How to Build a Resilient Electronics Supply Chain in 2025
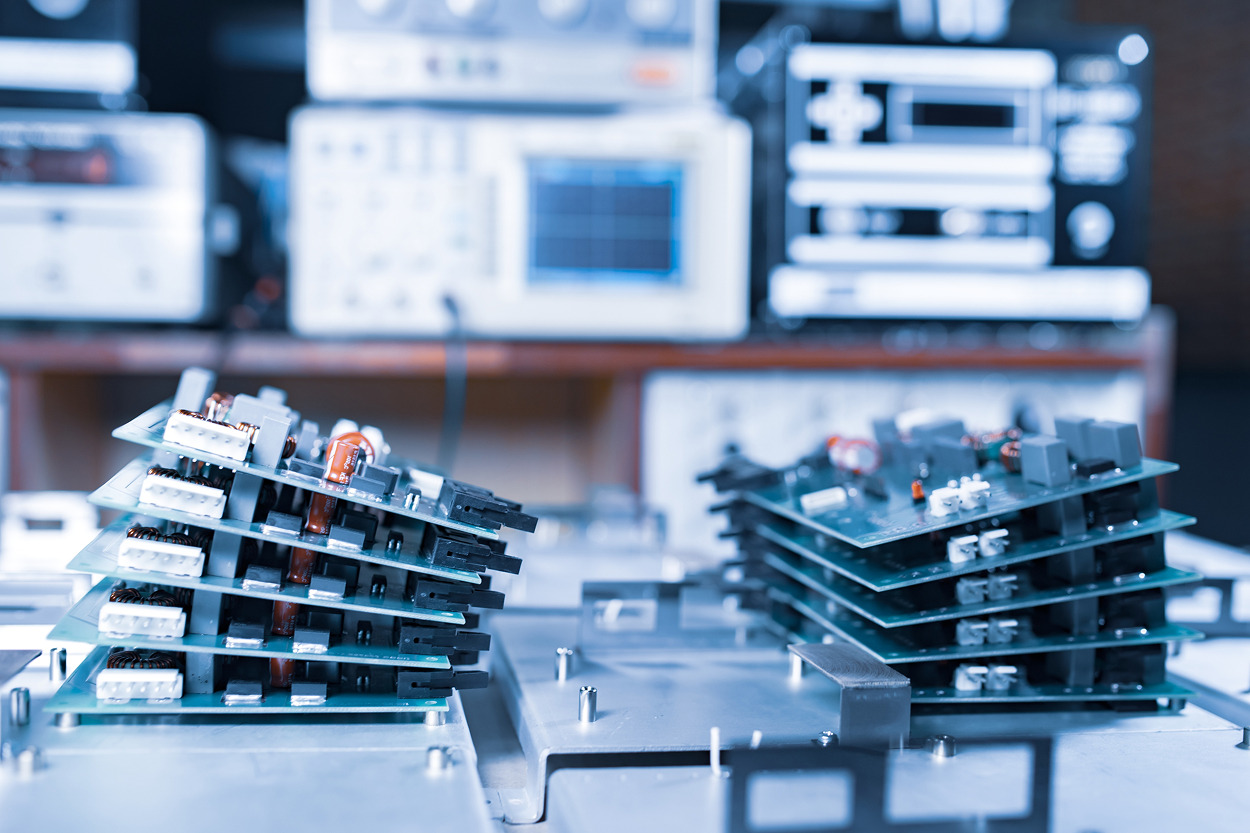
Getting Started: Why Supply Chain Resilience Is Mission-Critical
The global electronics industry has faced unprecedented disruptions over the last five years—from chip shortages to geopolitical conflicts and logistics bottlenecks. In 2025, building a resilient electronics supply chain is no longer optional—it’s a competitive advantage and survival strategy.
Whether you're an OEM, startup, or product design house, your ability to source components, scale production, and adapt to market shifts depends on supply chain strength.
Key Pillars of a Resilient Electronics Supply Chain
1. Diversified Sourcing Strategy
Avoid dependence on a single vendor, region, or component type.
