Top 5 Tech Trends Shaping Industrial Automation in the Next 5 Years
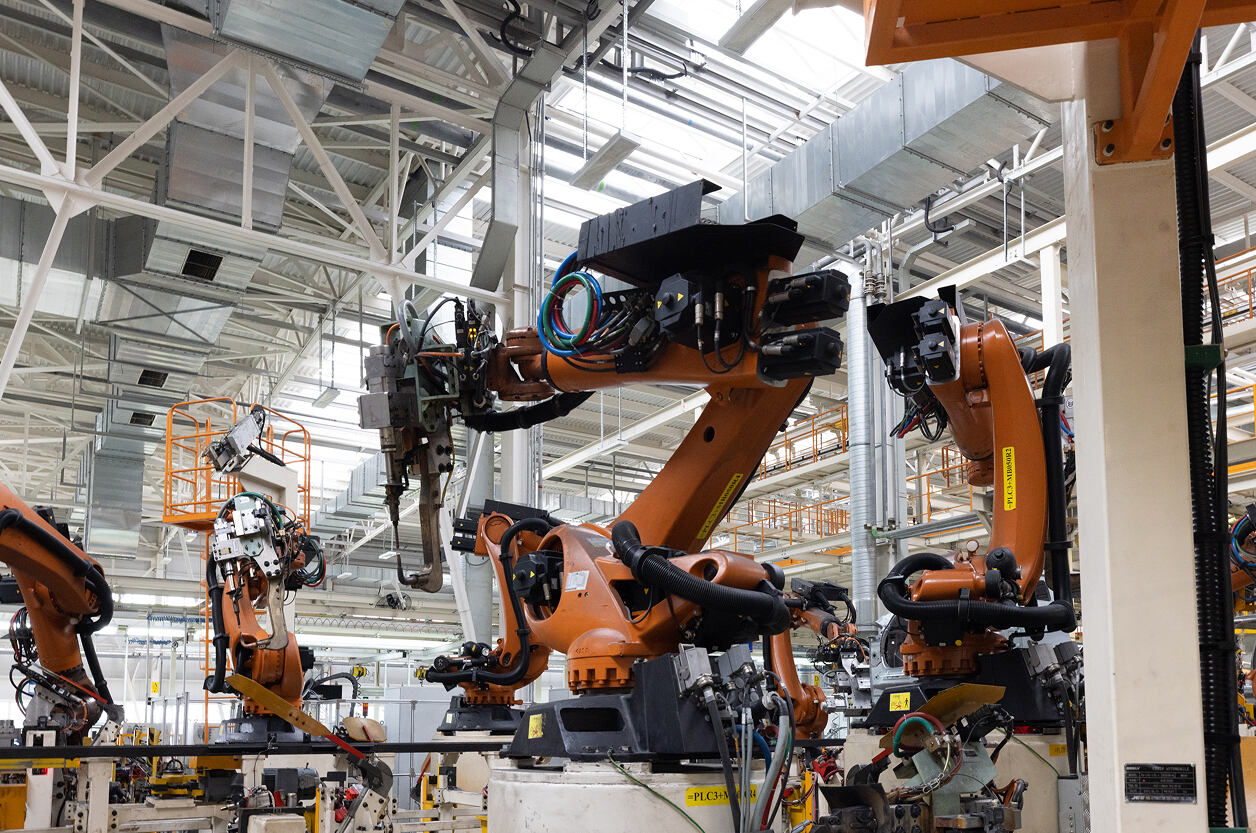
Introduction: Why Industrial Automation Is Entering Its Most Disruptive Phase Yet
The industrial sector is undergoing its most profound transformation since the introduction of PLCs and SCADA in the 1970s. Fueled by rapid advancements in connectivity, artificial intelligence, and digital engineering, industrial automation is evolving from programmed control to predictive, adaptive, and autonomous systems.
In the next five years (2025–2030), five core technology trends will drive this transformation — reshaping how factories, warehouses, utilities, and processing plants operate, scale, and adapt.
This article explores these trends and what they mean for OEMs, system integrators, and industrial product developers.
1. Edge AI and Machine Learning for Predictive Control
What’s happening: AI has moved from the cloud to the edge — enabling embedded devices to process sensor data locally and respond in real time.
