- FPGAs iCE40 series for a small form factor.
- MachXO3 FPGA family for control and security applications.
- ECP5.
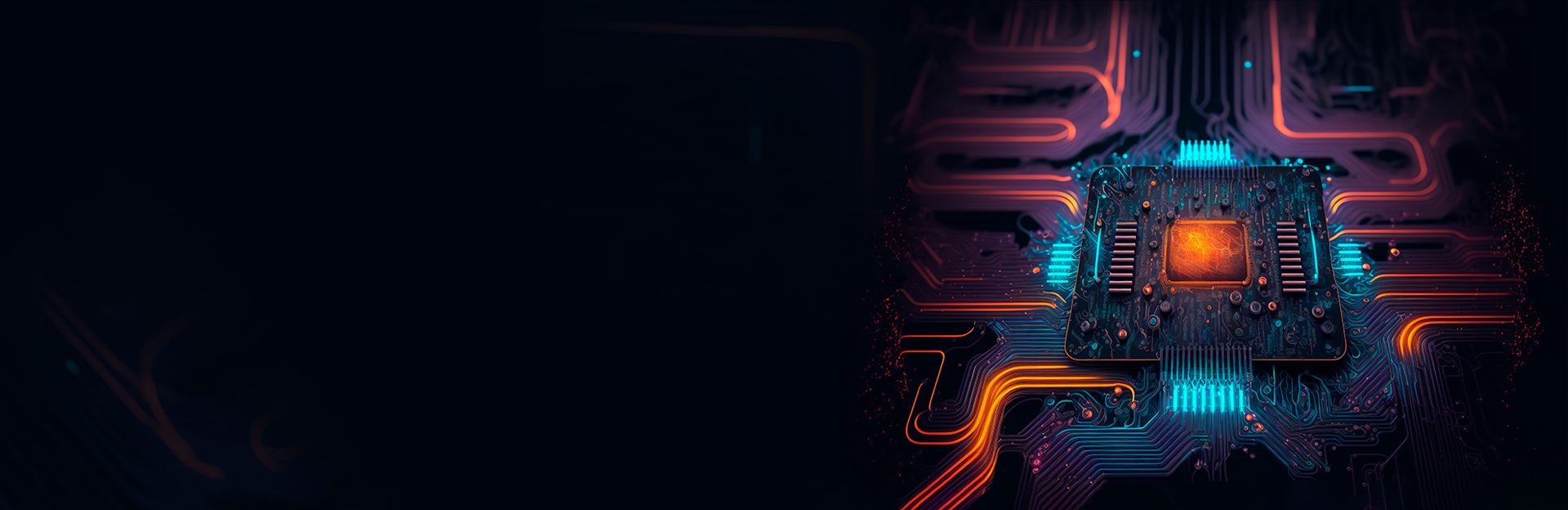
FPGA Design
for industrial automation and robotics
Industrial-Standard FPGA Solutions
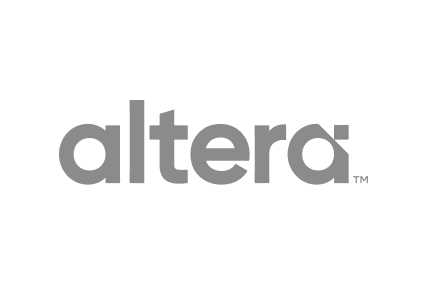
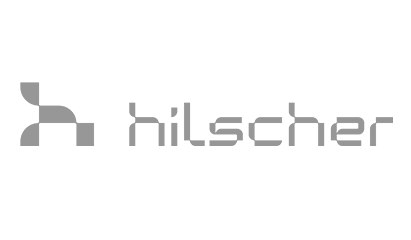
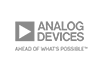
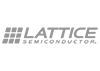
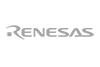
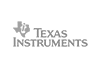

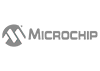
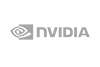
Our Official Partner Vendors
- Agilex®, Arria®, Cyclone®, Stratix®, and MAX® series
- IP & logic blocks, high-speed transceivers & I/Os, and configurable embedded SRAM.
- Intel software tools to optimise development time, costs, and power.
- FPGAs: PolarFire Mid-Range, IGLOO 1/2, ProASIC 3, Fusion Mixed-Signal.
- SoC FPGAs: PolarFire, SmartFusion 1/2.
- Radiant-tolerant and antifuse FPGAs.
Our Tech Map in FPGA
Vitis/Vivado, Quartus Prime, Diamond, Libero, Matlab
NVidia Jetson, Alveo, OpenVINO, TensorFlow, Keras, Caffe
Verilog, VHDL, System Verilog, VivadoHLS, Simulink/HDL Coder, С/C++, Python
High-speed PCBs, power electronics PCBs, DDR4, JESD204b, SDI, SI, PI, thermo modelling
Zynq/Zynq US+, Cyclone V SoC, Cyclone10, ECP5, MPF500
EtherCAT, PROFINET, EtherNet/IP, DeviceNet
Nios, Nios II, RISC-V, VexRiscv, MicroBlaze, MIPS, OpenRISC
10/100/1000, 10G
Our Case Studies
Explore our FPGA-based solutions for industrial automation, energy and robotics.
AC/DC converters with PFC IP core
IP cores: ADC_RX, PI/PID controller, PWM, 2p2z compensator, 3p3z compensator, LPF, power calculation
We develop advanced AC/DC converters for a wide range of power applications and create cascaded, high-power, and robust systems beyond traditional microcontrollers' capabilities.
Our solution includes the essential building blocks for the operation of AC/DC converters, such as an analogue-to-digital converter (ADC) to receive data from electrical circuits, a circuit to precisely control current and voltage, and an IP core to generate PWM signals.
Additionally, we employ a PFC IP core which enables power factor correction and ensures optimal performance and efficiency. By utilising high-performance logic FPGAs, our AC/DC converters provide a level of precision and performance that is unmatched by traditional solutions, allowing businesses to achieve greater efficiency and cost savings.
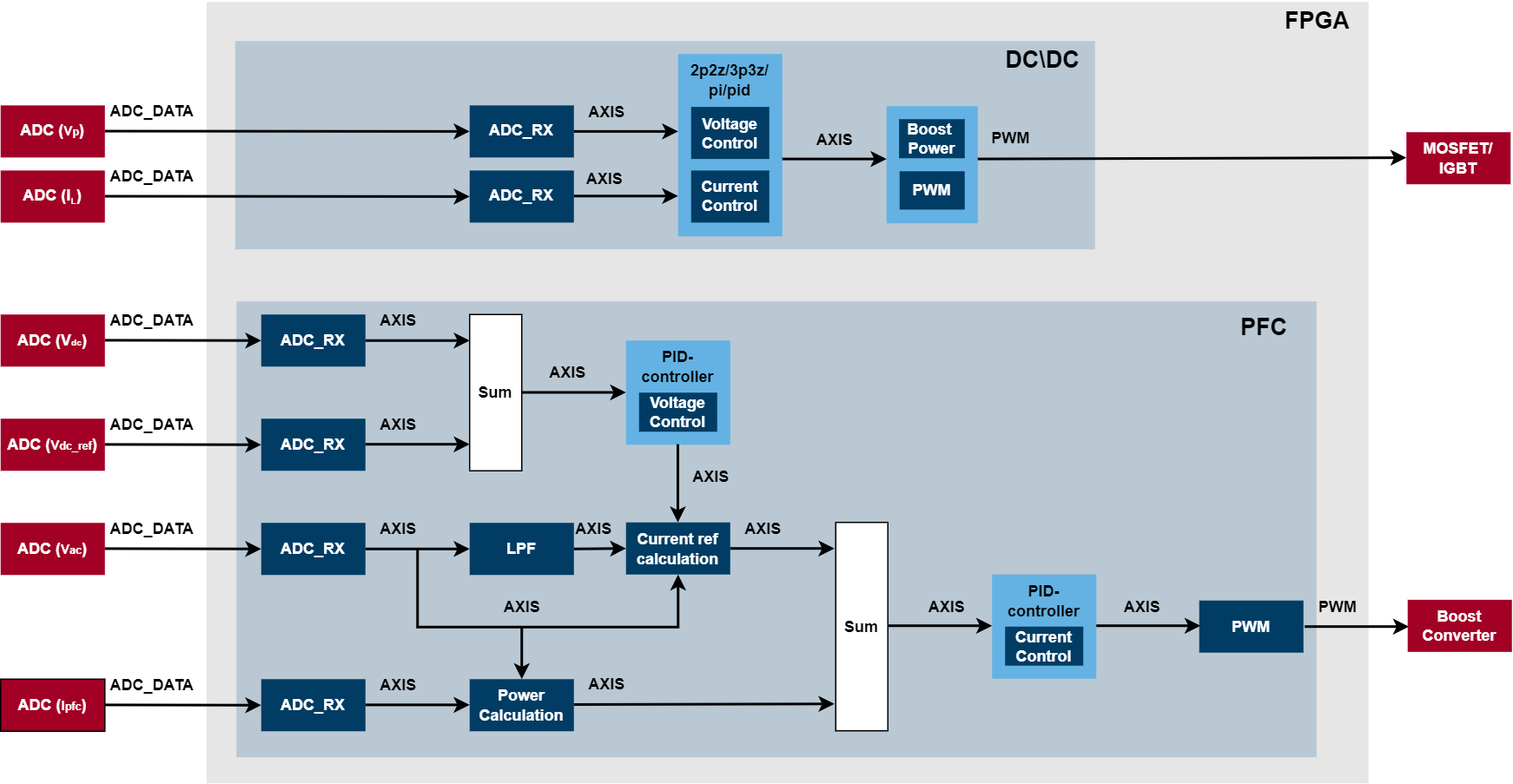
DC/DC for solar power systems
IP cores: ADC_RX, PI/PID controller, PWM, 2p2z compensator, 3p3z compensator, MPPT
We develop cutting-edge DC/DC converters that target a wide range of power applications, focusing on industrial automation and electric power systems.
Our team creates cascaded high-power solutions that are tailored to meet the specific needs of solar power systems.
Our solution incorporates key building blocks: an ADC to receive data from electrical circuits, a circuit controlling current and voltage, and an IP core generating PWM signals.
Also, we incorporate advanced control techniques such as 2p2z and 3p3z compensators as an alternative to traditional PI/PID controllers, resulting in enhanced performance and efficiency.
