Integrating EtherCAT, CANopen, and CoE in Industrial Automation Projects
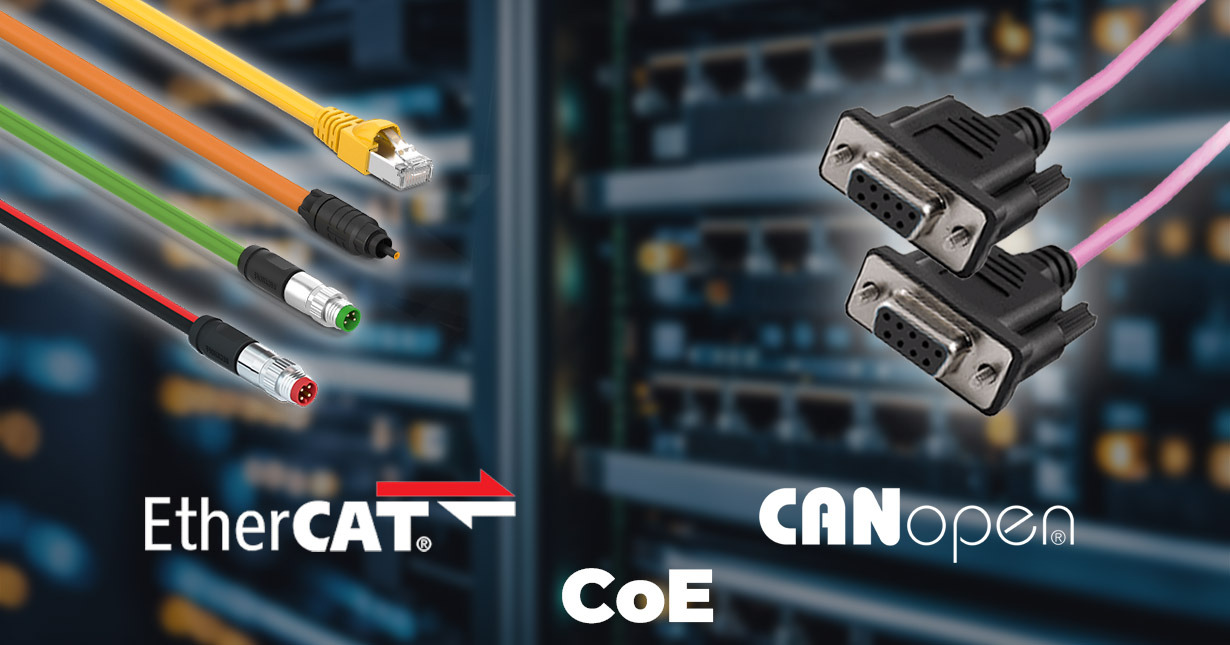
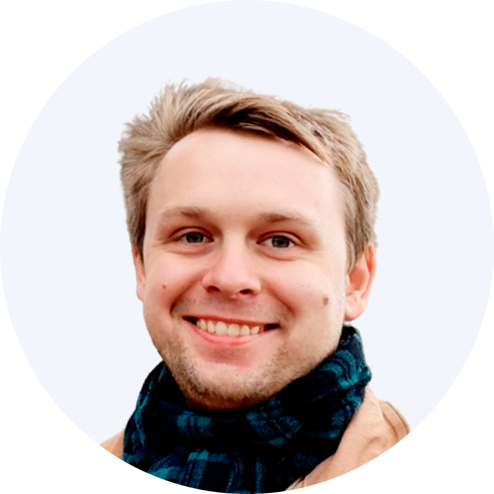
Choosing the right communication protocol is critical to the success of industrial automation projects. The selection process can be challenging with various protocols available, each with unique benefits, costs and implementation issues. EtherCAT and CANopen each offer valuable features tailored to the specific requirements of industrial applications.
