Future of Smart Manufacturing: AI, Robotics, and Beyond
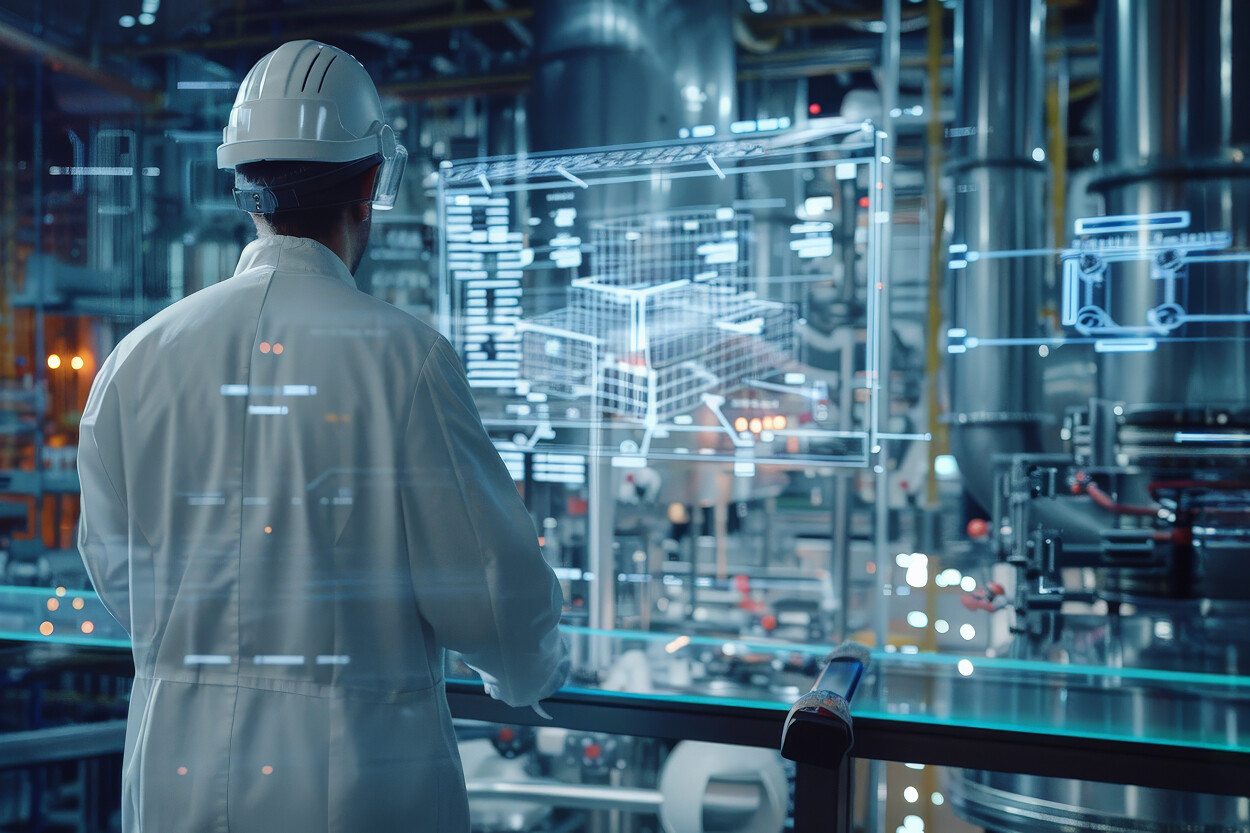
Getting Started: Why Smart Manufacturing Is Entering a New Era
Smart manufacturing is no longer a buzzword — it’s a competitive necessity. In 2025 and beyond, the convergence of AI, advanced robotics, IIoT, and data-driven decision-making is transforming how products are made, monitored, and optimized.
This article explores where smart manufacturing is headed and how OEMs and EMS providers can future-proof their operations for what comes next.
1. AI Becomes a Central Brain, Not Just a Tool
AI is evolving from a bolt-on enhancement to a core engine in manufacturing environments. From real-time process control to predictive analytics, AI systems are enabling proactive, adaptive production lines.
