Digital Transformation in Manufacturing: From Idea to Implementation
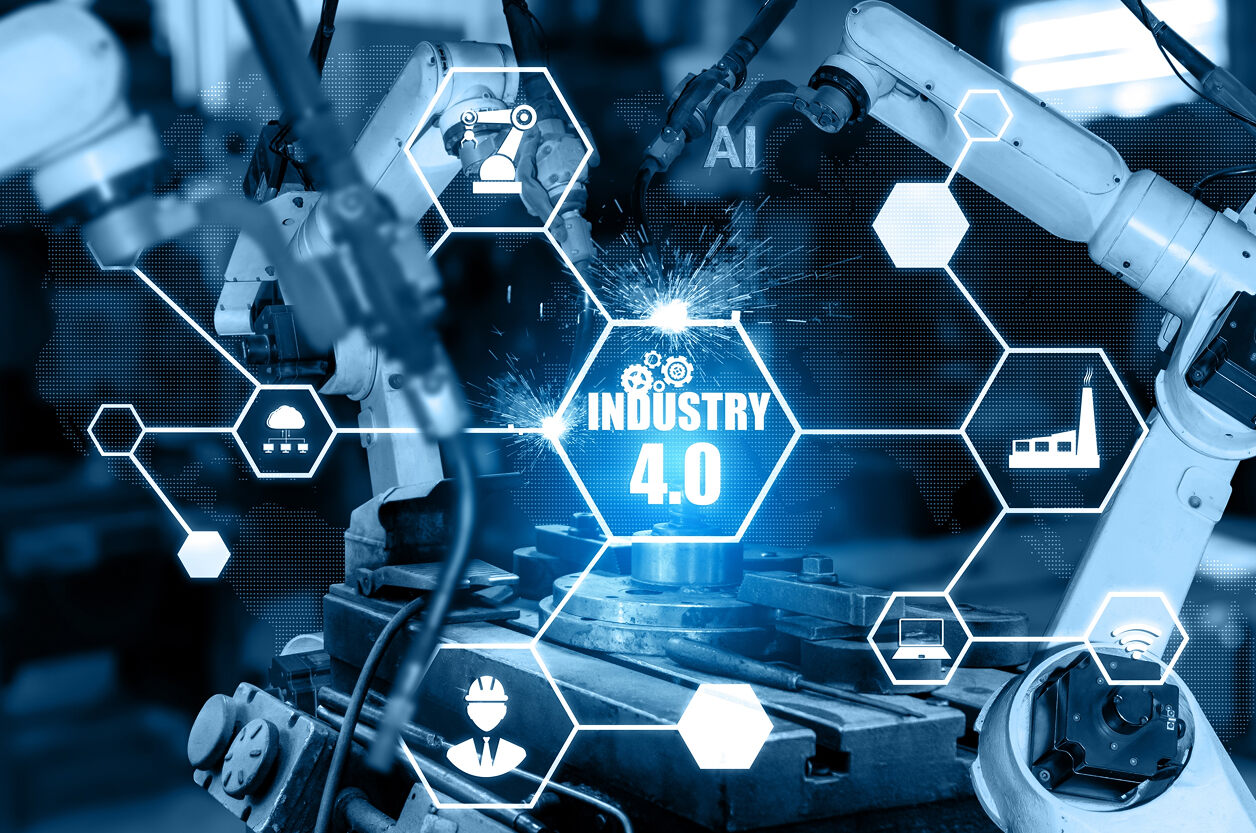
Digital transformation has moved from buzzword to competitive necessity in the manufacturing sector. Global supply chain disruptions, rising energy costs, and the push for more sustainable operations have all accelerated the adoption of Industry 4.0 initiatives. But moving from initial idea to a fully integrated digital operation is a major engineering and organizational challenge.
In this article, we’ll explore the key technologies that drive digital transformation in manufacturing, typical pitfalls companies face, and engineering best practices to turn pilot projects into scalable, resilient solutions.
What Does Digital Transformation Mean in Manufacturing?
Digital transformation in manufacturing is more than installing a few sensors on machines. It’s about connecting assets, automating decision-making, and optimizing processes across the entire value chain.