We specialise in EtherCAT (CoE and other mutexes) and CANopen to drive industrial automation projects. We provide schematic design, PCB layout, and firmware development services for EtherCAT-based industrial automation solutions. Our team has the experience and expertise to bring your project to life, whether you need high-speed real-time systems, CANopen devices, or CoE network efficiency.
Table of contents
How to choose the right protocol?
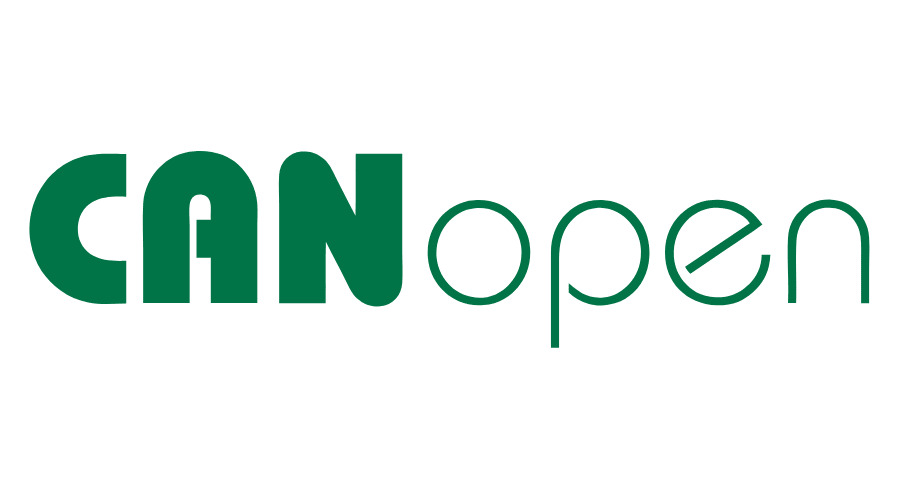
CANopen
CANopen (controller area network open), developed in the 1990s by the CAN in Automation (CiA) group, originates from the CAN protocol. Initially created for automotive applications, CANopen has spread to industrial applications.
CANopen is built on top of the CAN protocol, providing a higher-level protocol that manages communication, configuration and data exchange between devices.
At Promwad, we specialise in customising solutions based on CANopen to meet the needs of your industrial automation projects. Our expertise extends across various CANopen application profiles, including the CiA 402 series for drive and motion control, CiA 404 for measuring devices and closed-loop controllers, CiA 407 for train vehicle control systems and many more.
The diagram of a CANopen device state machine. Source: codesys.com
CANopen is renowned for its flexibility and cost-effectiveness. It supports many device profiles and is efficient, especially in environments requiring deterministic communication, but high data rates are unnecessary.
This protocol is used in industrial automation, especially in smaller systems that do not require the high-speed capabilities of EtherCAT. It is also indispensable in automotive, medical devices, building automation and small industrial equipment.
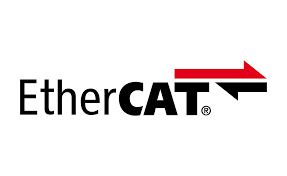
EtherCAT
EtherCAT (Ethernet for control automation technology) was introduced by Beckhoff Automation in 2003 as a high-performance fieldbus-based Ethernet system. Developed to fulfil the real-time requirements of industrial automation, EtherCAT quickly gained popularity due to its exceptional speed and efficiency and has become one of the most widely used communication protocols in the industrial automation sector.
EtherCAT is the most real-time network currently used in industrial automation, offering the lowest possible margin of error. By integrating an EtherCAT PLC, manufacturers can achieve real-time control and synchronisation across all connected devices.
EtherCAT dataflow. Source: ethercat.org
Our engineering team creates custom PLC solutions based on EtherCAT for industrial automation projects. Promwad is a member of the EtherCAT group, and we use this standard in robotics, motion control, and packaging systems, where its ability to process large amounts of data with minimal latency is crucial.