Why it matters:
- Reduces latency for time-critical decisions
- Enables predictive maintenance based on behavioral models
- Increases resilience by reducing reliance on cloud infrastructure
Real-world use cases:
- Anomaly detection in rotating equipment using vibration + ML models
- Predictive quality control on production lines with computer vision
- Adaptive process optimization in chemical and food manufacturing
Technology enablers: Edge AI chips (NXP i.MX 9, Renesas RZ/V2L, Lattice Avant), frameworks like Edge Impulse, TensorFlow Lite for Microcontrollers, RTOS integration with model inference pipelines.
2025–2030 outlook: Expect factory devices to become AI-native, with models retrained at the edge using federated learning or MLOps practices.
2. Interoperability Through Unified Industrial Protocols
The problem: Legacy systems rely on proprietary fieldbuses, vendor-specific integrations, and siloed architectures that limit scalability.
The trend: Open, vendor-neutral communication protocols are gaining ground:
- OPC UA over TSN
- MQTT + Sparkplug B for lightweight messaging
- EtherCAT + Ethernet-APL for real-time deterministic Ethernet
Benefits:
- Plug-and-play device integration
- Cross-vendor communication in brownfield and greenfield sites
- Easier migration to Industry 4.0 and digital twin environments
What to watch: Adoption of IEC 61499 function blocks as a standard for event-driven automation logic, interoperability with cloud APIs for remote control and monitoring.
Promwad supports embedded protocol stacks and hardware integration for modernizing industrial interfaces.
3. Digital Twins and Model-Based Engineering
The concept: A digital twin is a real-time, virtual representation of a physical system — used to simulate, monitor, and optimize operations.
Why it’s growing:
- Enables remote commissioning and system tuning
- Supports predictive diagnostics and process optimization
- Simplifies training, testing, and certification
Technologies involved: 3D CAD + simulation tools (ANSYS Twin Builder, Siemens NX), IoT platforms that sync data in real time, open standards like FMI (Functional Mock-up Interface).
Trends to watch: Integration of PLC code and physics-based models in the same runtime, digital twin “ecosystems” that span OEMs, integrators, and end users, coupling twins with AI models for next-gen control systems.
Implementation challenges: Data quality and sensor integration, real-time synchronization, model maintenance as systems evolve.
4. Collaborative Robotics (Cobots) and Autonomous Systems
What’s changing: While traditional industrial robots are locked in cages, collaborative robots (cobots) and AMRs (autonomous mobile robots) are entering shared spaces with human workers.
Key advances:
- Safe path planning with 3D sensors and AI
- Flexible reprogramming for changing tasks
- On-the-fly integration with MES and WMS systems
Applications: Bin picking and assembly on hybrid lines, autonomous material transport in smart warehouses, inspection and maintenance tasks in hazardous areas.
Tech drivers: ROS 2, MoveIt, and real-time control frameworks; EtherCAT-based motion control; AI-enhanced vision and grasping libraries.
Expect to see cobots not just assisting but learning and adapting through reinforcement learning and shared data sets.
5. Cybersecurity and Regulatory Compliance in Industrial Environments
Why it’s urgent: Industrial systems are increasingly connected — and that makes them vulnerable. Attacks on water utilities, pipelines, and factories have proven the risk.
Key regulatory frameworks: IEC 62443 (Industrial Network Security), NIST 800-82, ISO/SAE 21434 for automotive industrial applications, Cyber Resilience Act (EU, in force from 2025+).
Emerging strategies:
- Security-by-design at the silicon and firmware level
- Zero-trust architectures with identity-based access
- Secure boot, OTA updates, and encrypted logging
What's ahead: Cybersecurity will become a product feature, not an IT afterthought — embedded in PLCs, drives, HMIs, and sensor nodes.
6. Edge-to-Cloud Integration for Closed-Loop Industrial Intelligence
As edge devices become smarter, the flow of information between the edge and the cloud must become more seamless, secure, and real-time. This trend represents the convergence of operational technology (OT) and information technology (IT).
Key developments:
- Data preprocessing at the edge to reduce cloud payloads and costs
- Cloud-native microservices for SCADA/PLC integration
- Real-time feedback loops between factory sensors and cloud-based AI engines
Use cases: Cloud-to-edge synchronization of production schedules and quality control parameters, dynamic model deployment from cloud AI platforms to on-device accelerators, visualization dashboards powered by Azure IoT, AWS Greengrass, or private Kubernetes clusters.
