Turnkey Electronics Manufacturing: Pros, Cons, and When It Makes Sense
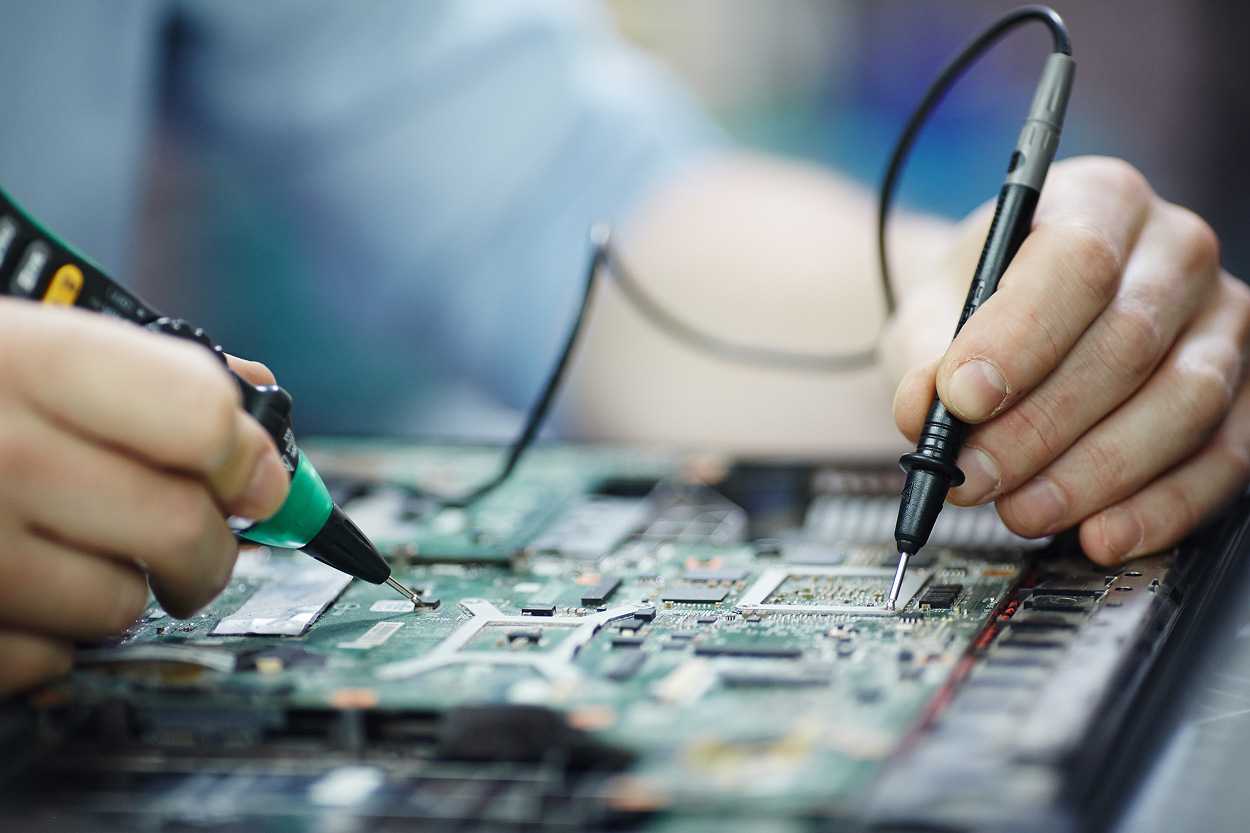
Getting Started: What Is Turnkey Electronics Manufacturing?
Turnkey electronics manufacturing refers to a production model in which a single EMS (Electronics Manufacturing Services) provider handles the entire process—from component sourcing and PCB assembly to testing, packaging, and delivery.
It’s an all-in-one solution designed to streamline supply chains and reduce overhead for OEMs, startups, and scaling hardware companies. But is it always the best option? In this article, we explore the pros and cons of turnkey EMS and outline scenarios where it offers real strategic value.
What’s Included in a Turnkey EMS Offering?
- BOM validation and procurement
- PCB fabrication and assembly
- Functional and in-circuit testing
- Mechanical assembly and enclosure integration
- Packaging, labeling, and logistics
- Quality control and traceability
This model allows clients to hand off production to a specialized partner, focusing instead on product development, marketing, and sales.