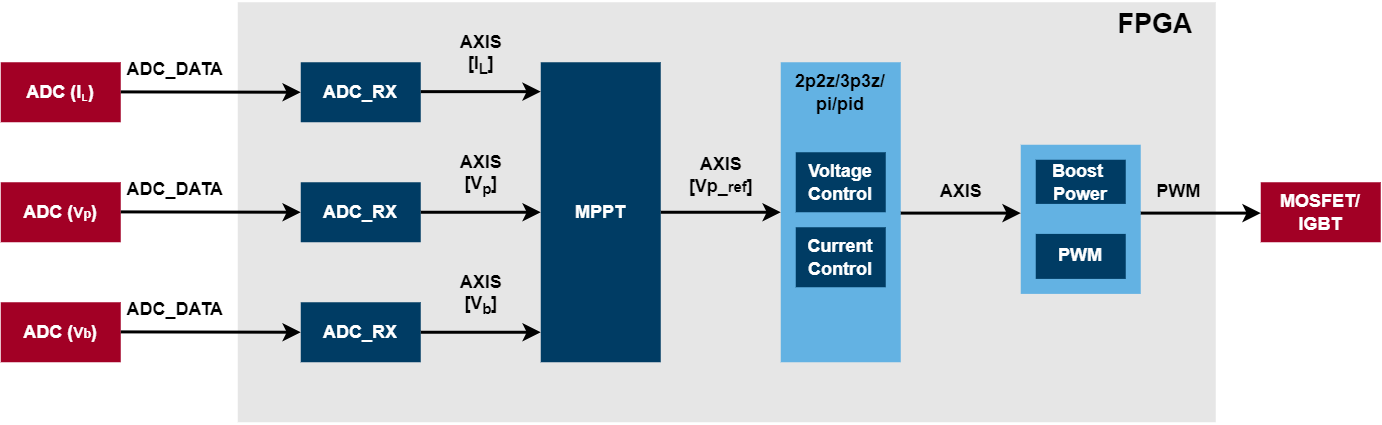
DC/AC for power applications
IP cores: ADC_RX, PI/PID controller, PWM, Notch filter, Sin/Cos generator, current calculation, GPIO
We design high-power FPGA solutions that can be used in DC/AC converters and go beyond the capabilities of traditional microcontrollers and DSPs.
The integral components include an ADC for data reception from electrical circuits, a circuit governing current and voltage, and an IP core for PWM signal generation.
We incorporate advanced features such as a Sin/Cos generator, which sets the desired output voltage profile, and a variety of additional components to optimise the converters’ performance and efficiency.
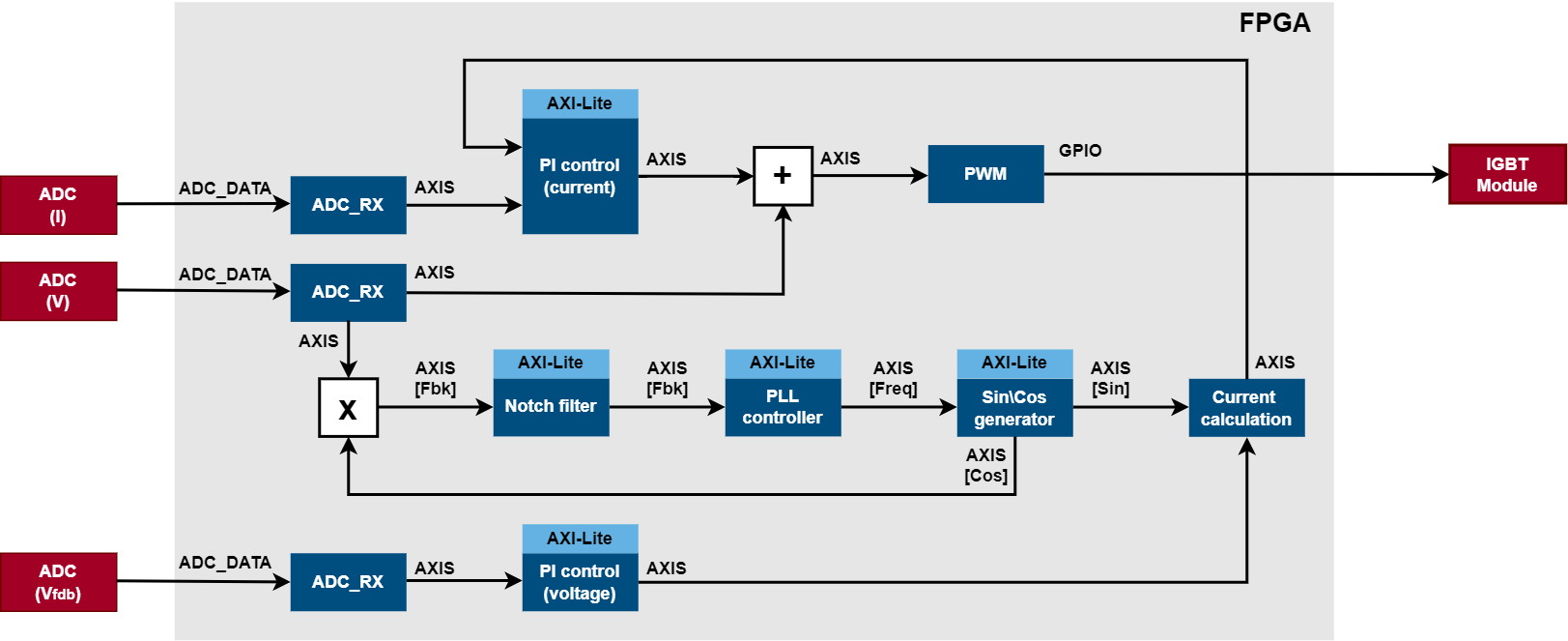
PFC, four-phase interleaved boost converter
IP cores: ADC_RX, PI/PID controller, LFD, current ref calculation, power calculation, PWM
The four-phase interleaved boost converter (PFC) is a cutting-edge circuit design that builds upon traditional boost converters. Unlike the original design, which operates in parallel, the PFC utilises an interleaved approach, where the number of parallel boost converters depends on the circuit load.
This innovative design addresses the issue of overload burden faced by the traditional boost converter, which often requires larger equipment and increased switch operation as the circuit load increases.
The PFC ensures improved performance, as well as reduced equipment size and switch operation load.
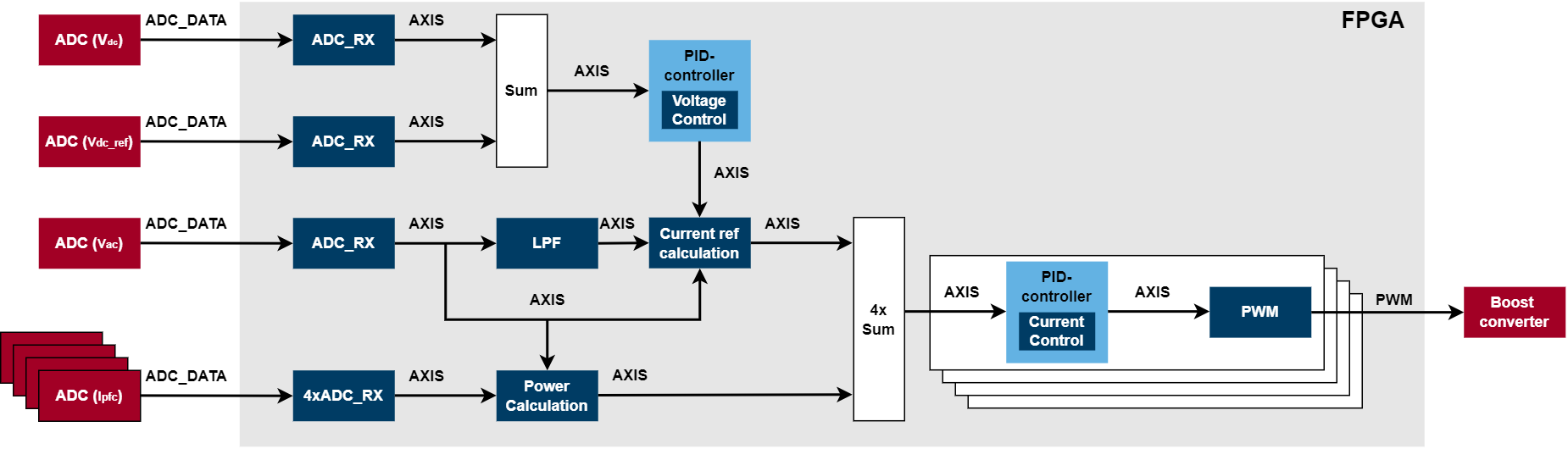
Three-phase active power filter (APF) with first harmonic detectors (FHD) control circuit
IP cores: PI/PID controller, first harmonic detector, ADC_RX, PWM
The three-phase active power filter (APF) is an advanced technology to compensate for higher harmonics in electrical systems.
This compensator utilises three first harmonic detectors (FHDs) to calculate the compensation currents (Ic). The compensation process involves subtracting the first harmonic component (IH1) from the load current (IL) to achieve a cleaner and more stable output.
The compensation reference signal (ICr) is a reference for the output current controller, which controls the output inverter transistors in conjunction with pulse width modulation (PWM).
This solution eliminates the negative effects of harmonic distortion, such as decreased efficiency, increased equipment wear and tear, and power quality issues.
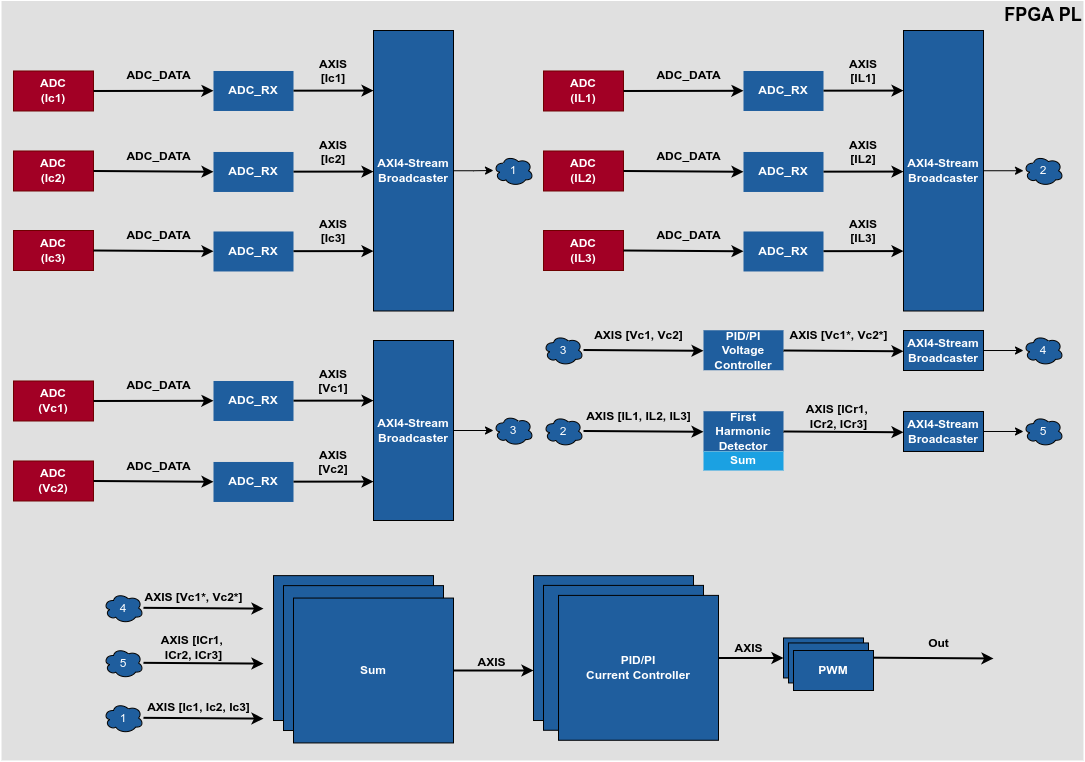
PQ algorithm for active power filter (APF)
IP cores: Clark, park, high-pass filter, park inverse, Clark inverse, ADC_RX
The p-q algorithm is based on a set of instantaneous powers that can be calculated from voltage and current waveforms without restrictions on their shape or amplitude. This solution can be applied to three-phase systems regardless of whether they have a neutral wire or not.
Furthermore, the p-q algorithm is not only effective in steady-state conditions but also in transient states, making it a suitable choice for various applications. This algorithm can be implemented using digital industrial controllers such as FPGA and DSP, which provide high-performance and efficient control of power systems.
