Rapid Prototyping and Manufacturing of Complex Engineering Solutions
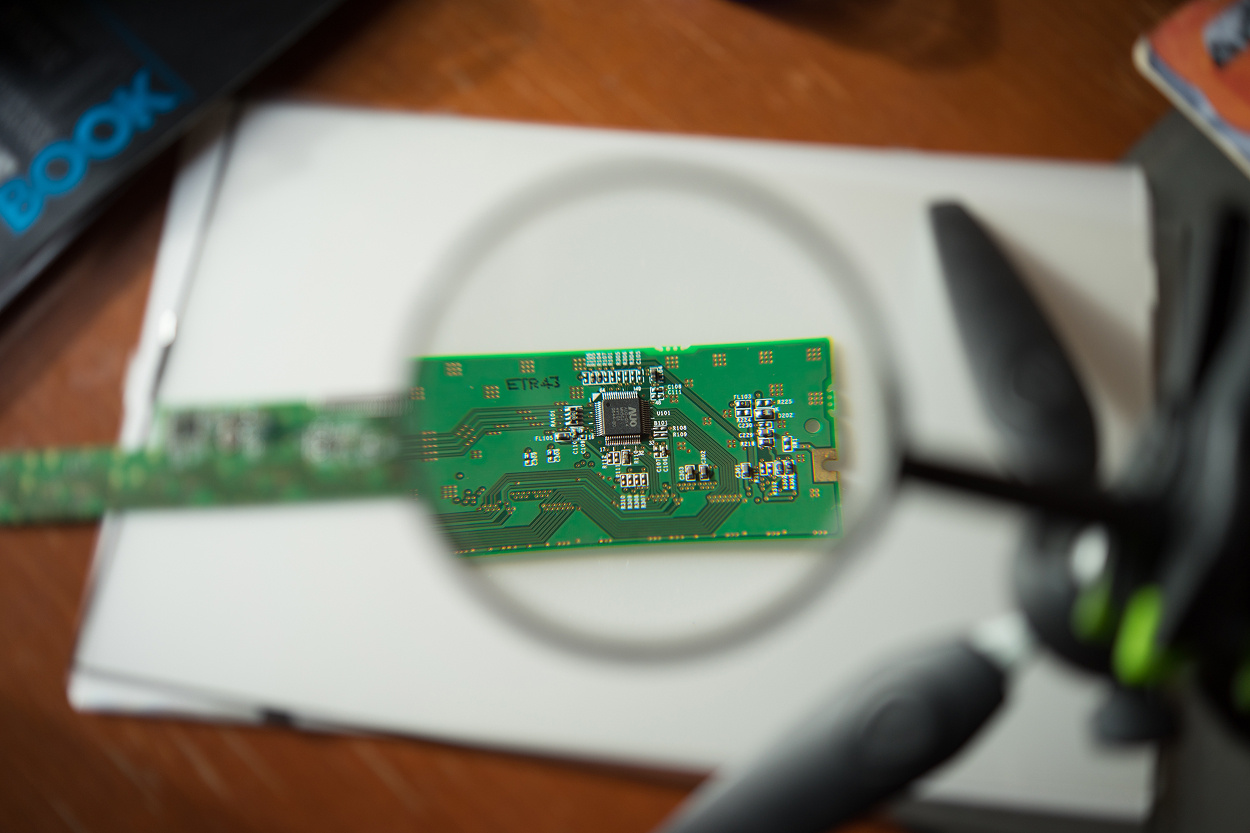
Introduction: Speed Meets Complexity in Modern Engineering
In 2025, hardware design is not just about precision — it's about speed. Markets demand faster iteration cycles, early validation, and scalable transition from prototype to production. For companies building sophisticated electronic devices, the ability to quickly move from idea to functional prototype and into manufacturing is a major competitive advantage.
This article explores best practices, tools, and workflows that enable rapid prototyping of complex engineering solutions — and how to turn prototypes into reliable, mass-producible products.
