Delta Robot Design for Conveyors
Project in a Nutshell: We designed a custom delta robot for a UAE conveyor equipment manufacturer, enabling them to reduce dependence on global suppliers and offer a scalable, tailored solution to increase customer loyalty.
Powered by the NVIDIA Jetson Orin Nano controller running Linux + RTOS and the Infineon XMC 4800-based servo drives, the robot leverages EtherCAT for precise synchronisation and meets global standards.
Customised delta robotics are used not only in conveyor technology but also in the packaging, assembly, and logistics industries. They help to reduce costs by improving operational accuracy and ensuring flexible production processes.
Client & Challenge
A conveyor equipment manufacturer from the United Arab Emirates asked us to develop a custom delta robot for their conveyors.
Our client had two objectives:
- To create their own solution and reduce their dependence on global suppliers such as ABB and Fanuc.
- To keep their customers in their own ecosystem, ensuring long-term cooperation through unique customised designs.
The client chose Promwad due to our experience creating complex robotic systems, deep understanding of automation tasks, and development expertie with modern NVIDIA and Infineon platforms.
Solution
We designed a state-of-the-art delta robot platform based on the NVIDIA Jetson Orin Nano controller running Linux and RTOS for real-time operation. The controller manages the robot's movement and task execution, providing high-speed and accurate operations.
We chose the Infineon XMC 4800 platform for the servo drives development. Data exchange and real-time synchronisation of the servo drives with the central control unit is achieved via EtherCAT.
How Servo Drives Work:
The high precision and speed of delta robots are achieved with a three-level drive control system, each level responsible for a certain aspect of the motors:
- A position loop controls the precision of the movement and ensures automatic adjustments when necessary.
- A velocity loop controls the speed of the arms, allowing the delta robot to move quickly and smoothly between set points, which is especially important for pick-and-place tasks.
- A current loop regulates the current to the motors, reducing the risk of overloading and ensuring stable robot operation even under high load.
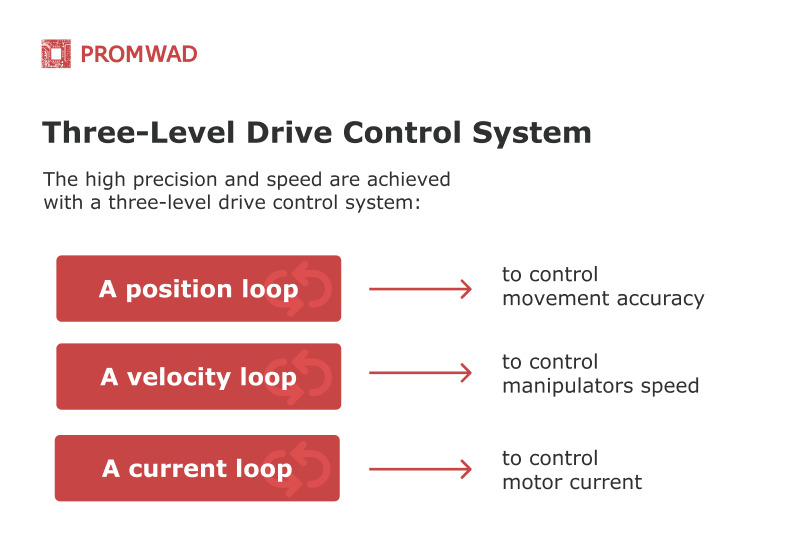
For control and precision, we equipped the robot with the MIPI CSI-2 (Camera Serial Interface 2), which provides two cameras located on either side of the work area.
Kinematics
The created delta robot is a three-arm design with a fixed base connected to a moving platform. As the motors are located on the base and the moving parts are lightweight, the delta robot is ideal for pick-and-place tasks.
The main challenge in working on the delta robot design is calculating its kinematics: the mathematical calculations required to ensure accurate moves of the working part.
In developing the delta robot, we solved two key problems:
- Inverse kinematics. In order to move the working part of the robot (the end effector) to a given point, for example (X, Y, Z), we need to calculate the angles of the three arms. We did this by knowing the dimensions of the robot and determining the angles for each arm, starting with one in the YZ plane and then repeating the calculations for the other two, taking into account the symmetry of the structure. This allows for precise positioning of the end effector.
- Forward kinematics. If the angles of the levers are known, we can calculate the current position of the working tool. To do this, we determined the lever joint points, built three spheres around them and found their intersection — this was the position of the working part (X, Y, Z).
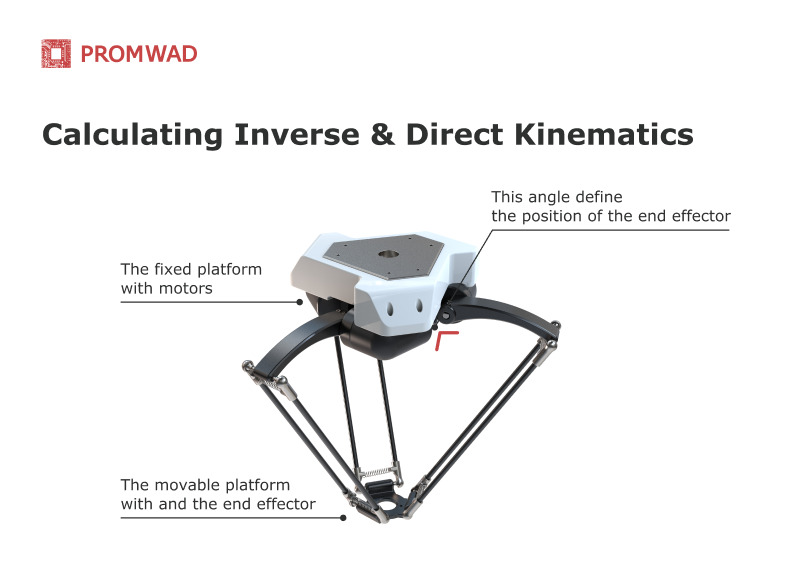
These calculations allow the robot to move accurately, smoothly, and efficiently to perform tasks.
Delta Robot Software Control
To control the motion of the delta robot, we developed two main programs: one to calculate the position of the working tool (forward kinematics) and one to determine the rotation angles of the arms (inverse kinematics). These functions are written in C and use robot design parameters such as arm lengths and platform dimensions.
Business Value
Our client received a branded robotic solution, enabling them to reduce their dependence on international suppliers and build long-term relationships with their customers.
The newly designed advanced product meets global standards, is customised to the specific needs of the local market, and can be scaled and adapted to future requirements.
More of What We Do for Robotics
- Robotics Design Services: check out our robotics software and hardware development services.
- Universal Platform for Service Robots: a case study on the development of an Qualcomm-based and AI-powered autonomous service robot.
- Solving Critical Compatibility Problem: how we solved the interoperability challenges of industrial robotics platforms with Hilscher netX.