How We Design Air Cooling Systems for Electronics: Engineering Methods and Real-World Tradeoffs
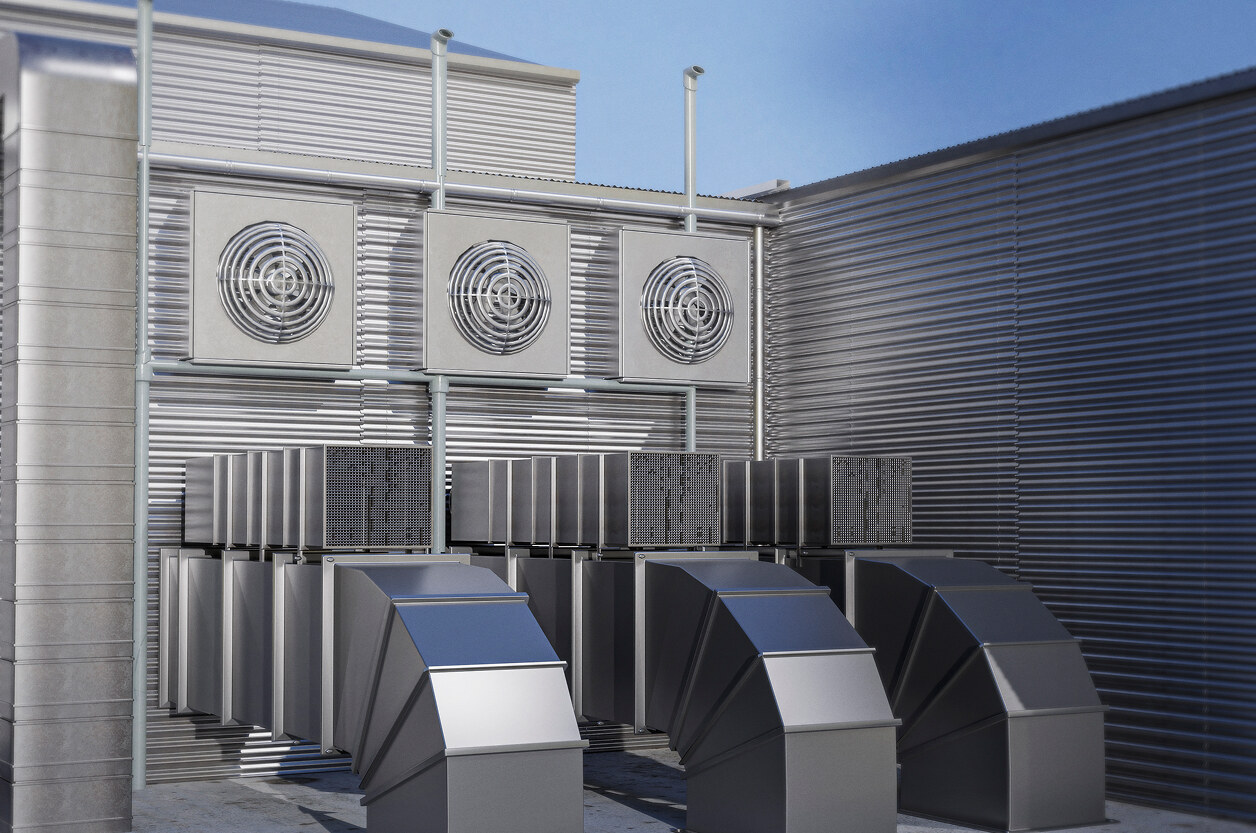
Why Air Cooling Remains Essential in Embedded Hardware Design
In embedded and industrial electronics, heat is a silent killer. From SoCs and FPGAs to power modules and RF components, rising temperatures degrade performance, shorten lifespan, and cause thermal shutdowns.
While liquid cooling and heat pipes exist, most applications — especially in telecom, automotive, and IoT — still rely on well-designed air cooling systems to maintain safe operating conditions. The key is making it efficient, reliable, and manufacturable.
In this article, we walk through how Promwad engineers design air-cooled systems that meet thermal and mechanical demands in real-world products.
Step 1: Understanding the Thermal Load
Thermal design starts with clear answers to:
- What components dissipate the most power?
- What is the max allowable junction temperature (Tj)?
- What ambient temperature range will the device see?
We gather power budgets, environmental specs (e.g., -40°C to +85°C), and form factor limitations early — then begin mapping heat paths.
Step 2: Passive Cooling Strategy (Before Adding Fans)
Element | Function | Considerations |
Heat sinks | Absorb and spread component heat | Material (Al vs Cu), fin geometry |
PCB copper planes | Spread heat across board | Layer stackup, thermal vias |
Thermal pads | Improve interface between component and sink | Thickness, compliance, conductivity |
Enclosure as heatsink | Use housing to dissipate heat to environment | Material choice, surface contact |
Passive design is preferred for reliability and noise. We try to delay fan use as long as possible.
Step 3: Simulating Natural and Forced Convection
Promwad engineers use CFD tools (e.g., Ansys Icepak, SolidWorks Flow) to simulate airflow:
- Identify hot spots and recirculation zones
- Optimize vent placement and internal air channels
- Validate heat sink effectiveness and pad interface
CFD lets us test virtual enclosures before building physical prototypes, saving weeks of iteration.