Pros of Turnkey Electronics Manufacturing
1. Simplified Supply Chain Management
One vendor handles everything, reducing the complexity of managing multiple suppliers, logistics, and quality control protocols.
2. Faster Time-to-Market
Turnkey EMS providers often optimize lead times through vendor relationships, purchasing power, and production readiness.
3. Cost Efficiency at Scale
By consolidating tasks under one roof, overhead costs drop. EMS providers can leverage bulk procurement and streamlined production processes.
4. Centralized Communication
No more chasing multiple vendors. A single point of contact simplifies engineering changes, delivery schedules, and troubleshooting.
5. Easier Risk Management
Turnkey manufacturers take responsibility for sourcing, testing, and logistics—transferring much of the operational risk from the client.
When Turnkey Manufacturing Makes Sense
Use Case | Why It Works |
Startups | Limited internal resources; need speed and simplicity |
Scaling SMEs | Consolidate processes during rapid growth |
Low-volume, high-mix products | Turnkey EMS handles flexible builds and rapid changeovers |
MVP & Pilot Projects | Test product-market fit without setting up a supply chain |
Remote teams | Lack of in-house ops makes centralized production ideal |
Potential Downsides to Consider
1. Less Control Over Individual Steps
Outsourcing the entire process can mean less visibility into individual workflows like sourcing or factory testing.
2. Vendor Lock-in Risk
Deep integration with one EMS can make future vendor switching more complex and time-consuming.
3. Less Price Transparency
You may not see the exact margins across BOM items or labor costs, compared to handling parts of the supply chain yourself.
4. Minimum Volume Commitments
Some turnkey EMS providers prioritize clients with high-volume orders, limiting flexibility for small batch or niche products.
How to Choose the Right Turnkey EMS Partner
- Proven track record with similar product categories
- Transparent project management and pricing structure
- DFM/DFT support during onboarding
- In-house testing and quality control
- Geographic alignment with your markets or logistics hubs
Real-World Case Studies: Turnkey in Action
Case 1: Scaling an IoT Startup from Prototype to Mass Production
A European IoT startup approached Promwad with a fully functional prototype of a smart energy meter. The challenge was to move to small-batch production while preparing for scalability without building an internal supply chain.
Solution: Promwad handled:
- BOM optimization and alternate sourcing for long-lead components
- EMS partner selection and onboarding in the EU region
- Pilot run with 100 units followed by ramp-up to 5,000
- Full DFM and DFT adaptation for test jigs and yield optimization
Result: Time-to-production reduced by 35%, while unit cost decreased by 22% thanks to consolidated procurement.
Case 2: Medical Device Manufacturer Moving to a Turnkey Partner
A US-based medtech company needed a new EMS partner for a Class II medical wearable after production challenges overseas.
Solution:
- Promwad audited the previous production process and requalified suppliers
- Coordinated transition to a European EMS facility with ISO 13485 certification
- Provided turnkey services including secure packaging, traceability, and quality audits
Result: Regulatory compliance improved, returns dropped by 18%, and time-to-ship per unit was cut by 21%.
Case 3: Consumer Electronics Client Testing a New Product Line
A leading audio brand partnered with Promwad to develop and test a new wireless speaker lineup for the EU market.
Solution:
- End-to-end turnkey support: hardware co-design, firmware integration, and mechanical assembly
- Developed custom packaging and drop-resistance testing procedures
- Managed contract manufacturing in Poland, including logistics for Amazon fulfillment
Result: The client launched the product 6 weeks ahead of the original schedule and received a design award at IFA.