We use different hardware platforms to support industrial network solutions, especially EtherCAT-based systems, including Texas Instruments (AM335x, AM437x, AM57x, AMIC110, AMIC120, AM654x, AM64x) for robust processing and real-time control, and Infineon (XMC4300, XMC4800) for high-performance applications.
Our stack also features Microchip (LAN9254, LAN9253, LAN9252) and ASIX Electronics (AX58400, AX58200) for compact, flexible network interfaces, alongside Beckhoff's ET1100 for seamless communication.
EtherCAT and Its Protocols: FOE, EOE, SOE
EtherCAT's versatility is further enhanced by its support for various communication protocols, including:
- FOE (File Access over EtherCAT) allows for file transfer between devices on the EtherCAT network, makes it easier to manage firmware updates and configuration files.
- With EOE (Ethernet over EtherCAT), standard Ethernet frames can be transmitted over the EtherCAT network, for integration of existing Ethernet devices.
- SOE (Servo over EtherCAT) is specifically designed for servo drive applications, it offers precise control and synchronisation of servo motors, which is critical in high-performance automation systems.
These protocols collectively expand EtherCAT's capabilities and allows for a more integrated and flexible automation solution.
Applications of EtherCAT
EtherCAT’s architecture and protocol support make it the preferred choice for many applications:
- Servo Drives & Motor Control
The precision and speed of EtherCAT make it ideal for controlling servo motors in applications such as CNC machines and robotic arms.
- PLC/DAQ Systems
Integration with PLCs and data acquisition systems allows for real-time monitoring and control for high operational efficiency.
- Robotics
EtherCAT’s low latency and high determinism facilitate the development of robotic systems that require precise motion control and coordination.
- CNC Machinery
The protocol’s ability to handle multiple axes of movement efficiently makes it a staple in CNC applications for intricate and precise machining processes.
CoE
CoE, or CANopen over EtherCAT, is a powerful combination that takes the strengths of both CANopen and EtherCAT. By running CANopen protocols over EtherCAT, users can benefit from the real-time performance of EtherCAT while retaining the simplicity and familiarity of CANopen. This integration is important for applications where existing CANopen devices must be integrated into a high-speed EtherCAT network.
Using CoE enables simple communication between CANopen and EtherCAT devices, creating a unified and efficient network. Devices can interoperate without requiring extensive modifications or adaptations, reducing implementation time and costs. Integrating EtherCAT with CANopen increases network performance, especially in complex automation systems.
CoE is typically used in environments where legacy CANopen and newer EtherCAT devices coexist. For example, in large manufacturing plants where different parts of the production line may use different protocols, CoE enables these parts to communicate effectively.
How to choose the right protocol?
Feature | EtherCAT | CANopen |
Communication type | Ethernet-based, master-slave architecture | CAN (controller area network), multi-master |
Data transfer speed | High speed (up to 100 μs cycle times) | Moderate speed (up to 1 Mbps) |
Real-time capability | Excellent real-time performance | Good real-time capabilities |
Scalability | Highly scalable, supports hundreds of devices | Limited to fewer devices due to bandwidth |
Protocol complexity | Relatively complex, requires specialised knowledge | Simplier and easier to implement |
Network topology | Flexible (line, tree, star) | Limited (typically linear) |
Synchronisation | Precise synchronisation for multi-axis control | Good synchronisation capabilities |
Application focus | Robotics, CNC, motion control | Industrial automation, embedded systems |
Cost | Cost-effective with standard Ethernet hardware | Generally lower cost of implementation |
Diagnostics | Advanced error handling and diagnostics | Basic diagnostics |
Device support | Extensive support for various manufacturers | Supported by many embedded and automation devices |
Comparison of EtherCAT and CANopen key characteristics
These are the points to be focused on and taken into account when selecting a protocol:
- Application requirements
When selecting a communication protocol for industrial automation, the first step is to define the application's specific requirements: real-time data processing, network size, and communication speed.