What Is Rapid Prototyping in Electronics?
Rapid prototyping in electronics refers to the fast and iterative development of functional hardware or embedded systems using:
- Low-volume PCB fabrication
- 3D-printed or CNC-milled enclosures
- Off-the-shelf development kits
- Quick-turn assembly partners
It enables engineers to:
- Validate electrical and mechanical integration
- Test firmware and drivers on real hardware
- Evaluate form factor, thermal, and EMI behavior
Promwad Insight: We help clients reduce time-to-first-prototype from months to 2–4 weeks using parallel design streams, in-house validation tools, and pre-certified modules.
Agile Prototyping Workflow: From Idea to Validation
- Specification Mapping
Translate high-level requirements into architecture blocks
Identify reuse opportunities (IP, dev kits, modules) - Schematic + PCB Design
Fast layout using modular templates
DFM constraints applied from the start - Mechanical + Thermal Co-Design
Use of STEP + IDF files to align PCB and enclosure
Thermal simulation before build - Assembly and Bring-Up
Partner with fast-turn EMS providers
Initial testing with boundary scan and in-circuit probes - Firmware and Testing
Bootloaders, drivers, diagnostics
Unit testing and CI/CD if applicable
Prototyping Tools and Platforms Used in 2025
Category | Tool/Platform | Use Case |
Schematic & PCB | Altium Designer, KiCad | High-speed layout and simulation |
Mechanical Design | SolidWorks, Fusion 360 | Enclosure co-design and fit testing |
Simulation & DFM | SimScale, Siemens Valor | Thermal, EMI, manufacturability |
Embedded Firmware | Zephyr RTOS, PlatformIO | Modular firmware dev |
Prototyping Kits | Raspberry Pi CM4, STM32 Nucleo | Low-cost PoC & testing |
Prototyping Services | PCBWay, JLCPCB, MacroFab | Fast PCB + assembly |
Case Study: Industrial IoT Gateway From Design to First Prototype
A European industrial automation company partnered with Promwad to build a ruggedized IoT gateway with cellular connectivity, industrial fieldbus support, and OTA firmware update capability.
Timeline:
- Week 1–2: Architecture, component selection, enclosure modeling
- Week 3–5: Schematics, PCB design, 3D simulation, BOM sourcing
- Week 6–7: Assembly and initial bring-up, firmware load
Key accelerators:
- Reuse of Promwad IP blocks (modem, power, secure boot)