Best practices:
- Qualify multiple suppliers for critical components
- Use regional alternates for Asia, EU, or North America
- Maintain a list of approved substitutes
2. Active BOM Management
Keep your Bill of Materials (BOM) flexible, current, and future-proof.
Action items:
- Monitor lifecycle status and lead times for all components
- Integrate supply chain intelligence into the design phase
- Use parametric search tools to evaluate drop-in replacements
3. Strategic EMS Partner Selection
Your contract manufacturer plays a key role in supply chain resilience.
What to look for:
- Proven sourcing network and inventory transparency
- Local vs. offshore production capabilities
- Agility in responding to shortages or allocation
4. Inventory and Buffer Planning
Move from just-in-time to just-in-case strategies where appropriate.
Methods to apply:
- Define safety stock levels for long-lead or high-risk components
- Use predictive analytics for demand forecasting
- Leverage vendor-managed inventory (VMI) programs
5. Supplier Relationship Management (SRM)
Build trust, visibility, and strategic alignment with your key suppliers.
Tactics:
- Conduct regular QBRs (Quarterly Business Reviews)
- Share forecasts and design roadmaps
- Collaborate on EOL (End-of-Life) planning
6. Geographic and Political Risk Assessment
Stay informed about risks from trade wars, sanctions, and regional instability.
Tools to use:
- Risk dashboards from market intelligence platforms
- Tariff and customs compliance trackers
- Multi-sourcing plans for geopolitical hotspots
Emerging Trends That Will Shape 2025 Supply Chains
Trend | Impact |
AI-driven supply chain tools | Enable dynamic planning and anomaly detection |
Digital twins for logistics | Model risks and optimize transport paths |
Onshoring and nearshoring | Reduce transit time and exposure to global disruption |
Sustainable sourcing requirements | Push for traceable, eco-friendly component sourcing |
Embedded ML for demand forecasting | Improve accuracy using edge analytics |
How Promwad Supports Resilient Supply Chains
At Promwad, we help electronics companies strengthen their supply chains through:
- EMS partner selection and auditing in Europe and Asia
- Component sourcing strategy with verified alternates
- BOM analysis and risk scoring tools
- DFM/DFT design to improve manufacturability and testability
- Transition support during supplier or factory changes
We work as an extension of your engineering and procurement team to minimize disruption and reduce time-to-market.
Real-World Example: Consumer IoT Device Launch
A client in the smart home sector faced a 38-week lead time on a key MCU during their pre-production phase.
Promwad solution:
- Analyzed pin-to-pin compatible alternatives from three vendors
- Verified performance with minimal firmware changes
- Reworked the BOM with sourcing buffers and onboarding a new EMS in Eastern Europe
Outcome: The client avoided a six-month delay and delivered the product to retail partners on schedule.
Real-World Case Study: Automotive Control Unit Supply Chain Diversification
An automotive Tier 1 supplier worked with Promwad to de-risk their supply chain for a custom control unit, initially built entirely in East Asia. Due to increased lead times and quality inconsistencies, the company aimed to establish an EU-based supply strategy.