Examples of impact:
- Predictive maintenance algorithms reduce downtime by 30%+
- AI vision systems detect micro-defects invisible to humans
- ML-driven yield optimization tunes parameters dynamically
OEM Action Tip: Begin collecting structured production data now — AI thrives on clean, historical data sets.
2. Collaborative Robotics Go Mainstream
Next-gen cobots (collaborative robots) are designed to work safely alongside humans — not replace them. Their affordability and flexibility make them ideal for mid-volume and mixed-product lines.
Trends to watch:
- Plug-and-play deployment with no-code programming
- AI-enabled grasping and adaptive path planning
- Integration with ERP and MES systems for dynamic tasking
Industries impacted:
- Electronics assembly
- Medical device packaging
- Consumer electronics fulfillment
3. Digital Twins and Virtual Commissioning
Digital twins — virtual replicas of physical production assets — are revolutionizing how factories design, simulate, and troubleshoot workflows.
Key benefits:
- Reduced time and cost of new line setup
- Faster root cause analysis during failures
- Real-time monitoring and scenario planning
Promwad Insight: We support clients in modeling test stations and production cells in CAD + simulation tools before physical builds — reducing ramp-up risk.
4. Hyperconnected Manufacturing with IIoT
The Industrial Internet of Things (IIoT) is laying the foundation for event-driven operations, device-level diagnostics, and cross-facility orchestration.
Use cases in 2025+:
- Smart sensors tracking vibration, energy use, and equipment cycles
- Edge devices feeding contextual data to cloud-based MES systems
- Real-time alerts for operator safety, predictive quality, and inventory flow
Adoption barrier: Cybersecurity and interoperability — modern protocols like OPC UA and MQTT are key enablers.
5. Autonomous Material Handling and Logistics
AI-powered AGVs (automated guided vehicles), drones, and robotic pick-and-place systems are redefining factory and warehouse logistics.
Capabilities expanding:
- Real-time re-routing based on floor conditions and production queue
- Integration with ERP and warehouse management systems (WMS)
- Object detection and avoidance powered by vision AI
Result: Faster, safer, and more responsive material flow — without fixed conveyor systems.
6. Sustainability and Energy-Aware Production
Smart factories are also green factories. Resource-efficient production not only lowers costs but aligns with ESG and regulatory targets.
Key technologies:
- Energy monitoring + load balancing via smart grids