This often involves:
- Equipping machines and production lines with IoT sensors for real-time data.
- Integrating shop-floor systems with enterprise software (ERP, MES, PLM).
- Using machine learning to predict failures or optimize scheduling.
- Applying digital twins to model processes and test improvements virtually.
- Enabling remote monitoring and even remote service interventions.
Key Technology Pillars of Digital Manufacturing
Industrial IoT (IIoT)
Sensors collect data on machine states, environmental conditions, energy use, and product quality. Protocols like OPC UA, MQTT, and TSN enable secure, low-latency data flows.
Advanced Analytics and AI
AI models forecast demand, optimize maintenance schedules, and detect anomalies in real-time production data. Predictive maintenance minimizes downtime while improving resource allocation.
Digital Twins
Virtual models of machines or whole production lines allow “what-if” simulations. Engineers can test process changes digitally before modifying physical systems.
MES and ERP Integration
Manufacturing Execution Systems (MES) link production with planning. Seamless MES-ERP integration enables dynamic scheduling, quality tracking, and cost optimization.
Edge Computing
Local processing reduces latency and bandwidth. For example, inspecting products with machine vision directly on the line, rather than uploading all data to the cloud.
Challenges in Implementing Digital Transformation
Legacy Equipment
Older machines may lack connectivity. Retrofitting requires protocol converters or edge gateways.
Data Silos
Different departments often use incompatible systems, blocking end-to-end visibility.
Change Management
Digital initiatives often fail due to lack of operator buy-in or resistance from middle management.
Security Risks
More connected assets increase attack surfaces. Secure protocols, segmentation, and continuous monitoring are essential.
From Pilot to Scale: How to Execute Successfully
Start with a Clear Business Case
Is the goal to reduce downtime by 20%? Cut energy costs by 15%? Improve product traceability?
Quantify potential ROI before technology decisions.
Build Cross-Functional Teams
Digital transformation is not just IT. It needs operations, maintenance, engineering, and financial stakeholders aligned.
Use Modular Architectures
Deploy modular IoT platforms and analytics so you can start small and scale. Avoid monolithic solutions that lock you in.
Ensure Interoperability
Select vendors and integrators that support open standards like OPC UA, MQTT, and REST APIs. This future-proofs investments.
Plan for Security from the Start
Use zero-trust principles. Segment OT from IT networks, implement device authentication, and monitor traffic for anomalies.
Long-Tail Technical Questions and Answers
How do you connect legacy CNC machines to digital systems?
Use edge gateways that can read data over RS-232, Modbus, or proprietary protocols, then translate to MQTT or OPC UA for higher-level systems.
What is the role of a digital twin in manufacturing?
A digital twin replicates physical assets or processes in software. It enables predictive maintenance, process optimization, and rapid experimentation without risking live production.
Can you do AI directly on the factory floor?
Yes. Edge computing platforms run ML models for tasks like visual inspection or predictive maintenance without sending data to the cloud, reducing latency and bandwidth.
How does cybersecurity change in Industry 4.0?
Every connected sensor or gateway is a potential attack point. Use network segmentation, device certificates, and continuous threat monitoring.
Why do so many digital projects fail after pilots?
Often due to poor integration with existing workflows, underestimated change management, or lack of ROI tracking. Sustainable programs link metrics directly to financial or operational KPIs.
Future Trends in Digital Manufacturing
Hyper-Personalized Production
Flexible production lines driven by real-time demand data will allow mass customization at scale.
Autonomous Decision-Making
Combining AI, MES, and ERP means systems can autonomously schedule, reallocate, and even order spare parts without human intervention.
Sustainability Dashboards
Integrated data from energy meters, process sensors, and supply chain will provide carbon dashboards — critical for meeting ESG targets.
5G on the Shop Floor
Private 5G networks enable reliable low-latency connectivity for AGVs, robots, and mobile inspection units.
