Designing CNC-Milled Enclosures for Electronics: Benefits, Challenges, and Best Practices
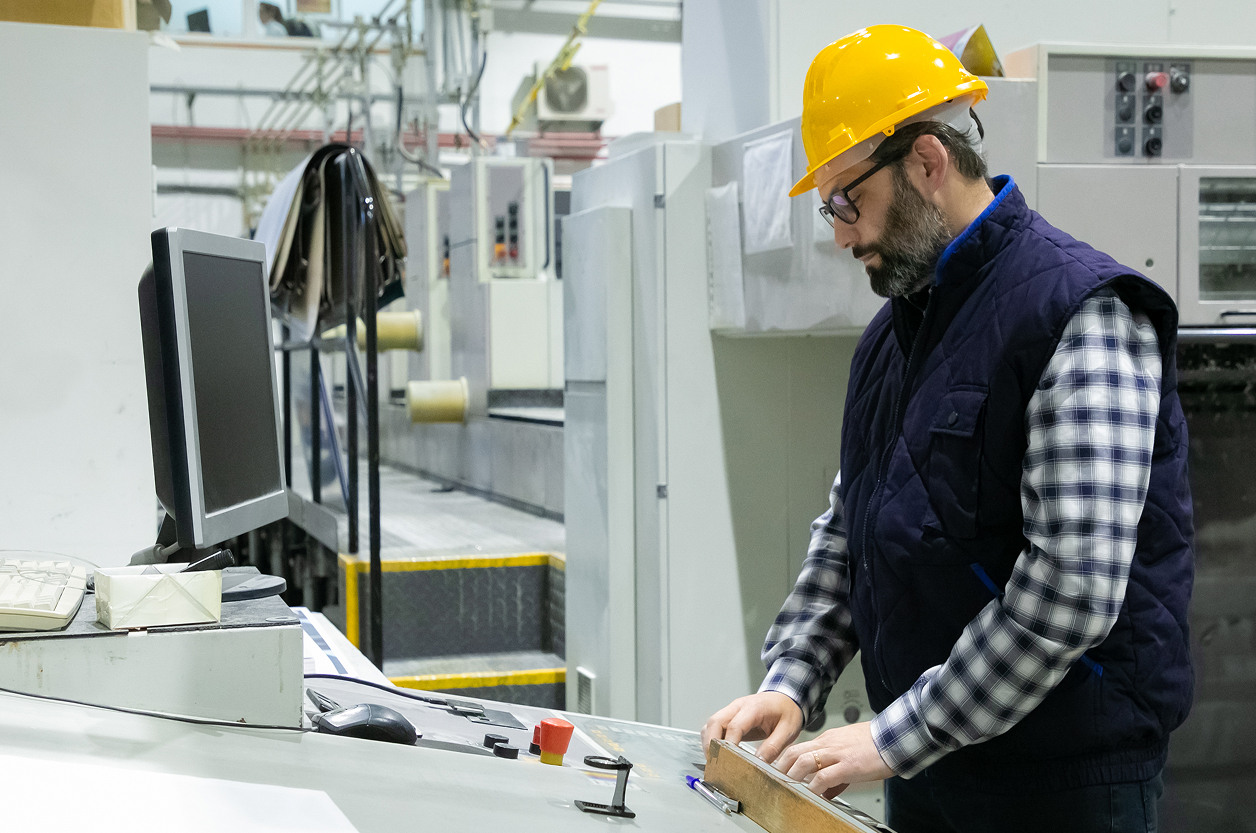
Why CNC-Milled Enclosures Are Gaining Popularity in Modern Electronics
Injection molding dominates large-scale production, but when you need flexibility, speed, and mechanical precision, CNC-milled enclosures are often the best path forward. Whether you’re prototyping, manufacturing in small batches, or building rugged devices for harsh environments, milled enclosures bring unmatched mechanical strength and design freedom.
