Smart Wireless Thermostats: Design & Manufacturing
Project in Nutshell: We helped a company in the construction industry significantly reduce the cost of purchasing and installing thermostats for multi-unit apartment buildings by designing and manufacturing their custom wireless device. Initially, our client used expensive wired solutions with complex installation (1,000+ devices per building).
Our estimates showed that launching the design and manufacturing of a custom wireless device would pay for in just two years!
Client & Challenge
Our client, a North American building contractor, specialises in installing security and ventilation systems in large apartment blocks with hundreds of flats and 1,000+ sensors per building. The cost of purchasing and installing ready-made wired sensors was a significant part of the budget.
The company considered buying cheaper foreign analogues as a solution, but they did not meet specific regional requirements for certification. This is how the hypothesis arose that developing a proprietary wireless thermostat could solve the problem of the high cost of purchasing and installing.
As a result, the client chose Promwad because our expertise allowed us to verify this hypothesis, make the necessary calculations, and develop a turnkey device.
Solution
Promwad calculated the cost of design and manufacture of wireless thermostats with a given production volume, considering the reduction in the cost of wiring and installation. The preliminary calculation showed that the project costs would be recouped within two years, so we decided to start the development together with the client, collaborating on a time & materials model.
We developed a turnkey solution, including thermostat design, unified hardware design, firmware development, Linux-based gateway software development, and the first pilot batch manufacturing. To do this, we built a team consisting of:
- industrial and mechanical designers;
- PCB design engineers:
- software and firmware engineers.
1. Concept Development
During the planning phase, we determined that the product would consist of a thermostat, gateway, control software, and firmware. The device must be wireless, so our engineers chose a wireless mesh network compliant with IEEE 802.15.4.
The advantage of controlling wireless smart thermostats via the gateway is efficiency: one gateway can serve up to 20 thermostats. Rather than connecting each thermostat directly to the network, all of them can communicate via the gateway. This simplifies network management and saves energy consumption.
2. Hardware Development
We developed a universal board for the gateway and thermostat, significantly reducing the cost of developing and debugging the RF part. The versions of the board for the thermostat and the gateway differ only in the set of installed components.
Our gateway solution was based on the Raspberry PI 4B 4 SoC and a universal board that acts as a wireless network processor, which is connected to each thermostat on a mesh network via industrial communication protocols. This ensured the smooth operation of the thermostats in the single climate control system.
The hardware of the wireless thermostat has such features as:
- isolated power supply from one of two power sources (AC/DC);
- an enclosure с buttons and a display with controlled backlight;
- measurement of ambient temperature and humidity;
- CO2 measurement (optional);
- control of 9 discrete outputs from the selected power source — for climate, heating, cooling, and ventilation.
For wireless data transmission, we used a microcontroller from Texas Instruments.
Also, we chose a monochrome backlit graphic display for clear information display even in daylight.
3. Software Development
We took care of all stages of software development, including wireless communication blocks, display and sensor drivers, and a UX design for the screen. All software and related documents were stored in GIT repositories, following GIT flow practices.
For the gateway software, we utilized Docker containers for building the Linux OS image and Yocto as the system for building it. To develop the gateway software, we used the C++ language (C++14) with the Cmake build system and integrated third-party libraries including:
- dbus-lib for communication between multiple processes;
- spdlog for logging in C++;
- wpantund for management and wireless network interfaces.
We also wrote the firmware for the thermostat in C++, using an existing architecture that allows parallel development. Our engineers implemented the firmware using the TI-RTOS real-time operating system.
SQLite served as our data storage solution, and JSON messages facilitated component interaction via dbus, with a multi-level logging system implemented using the spdlog library.
Before commencing development, a state diagram for the thermostat's human-machine interface was crafted to outline the user interaction cycle.