If the application requires real-time control and precise synchronisation, such as in robotics or motion control, EtherCAT is usually the best choice. While reliable, CANopen is better suited for applications with less stringent real-time requirements.
- Network size
The size of the network and the number of devices it supports can influence protocol selection. EtherCAT excels in large, complex networks where multiple devices need to communicate rapidly. CANopen is more suited to smaller networks where simplicity and cost-effectiveness are prioritised. CoE is ideal for medium to large networks that require scalability without sacrificing performance.
Clock synchronisation in EtherCAT networks. Source: ethercat.org
- Communication speed
EtherCAT provides unparalleled communication speeds, perfect for high-speed data exchange applications. CANopen is slower but sufficient for many control systems, particularly automotive and embedded systems. CoE leverages the speed of EtherCAT while maintaining compatibility with CANopen, offering a balanced solution for systems that require both speed and flexibility.
- System complexity
EtherCAT is best suited for complex, high-speed systems where multiple devices and subsystems must communicate with each other in real-time. It is the perfect choice for intricate automation processes such as those found in manufacturing and robotics.
CANopen is preferable for simpler, more straightforward systems where the primary goals are reliability and cost-effectiveness. It is commonly used in embedded systems, automotive applications (both CANopen and CAN), and smaller industrial setups where system complexity is relatively low.
CoE is a versatile solution for integrated systems requiring high-speed communication and simple device management. This protocol is particularly useful in environments where existing CANopen devices must be incorporated into a more complex EtherCAT network.
- Scalability
EtherCAT is highly scalable, supports many devices, and easily accommodates system expansions. Its flexibility in network design makes it a future-proof choice for large-scale industrial applications.
CANopen and controller area network in applications offers scalability on a smaller scale, it suitable for applications that are likely to expand but do not require the extensive capabilities of EtherCAT. It is particularly well-suited for embedded systems and automotive applications where network size may increase incrementally.