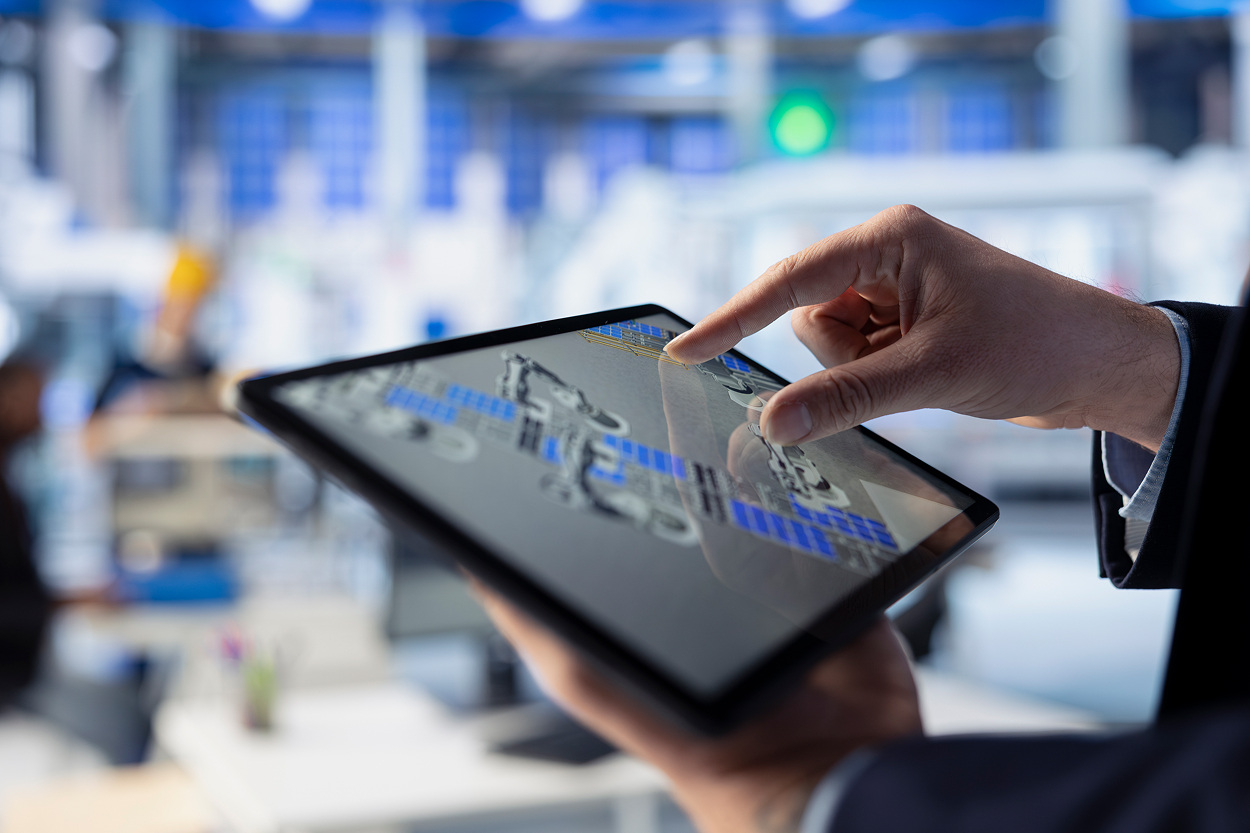
Practical Example: A Factory Going Digital
A mid-sized electronics manufacturer started by:
- Retrofitting old pick-and-place machines with OPC UA gateways.
- Feeding production data into a lightweight MES.
- Using an AI tool on edge servers to predict solder defects based on paste thickness and humidity.
This reduced defect rates by 18% in six months, delivering measurable ROI that justified extending the project plant-wide.
Conclusion: Engineering the Future of Manufacturing
Digital transformation in manufacturing is not a one-time IT project. It’s a multi-year evolution involving hardware, firmware, network engineering, and business process rethinking.
From designing retrofit IoT modules and secure edge compute to integrating machine learning with MES/ERP, Promwad helps industrial companies build digital ecosystems that deliver real savings and new business capabilities.
If your production environment needs smarter, more resilient systems, let’s talk about how to bring your digital roadmap to life — from pilot to global scale.
Our Case Studies