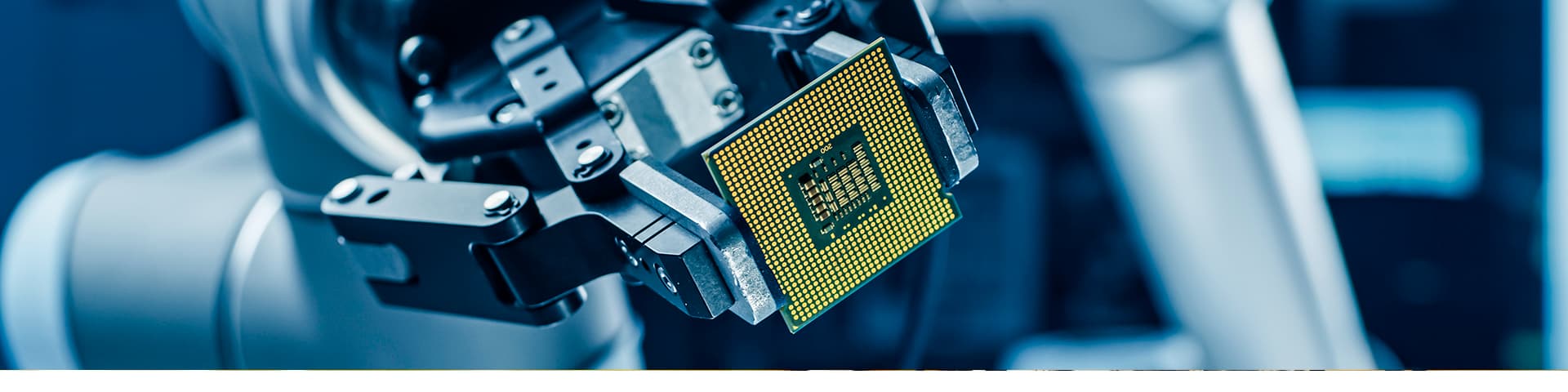
Hardware startups: a journey from prototype to mass production
In the previous article, we gave our vision of how to make hardware startups less hard. Now, we want to dig deeper and clarify a crucial process for any electronics design project—reaching mass production.
We often explain to our new clients: "The innovation and bold experiments are important, but there is one more practically oriented thing as manufacturing the product at scale. This often becomes really challenging, as, unlike prototyping, it involves a bit different mindset. There is a huge gap between making one device and making 10,000".
The biggest mistake of many hardware startups is reaching the production stage with a designs that are not fully verified. They miss validation and ignore such general engineering practice as "design for manufacture and assembling" (DFMA). As a result, product owners can reveal later that their original idea may not be achievable at all. This usually occurs due to a lack of experience in the product development from a mass production perspective.
DFMA is basically a complete set of documentation, including a detailed description of the product, materials, components, technical requirements, principles of operation, and methods of manufacturing.
In practice, the consideration of manufacturing requirements usually begins not from the first sketches of a product but from the stage of mass production, when hardware startups together with an experienced technical partner or specialists from the manufacturer side (we’ll discuss later how to choose them) make a full revision of the product design. The goal is to understand what else can be improved in order to minimize costs and improve the quality. It is important to consider the advice of contract manufacturers, because they experts in mass production.
It’s not surprising that the first thing you decide is choosing a manufacturer in China. You basically have two main options then: choosing one general contractor who will be responsible for all stages of production (components purchasing and testing, setting up a production line, packaging and shipment), or go independently—to purchase components, and order only the services of assembly/packaging of the product.
If you do not have experience in the manufacturing electronic devices and enclosures in China, then use the services of the general contractor. This will significantly reduce not only the paperwork but also the production time, as well as minimizes the risks of failure (late delivery, components’ defects, etc.).
What’s more, you may find a side company, that on your behalf will hold a tender among potential general contractors and offer an adequate list of partners with a detailed description of all the pros and cons of your cooperation.
After successfully choosing the contractor, there comes a stage of pre-production. It’s important to protect your intellectual property (IP) throughout the manufacturing process. If you are concerned about sensitive IP, you should get a signed non-disclosure agreement (NDA). Make sure that your contractor doesn’t have access to your entire hardware and software design data. The result of the pre-production stage must be a "golden sample" — a product that fully meets all requirements or the perfect example of each unit produced in the future.
And here we are—the production of your first batch has started, and the first inspection of the assembly line is taking place. If any errors are detected, your should take measures to eliminate them. In the end, your mass production will be launched with a controlled defect rate and no "surprises" in the future.
All in all, remember to select a manufacturer carefully, test your design on being 100% compilable with mass production requirements, and come through all the production stages attentively controlling each iteration. If you have any questions left, feel free to contact us. We wish you successful hardware projects for the development of your business!