Benefits: Agile production systems, unified data lakes, reduced latency for mission-critical control.
Barriers to adoption: Latency, cybersecurity, and data model fragmentation.
Industrial companies that adopt cloud-edge co-design models will gain visibility, efficiency, and adaptability — laying the foundation for autonomous operations.
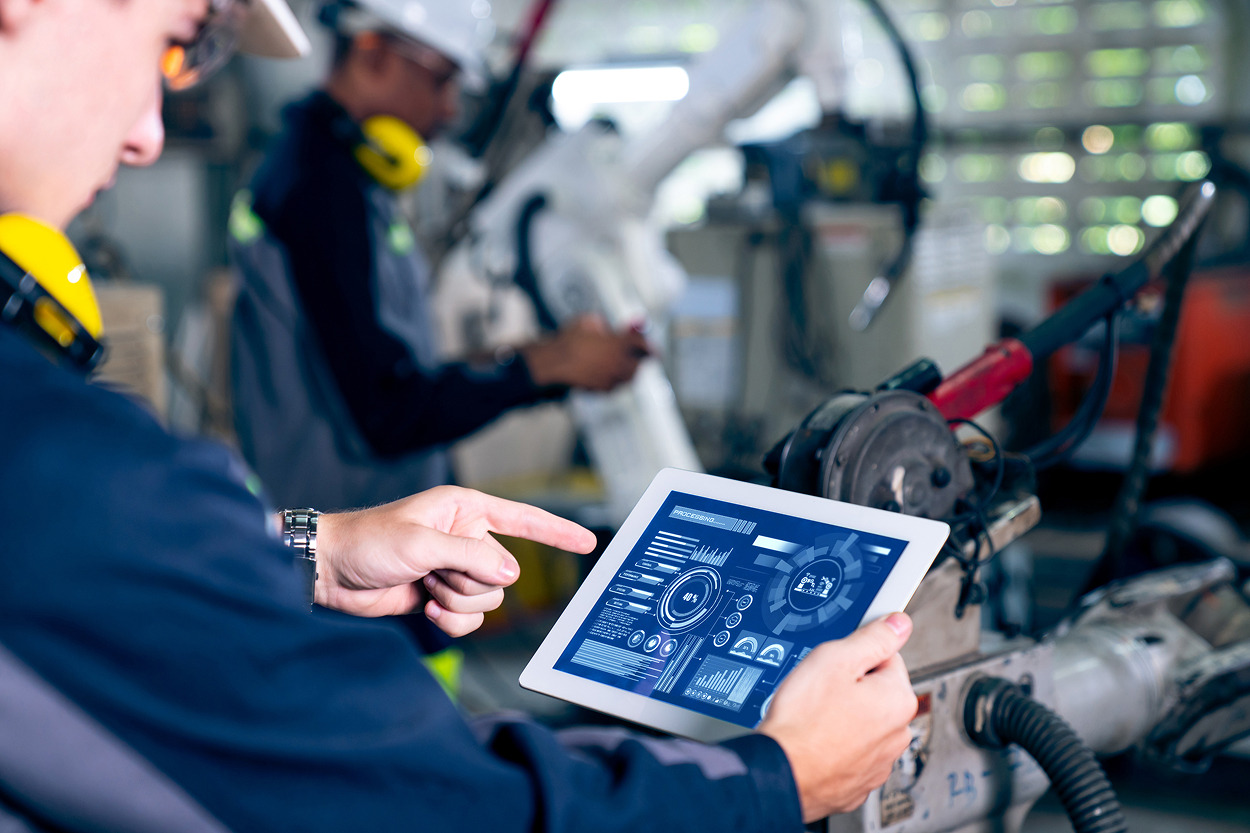
Final Thoughts: From Automation to Autonomy
The next five years will redefine industrial automation — blending real-time control with AI, connectivity with cybersecurity, and physical systems with digital twins.
OEMs, system designers, and tech vendors who embrace these trends early will build more adaptable, scalable, and future-proof platforms.
Promwad engineers next-gen embedded and edge systems for industrial automation — helping clients adopt AI, real-time networking, and secure-by-design hardware/software.
Let’s shape your future of automation — together.
Our Case Studies in Industrial Automation