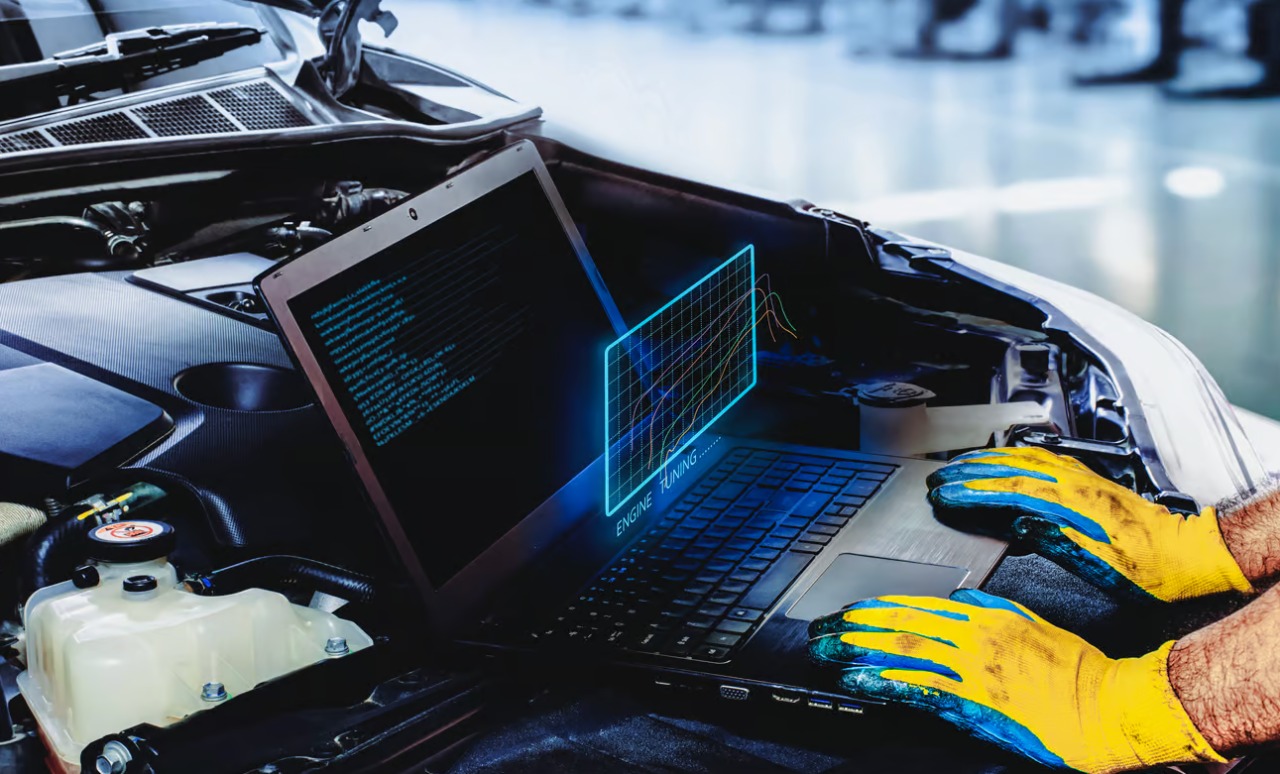
CANopen is commonly used in automotive to connect the ECU with other components, such as sensors and actuators
CoE provides a scalable solution by allowing CANopen devices to be integrated into an EtherCAT network. This makes it possible to expand a system without entirely overhauling existing infrastructure.
Comparing hardware costs and ease of implementation
When selecting the best protocol for industrial automation, it is important to consider hardware costs and ease of implementation, which impacts the overall budget and project timeline. To help you make the right choice, we've compared each protocol's hardware costs, challenges, and support specifics.
- Cost analysis
EtherCAT generally requires higher initial costs due to the need for specialised NICs, controllers, and switches. While the upfront investment in EtherCAT hardware is significant, supporting complex, high-speed networks pays off in the long run. Over time, the long-term benefits of EtherCAT, such as reduced downtime and improved performance, often justify the initial expenses.
On the other hand, CANopen is more cost-effective from a hardware standpoint. It requires less expensive controllers and simpler network components and is an attractive option for smaller systems and embedded applications.
The affordability of CANopen hardware makes it suitable for projects with limited budgets or where high-speed connectivity is not critical. CoE can be a cost-saving solution for projects where a full migration to EtherCAT would be too expensive.
- Implementation challenges
EtherCAT is known for its complexity, which can present some implementation challenges. With a steeper learning curve, EtherCAT suits for organisations with experience managing complex automation systems or those willing to invest in extensive training and development.
In contrast, CANopen is much simpler to implement. Its straightforward architecture and the wide availability of compatible hardware and software make it easy to integrate into existing systems. CANopen's simplicity reduces the time and effort required for deployment, making it the best choice for projects with tight deadlines or teams with little experience with industrial communication protocols.
