Fish finder: industrial & mechanical design
Client
The customer is a European researcher and manufacturer engaged in the development of test & measurement equipment: portable echo sounders and other related devices for amateur and professional fishing.
Challenge
Industrial design and construction of the new generation echo sounders. Designers should take into account the customer's corporate identity and adapt the enclosure to the harsh conditions of operation, including low temperatures, down to -30℃.
Specified requirements:
- To develop a modern design and vandal-resistant construction with protection against water and dust according to IP67 standard, with resistance to impact and falling from a height of 1.5 m on a hard surface.
- To Install the connector for the sensor in the construction.
- To ensure easy assembly and maintenance of the device.
- Provide a place to install the battery inside the case.
Solution
We have developed the device enclosure and a hermetic vandal-resistant construction. We provided a high degree of protection against dust and moisture according to IP67 standard. The robust design and rubberized enclosure withstands falling from a height of 1.5 m on a hard surface.
We also implemented a hermetically sealed sensor connector in the housing and made it easy to assemble and maintain.
Each step of our designers' and engineers' work was coordinated with the customer to take into account the limitations of the device hardware platform.
Promwad's technologists offered optimal materials and production technologies. The design solution was tested on prototypes: to test the assembly, a sample was printed on a 3D printer using the FDM-extension technology, and for the final check the prototype body was made by milling.
1. Concept
We have studied the client's products as well as successful analogues and prototypes in the world market.
Based on the results of this study, we proposed to design an enclosure, which will be manufactured by the method of two-component casting with mortar glass. Such decision will allow to refuse glass and buttons insertion, as a result the enclosure will be better protected from water and dust.
To simplify the assembly of the enclosure we decided to design the device as two halves connected by four screws. One of the halves will be equipped with a "spike" for pressure on the rubberized mating part. This will ensure the tightness of the device.
2. Industrial design
During the sketching process, our designers have worked out several basic directions for further development of the new product's enclosure, taking into account the customer's requirements, restrictions on size, display, number of buttons and external connector for the sensor.
After selecting the original design, we have worked through the implementation options for the buttons. In doing so, we took into account the requirements of the device business logic and user-friendliness.
The final step in industrial design development is the preparation and approval of renderings reflecting the appearance of the finished product.
3. Enclosure design
4. Prototyping
To verify the overall results of our work and to test the assembly of the echo sounder, we produced prototypes using the FDM-extraction method. This fast and affordable 3D printing technology allows us to obtain a sample close to the factory version of the device. Quality of a surface thus remains average, but for our purposes at the first stage of prototyping it was not important. We assembled the device together with all components - connectors, display and battery:
Based on the results of the prototype study, we have corrected the design and construction of the enclosure. We changed the location of the connector to improve hermeticity and ease of assembly.
After modifying the design and construction of the enclosure, we produced a sample that was as close as possible to the serial product.
5. Manufacturing launch
While developing the tooling, we prepared and agreed with the customer the necessary molds, choosing the optimal injection points, taking into account the simulation of parts for warping.
The figure below shows the injection point of thermoplastic polymer and the results of computer simulation of physical processes:
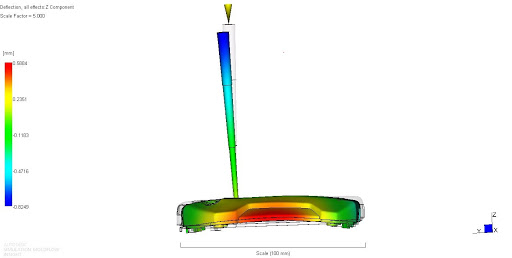
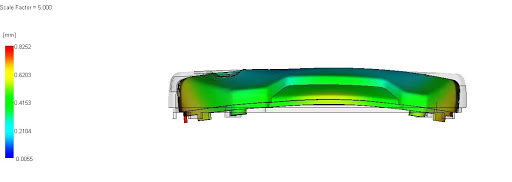
- For the upper part, the "glass" is poured separately and silkscreened. This glass is used as a mortar piece, which is poured over the plastic.
- The resulting plastic part with glass is poured in rubber (TPU), which also forms the elastic buttons, serves as a protective bumper and is a "gasket" to ensure tightness of the enclosure when assembled with the bottom part, which is produced in the same way, but without mortgaging parts.
Business Value
We helped the customer to launch a new enclosure, which became the basis for a series of products.
At the beginning of 2020, we manufactured and delivered more than 60,000 enclosures to our customer.
As part of our previous project, we also developed a sealed enclosure for wireless Wi-Fi beacons - they are supplied as standalone products and in pairs with receiver units. The beacons also work together with smartphones and display measurement data in a mobile application.
Thanks to our contribution, the customer remains one of the market leaders of fish finders, withstanding competition not only on the local but also on the world market. The company is the outfit sponsor of the winners of the world championships in fishing.