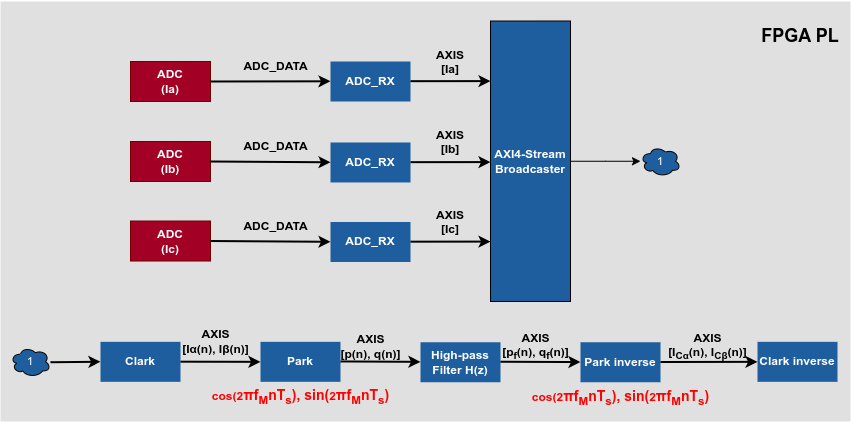
Motor control for BLDC/PMSM/ACIM (sensored)
IP cores: PID, ADC_RX, encoder, SVPWM, PWM, Clark, park, high-pass filter, park inverse, Clark inverse
We designed a sensored motor control for brushless DC (BLDC), permanent magnet synchronous motors (PMSM), and AC induction motors (ACIM) for real-time monitoring of the motor's position and speed, providing a high level of control and accuracy through sensors. It enables improved product quality, increased productivity, and reduced downtime in the manufacturing processes.
Sensored motor control provides greater flexibility and scalability, allowing businesses to adapt to changing requirements, implement new technologies, and improve product quality. Such systems can be integrated with PLCs and FPGAs to create more efficient and cost-effective control solutions.

Motor control for BLDC/PMSM/ACIM (sensorless)
IP cores: PID, ADC_RX, SVPWM, PWM, Clark, Park, high-pass filter, Park inverse, Clark inverse
Sensorless control of brushless DC (BLDC), permanent magnet synchronous motors (PMSM), and AC induction motors (ACIM) allows businesses to achieve significant cost savings by eliminating the need for physical sensors. This technology uses advanced algorithms to estimate the position and speed of the motor based on its electrical signals.
This can improve performance in applications such as electric vehicles, drones, and industrial automation. Sensorless control can be integrated into a wide range of applications and be easily adapted to changing requirements.
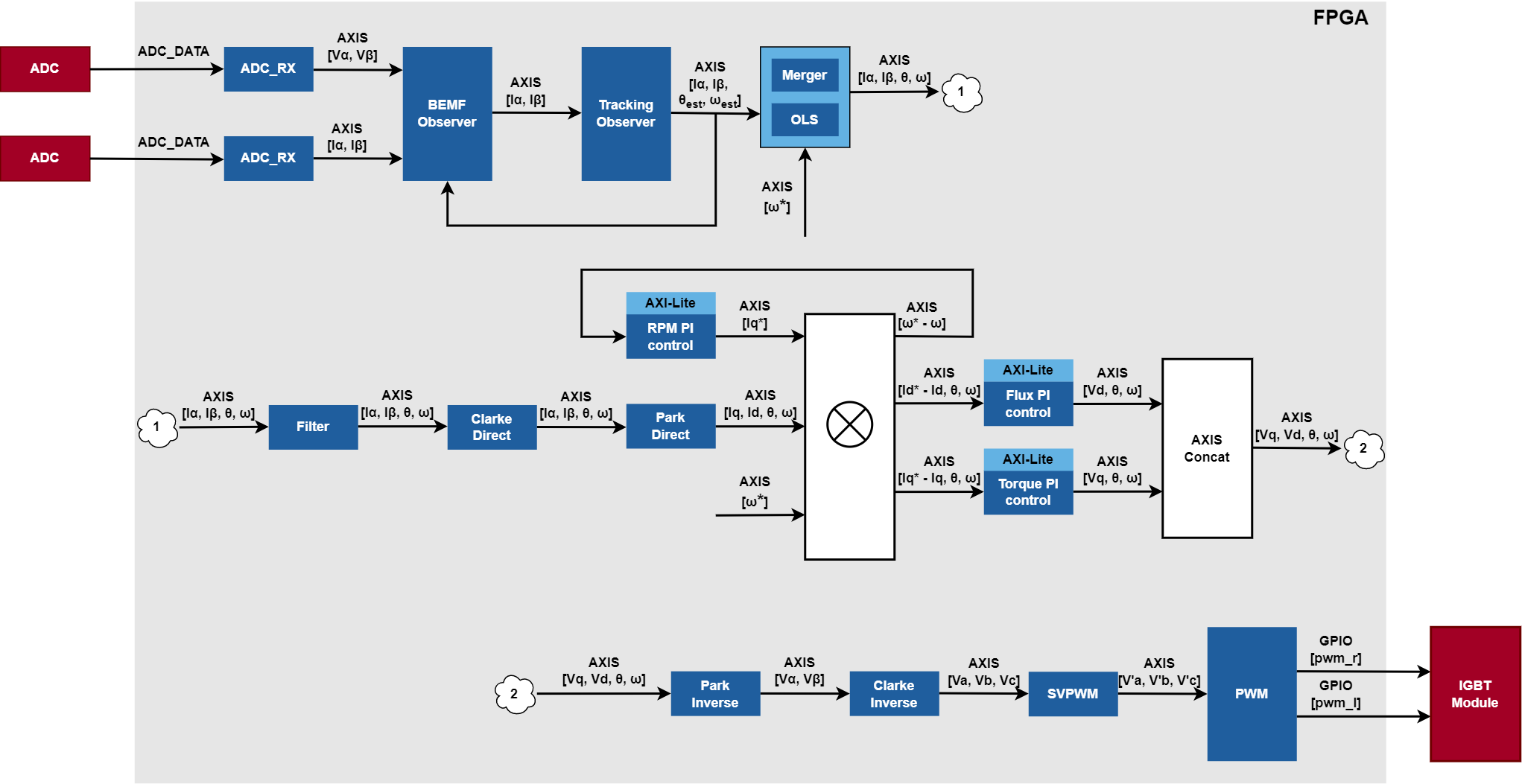
Motor control for BLDC/PMSM/ACIM (sensored), TLI (three-level inverter)
IP cores: PID, ADC_RX, encoder, SVPWM, PWM, Clark, Park, high-pass filter, Park inverse, Clark inverse
Sensored motor control for brushless DC (BLDC), permanent magnet synchronous motors (PMSM), and AC induction motors (ACIM) allow for real-time monitoring of the motor's position and speed, providing a high level of control for robotics, automation, and transportation.
Such systems enable high-performance and high-precision motion control. By incorporating three-level inverters (TLI) into the control system, businesses can achieve a high level of power conversion efficiency, reducing energy costs.
Sensored motor control with a TLI can also increase the power density of the motor, leading to more compact designs.
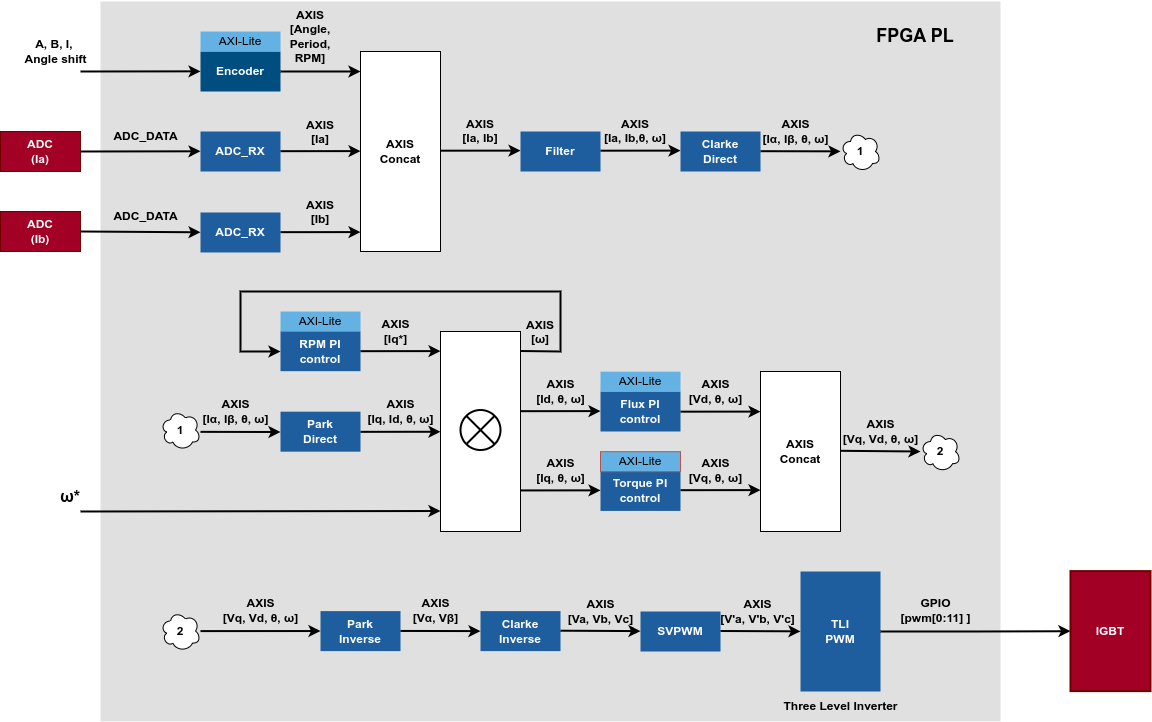
FPGA-based servo drive for industrial applications
IP cores: PID, ADC_RX, encoder, SVPWM, PWM, Clark, Park, high-pass filter, park inverse, Clark Inverse
We design servo drives based on FPGA to change the way businesses approach motion control. These highly customisable integrated circuits can be programmed to perform digital signal processing, control logic, data storage, and other functions.
FPGA in servo drives enables the implementation of advanced control algorithms to improve the precision and stability of motion control systems. Also, these solutions can handle high-speed data acquisition and processing, which can be used for real-time control, resulting in faster production cycles, increased throughput, and effective future upgrades and adjustments.