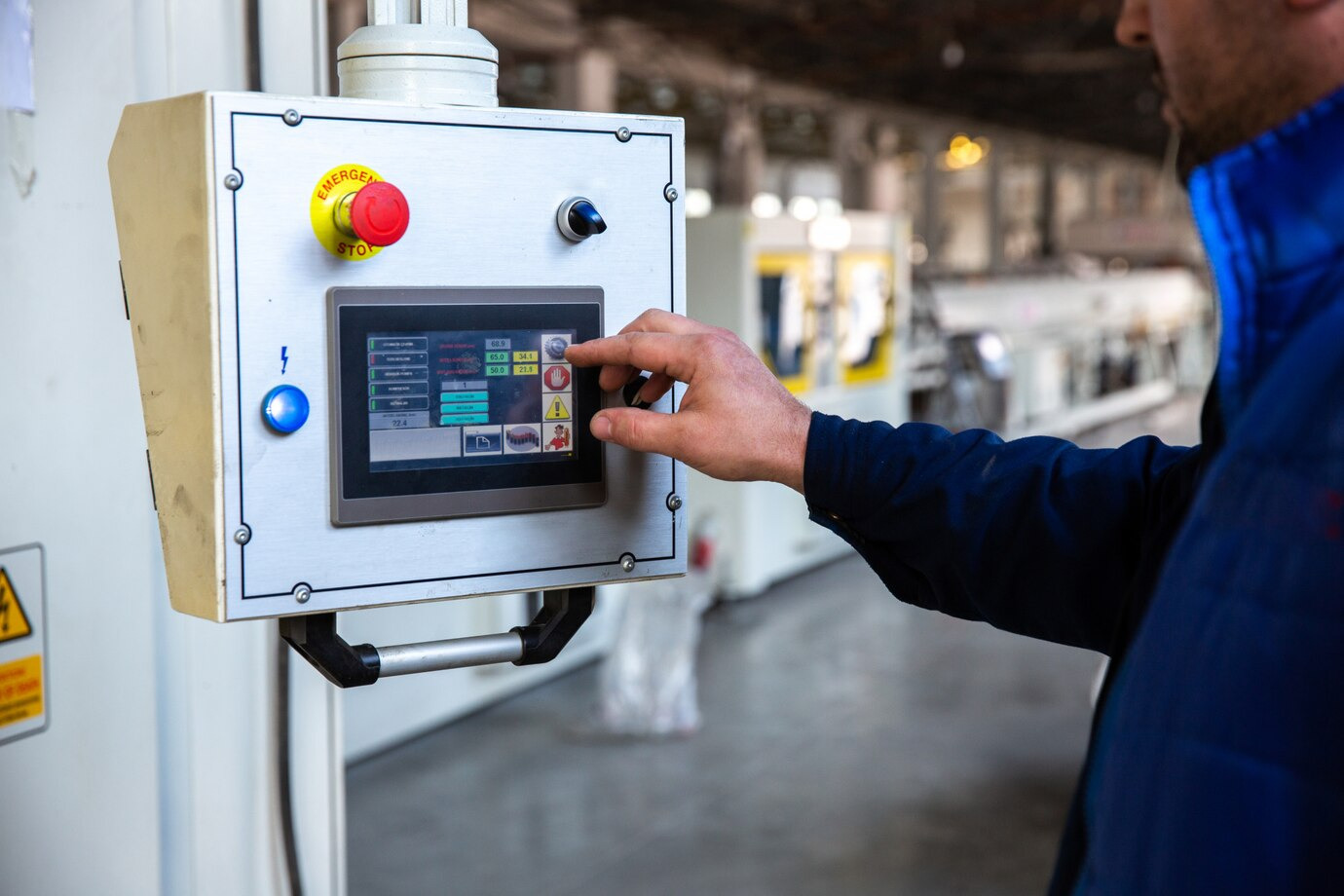
CoE useful in large-scale industrial plants, factory automation, motion control systems, and robotics
CoE offers a blend of CANopen's simplicity with EtherCAT's advanced capabilities. While integrating CANopen devices into an EtherCAT network can be challenging, the process is generally less complex than a full EtherCAT implementation.
- Maintenance and support
EtherCAT generally requires more intensive maintenance due to its complexity and the need for regular updates to network configurations, firmware, and software. However, its widespread use in high-performance industrial applications means a huge support community and a wealth of resources to assist with maintenance challenges.
On the other hand, CANopen is easier to maintain and has lower ongoing requirements. Once implemented, CANopen systems require minimal intervention, and finding support and spare parts is relatively straightforward, making it a reliable, low-maintenance option for long-term use.
While integrating and maintaining a CoE network might demand more effort than a standalone CANopen system, it is generally less labour-intensive than maintaining a full EtherCAT setup. The combined support from both EtherCAT and CANopen communities ensures that CoE users can access to a broad range of knowledge and resources.
