Contract Manufacturing vs. OEM In-House Production: What’s Better in 2025?
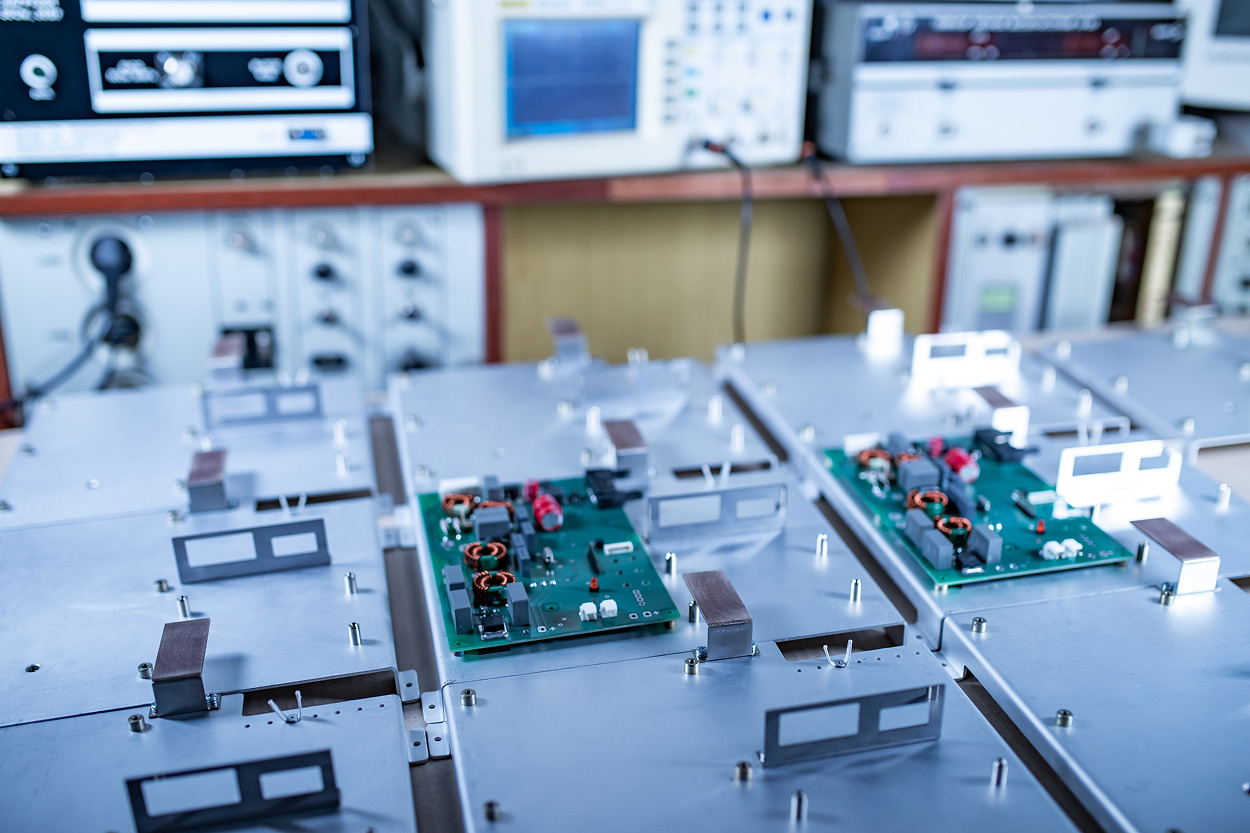
Getting Started: The Manufacturing Model Dilemma
As electronics products grow more complex and supply chains remain volatile, companies are reassessing whether to keep production in-house or outsource to contract manufacturers (CMs/EMS providers). Both approaches have trade-offs in 2025—especially when time-to-market, quality control, and global logistics are at stake.
In this guide, we break down the benefits, risks, and ideal use cases for contract manufacturing vs. in-house production so you can choose the right model for your business.
What is Contract Manufacturing?
Contract manufacturing (CM), or working with Electronics Manufacturing Services (EMS) providers, means outsourcing the entire or partial product assembly process to a third party.
Typical services include:
- PCB assembly and testing
- Component sourcing and logistics
- Box-build and system-level integration
- Quality control and certifications
What is In-House Production?
In-house production refers to a company manufacturing its own electronics, typically under the OEM’s (original equipment manufacturer) control. This includes:
- Operating internal SMT lines and test stations
- Managing material procurement
- Building internal quality assurance teams
- Hiring and training production staff
Side-by-Side Comparison: CM vs. In-House
Criteria | Contract Manufacturing | In-House Production |
Upfront Investment | Low – Pay per unit or NRE fees | High – Facility, equipment, staffing |
Scalability | High – Rapid ramp-up with partner capacity | Limited – Dependent on internal resources |
Time-to-Market | Faster with experienced EMS | Slower – learning curve and ramp-up |
Supply Chain Access | Strong – EMS has existing networks | Weak – needs building from scratch |
IP & Confidentiality | Risk with external access | Full internal control |
Customization Control | May be limited by EMS capabilities | Full flexibility in process engineering |
Compliance & Certifications | Provided by EMS (ISO, IPC, etc.) | Requires in-house expertise |
Ongoing Costs | Variable – scalable with volume | Fixed – regardless of order volumes |
When to Choose Contract Manufacturing
- You’re launching a new product and need speed
- Your team lacks production infrastructure
- Your BOM involves complex sourcing and global logistics
- You want to leverage existing quality and testing processes
- You need certifications like ISO 13485, IATF 16949, or ITAR quickly
Example: A startup launching a wearable medical device opts for a turnkey EMS in Eastern Europe, achieving CE compliance and shipping in under 6 months.