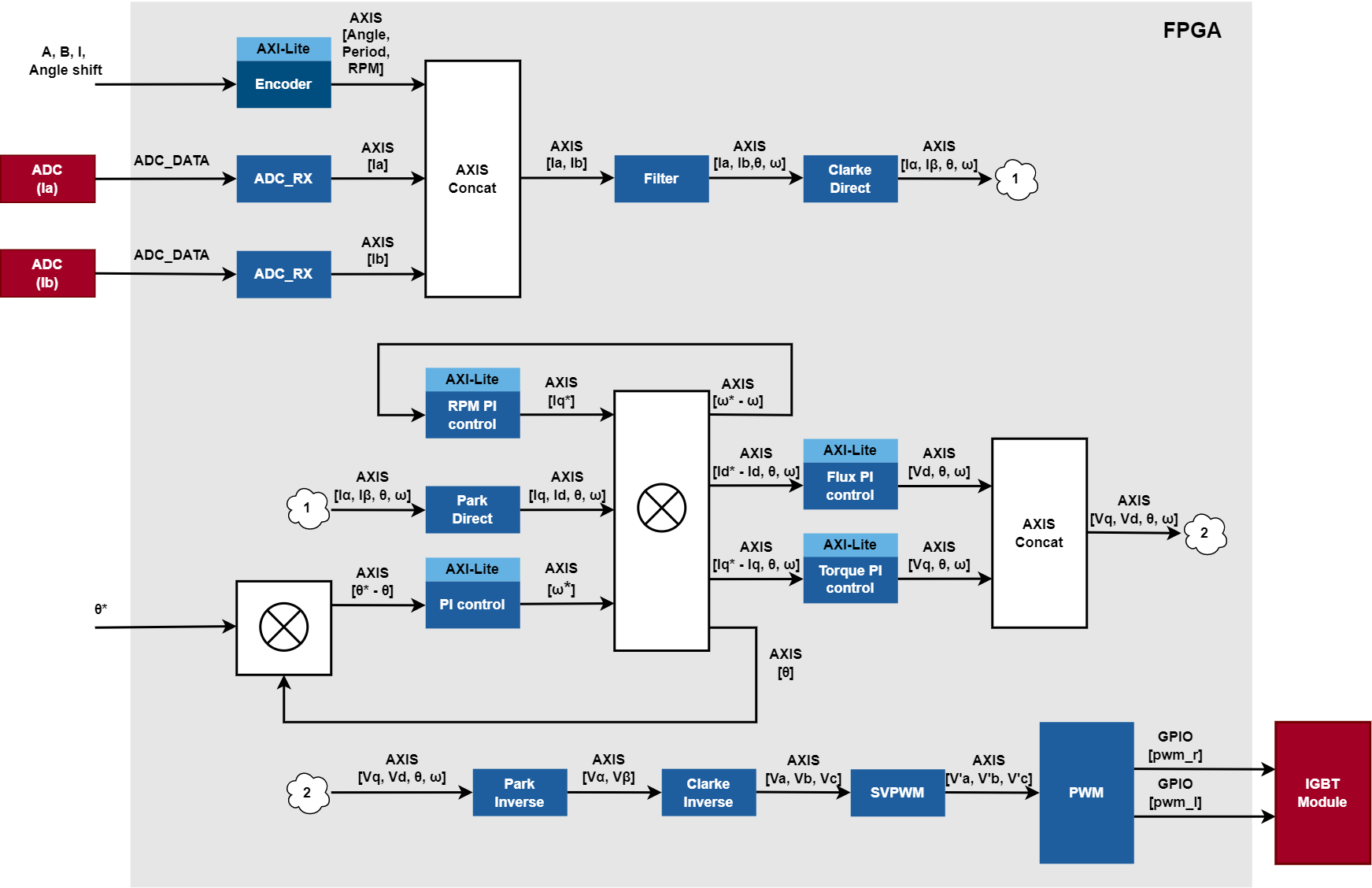
Back-electromotive force (BEMF) observer for permanent magnet synchronous motors (PMSM)
IP cores: PI/PID, Park inverse, Clark inverse, Sin/Cos
A BEMF observer is a sensorless control algorithm that estimates the rotor position of the PMSM, eliminating the need for physical sensors. The BEMF observer for PMSM on FPGA technology can be used in robotics, automation, and transportation.
By implementing this algorithm on this technology, businesses can achieve real-time control and high-performance motion control. It helps reduce energy costs, as BEMF observers can improve power conversion efficiency.
Additionally, the flexibility and scalability of FPGA technology allow the system to be easily updated, making it a cost-effective solution in the long run.
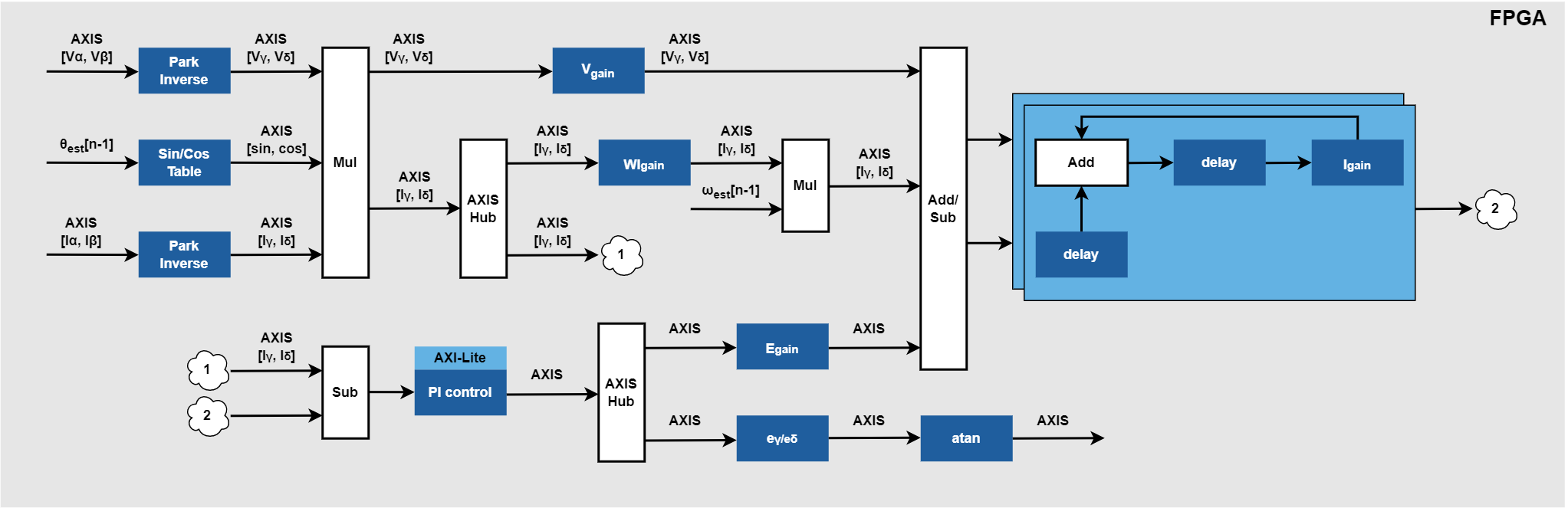
Inkjet printer controller
IP cores: sensored FOC BLDC, inkjet printer controller, PCIe
Single-pass inkjet printing systems require specialised logic to form images on paper accurately. To achieve this, our engineering team used separate IP cores to control the paper feed speed and the transfer of RAW images from memory.
The print controller utilises the speed setting provided by the IP core that is in charge of controlling the paper feed speed. This separation of functionality allows the system to be seamlessly upgraded.
Additionally, single-pass inkjet printing systems with specialised logic and IP cores provide a powerful and cost-effective solution tailored to the printing industry.
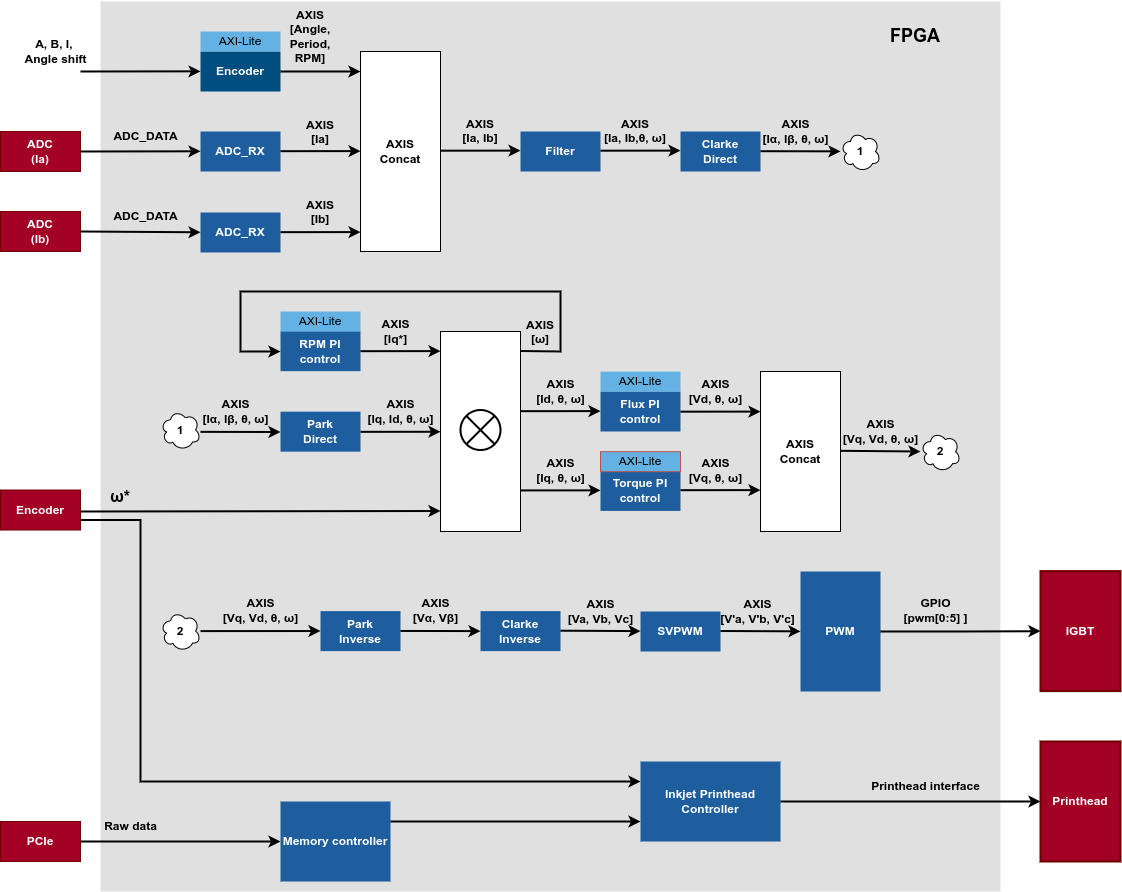
Multi-encoder master IP core interface
IP cores: EnDat 3, HIPERFACE DSL, SCS open link
We designed a solution for the multi-protocol position encoder interface to simplify the integration of fully digital encoder interfaces such as EnDat 3, Single Cable Solution (SCS) Open Link, and HIPERFACE DSL into industrial systems. This IP core is part of a black channel, meaning it does not require examination from a safety perspective, which greatly facilitates system integration.
The solution includes Safe 1 and Safe 2 interfaces to connect the safety part of the motor feedback system.
Safe 1 interface is used for configuration and reading a primary safety-related position and is structured as an array of 128 8-bit wide registers for memory-mapped read and write access.
Safe 2 interface is used for reading a secondary safety-related position, and it is structured as an array of 64 8-bit wide registers for memory-mapped read-only access.