Challenge:
- Sole-source dependency for PCBs and enclosures
- 20% annual price fluctuations
- Limited access to Tier 2 suppliers
Solution:
- Reorganized BOM with regionally balanced suppliers in Poland, Germany, and Czechia
- Transferred EMS to a facility with ISO/TS 16949 certification
- Developed a digital twin of logistics and production lines to model scenarios
Results:
- 40% improvement in lead time predictability
- 17% cost savings through dual-sourcing
- 3-week faster ramp-up on new model launch cycles
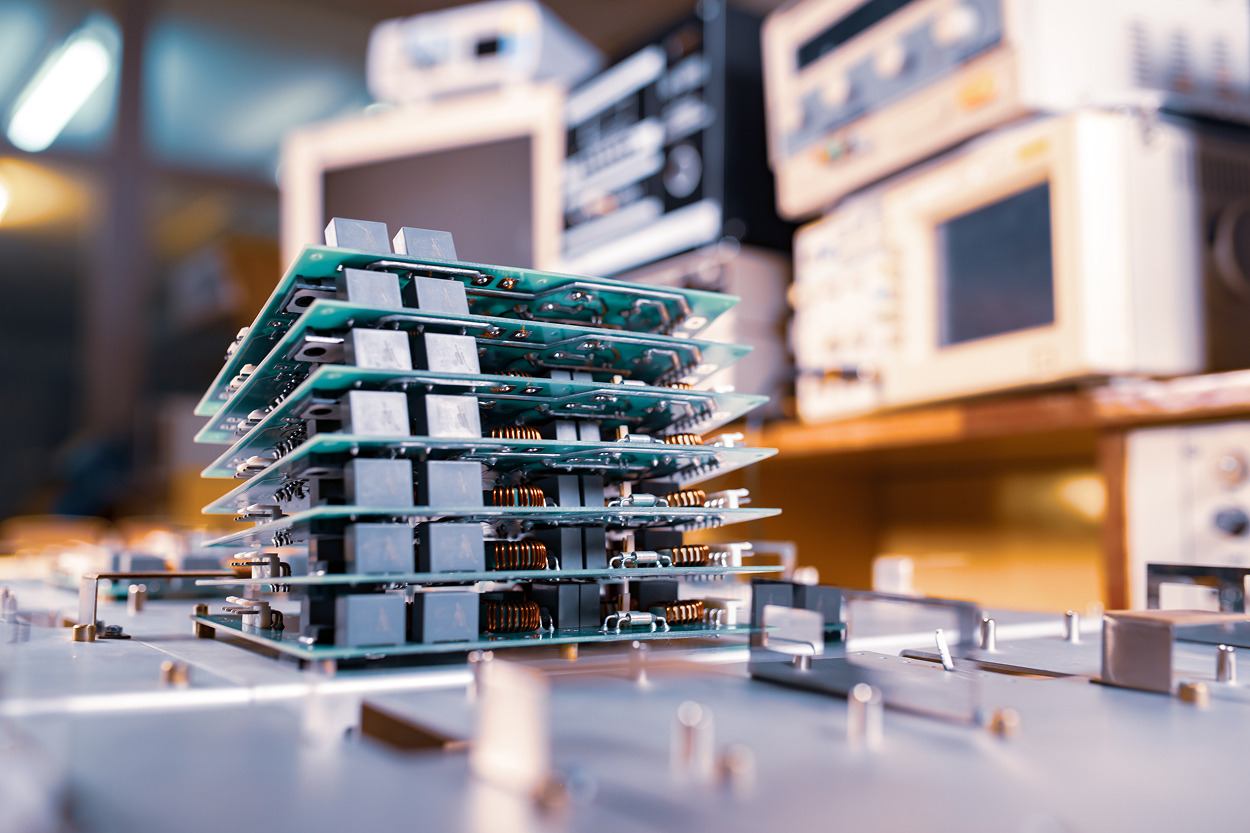
What the Experts Say About Supply Chain Strategy in 2025
"In today’s environment, electronics companies must assume disruption is constant, not occasional. A resilient supply chain isn’t just about backups—it’s about intelligent design. Redundancy, local production nodes, and AI-driven planning are the new normal."
— Anita Chowdhury, VP of Supply Chain Innovation, Cambridge Innovation Institute
"We see companies moving toward more modular BOMs to make component switching easier. Engineering teams are becoming procurement-aware, which is a massive culture shift."
— Lars Köhler, Senior EMS Consultant, IPC Europe
Final Thoughts: Build for Flexibility, Not Just Cost
In 2025, the most resilient electronics companies will be those that treat supply chains as a strategic asset—not just a cost center. By embracing smart sourcing, predictive planning, and agile EMS relationships, you’ll be ready to launch, scale, and adapt in any market condition.
Let Promwad help you audit and fortify your electronics supply chain for what’s next.
Our Case Studies in Electronics Manufacturing