The Future of Contract Manufacturing: Modular, Local, Automated?
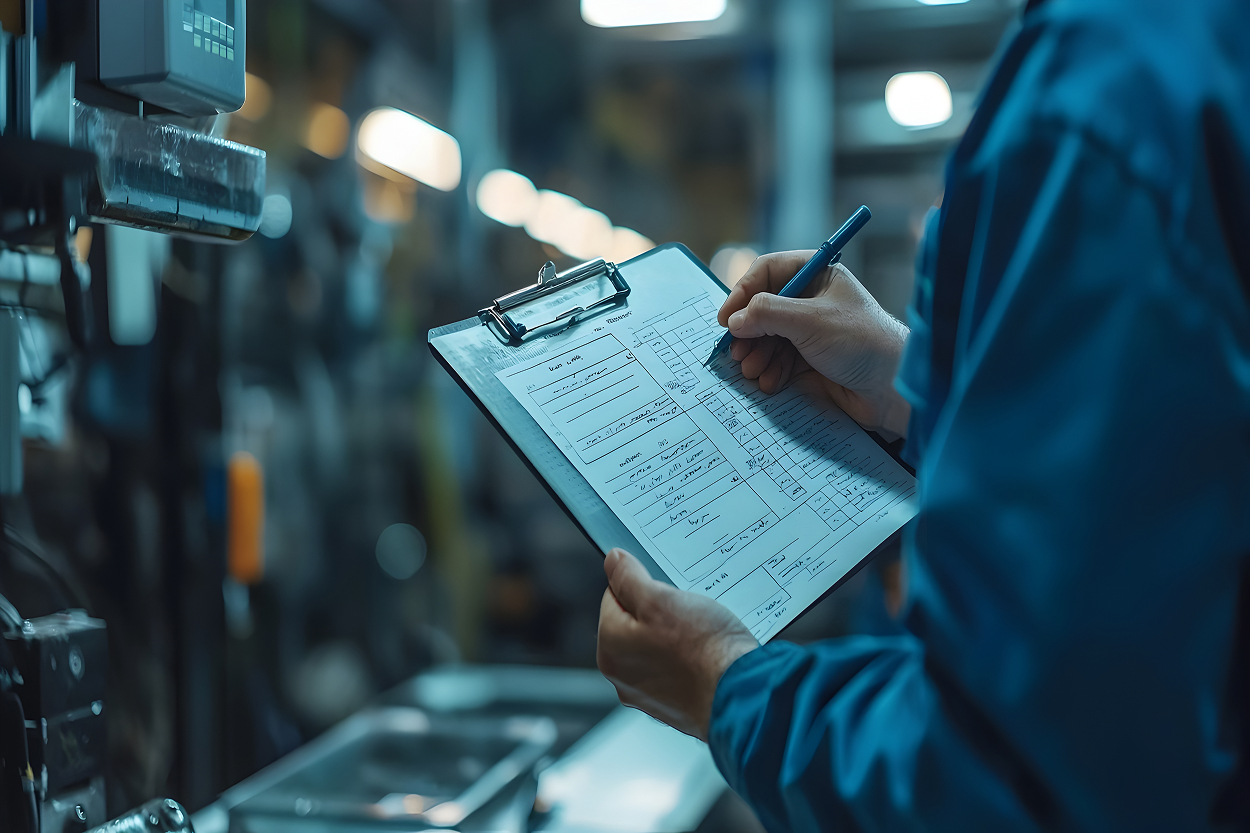
Getting Started: Why Contract Manufacturing Is Evolving
Contract manufacturing (CM), long valued for its cost-efficiency and scalability, is undergoing a transformation. OEMs now seek greater resilience, shorter lead times, and localized production options. The global events of the past years — from semiconductor shortages to geopolitical shifts — have only accelerated this evolution.
What does the future of contract manufacturing look like between 2025 and 2035? The answer lies in a modular, local, and highly automated model that prioritizes flexibility over volume alone.
Key Drivers of Change in EMS
- Disrupted supply chains → Need for local/regional redundancy
- Component scarcity → Agile BOM management and substitutions
- Talent shortages → Demand for automation in labor-intensive processes
- Sustainability goals → Pressure to reduce logistics emissions and waste
- Customization → Shift from mass production to configurable, smaller batches
1. Modular Manufacturing: Flexibility at Scale
What is it?
