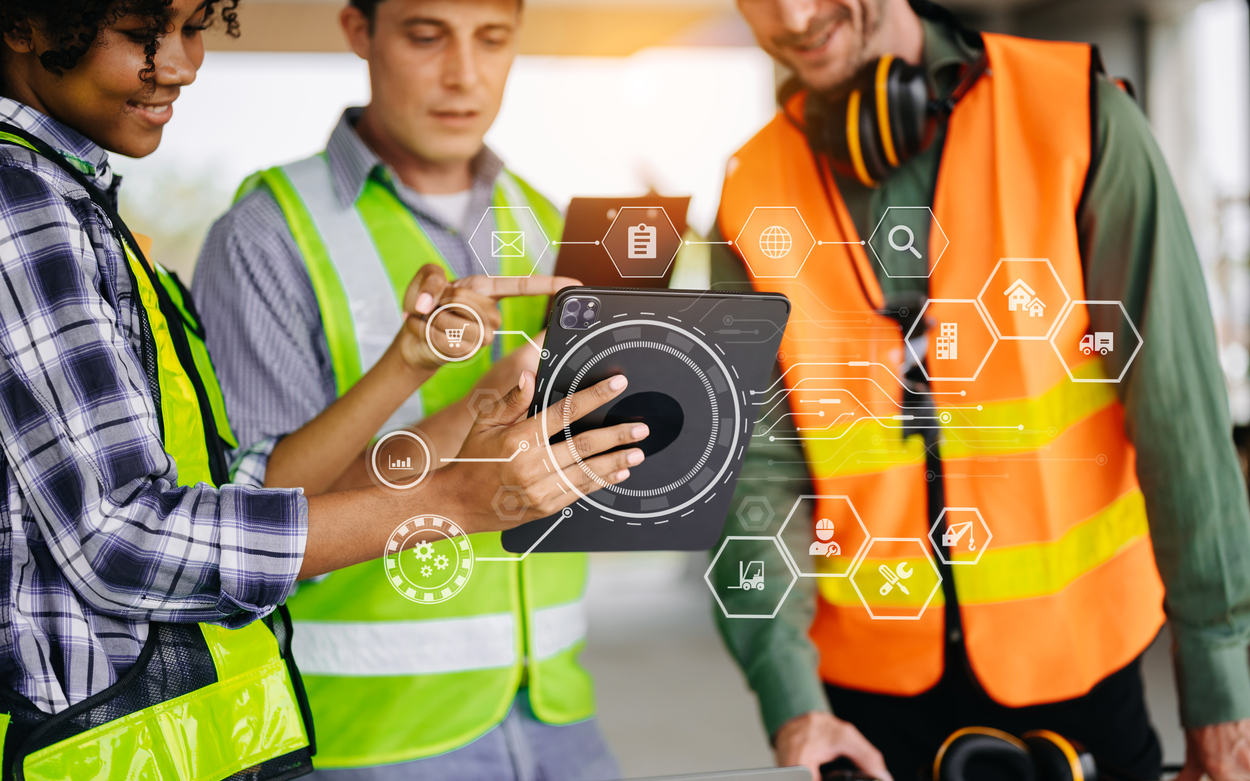
Key applications include:
- Anomaly detection: Quickly identify deviations from normal operations.
- Predictive modeling: Forecast equipment lifespan and maintenance intervals.
- Root cause analysis: Automatically diagnose underlying problems.
Gartner forecasts that by 2025, companies utilizing AI-driven predictive maintenance will achieve a 10–20% reduction in maintenance costs.
4. Digital Twins for Enhanced Predictive Insights
Digital twins, virtual replicas of physical assets, are revolutionizing predictive maintenance by offering simulation capabilities and deeper insights into equipment performance.
Digital twins allow:
- Real-time asset monitoring and simulations
- Predictive scenarios to optimize maintenance schedules
- Remote diagnosis and troubleshooting
GE Digital estimates digital twins could cut downtime by 30%, significantly boosting operational efficiency.
5. Integration with Augmented Reality (AR)
Augmented reality is increasingly utilized to assist technicians during maintenance procedures. IoT predictive maintenance data combined with AR glasses helps streamline complex tasks and repairs, minimizing human errors.
Advantages of AR in maintenance:
- Hands-free visualization of IoT sensor data
- Guided step-by-step procedures in real-time
- Remote expert assistance, improving accuracy and safety
According to ABI Research, AR adoption in industrial maintenance will increase by 66% annually until 2025.
6. Predictive Maintenance-as-a-Service (PdMaaS)
The Predictive Maintenance-as-a-Service model offers companies the flexibility to adopt predictive maintenance solutions without large upfront investments. IoT-enabled PdMaaS providers handle data analytics, asset monitoring, and issue alerts remotely.
Advantages include:
- Reduced capital expenditure
- Easy scalability across multiple facilities
- Access to cutting-edge technologies without internal expertise
Market Research Future expects the global PdMaaS market to grow at a CAGR of 28% through 2025.
7. Emphasis on Cybersecurity for IoT Devices
As IoT adoption grows, protecting IoT sensors and data from cyber threats is increasingly critical. Predictive maintenance data, which can be sensitive and business-critical, requires robust cybersecurity measures.
Key cybersecurity measures:
- Secure IoT device authentication
- End-to-end encryption of data transmissions
- Regular security audits and firmware updates
The cybersecurity market for IoT is projected by MarketsandMarkets to reach $36.6 billion by 2025, highlighting its growing importance.
Real-Life Industry Examples of IoT-Enabled Predictive Maintenance
Here are some successful real-world implementations showcasing predictive maintenance benefits:
Company | Industry | Results |
Rolls-Royce | Aerospace | Reduced engine maintenance costs by 30% using IoT sensor data and digital twins. |
ThyssenKrupp | Elevator Maintenance | Improved service reliability by 50% through IoT-connected predictive maintenance. |
Shell | Oil & Gas | Decreased equipment downtime by 20% using sensor-driven predictive analytics. |
Expert Opinions
“Predictive maintenance empowered by IoT data is no longer optional—it’s essential for companies aiming to remain competitive and cost-effective,” — Kevin Ashton, technology pioneer who coined the term "Internet of Things."
“Adopting IoT-based predictive maintenance allows businesses to transform reactive practices into proactive strategies, significantly enhancing operational efficiency,” — Michael E. Porter, Harvard Business School professor.
Promwad's Role in IoT Predictive Maintenance
Promwad provides comprehensive IoT solutions, assisting businesses in adopting predictive maintenance strategies effectively:
With expertise in embedded hardware, software development, and IoT connectivity, Promwad helps businesses harness predictive maintenance for maximum operational efficiency.
Conclusion
By 2025, predictive maintenance driven by IoT will profoundly transform industries, reducing costs, increasing reliability, and enhancing competitive advantage. Businesses that proactively adopt these top trends will position themselves as industry leaders, driving efficiency and growth through innovative IoT solutions.
Stay informed and leverage predictive maintenance to its full potential.