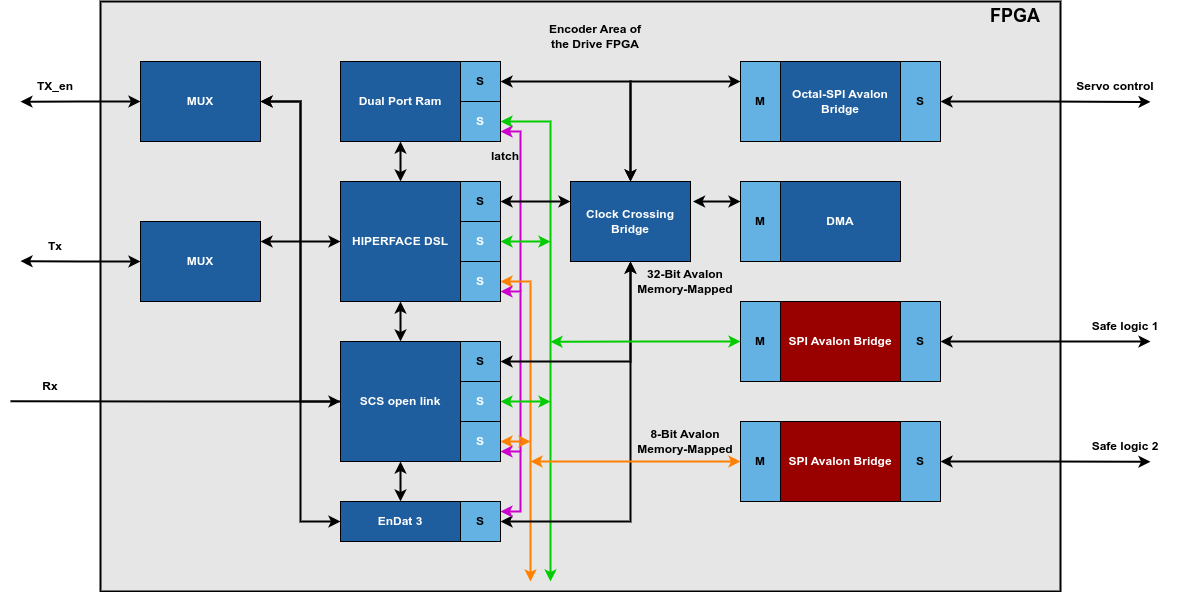
6-axis robot controller
IP cores: PCIe, 6 servo drive
Integrating servo drive IP cores into an FPGA is a robust solution for achieving optimal performance in robotics solutions. We ensured high precision and control by using up to 6 servo drive IP cores per FPGA.
We resolved dynamic and spatial orientation challenges for 6-axis robots with the NVIDIA Jetson Orin and Xavier platforms that provided next-level hardware solutions for robotics.
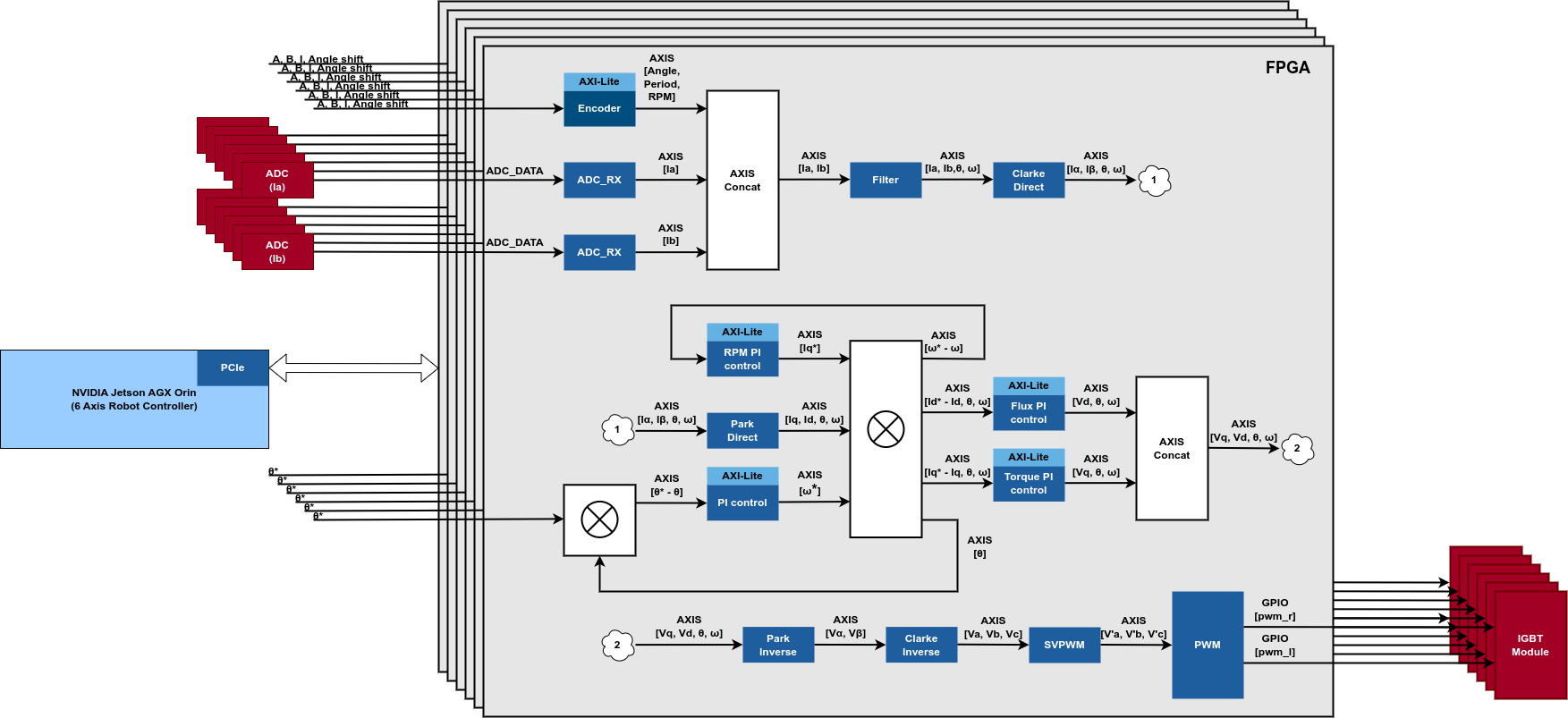
EtherCAT slave
IP cores: RGMII controller, loopback functions, asynchronous FIFO, AXIS switch, EtherCAT FMMU, SM, DPRAM, time module, memory controller
EtherCAT is an Ethernet-based fieldbus system for industrial automation. It ensures fast and precise communication between devices.
By integrating EtherCAT slave on FPGA, businesses can achieve real-time communication, high-performance motion control, and efficient data processing.
Our engineers can integrate this solution with other systems, such as PLCs and HMIs, reducing system costs and increasing the overall system's efficiency.
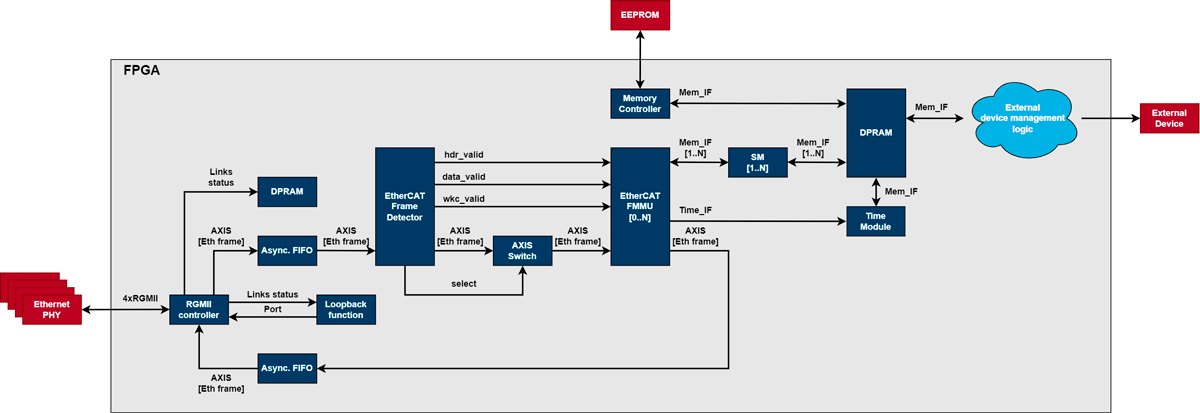
Design of 3D lidar
IP cores: register file, AXI DMA, CPACK, RX JESD TPL, RX JESD LINK, JESD PHY, SYNC, TIA channel sequencer, PWM, motor control, laser driver IP, memory interconnect, PCIe
High-level specification
Key features:
- Horizontal resolution of 16 pixels
- Data sampling up to 1GSPS on 4 separate channels
- The design is verified to comply with class I laser safety
- Standardised FMC connector plugs into the FPGA board of choice
- Out-of-box demo for target range measurement
- Complete open-source software framework
- Licensable JESD204B interface framework for deterministic data delivery to host wrappers for Matlab, Python LiDAR-specific API for system control and data acquisition.
The platform development environment supports industry-standard Linux Industrial I/O (IIO) applications, MATLAB, Simulink, custom C/C+, Python, and C# applications, HDL reference designs, and drivers to allow zero-day development.