- In-house test fixtures and bootloader stack
- Parallel mechanical and PCB iteration
Results:
- First working prototype in under 8 weeks
- FCC and CE pre-compliance tests passed on the first iteration
- Ready for pilot batch manufacturing after minor mechanical tweaks
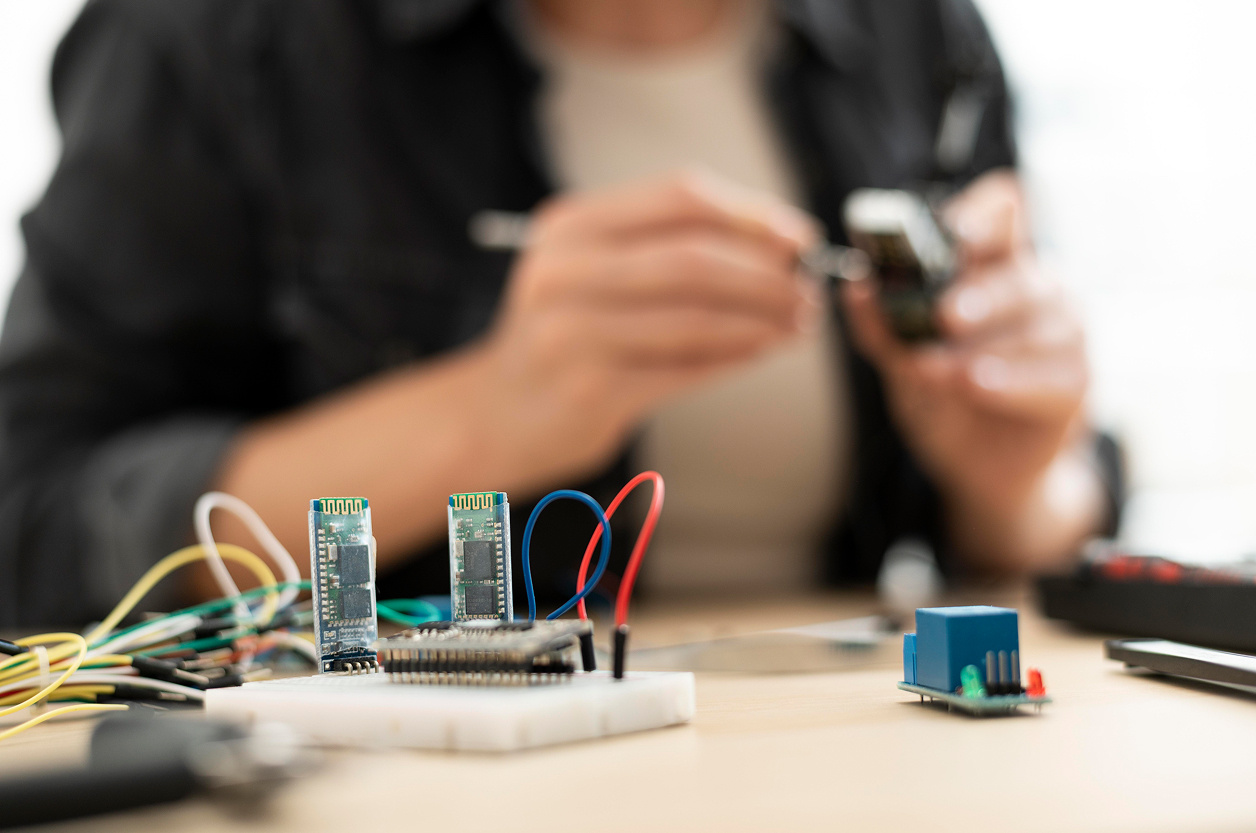
Turning Prototypes Into Scalable Products
To transition from proof-of-concept to production, rapid prototyping must evolve into a robust NPI (New Product Introduction) process:
What’s needed:
- DFM/DFT review before locking design
- Supply chain and sourcing alignment
- Documentation (BOM, gerbers, test plans, certifications)
- EMS onboarding and pilot batch testing
Promwad Services:
- Engineering samples and EVT/DVT builds
- Manufacturing audit and partner onboarding
- Test automation and fixture design
Additional Case Study: Consumer Wearable from MVP to Pilot Production
A European startup approached Promwad with a vision to launch a health-focused wearable device with embedded biosensors, BLE connectivity, and a companion mobile app. The challenge was to validate hardware feasibility, UX ergonomics, and production cost — all within three months to meet investor milestones.
Approach:
- Used Nordic nRF5340 module for BLE + sensor fusion
- 3D-printed flexible enclosures for wrist comfort testing
- Custom test app for over-the-air parameter logging
Timeline:
- Week 1–2: Component selection, RF layout simulation
- Week 3–4: Schematic + PCB design, enclosure fit iterations
- Week 5–7: PCB fab, BLE stack tuning, battery tests
- Week 8–10: Pilot run of 50 units for UX, EMI, and user trials
Outcome:
- MVP completed in 10 weeks
- Firmware OTA-ready with test suite
- Used for field tests and certification pre-validation
Final Thoughts: Iterate Fast, Manufacture Smart
In the race to innovate, rapid prototyping gives hardware companies the agility of startups with the scalability of established players. But to truly benefit, your workflow must connect quick iteration with structured production paths.
At Promwad, we help companies reduce risk, accelerate timelines, and move from idea to mass production through integrated design, validation, and EMS support.
Ready to build your next complex engineering solution — fast and right the first time?
Our Case Studies in Electronics Manufacturing