Modern Approaches in Industrial Design: Where Engineering Meets Experience
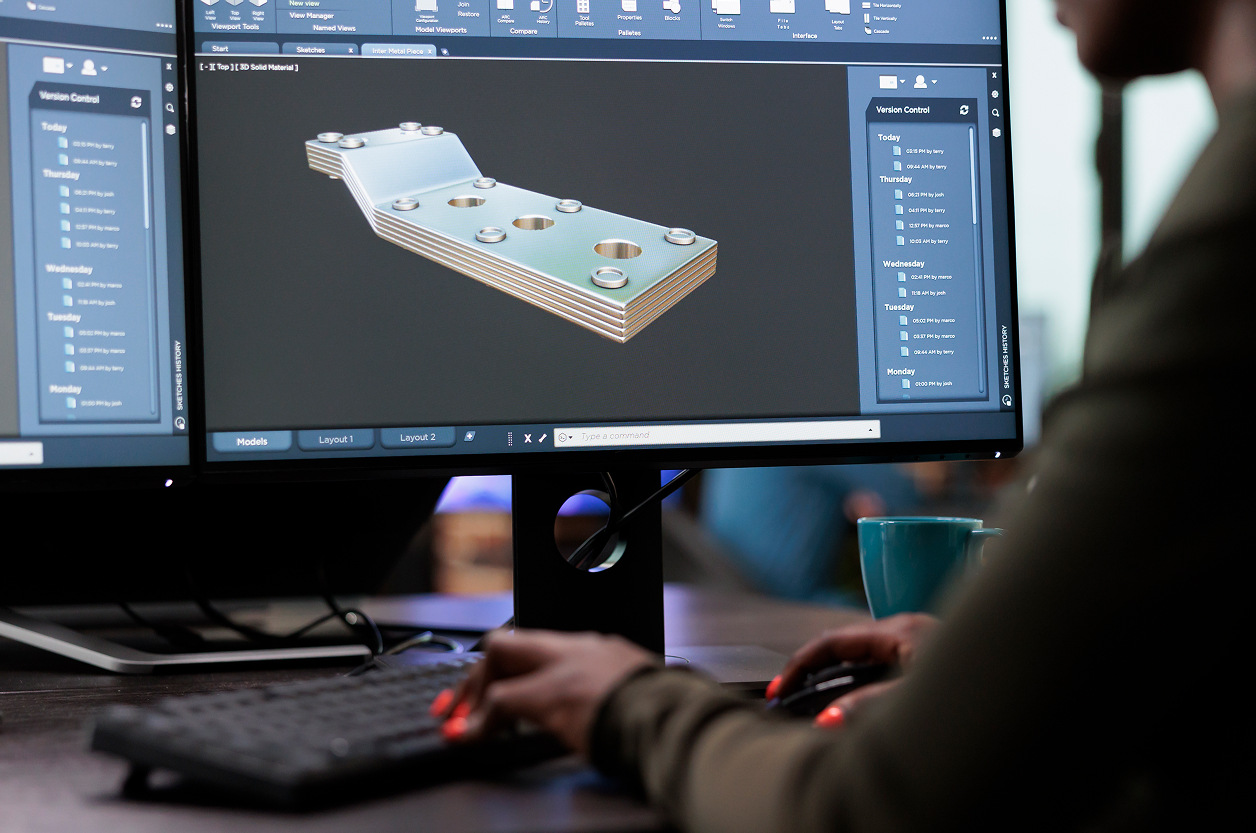
Why Industrial Design Matters More Than Ever
In a world of commoditized hardware, a product’s form, feel, and user experience can be the deciding factors in its success. Industrial design isn’t just about making things look good — it’s about aligning aesthetics with function, manufacturing feasibility, and brand identity.
In this article, we explore modern approaches to industrial design that blend creativity with engineering realities. Whether you’re building medical devices, IoT wearables, or industrial controls, these strategies help you stand out — and scale.
Key Shifts in Modern Industrial Design
1. From Style-First to Use-First
The focus has shifted from pure aesthetics to usability-driven design. Great products solve user problems before they make visual statements.
Examples:
- Touchpoints optimized for gloved or wet hands
- Enclosures shaped for easier mounting or replacement
- Displays angled for visibility in sunlight or tight spaces
2. Integrated Mechanical and Electronic Thinking
Designers work closely with hardware and software engineers to:
- Account for PCB constraints
- Integrate antennas and sensors seamlessly
- Enable manufacturability (DFM) from day one
This approach reduces surprises and late-stage design conflicts.
3. Sustainability and Circular Design
More companies now prioritize materials and design choices that:
- Enable disassembly and recycling
- Use fewer plastic blends or add biodegradable options
- Reduce part count and packaging waste
This is especially relevant for medical, consumer, and EU-regulated products.
Tools That Drive Modern Industrial Design
Tool/Platform | Application |
SolidWorks/Fusion 360 | 3D mechanical modeling and rendering |
Rhino + Grasshopper | Parametric exploration and organic forms |
KeyShot/Blender | Visual prototyping and presentation renderings |
Figma + Adobe XD | Screen and UI prototyping for device displays |
VR/AR simulation | Ergonomic studies and spatial validation |
Digital twins and simulation platforms are increasingly part of the process.