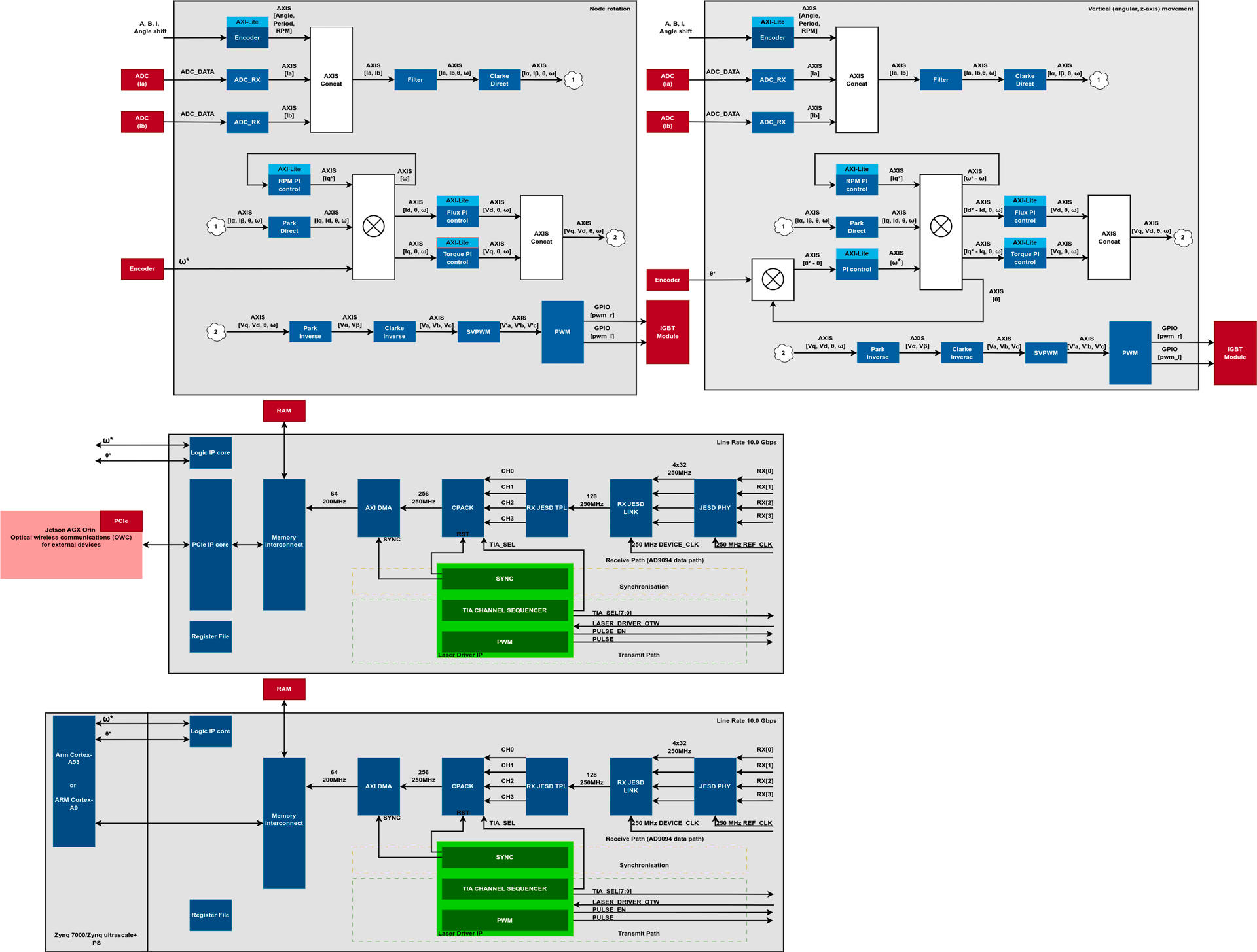
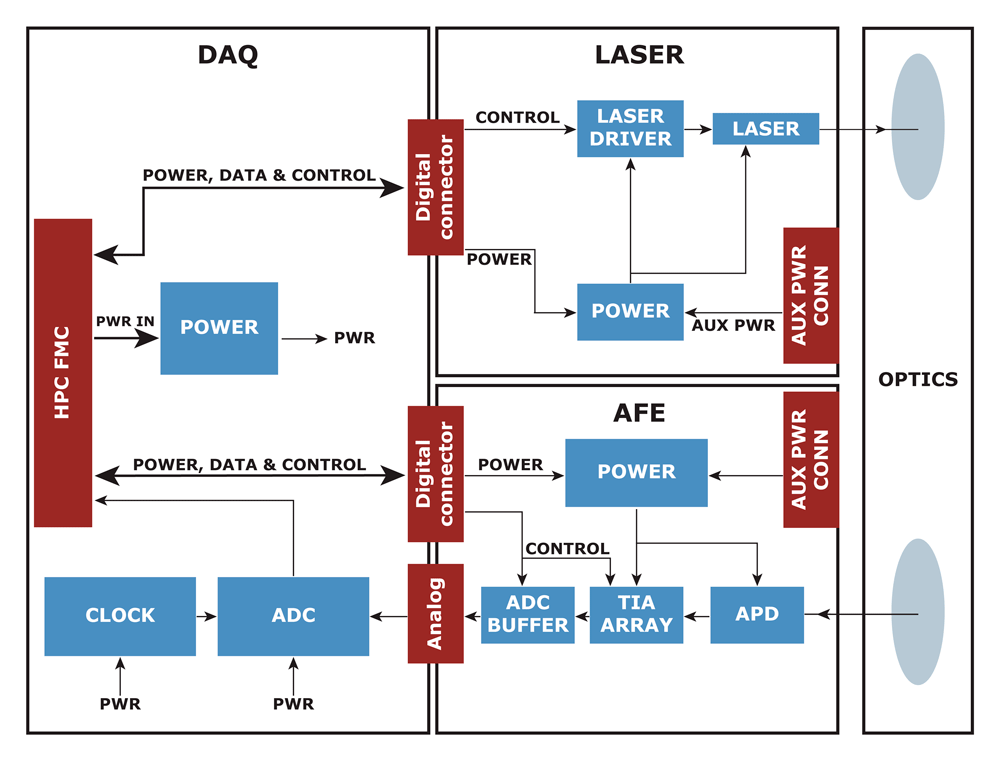
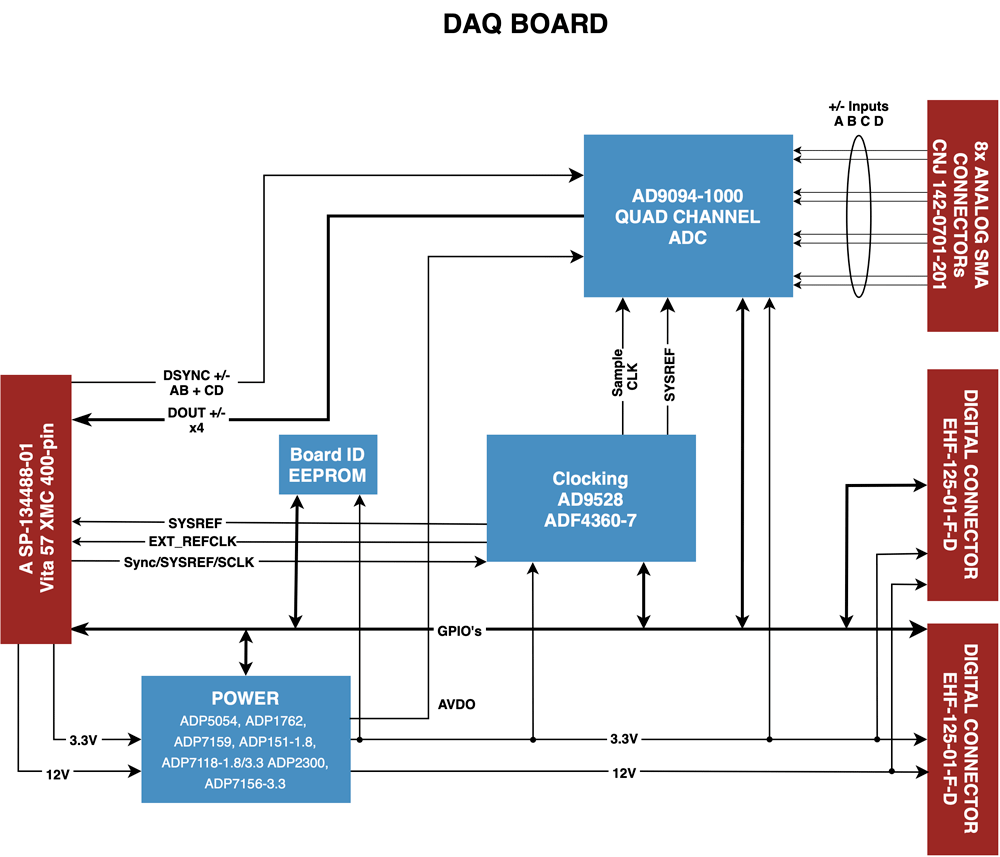
DAQ Board
High-speed data acquisition board containing the AD9094 quad-channel ADC and clocking control for the full system. The FMC-compliant connector interface means that this board can be connected to the user’s preferred development board. The laser and AFE boards connect directly to this solution.
Laser Board
The laser board is mated to the AFE board for mechanical mounting on an optional tripod stand. Then it is connected electrically to the DAQ board using the cable provided. It contains 4 individual lasers with an appropriate precision driver and power components for the accurate firing of the lasers. To alter the laser field-of-view, custom fast-axis collimator optics are available from optics suppliers.
AFE Board
The AFE board contains a 16-channel APD from the first sensor and 4 ADI LTC6561 Quad channel TIA's with necessary power and timing signal chains. Custom optics can be fitted to the board using industry-standard mounting adapters based on individual use cases.
The real-time processing capabilities of FPGA allow for the fast and accurate acquisition of 3D data, providing a high level of precision in navigation and object detection. This can improve safety, efficiency, and productivity in various applications.
The integration of 3D lidar on FPGA technology also enables businesses to reduce the size, cost, and power consumption of their systems.
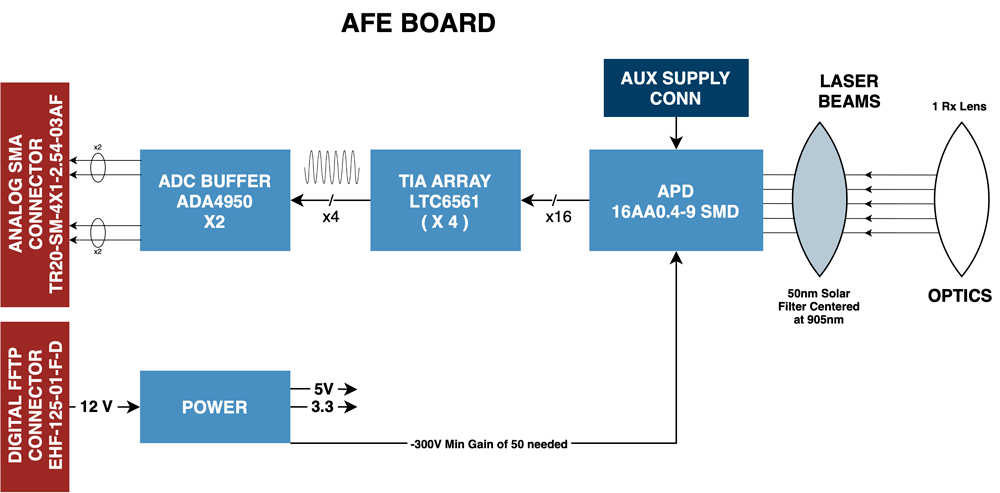
Design of automatic transfer switch (ATS)
IP cores: RMS, SAG, SWELL, power factor, apparent power, reactive power, real power, period and phase angle detector, timer, prediction control, FFT, filter, interrupt controller, memory controller, ADC_RX, logic ATS, ZCR detector
An automatic transfer switch (ATS) is an essential technology for ensuring the uninterrupted operation of network equipment. ATS solutions can be implemented using microcontrollers or DSPs, but FPGA technology provides greater flexibility and reliability.
Our engineers integrated RISC-V soft CPUs that enhanced the performance of the entire system. This approach not only improved the reliability of ATS but also allowed easy updates and upgrades to the system.
Overall, FPGA-based automatic transfer switch solutions provide a powerful, reliable, and flexible approach to ensure the uninterrupted operation of the network equipment.