- Lifecycle tracking for carbon footprint and material sourcing
- Smart scheduling to avoid peak energy pricing windows
Compliance readiness: EU’s Corporate Sustainability Reporting Directive (CSRD) and Digital Product Passport (DPP) adoption are accelerating.
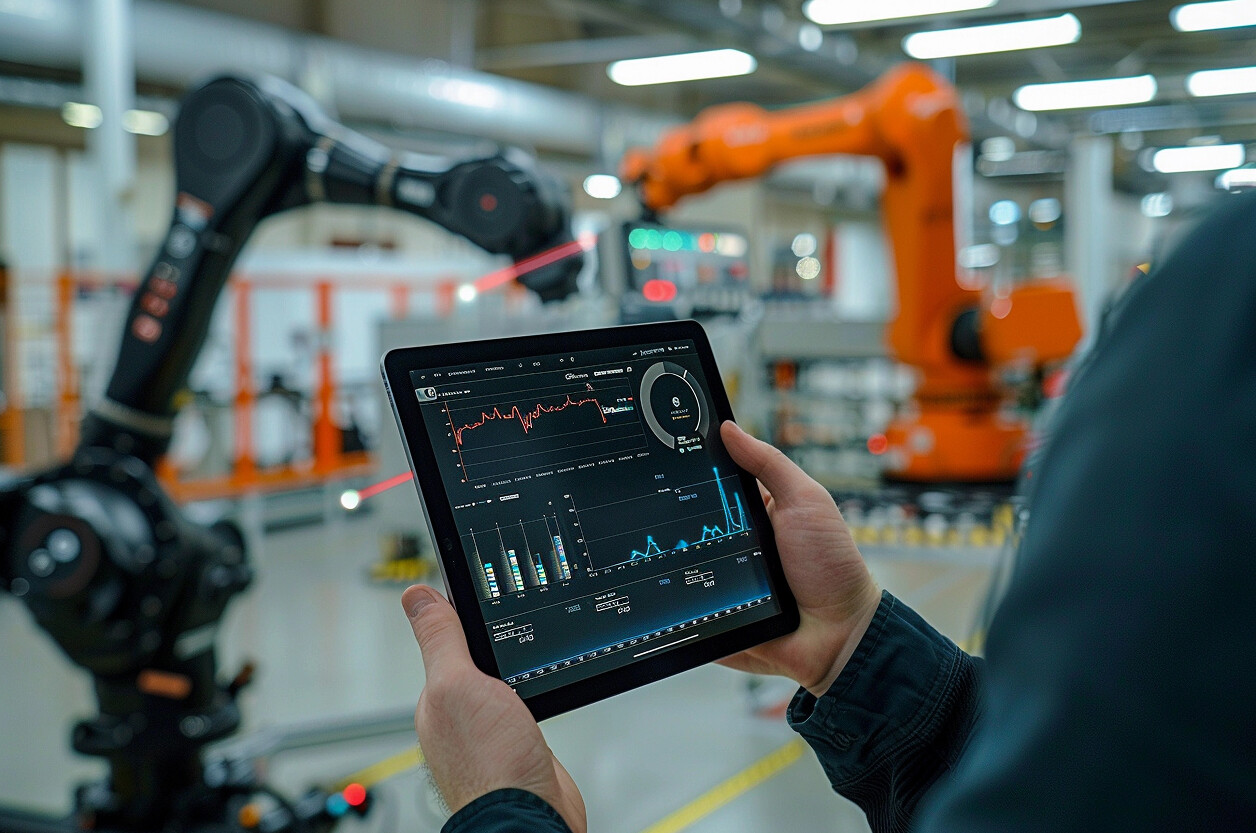
Summary Table: Smart Manufacturing Trends and Impacts
Trend | Core Benefit | Strategic Advantage |
AI Process Optimization | Higher yield, lower downtime | Real-time adaptability |
Collaborative Robotics | Safer automation, faster changeovers | Flexibility for varied product lines |
Digital Twins | Virtual simulation and testing | Reduced commissioning time |
IIoT Infrastructure | Asset visibility and control | Scalable factory intelligence |
Autonomous Logistics | Smart routing and material flow | Faster fulfillment and less manual labor |
Energy-Aware Production | Reduced operating cost, compliance | Sustainability and regulatory leadership |
Real-World Case Study: Smart Manufacturing in Action
A European OEM producing industrial power inverters partnered with Promwad to modernize their manufacturing workflow across two sites in Lithuania and Germany.
Objectives:
- Reduce changeover time for 5 product SKUs
- Improve traceability for ISO 9001 and IEC 62443 compliance
- Enable predictive maintenance on SMT lines
Solutions Implemented:
- Designed and deployed digital twins of each production cell for offline testing and training
- Integrated AI-driven inspection systems using vision models to flag soldering defects
- Enabled IIoT edge devices to stream temperature, vibration, and production metrics to a unified dashboard
- Developed a central MES system to coordinate real-time production tasks between sites
Results:
- 21% improvement in yield across all SKUs
- Weekly line reconfiguration time reduced by 36%
- Data traceability enabled full regulatory audit pass in 2024
Final Thoughts: Start Building the Factory of the Future Today
Smart manufacturing in 2025 and beyond will be defined by integration: machines, systems, people, and data working in concert. OEMs and EMS providers who adopt AI, robotics, and digital workflows early will not only improve efficiency — they will gain the agility to thrive in an unpredictable global landscape.
At Promwad, we help electronics companies implement smart manufacturing strategies — from automated test setups and digital twin modeling to real-time IIoT systems and traceable documentation workflows.
Let’s engineer the future of intelligent, resilient manufacturing — together.
Our Case Studies in Electronics Manufacturing