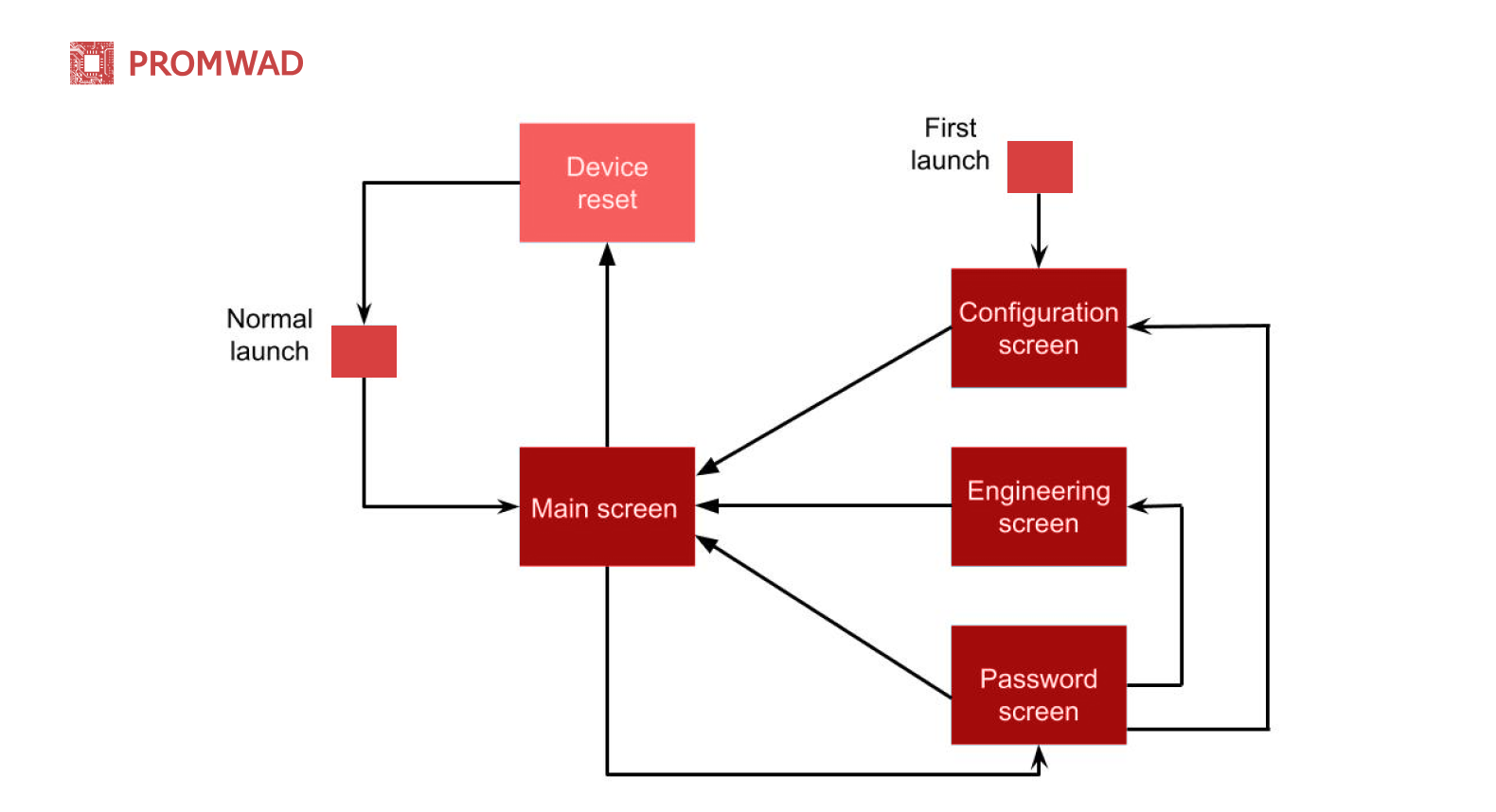
General HMI state diagram
4. Enclosure and mechanical design
In smart thermostat design, we have focused on modern industrial styling, ease of assembly, and tamper protection. The thermostat enclosure consists of two parts with service access, which are secured with a security screw.