A production model built on interchangeable, reconfigurable units (lines, jigs, software, supply modules) that can be quickly adapted to product variants or new clients.
Benefits:
- Faster NPI (New Product Introduction)
- Cost-effective production of multiple SKUs
- Reuse of test setups and hardware blocks
Enablers:
- Standardized production cells and test stations
- Modular software and digital twins for line setup
- Plug-and-play fixture systems
Example: An EMS partner serving five medtech startups reuses 70% of its functional test and SMT processes across product lines.
2. Localized Production: Reducing Risk and Lead Times
Trend:
Brands are moving closer to their markets. From Eastern Europe to North America, OEMs want shorter transport routes, faster prototyping, and reduced customs exposure.
Impacts:
- Nearshoring in EU (Lithuania, Serbia, Poland) and North America (Mexico, Texas)
- Rise of microfactories and regional EMS nodes
- Local fulfillment for logistics-sensitive sectors (e.g. EV, healthcare, wearables)
Promwad Insight: In 2024–2025, we observed a 40% increase in client requests for dual-region manufacturing strategies that combine Asia with the EU or LatAm.
3. Automation: The Smart Factory Revolution
Evolution:
Factories are moving beyond basic robotics to include:
- Machine vision-based inspection
- Automated traceability and ERP integration
- AI-based scheduling and predictive maintenance
Value:
- Higher yield, lower rework rates
- Real-time production monitoring
- Less dependence on manual labor in high-cost regions
Case Example: A smart EMS facility in Germany reduced first-pass failure rates by 22% after implementing AI-driven visual inspection lines.
4. Software-Defined Manufacturing
A key element of the future is software-led orchestration of the factory:
- Cloud-based MES (Manufacturing Execution Systems)
- Remote line setup and recipe management
- Cross-site data analytics and traceability
This allows for centralized product configuration, decentralized production, and dynamic routing of jobs to the most available site.
5. Sustainable and Circular Manufacturing
As regulation and consumer pressure mount, CMs are adapting:
- Low-impact material sourcing
- Waste tracking and energy reporting
- Support for product reuse, refurbishment, and recycling
Examples:
- Recyclable PCB substrates
- DPP (Digital Product Passport) support
- Take-back integration for consumer electronics
Comparative Table: Future EMS Attributes vs. Traditional Model
Feature | Traditional EMS Model | Future EMS Model (2025–2035) |
Location Strategy | Offshore, centralized | Distributed, local + global |
Batch Size Focus | High-volume, low-mix | Low-volume, high-mix (flexible) |
Automation Level | Manual + robotic arms | AI-driven, fully automated |
Engineering Collaboration | Limited, on-site | Remote-first, platform-integrated |
Environmental Compliance | Basic RoHS/REACH | Lifecycle reporting + circularity |
Test and QC | Manual + basic ICT | Vision, software-controlled, modular |
Promwad’s Role in Modern EMS Enablement
Promwad collaborates with forward-thinking EMS providers and OEMs to implement:
- Modular fixture and test strategies across products
- Transfer-ready design documentation and DFM/DFT
- Localized supply chains and dual-region sourcing models
- Digital tools for managing production scalability
Whether you manufacture in Eastern Europe, Asia, or the Americas, we help ensure consistency, quality, and long-term adaptability.
Expert Insight: Industry Voices on EMS 2030
“EMS used to be about cutting costs. Now it’s about reducing risk, increasing flexibility, and keeping up with innovation cycles.”
— Carlos Medina, Head of Global Ops, FutureBuild Systems
“AI is not replacing people in EMS—it’s letting us scale smarter, automate quality, and compete globally without raising costs.”