In this article, we break down the real-world advantages, design constraints, and tips for successful CNC-machined enclosure development — based on Promwad’s experience in industrial, automotive, and telecom device engineering.
What Is a CNC-Milled Enclosure?
CNC milling is a subtractive manufacturing process where material (usually aluminum or plastic) is precisely removed using multi-axis machines. For electronics enclosures, this means:
- Monolithic construction with no parting lines
- High dimensional accuracy
- Excellent EMI shielding and thermal performance (especially with metal)
- Low to medium volume production capability (10 to 5,000+ units)
Why Use CNC Milled Enclosures?
Advantage | Description |
Rapid production cycles | No tooling means faster development |
Design iteration flexibility | Easy to update CAD and re-run small batches |
Superior strength and stability | Especially true for aluminum and stainless steel |
Surface finish and detail quality | Machined logos, tight tolerance ports |
Thermal performance | Direct heat transfer to enclosure body |
For highly engineered products — like network switches, RF modules, or sensor gateways — milled housings are often a strategic choice.
Common Materials for Milled Enclosures
Material | Pros | Considerations |
Aluminum 6061 | Lightweight, machinable, corrosion-resistant | May need anodizing or powder coating |
Aluminum 7075 | Very strong, used in aerospace and defense | More expensive, harder to machine |
Stainless Steel | Rugged and impact-resistant | Heavy and costly |
POM (Delrin) | Rigid engineering plastic, good for insulators | No EMI protection, thermal limits |
PC, ABS | Used for internal parts or hybrid assemblies | Limited durability for outer cases |
Design Constraints for CNC Milling
Despite the flexibility, CNC machining has physical and economic constraints:
- Minimum Wall Thickness: Metal: 1.0–1.5 mm typical; Plastic: 1.5–2.5 mm minimum to avoid vibration
- Undercuts: Generally avoided; require special tooling or manual operations
- Internal Corners: Rounded due to tool diameter (typically 1–3 mm radius). Avoid expecting sharp 90° corners inside cavities
- Tolerancing: Typical: ±0.05 mm achievable. Necessary for fit with PCBs, connectors, and gaskets
- Surface Finish: As-milled, bead-blasted, anodized, powder-coated. Cosmetic surfaces may require polishing or masking
When CNC Milling Beats Injection Molding
Factor | CNC Milling | Injection Molding |
Development speed | Fast: No tooling | Slower: Tooling takes weeks/months |
Design change flexibility | Easy to modify CAD and re-run | Requires costly tooling adjustments |
Volume suitability | Low to medium (10–5,000 units) | Best at 5,000+ units |
Part durability | High for metal, variable for plastics | Medium to high (depends on material) |
Initial investment | Low | High (due to molds) |
Applications That Rely on CNC-Milled Enclosures
- Telecom & Networking – Heat-dissipating aluminum bodies for high-power switches and gateways
- Industrial IoT – Ruggedized units with IP65/67 sealing, milled gasket channels
- Medical Devices – Machined housings with precision threads and tight tolerances
- Automotive – Prototypes and low-volume control modules with integrated heat sinking
These are applications where EMI shielding, thermal control, or customization speed are business-critical.
How Promwad Designs Milled Enclosures
Our typical workflow:
- Mechanical Requirements Gathering – Impact rating, ingress protection, mounting method
- 3D Modeling and Drafts – Define clearances, component layout, machining directions
- Simulation and DFM Review – Thermal analysis, vibration behavior, manufacturing cost
- Pilot Production – Small batches for testing and field trials
- Surface Finishing – Anodizing, powder coating, laser marking as needed
We integrate electronics and enclosure design to ensure proper thermal dissipation, antenna behavior, and internal fit.