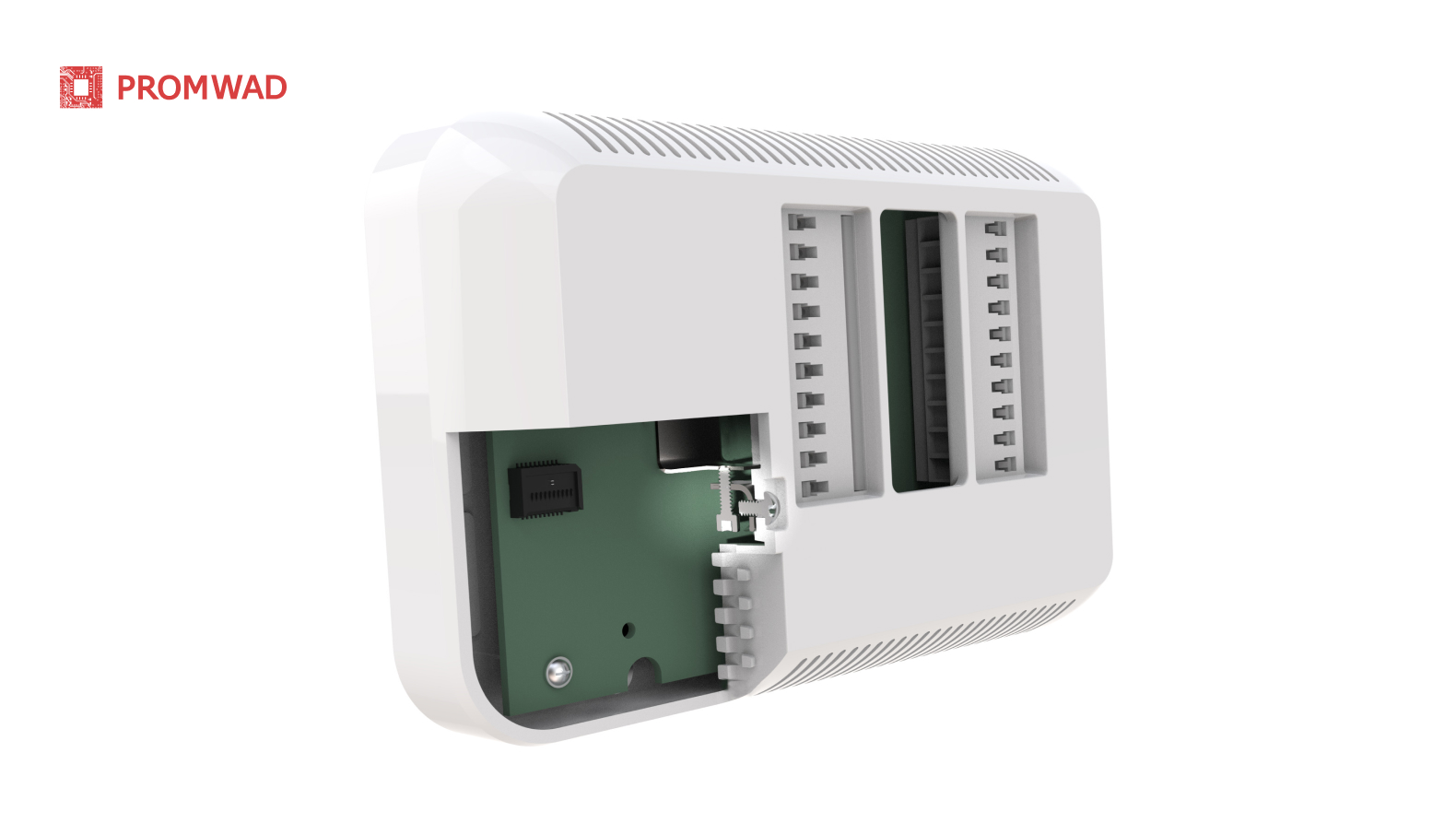
The bottom part of the thermostat enclosure
The lower part of the enclosure contains terminal blocks, a mounting bracket, and engraved terminals. The upper part contains a monochrome display, a universal PCB with control buttons, a CO2 sensor, and an antenna.
