Power Electronics for Fuel Cell Systems: Boost Converters, Inverters, and Energy Management
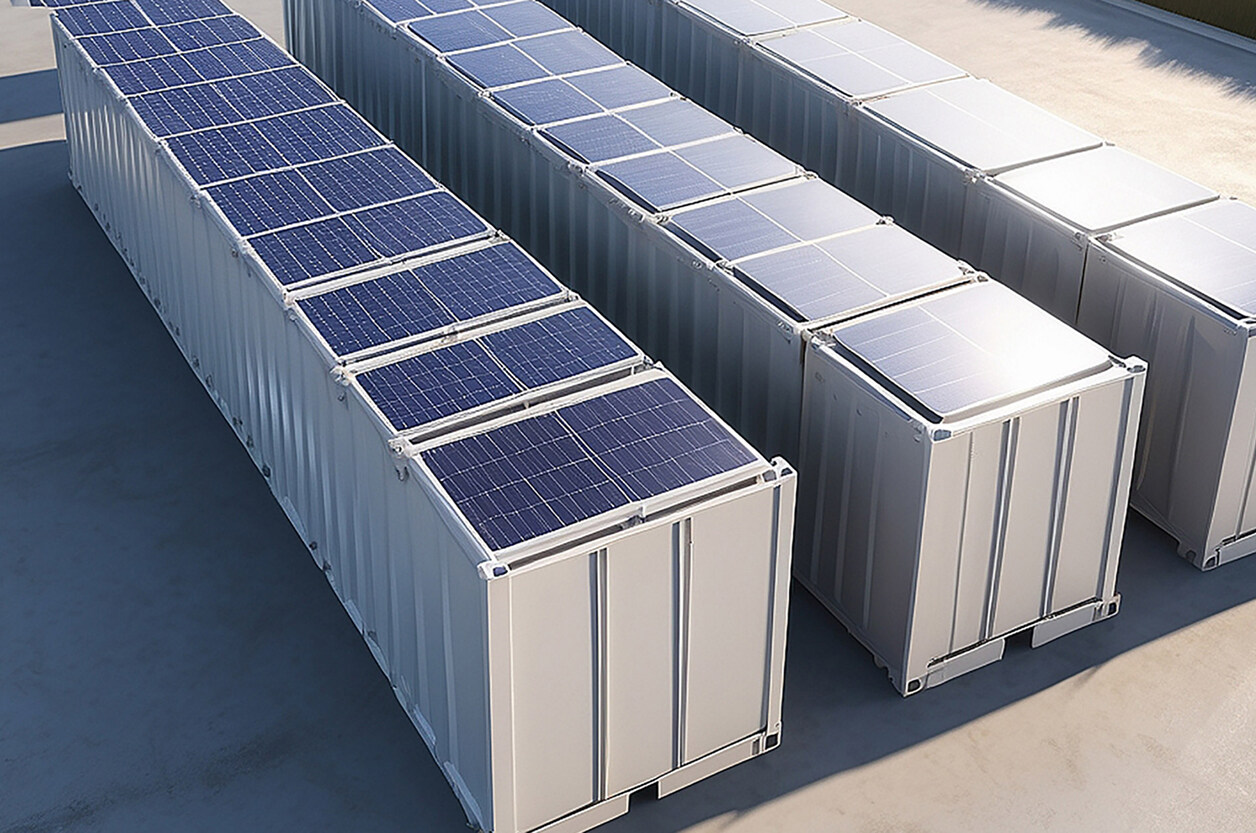
Fuel cells are increasingly used as primary or auxiliary power sources across industries — from heavy trucks and buses to stationary backup systems for data centers and factories. However, a fuel cell stack on its own delivers low, variable DC voltage that changes with load and aging.
This is why power electronics are at the heart of any fuel cell system. Boost converters, inverters, and sophisticated energy management modules transform unstable fuel cell output into stable, usable power. They also protect both the fuel cell stack and downstream loads from voltage fluctuations, transient currents, and operational faults.
This article explores the design of power electronics for fuel cell applications, highlighting typical topologies, control strategies, and the engineering challenges specific to hydrogen energy systems.