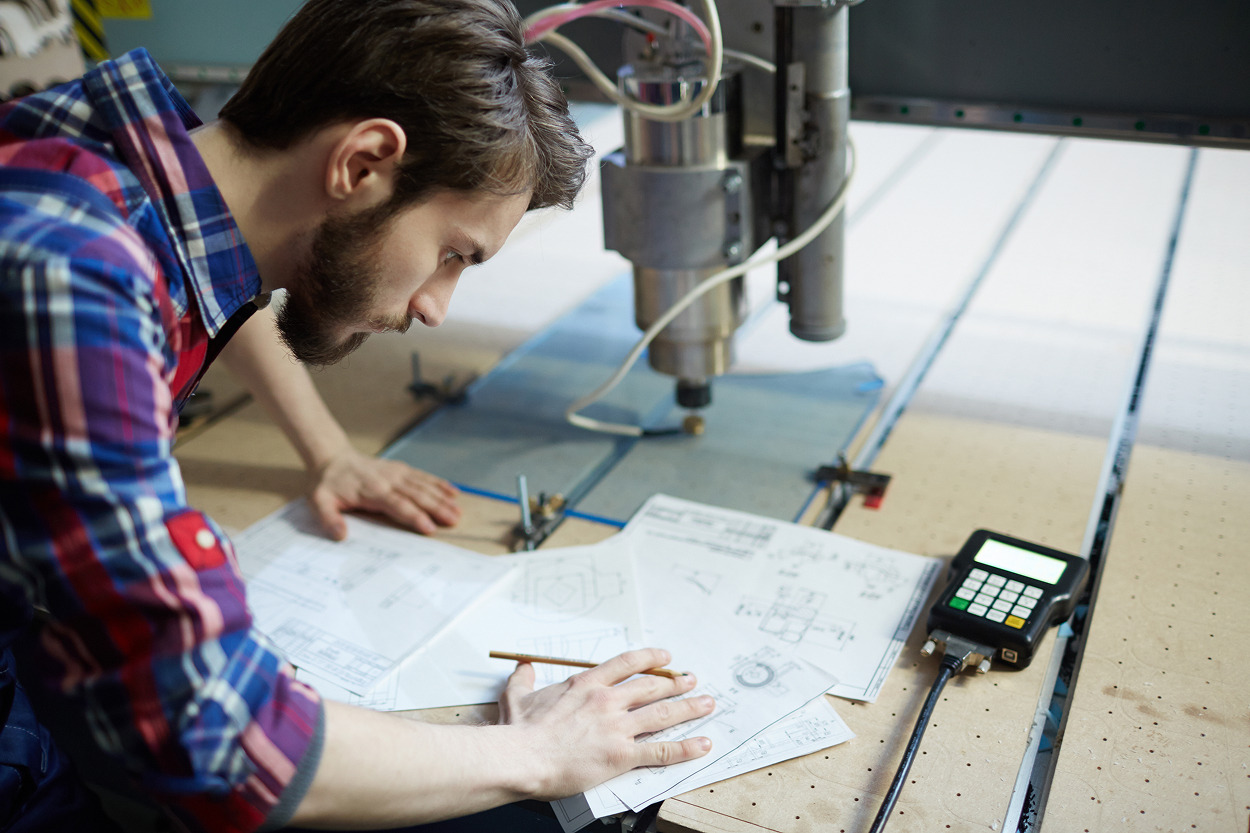
Design Tips for CNC Success
- Use generous internal radii for corner milling
- Avoid unnecessary deep pockets — they increase cycle time
- Align enclosure splits with natural component access points
- Integrate heat transfer features early — not as an afterthought
- Design for ease of assembly: thread inserts, captive screws, O-ring channels
A great milled housing isn’t just a box — it’s a mechanical interface with your product’s entire ecosystem.
Final Thoughts: When CNC Is the Right Choice
CNC-milled enclosures are not just for prototyping. In many industries, they’re the production-ready solution when reliability, customization, and speed matter most.
Promwad helps OEMs and startups design CNC-machined enclosures that balance cost, strength, aesthetics, and time-to-market.
Let’s design your next enclosure for real-world performance — and get it into users’ hands faster.
Our Case Studies