— Irina Valkova, Automation Lead, Promwad Partner Factory, Vilnius
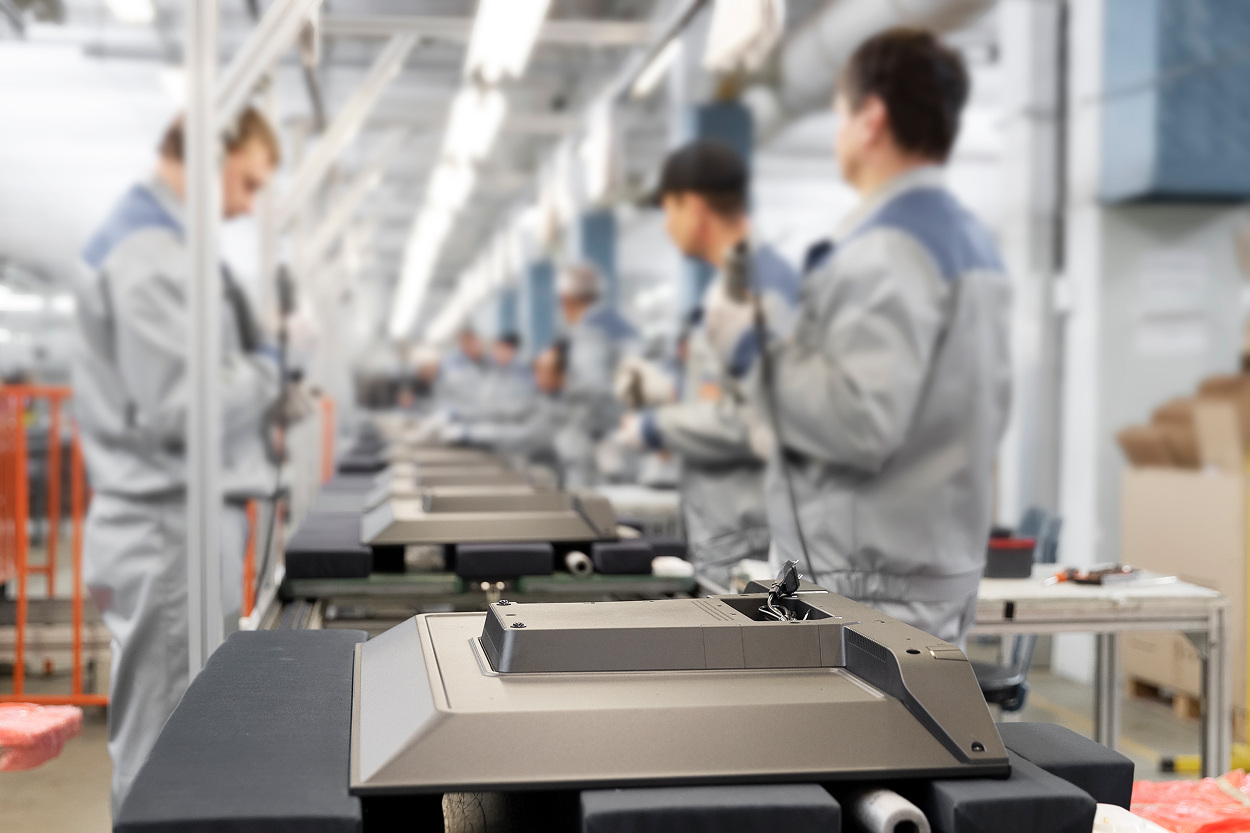
Additional Case Study: Scaling Industrial IoT Production with Modular EMS
A European industrial OEM was preparing to launch a fleet of smart energy meters across several countries. They needed a scalable and cost-effective EMS strategy that wouldn’t compromise on quality, certifications, or speed.
Challenges:
- Manufacturing in two separate regions (EU and SEA)
- Diverse certification needs (CE, FCC, UKCA)
- Managing SKU variants with similar core components
Promwad’s Role:
- Designed modular PCBs and test interfaces across all SKUs
- Worked with two EMS partners to establish mirrored production lines
- Enabled real-time test data syncing and analytics for QA compliance
Results:
- Production time per SKU reduced by 27%
- Lead time from PO to shipment dropped by 33%
- First-pass yield consistently above 97.5% across both regions
Final Thoughts: Time to Rethink EMS
The next decade of contract manufacturing will reward companies that prioritize adaptability. Modular design, local agility, and smart automation aren’t just industry buzzwords—they’re the new foundation for high-performing, resilient EMS partnerships.
At Promwad, we help you find and shape the EMS ecosystem that grows with your business, not against it.
Let’s design for what’s next—modular, local, and intelligent.
Our Case Studies in Electronics Manufacturing