Why Fuel Cells Need Dedicated Power Electronics
Unlike batteries, which maintain fairly flat voltage curves over discharge, fuel cell voltage drops under load and varies with:
- Current draw
- Hydrogen purity
- Cell temperature
- Stack age
For example, a typical PEM stack might deliver:
Load Current | Output Voltage |
No Load | 48V |
Nominal | 36V |
High Load | 24V |
But industrial equipment often expects a regulated 48V DC bus or even AC power. Power electronics smooth these variations and step voltages up or down as needed.
Core Power Electronic Stages in Fuel Cell Systems
Boost Converters (DC-DC)
A boost converter steps up variable, lower DC voltages from the stack to a stable higher voltage:
- Keeps DC bus constant even as stack voltage drops under load.
- Limits ripple that could disturb sensitive loads.
- Often employs interleaved phases to handle high currents efficiently.
Design considerations include:
- Fast transient response to load changes.
- Protection circuits to prevent overcurrent if stack voltage dips too low.
- Soft start mechanisms to prevent inrush that stresses membranes.
Inverters (DC-AC)
For AC-powered equipment or grid feed-in, an inverter converts DC output to 50/60 Hz AC.
- Grid-tied inverters synchronize phase and frequency.
- Off-grid inverters must handle dynamic loads and may integrate with battery buffers.
- Modern inverter control often uses space vector PWM (SVPWM) for high efficiency and low harmonic distortion.
Bidirectional Converters for Hybrids
Many systems pair fuel cells with batteries or supercapacitors:
- Fuel cells supply steady base load.
- Batteries handle rapid load spikes and regenerative braking (in vehicles).
- Bidirectional DC-DC converters manage power flow between fuel cells, storage, and DC bus.
Real-Time Control: Algorithms and MCUs
MPPT-Like Load Tracking
While MPPT (Maximum Power Point Tracking) is famous in photovoltaics, fuel cell controllers use similar algorithms to maintain optimal load points that balance efficiency and stack health.
- Avoid deep voltage sags that accelerate membrane degradation.
- Adjust duty cycles on boost converters to keep stack in target voltage-current window.
Ripple Management
High-frequency ripple can age fuel cells. Controllers integrate current loops that keep ripple under specified percentages.
Safety Protections
- Overvoltage and undervoltage lockouts on buses.
- Active current limiting during load faults.
- Soft shutdowns if hydrogen supply fails.
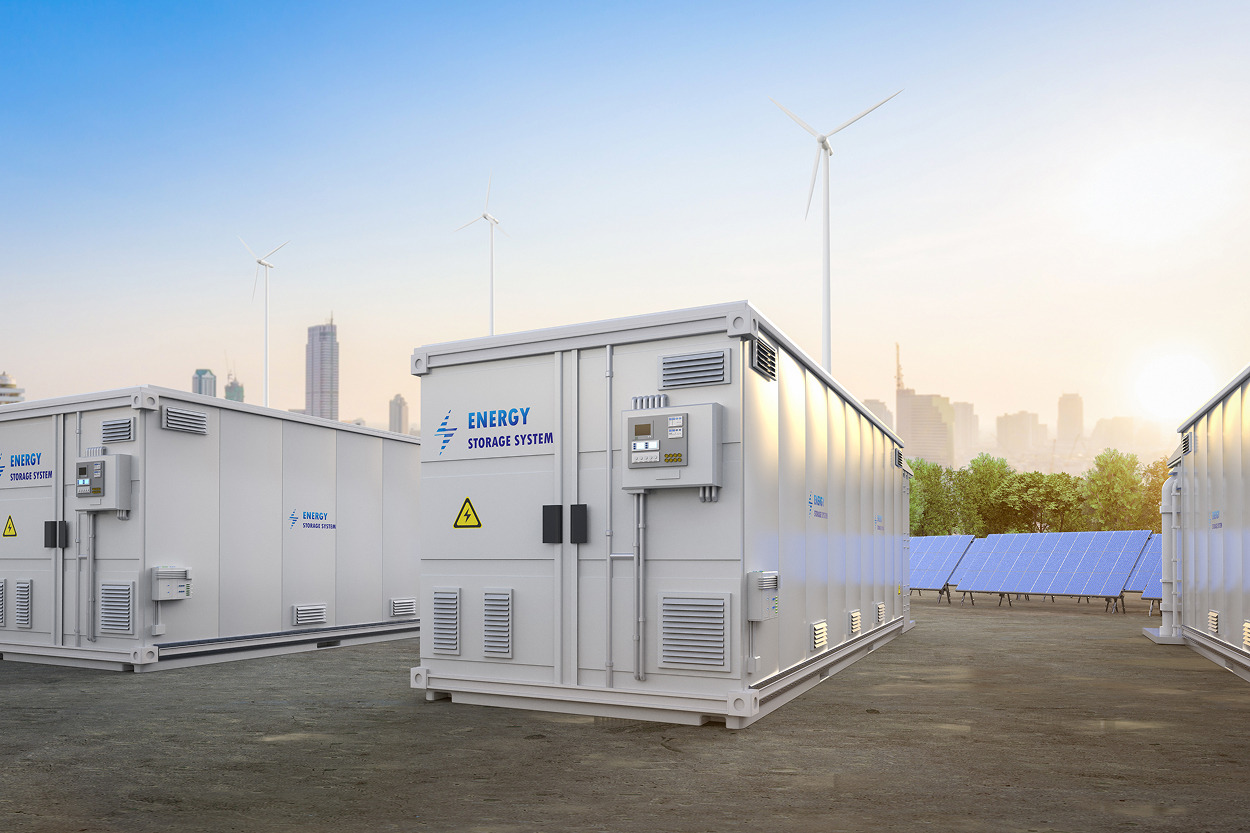
Long-Tail Technical Questions and Engineering Answers
Why not connect fuel cells directly to batteries or loads?
Because fuel cells have slow dynamic response. Without a DC-DC stage, load spikes can cause voltage collapse, damaging cells and dropping power to critical systems.
Can standard PV inverters work with fuel cells?