Prototyping in the Loop
Modern design cycles are iterative and parallel:
- 3D-printed mockups to test grip, fit, and scale
- CNC-cut shells to validate durability and finishes
- Foam/wood/foamcore models to explore proportions
Rather than perfecting CAD first, teams move fast from sketch to sample to get real-world feedback early.
Case-Based Collaboration: Designer + Engineer
True innovation happens when designers and engineers build solutions together. At Promwad, we:
- Align user needs and technical constraints from day one
- Host joint brainstorming and constraint mapping sessions
- Use shared CAD files and markup tools for direct edits
- Loop in industrial designers during PCB and antenna planning
This prevents last-minute compromises — and results in products that are both elegant and buildable.
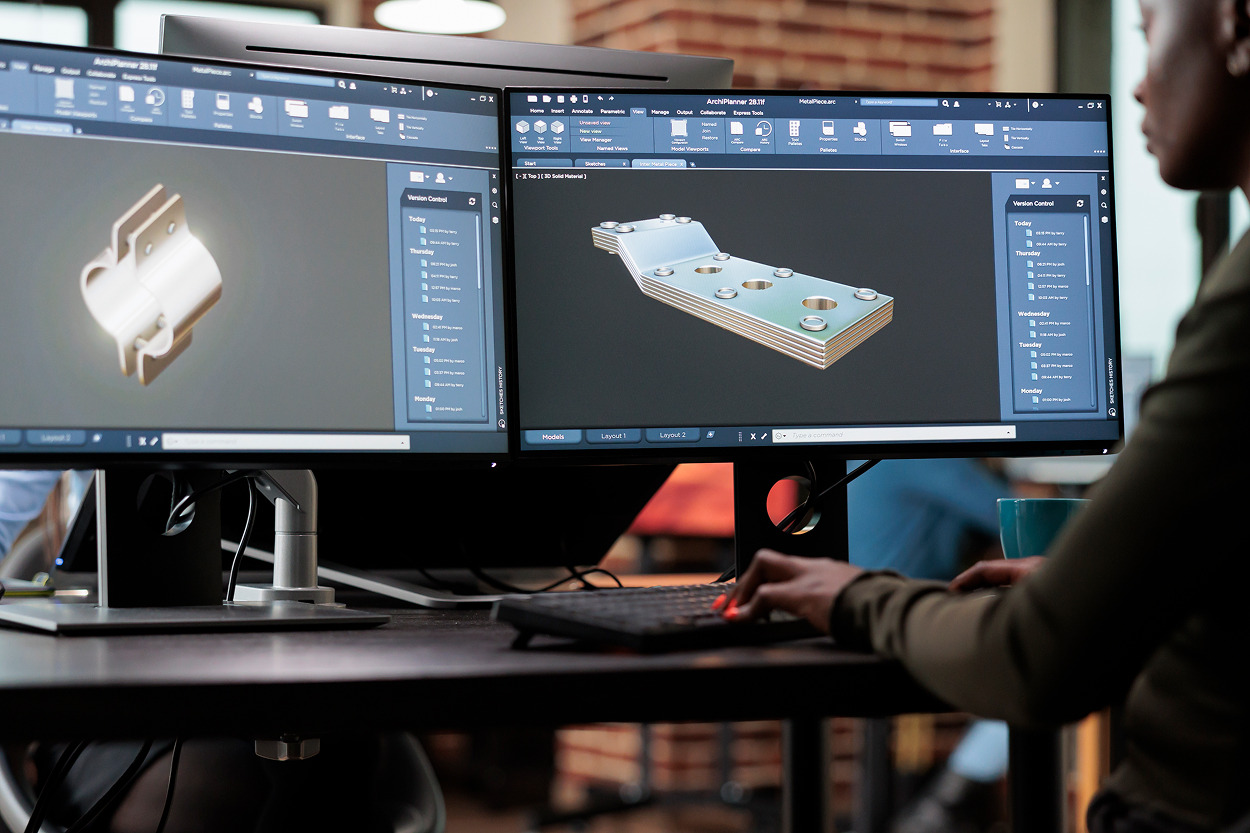
Trends to Watch in Industrial Design (2025 and Beyond)
Trend | Why It Matters |
Context-aware surfaces | Enclosures that respond to user conditions |
Bio-based composite materials | Reducing carbon footprint and waste |
Modular enclosures | Simplified repair and upgrade pathways |
Edge-integrated interfaces | Blending screens, sensors, and structure |
Transparent or open structures | Signaling trust, minimalism, and sustainability |
These are already being seen in wearables, smart appliances, and automotive interiors.
Final Thoughts
Modern industrial design is no longer a siloed discipline — it’s a strategic pillar of product success. Teams that integrate design early and deeply are more likely to build products that users love — and manufacturers can actually make.
At Promwad, we unite industrial design with embedded engineering to shape hardware that performs, delights, and scales.
Let’s create the next generation of purposeful, manufacturable devices — together.
Our Case Studies in Industrial Design