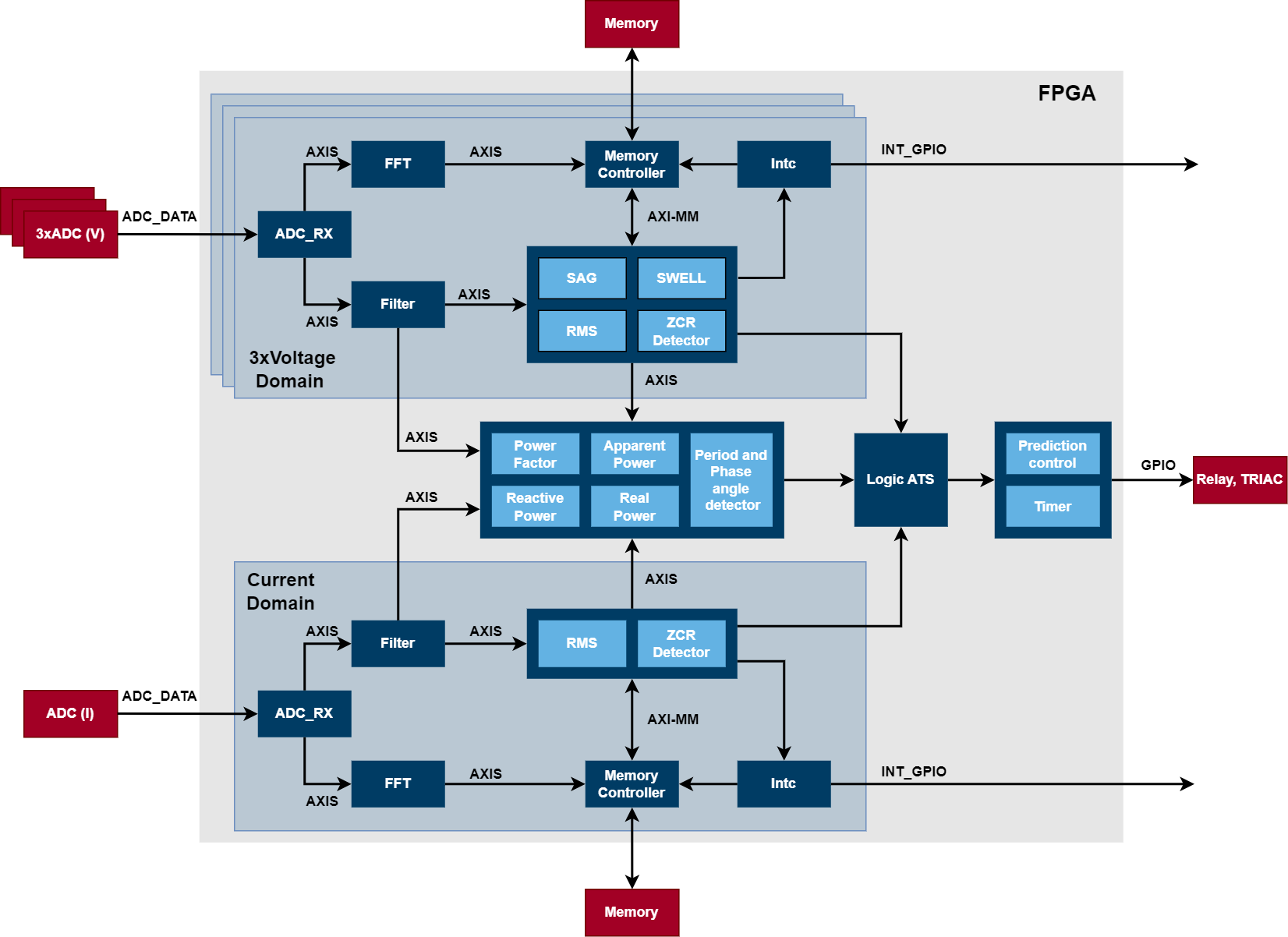
Three-phase electrical network analyser
IP cores: RMS, SAG, SWELL, power factor, apparent power, reactive power, real power, period and phase angle detector, FFT, filter, interrupt controller, memory controller, ADC_RX, ZCR detector, register file
We used FPGA technology to develop an advanced solution for power quality analysis. This new three-phase network analyser can be implemented using various hardware platforms.
The technology offers a new level of quality in the data provided on currents, voltages, frequency, parasitic harmonics, and more.
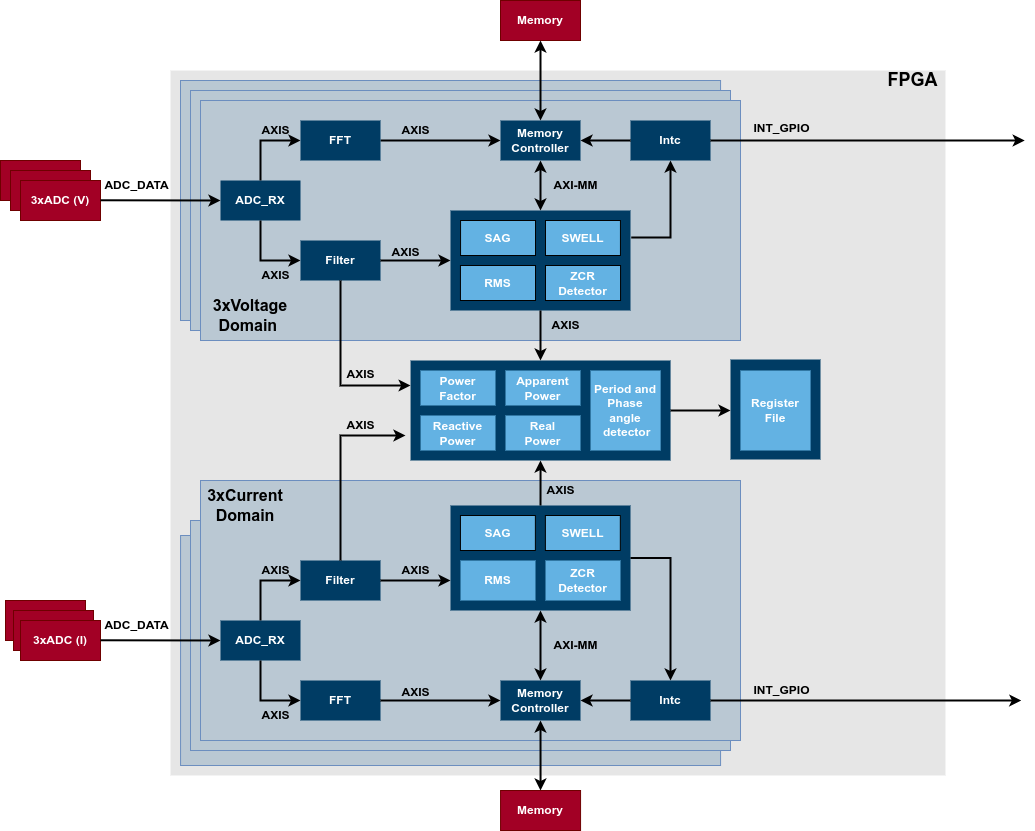
Mass flow metering
IP cores: ADC_RX, low-pass filter, Fourier analysis, register file, PID/PI controller, sine wave synthesis, SUM, zero-crossing detection (ZCR), drive synthesis control, DAC_TX, memory controller, calculate sine wave synthesis parameters, calculate balance terms
Coriolis mass flow measurement technology is the most accurate and reliable method for direct mass flow measurement. This technology utilises the Coriolis effect, where the oscillation of a vibrating tube is distorted by the flow of fluid passing through it, to measure the mass flow of fluids.
The designed flow metre is highly versatile and capable of operating under challenging process conditions, including two-phase flow. The technology is successfully implemented in commercial metres and is widely used in various industrial applications.
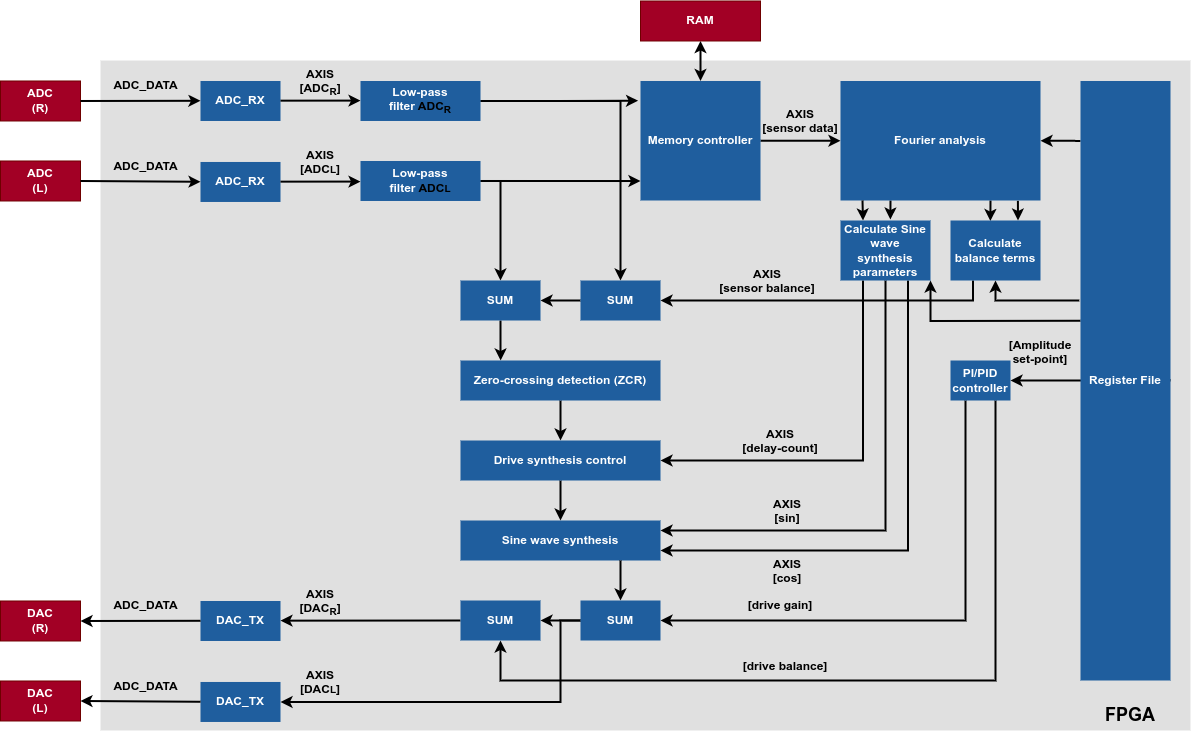
HSR/PRP protocols
IP cores: servo clocks, MAX, IEEE 1588 MAC, DEMUX, untagger, tagger, mux, queue, interconnection, 3x PDelay response, timestamp, frame parsing, timestamp buffer, correction TX, correction RX
IEC 61850-90-4, a standard for communication networks and systems in power automation. It uses Ethernet with the PRP and HSR protocols defined in IEC 62439-3 as a global standard for bus systems and process buses in substations.
PRP and HSR protocols involve zero-recovery time, which means that in the event of a network failure, communication does not stop, and there is no frame loss. This feature allows for the seamless connection and disconnection of devices without interrupting the network's workflow or other devices. It is critical for businesses that require high availability, reliability, and robustness in their industrial automation networks.
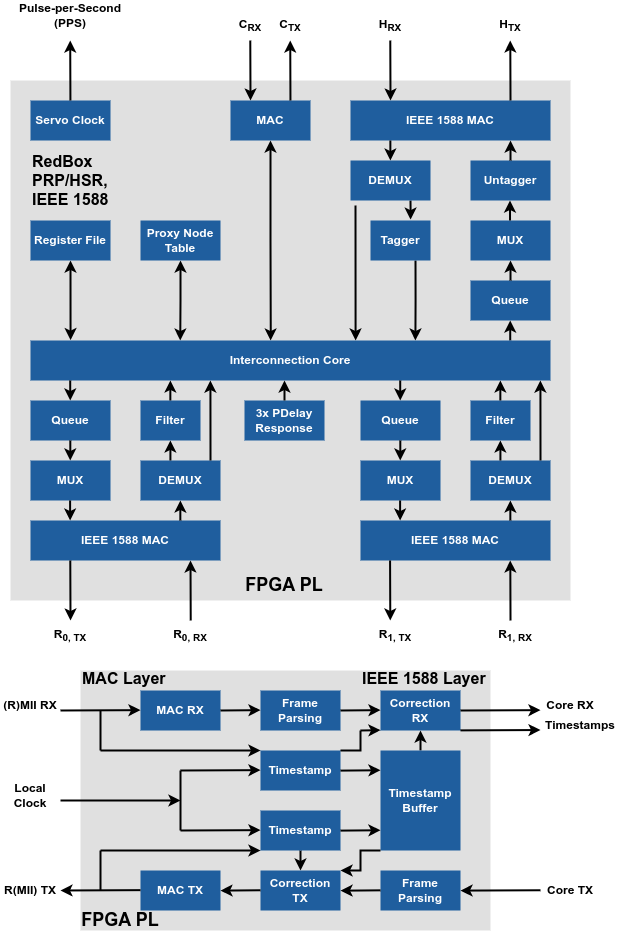
C37.94 transceiver IP core for teleprotection equipment
Our engineering team developed the C37.94 transceiver IP core for teleprotection equipment with full test coverage. This design is available for sale to companies that want to significantly reduce the time required to implement FPGA-based projects.