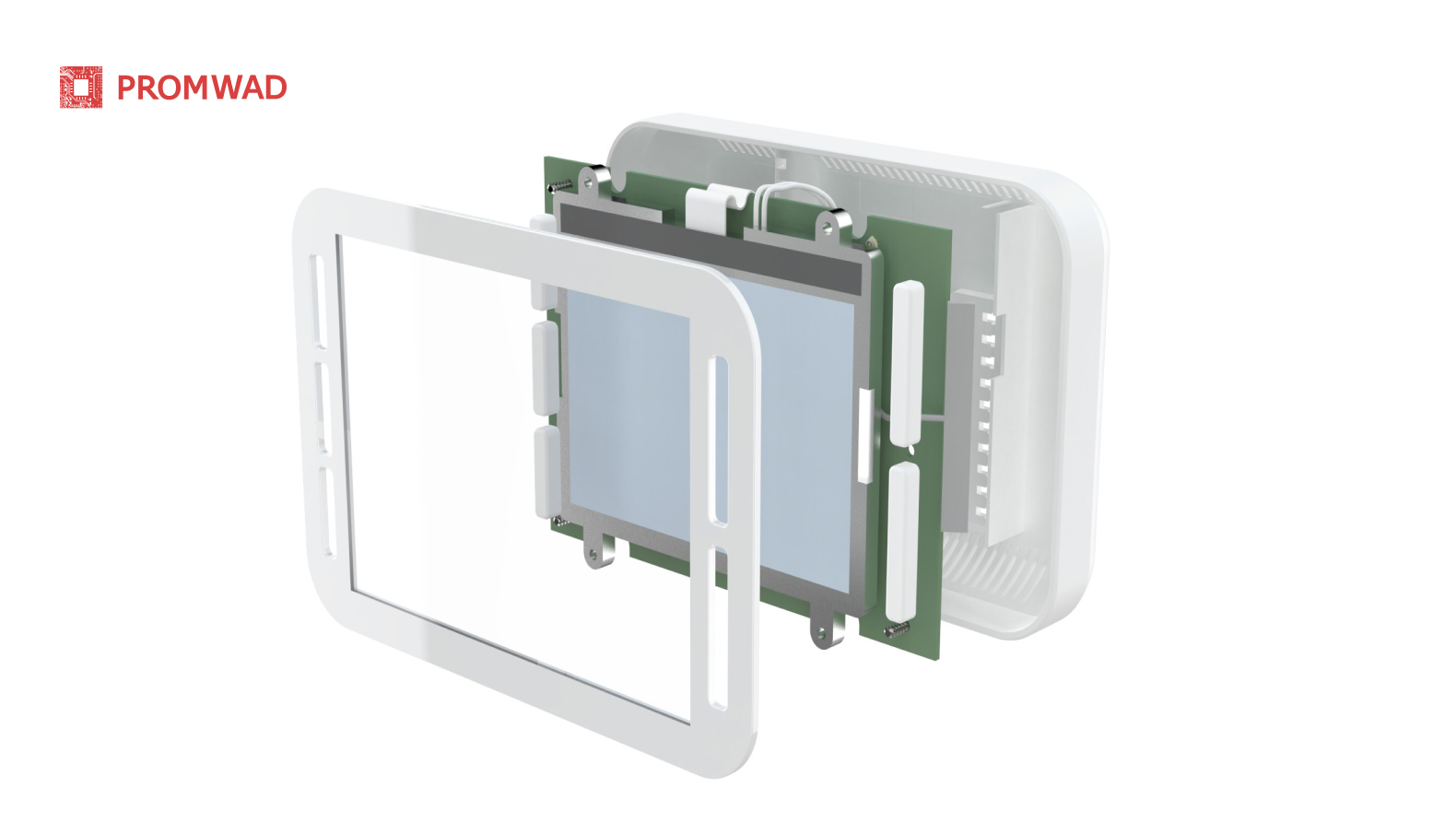
The prototype with a board layout
When designing the plastic enclosure, we analysed the filling of the mould to identify possible defects (sink marks, weld lines, and warping of parts) during plastic moulding.
