How Industrial Designers and Mechanical Engineers Collaborate in Hardware Projects
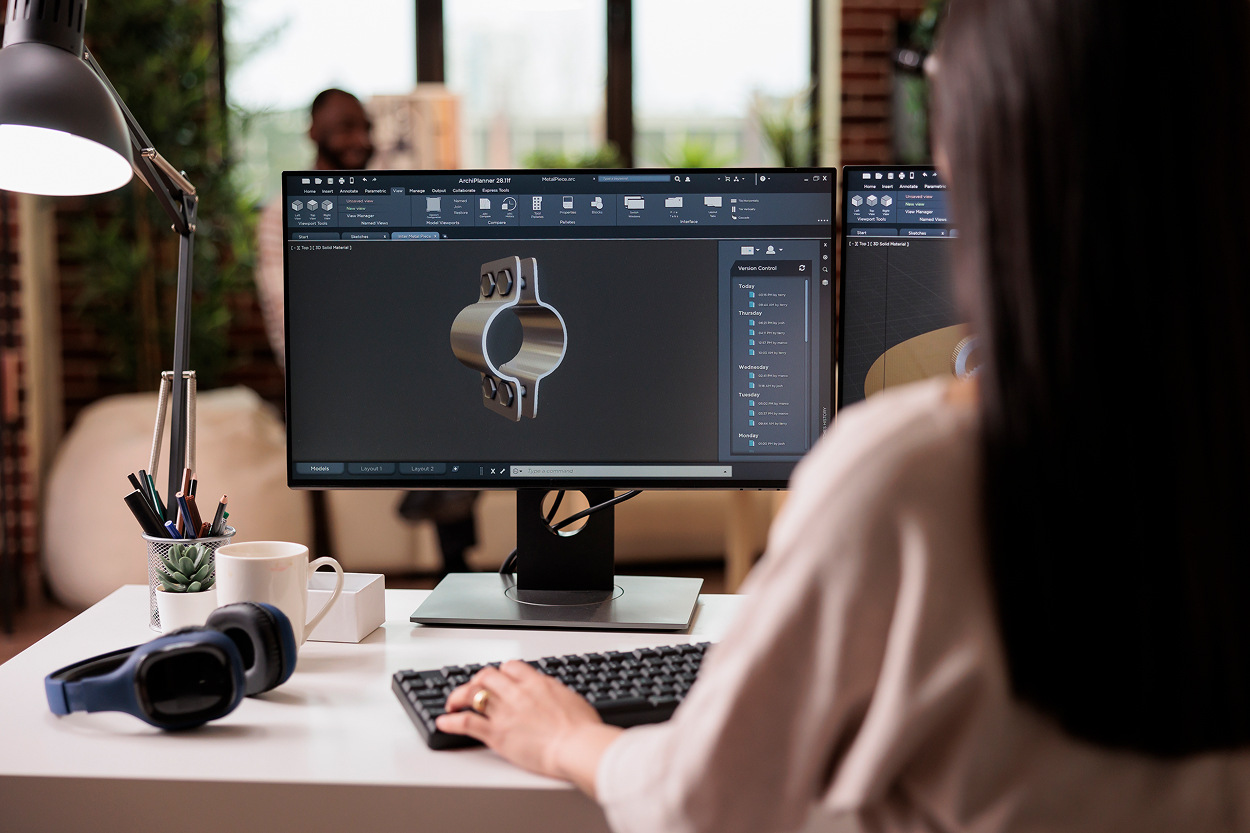
Why Designer–Engineer Collaboration Is Critical in Product Development
Too often, hardware products suffer from a split-brain problem: designers aim for beauty and usability, while mechanical engineers focus on constraints, tolerances, and manufacturability. When these teams work in silos, the result is friction, redesigns, and delayed launches.
But when design and engineering teams collaborate from day one, the result is products that look great, feel intuitive, and can be manufactured efficiently.
This article explores how close collaboration between industrial designers and mechanical engineers transforms product development — based on lessons from real-world Promwad projects.
Where Designer and Engineer Perspectives Meet
Area of Collaboration | Designer Focus | Engineer Focus |
Product shape & aesthetics | Visual balance, brand, emotion | Draft angles, tooling limitations |
Material choices | Tactility, color, feel | Strength, moldability, thermal behavior |
Mounting & assembly | Seamless surfaces, hidden fasteners | Accessibility, torque specs, part count |
User interaction | Ergonomics, button size, visibility | PCB placement, backlighting, tolerances |
Prototyping | Rapid feedback on proportions | Fit testing, validation, DFM |
By acknowledging each other’s goals early, teams create shared solutions rather than tradeoffs.
When Designers and Engineers Work in Sync
Here’s how this synergy plays out in practice:
1. Shared Design Reviews
- CAD + rendering sessions
- Material samples on the table
- Shared feedback on UI layout and mechanical alignment
2. Parallel Development Paths
- Designers start sketching and 3D modeling as engineers define PCB constraints
- Engineers simulate heat and vibration while designers refine grip and interface
- UI and enclosure evolve together for screen-based devices
3. Mutual Tool Access
- Designers review PCB layout in Altium viewer or 3D CoDesigner
- Engineers visualize surface finishes and lighting in KeyShot or Blender
- Everyone gains empathy for the others’ challenges
Common Challenges and How to Overcome Them
Challenge | Mitigation Strategy |
Design doesn’t match PCB size | Share board outline early and revise collaboratively |
Enclosure can’t be manufactured | Review DFM with both parties before tooling starts |
UI concept ignores hardware limits | Align display types, power budget, sensors in concept |
Late-stage layout changes | Use shared revision log and lock key parameters early |
Cross-functional planning beats post-handoff escalation every time.