When to Choose In-House Production
- You produce high-margin, low-volume custom electronics
- You require full IP protection for regulated products
- You want to invest long-term in process innovation
- You need close R&D and manufacturing integration
Example: An OEM producing defense-grade RF modules establishes its own cleanroom line to meet ITAR and NDAA sourcing rules.
Trends Influencing the Decision in 2025
- Rising labor & energy costs: Fuel the move toward outsourcing in high-cost regions
- Geopolitical shifts: OEMs are nearshoring to Eastern Europe and Mexico
- IP & security concerns: Push some companies to retain critical production steps in-house
- Smart factories & automation: Make in-house feasible for select use cases
Real-World Example: Scaling a Connected Device with a Hybrid Strategy
A mid-size European company developing smart home security systems faced a dilemma: continue in-house prototyping or expand quickly with external help. Their concern? Maintaining control over security protocols while entering three markets within one year.
Promwad’s Solution:
- Retained in-house assembly for encrypted modules to protect sensitive IP
- Outsourced plastic housing and final assembly to EMS partners in Lithuania and Vietnam
- Set up mirrored test procedures between internal and external production lines
Results:
- Time-to-market reduced by 40%
- Regional cost optimization led to 18% savings
- Full control over core firmware and secure elements was preserved
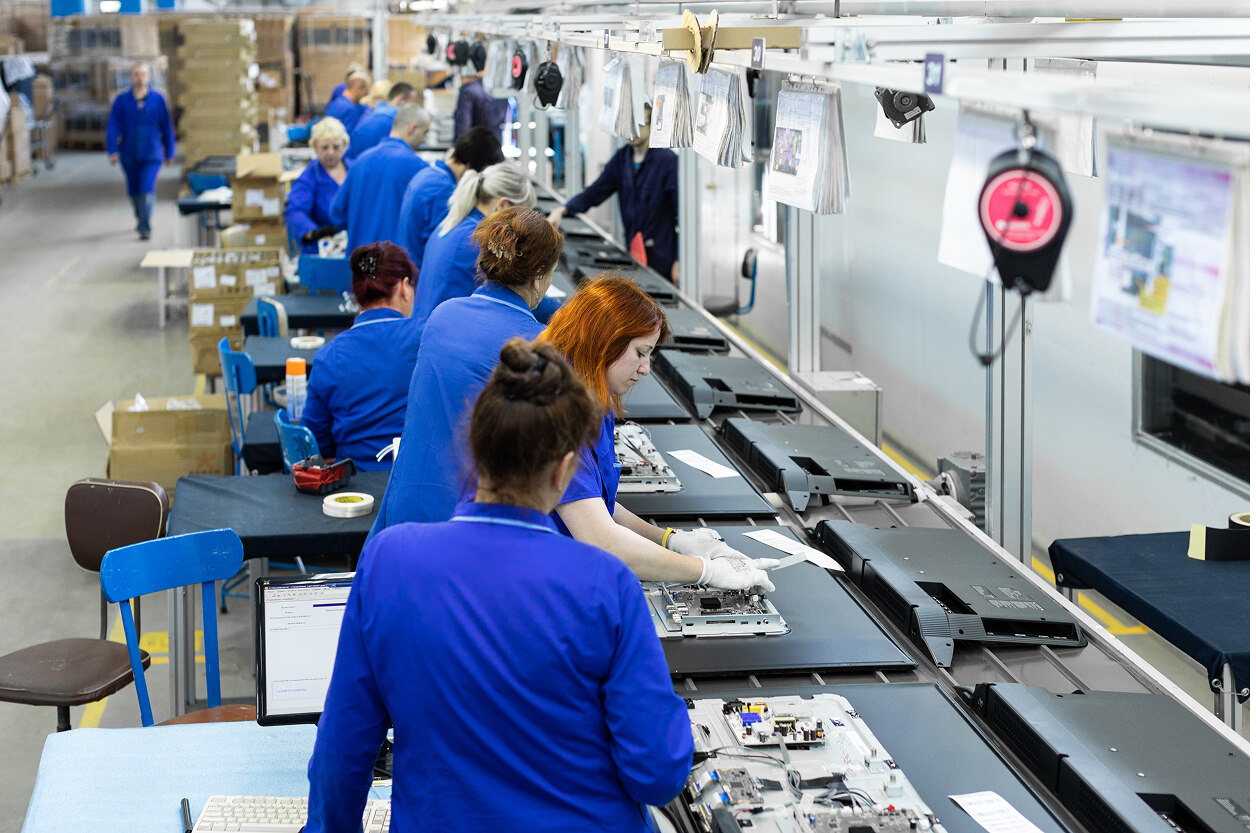
Promwad’s Perspective: Hybrid is the Future
We increasingly see OEMs blending both models. For example:
- Early prototyping and pilot runs in-house, mass production outsourced
- In-house test development, but box-build at EMS partners
- Dual-region manufacturing: critical parts locally, rest offshore
At Promwad, we support clients with:
- EMS partner selection and onboarding
- In-house/outsourced process analysis
- DFM/DFT optimization and transfer documentation
- Production transition support
Final Thoughts: Choose What Scales With You
There’s no one-size-fits-all approach. Contract manufacturing gives you speed, scale, and access to advanced capabilities. In-house production grants you control, privacy, and long-term innovation leverage.
The key is to align your choice with your stage of growth, compliance needs, and business goals. In 2025, flexibility is everything — and with the right partner, you don’t have to choose just one path.
Our Case Studies in Electronics Manufacturing