Use cases with industrial protocols
Robotics enhancement with EtherCAT
In a recent project, a robotics manufacturer turned to EtherCAT to boost their industrial robotic arms' communication speed and precision. The company had been grappling with the limitations of its existing communication protocols, which struggled to provide the real-time control necessary for high-speed operations. This lack of responsiveness led to inefficiencies, particularly in tasks requiring precision, such as assembly and welding.
The manufacturer reduced communication latency by integrating EtherCAT, enabling real-time data exchange between the robot controllers and sensors. This upgrade resulted in smoother, more coordinated robotic movements, crucial for accuracy in precision tasks. The shift to EtherCAT streamlined operations, allowing greater efficiency in future high-speed applications.
CANopen implementation in train vehicles
A rail vehicle manufacturer needed an interoperable communication system to replace proprietary protocols for efficiently integrating various subsystems like HVAC, door control, and passenger information systems. CANopen was selected to connect ECUs across the train. By implementing CANopen CiA 421, designed for rail vehicle applications, the system standardised communication between multiple subsystems and ensured seamless data exchange.
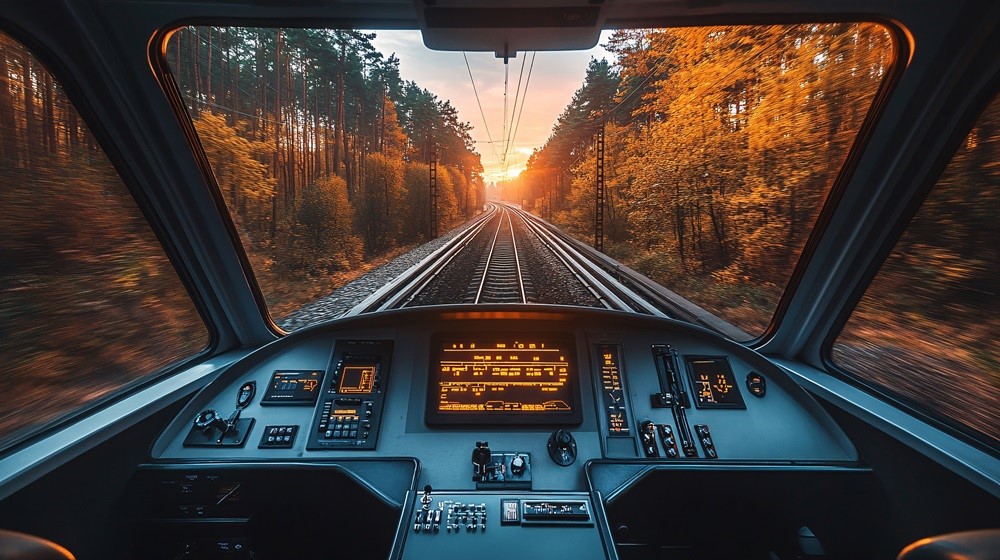
CANopen is used in rail vehicles to manage and monitor braking systems, door control units, HVAC systems, and lighting
The use of the CiA 421 protocol provided a framework for managing complex train control networks. It streamlined communication, reduced maintenance costs, and improved train safety and performance. The protocol also allowed for easier integration of new devices and future upgrades.
***
Choosing the proper communication protocol is critical to optimising the performance and reliability of industrial automation systems. You can select the protocol that best suits your project by carefully considering factors such as application requirements, system complexity and compatibility.
EtherCAT, CANopen and CoE all have their advantages, and understanding them will allow you to make an informed decision that will improve the efficiency of your operations.
Promwad offers customised solutions that meet industry standards and specific project goals. Whether you need expert advice on protocol selection, implementation support, or comprehensive systems integration, our team is here to help.
Let's discuss how we can help you achieve the best results for your industrial automation projects!