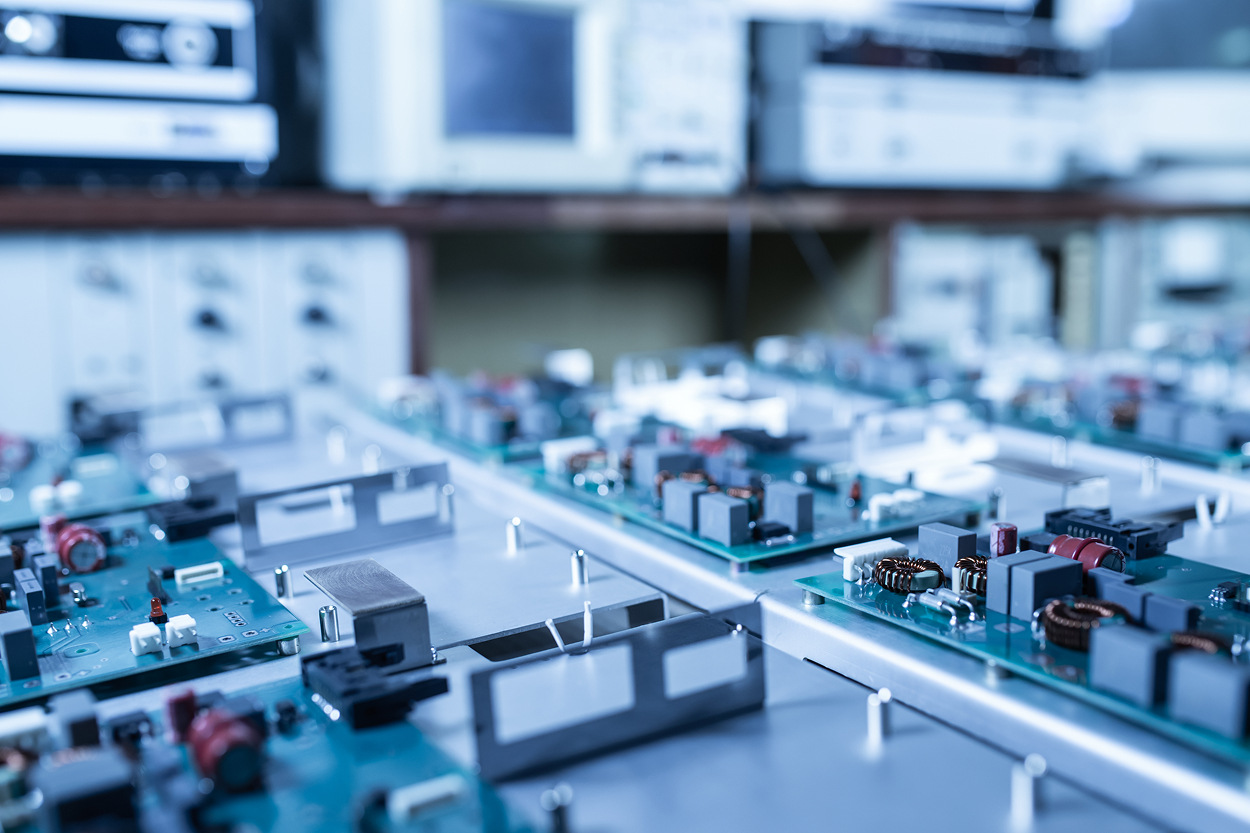
Promwad’s Approach to Turnkey EMS
At Promwad, we offer full-cycle support for hardware products—from industrial design and embedded development to turnkey manufacturing with trusted EMS partners across Europe and Asia.
What we provide:
- BOM optimization and sourcing strategy
- Contract manufacturer onboarding and supervision
- Functional test systems tailored to your product
- Packaging design and logistics planning
Our clients stay focused on innovation while we handle production end-to-end—with transparency and traceability at every step.
Turnkey vs. Consignment vs. Partial EMS: A Comparison
Model | Who Sources Components | Who Manages Assembly | Best For |
Turnkey | EMS | EMS | Startups, MVPs, distributed teams |
Consignment | Client | EMS | When you have preferred suppliers or stock |
Partial EMS | Shared responsibility | EMS | Complex BOMs or evolving designs |
Industry Outlook: Why Turnkey EMS Is Gaining Momentum
With growing product complexity, globalized teams, and rising demand for faster launches, turnkey models are becoming increasingly attractive.
A 2024 report by IPC reveals that OEMs using turnkey EMS reduced their time-to-production by 28% on average. The rise of connected devices, low-volume production runs, and agile hardware development all contribute to the shift toward full-cycle partners.
Final Thoughts: When Speed Meets Simplicity
Turnkey electronics manufacturing is not a one-size-fits-all solution, but in the right context, it can save time, reduce risk, and enable faster product launches.
If your team is stretched thin, working remotely, or scaling quickly, a reliable EMS partner with turnkey capabilities might be exactly what you need to stay competitive.
Let Promwad help you evaluate whether turnkey EMS is the right model for your next product—and if so, execute it with confidence.
Our Case Studies in Electronics Manufacturing