Key features:
- Error injection for standalone IP core simulation
- Fully compatible with standard IEEE Std C37.94â„¢-2017
- Support 1 to 12 time slots
- Master and slave modules available
- Internal clock data recovery
- Status flags
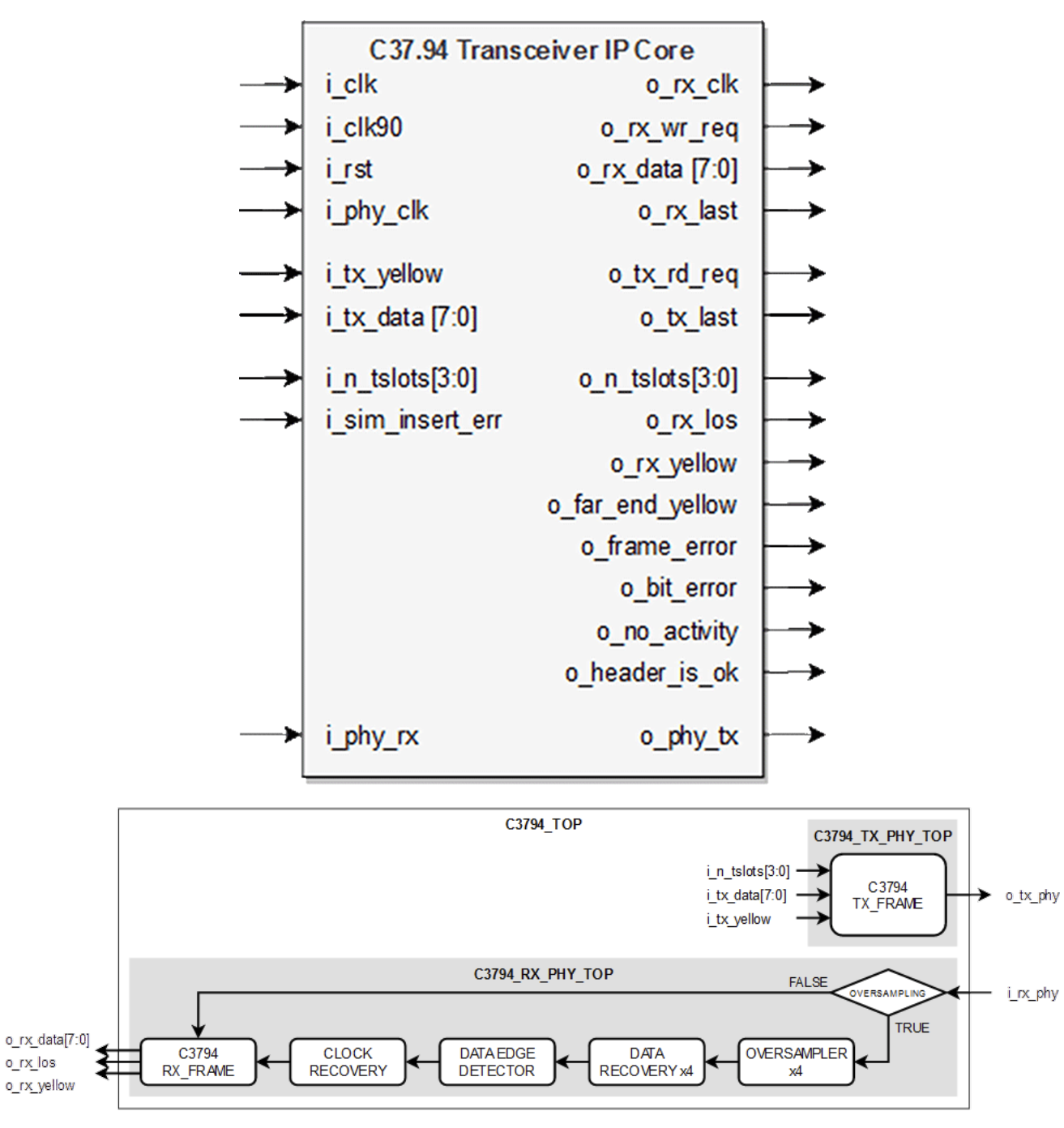
Safety PLC
IP cores: input driver, comparators, register, output block
FPGA-based safety PLCs process safety-critical control algorithms in real-time, providing high protection for personnel and equipment. This can improve security, efficiency, and productivity in various applications.
Integrating safety PLC can help businesses meet the newest safety standards and compliance requirements. It also allows for integrating several safety functions on a single platform.
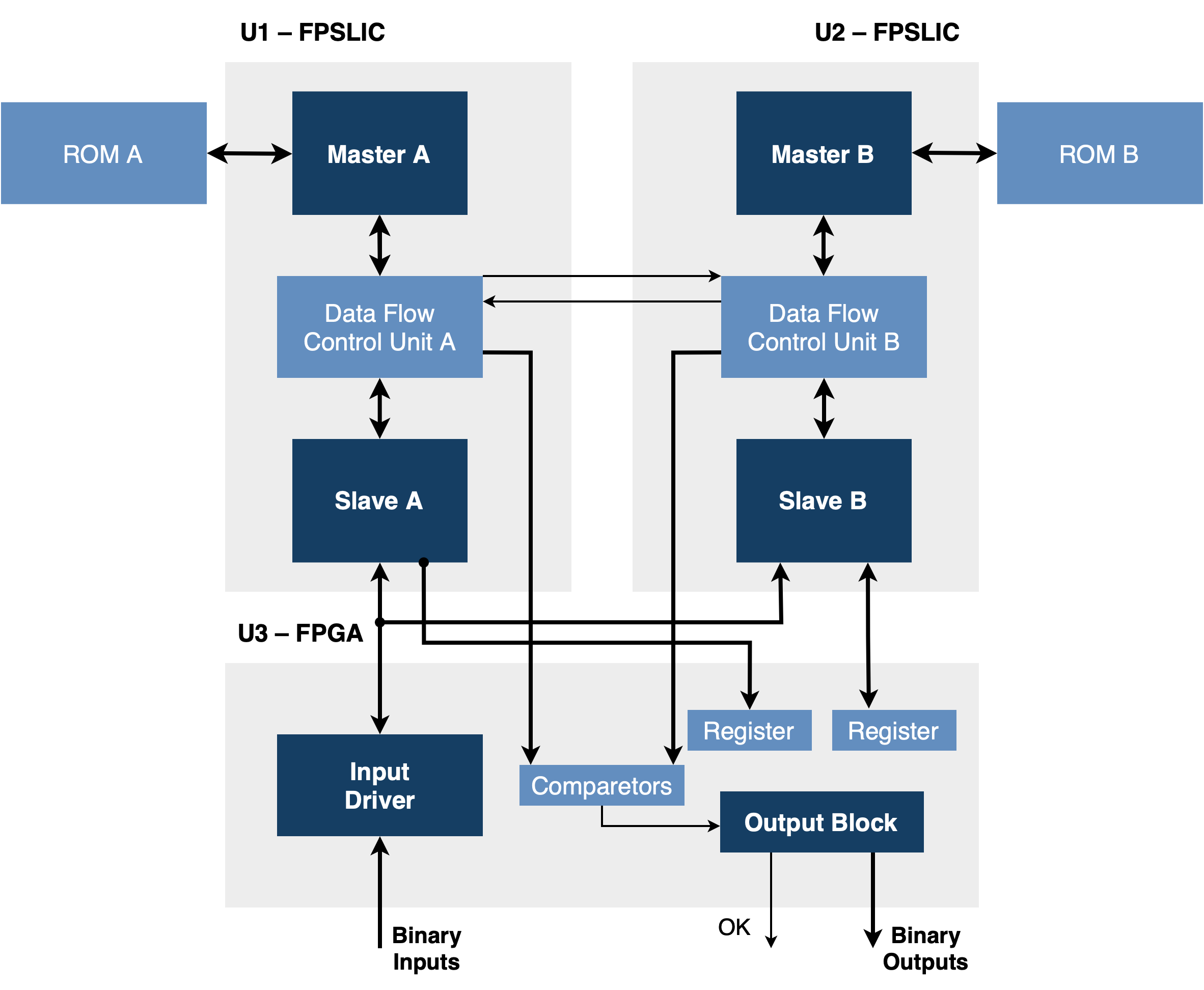
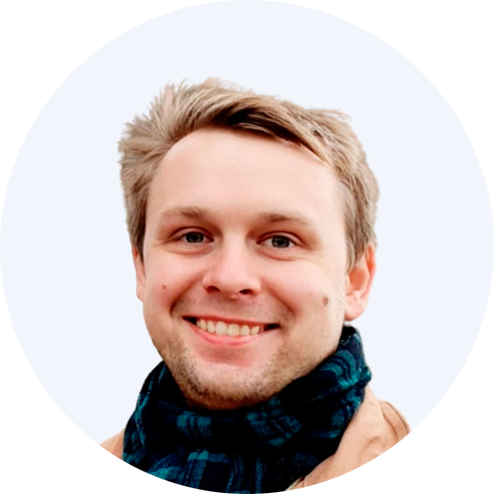
"FPGAs provide the versatility and flexibility needed to meet the ever-evolving demands of industrial automation, robotics, and energy sectors. The programmability of FPGAs enables us to design highly efficient real-time systems that can adapt to changing requirements and push performance boundaries. This makes FPGAs a powerful tool for addressing the most complex challenges in these industries."
— Roman Shuliankou, Head of Industrial Automation & Robotics
Our Case Studies in Industrial Automation
Do you need a quote for your FPGA design services for industrial automation and robotics?
Drop us a line about your project! We will contact you today or the next business day. All submitted information will be kept confidential.
FAQ
What are the advantages of using FPGAs in industrial automation?
- High-performance and real-time processing.
- Flexibility and reconfigurability.
- Energy efficiency.
- Improved reliability and ruggedness.
- Short time-to-market for new products.
- Cost savings compared to custom ASICs.
- Support for multiple standards.
- Industrial Networks (EtherCAT, PROFINET IRT).
- Support for absolute and incremental encoders (BISS, SSI, EnDat).
How do FPGAs improve the performance of robotics systems?
- Real-time processing.
- Parallel processing of multiple tasks.
- Low-latency communication.
- Improved accuracy and control.
- Enhanced signal processing capabilities.
- Increased system efficiency and reduced power consumption.
- Оne FPGA for 6, 10, or more axes.
- Industrial Networks (EtherCAT, PROFINET IRT).
- Support for absolute and incremental encoders (BISS, SSI, EnDat).
What are the benefits of using FPGAs in motion control systems for industrial automation?
- Real-time control and fast response times.
- Improved accuracy and precision.
- High-speed digital signal processing.
- Customizable and flexible hardware.
- Reduced system latency and jitter.
- Cost savings compared to custom ASICs.
- Оne FPGA for 6, 10, or more axes.
- Industrial Networks (EtherCAT, PROFINET IRT, etc.).
- Support for absolute and incremental encoders (BISS, SSI, EnDat).
What are the benefits of using FPGAs in industrial networking and communication systems?
- High-speed data processing and low-latency communication.
- Flexible and reconfigurable hardware design.
- Support for multiple protocols and standards.
- Improved security and data encryption.
- Reduced power consumption and improved reliability.
- Cost savings compared to custom ASICs.