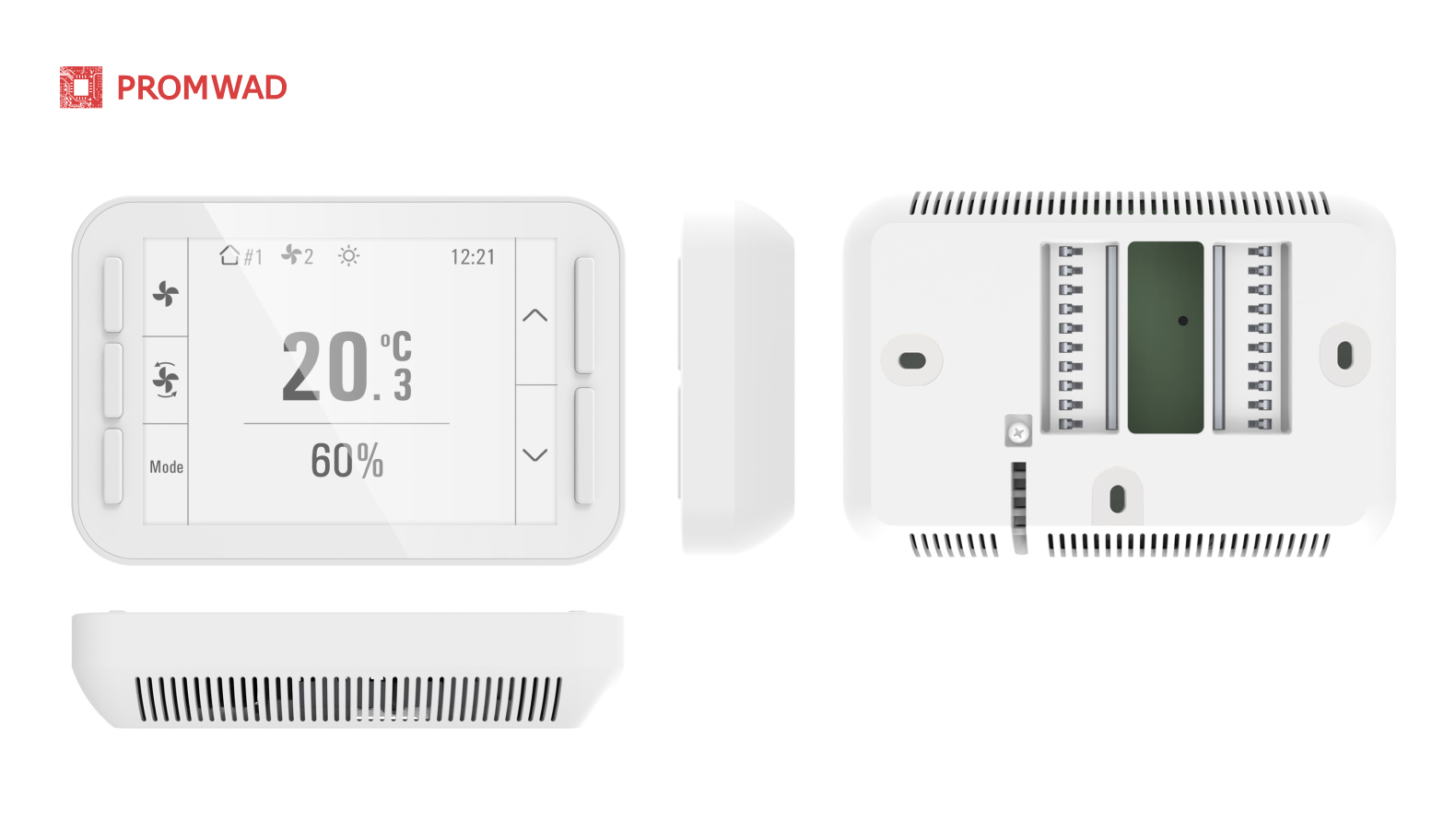
The second prototype of the wireless thermostat
The first prototype, built with 3D printing, allowed us to test the enclosure assembly, and then we made adjustments to improve the alignment of the top of the enclosure and the buttons. The second prototype was injection moulded using a silicone mould, which allowed us to test the functionality of the thermostats in the climate control system.
The gateway enclosure meets the IP54 standard for moisture resistance and is designed for easy assembly and maintenance.
Business Value
Our client received a proprietary mass-produced wireless thermostat that successfully passed certification confirming the compliance with regional safety and quality standards.
A batch of 1,000 is now in the production phase to equip the first building. Our team provides consultancy support for production on request.
As a result, our customer will have his own certified device to:
- to reduce labour and material costs by switching from wired to wireless smart thermostats (costs will be recovered within two years);
- to reduce installation time for the thermostats;
- to increase the efficiency of solutions by integrating advanced hardware and software components such as wireless mesh networks and real-time operating systems.
More of What We Do for Consumer Electronics
- Custom Enclosure Design: learn more about how we develop enclosures for electronic devices and embedded systems.
- Design of Game Device: a case study with a breakdown of the enclosure design process for a minimalistic and ergonomic gaming console.
- Home Air Quality Monitor: a case study on the development of a wearable IAQ monitor to monitor indoor pollution, temperature, and noise levels.