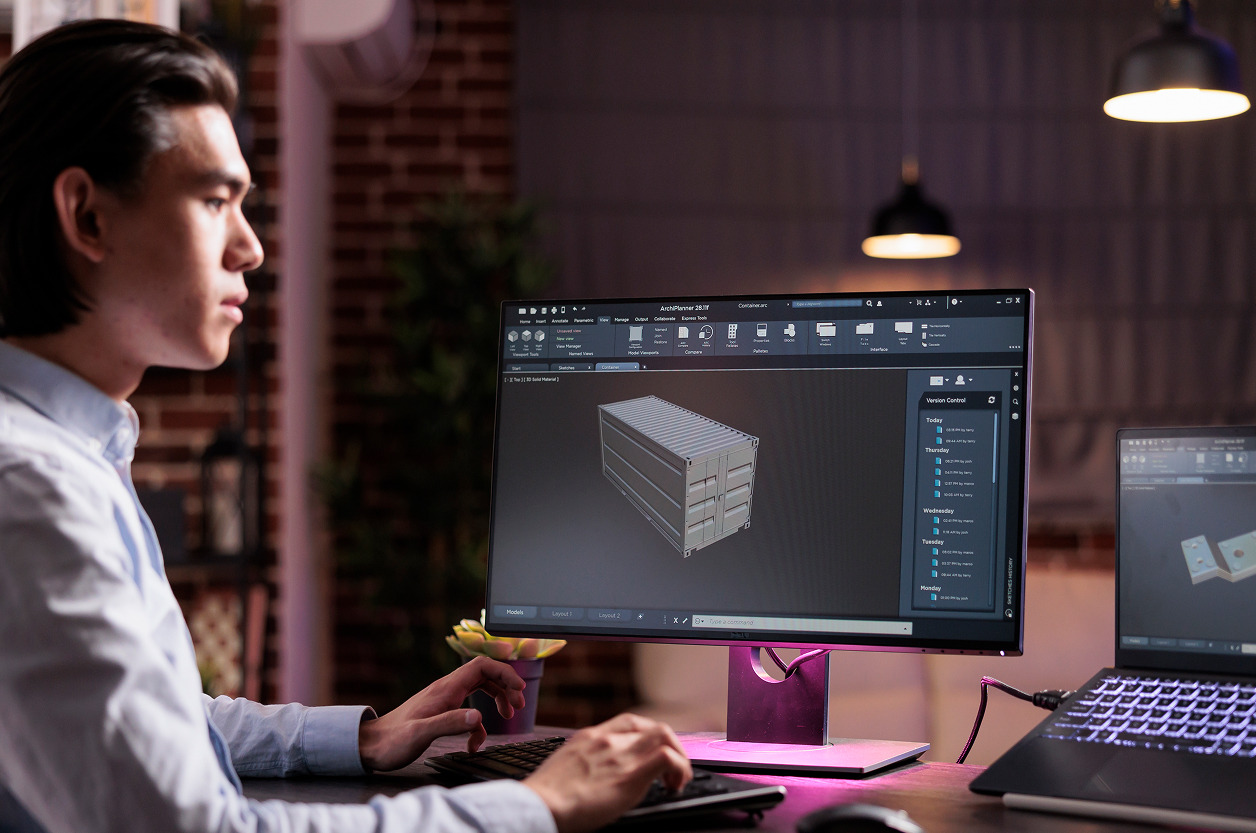
Real-World Collaboration: Promwad Examples
- Set-top box project: A sleek enclosure concept required snap-fit latches — but these interfered with antenna performance. Our joint team iterated on latch geometry and antenna tuning simultaneously.
- Medical wearable: The industrial design called for a seamless soft-touch finish. Mechanical engineers adapted parting lines and insert molding techniques to meet both tactile and manufacturing needs.
- Sensor gateway: Heat dissipation was a concern. Designers and engineers collaborated on fin placement and internal airflow, balancing looks with thermal performance.
Tools That Foster Better Collaboration
Tool | Used For |
Altium CoDesigner | Real-time PCB + enclosure alignment |
Fusion 360 | Shared 3D modeling and simulation |
Miro / FigJam | Concept sketching and interface brainstorming |
Notion / Confluence | Shared specs, design goals, decision logs |
Tooling is only half the story — the mindset is what makes the tools work.
Final Thoughts
The best hardware products don’t happen when designers hand off and engineers figure it out. They’re born from integrated thinking, iterative problem-solving, and mutual respect between disciplines.
At Promwad, our industrial designers and mechanical engineers build together from day one — shaping products that deliver delight and durability.
Let’s co-design your next product, the right way.
Our Case Studies in Industrial Design