Step 4: When Active Cooling Becomes Necessary
In some designs, passive methods can’t keep temperatures within safe margins. That’s when we:
- Select high-MTBF axial or centrifugal fans
- Simulate fan curves with expected back pressure
- Add dust filters or air grilles with minimized flow restriction
Fan placement is optimized to avoid dead zones — especially in sealed telecom and industrial enclosures.
Design Tradeoffs in Air-Cooled Systems
Factor | Tradeoff Example |
Performance vs Size | Bigger heat sinks = better cooling, but bulkier |
Noise vs Flow Rate | Faster fans cool more, but add acoustic noise |
Reliability vs Cost | Passive systems last longer, but may cost more |
Aesthetics vs Vents | Clean look vs thermal grille requirements |
Balancing these factors requires coordination between mechanical, thermal, and industrial design teams.
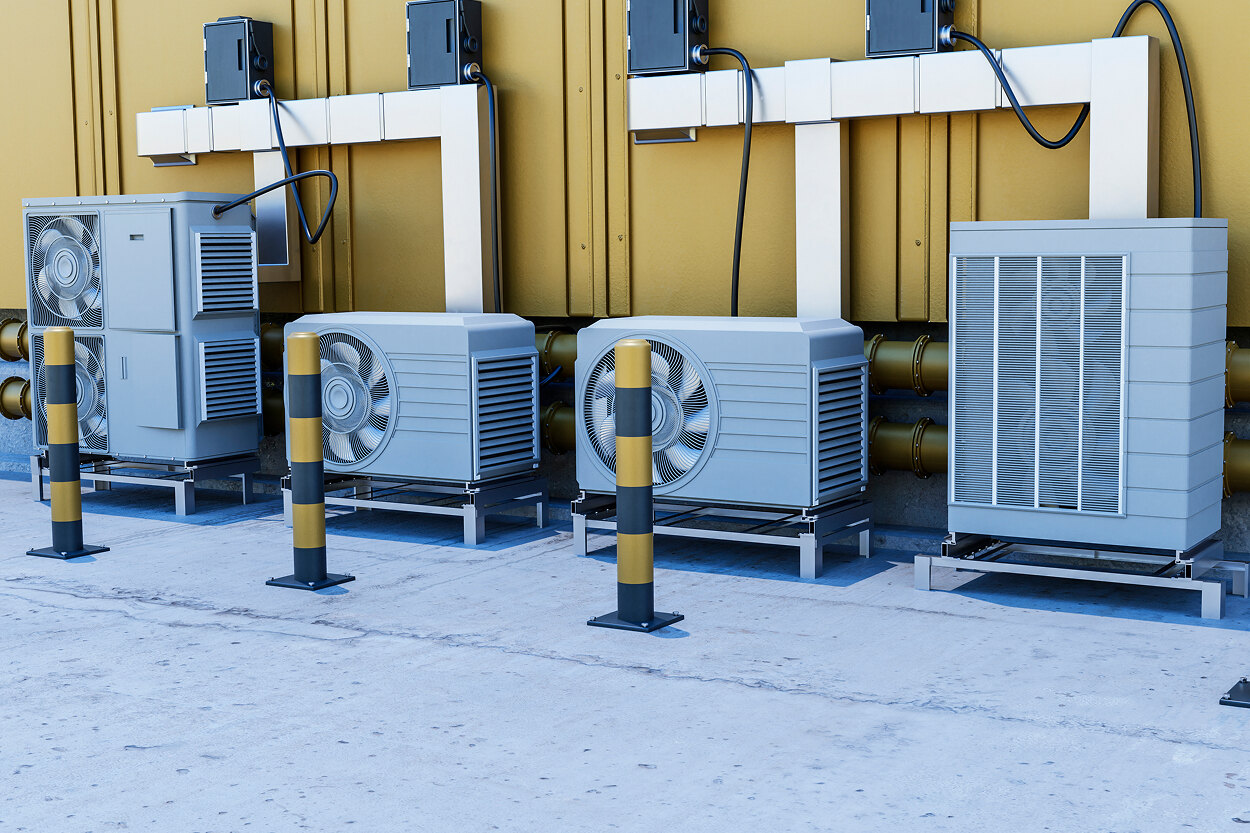
Real-World Case: Fanless Industrial Router
- Target: Operation at +70°C ambient
- Challenge: FPGA and switch chip with 20+ W combined dissipation
- Approach: Used aluminum enclosure as heat sink, thermal pads to lid
- Result: Junction temps held below 95°C under stress test without fan
The product passed thermal chamber cycling and was qualified for rail deployment.
Tips for Better Air Cooling Design
- Always check component derating curves at high temps
- Account for worst-case ambient + solar load if outdoors
- Design thermal interface stack-up carefully (pad + gap + sink)
- Include airflow simulation early in mechanical design
- Use thermal camera to validate real prototypes
Even simple air-cooled systems benefit from detailed planning.
Final Thoughts
Thermal failures can be hard to diagnose and expensive to fix. With the right thermal strategy, electronics can stay cool, reliable, and certifiable — without overengineering.
At Promwad, we specialize in air-cooled thermal design for compact, high-performance embedded systems — including simulation, integration, and mechanical co-design.
Let’s keep your next device cool — and your project on schedule.
Our Case Studies