Generally no. Fuel cells have different IV characteristics and faster droop under load, needing converters tuned for their response curves.
How is ripple controlled in fuel cell power stages?
Use high-frequency interleaved converters and LC filters. Typical targets are <5% current ripple to extend stack life.
What microcontrollers are used in these systems?
32-bit MCUs with fast ADCs and multiple PWM channels (e.g., STM32 F3/F4, TI C2000) are common. Safety co-processors monitor watchdogs and emergency shutdown lines.
Is galvanic isolation needed?
Yes, especially in systems interfacing with high-voltage buses (>100V) or feeding grids. Isolated gate drivers and isolated feedback paths ensure safety and EMC compliance.
Example: Power Electronics in a Hydrogen Bus
A fuel cell electric bus might use:
- PEM stack: Output varies from 30-70V depending on load.
- Boost converter: Raises to stable 400V DC bus.
- Bidirectional converter: Manages charge/discharge to 600V Li-ion battery pack.
- Inverter: Feeds three-phase AC to traction motors.
- Auxiliary converters: 24V rails for HVAC and controls.
Embedded controllers coordinate all stages, ensuring smooth transitions between regenerative braking, fuel cell supply, and battery assist.
Future Trends in Fuel Cell Power Electronics
- SiC and GaN switches: Higher frequency switching reduces passive size, improving power density and lowering losses.
- Integrated digital power: MCUs directly controlling gate drivers allow sophisticated adaptive algorithms that adjust switching for load profiles.
- AI health models: Machine learning at the edge predicts when ripple or thermal stress risks shortening stack lifespan.
Engineering Best Practices for Fuel Cell Power Electronics
Model Before You Build
Simulate electrical, thermal, and lifetime interactions. Tools like PLECS or Matlab Simscape catch resonance and filter issues early.
Separate Safety and Control
Use dual MCUs or safety islands to independently watch for overcurrent, hydrogen flow errors, or inverter faults.
Plan for OTA Updates
Field update capability helps tune control laws or ripple profiles as systems age or as new fuel sources are introduced.
Conclusion: Power Electronics Are the Heart of Fuel Cell Systems
Efficient, reliable power electronics turn fuel cells from lab curiosities into robust powerplants for vehicles, factories, and off-grid sites. They stabilize voltages, protect delicate membranes from electrical abuse, and coordinate energy flows with batteries or supercapacitors.
At Promwad, we develop embedded systems and power electronics for hydrogen applications — from boost and inverter control to robust safety firmware and secure OTA. If you’re designing next-generation fuel cell platforms, our engineering teams can help create the foundation for efficient, long-life systems.
Our Case Studies