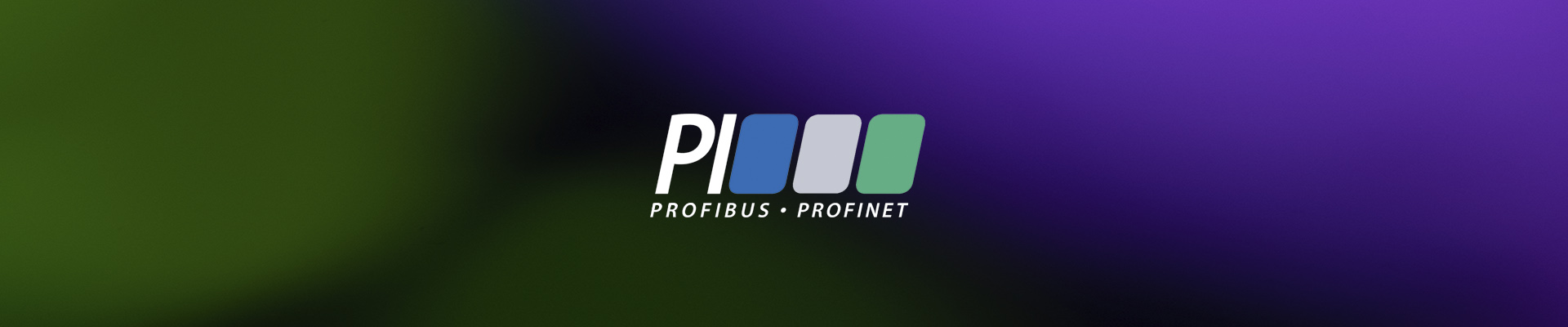
Promwad Joined the PROFIBUS & PROFINET International
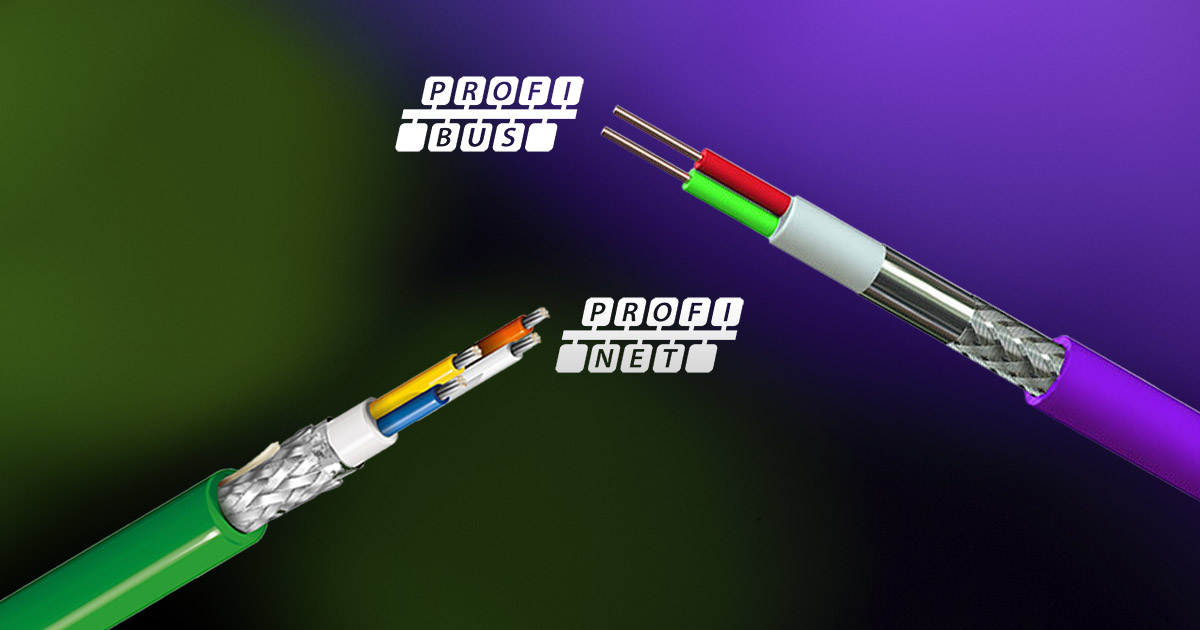
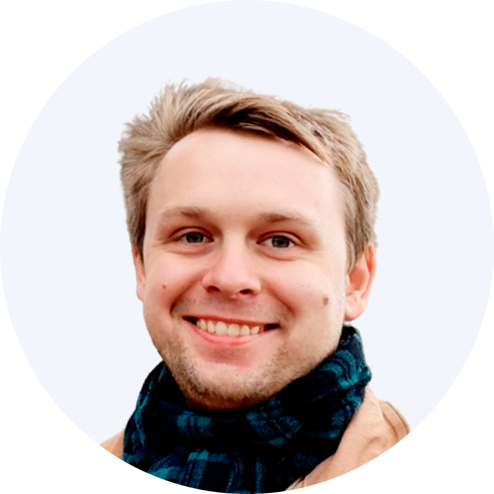
We became members of PROFIBUS & PROFINET International (PI) to provide our clients with extra value and develop solutions based on the leading standards in industrial automation – PROFIBUS and PROFINET.
Table of contents
PROFIsafe & PROFIenergy Technologies
Case Study: DC/AC Servo Drives
We became members of PROFIBUS & PROFINET International (PI) to provide our clients with extra value and develop solutions based on the leading standards in industrial automation – PROFIBUS and PROFINET.
Here are some of the benefits of our official membership in PI, the largest international organisation that develops and promotes PROFIBUS, PROFINET, PROFIsafe and PROFIenergy technologies:
- Accelerated and simplified product development through the free use of patents and technical documentation.
- Product certification to ensure devices and systems meet communications standards.
- Technical support and documentation, training and troubleshooting assistance.
- Access to expertise and networking with other industrial automation companies.
Why is the possibility of working with these technologies – PROFIBUS, PROFINET, PROFIsafe, PROFIenergy – so crucial for our clients who use our engineering services to create solutions for industrial networks, servo and stepper motor drives, PLC, DAQ, and sensors? Let's take a closer look at them.
Why do you need PROFINET?
PROFINET embedded services provide a reliable solution for real-time data exchange between different automation devices. PROFINET, an Ethernet-based protocol, enables smooth integration of devices from different manufacturers, ensuring compatibility and reliability in complex automation environments. This technology is particularly valuable in industries that require high-speed data exchange and deterministic communication, such as manufacturing, automotive and process control.
In the context of PROFINET embedded design, we focus on integrating PROFINET capabilities directly into embedded systems such as PLCs (programmable logic controllers), sensors, actuators and other industrial equipment. Promwad also provides custom embedded software development, network performance optimisation and PROFINET compliance services for real-time operations and latency reduction in mission-critical processes.
As part of this service, we configure and test embedded devices in a PROFINET environment. It includes configuring communication parameters and addressing and diagnostic tools that help monitor and maintain network health. The ability to perform real-time diagnostics and rapid troubleshooting minimises downtime and ensures continuous operation in industrial environments.
For enterprises, using PROFINET embedded services means better flexibility of automation systems. As production requirements change, companies can easily modify their operations by integrating new devices into the PROFINET network without huge reconfiguration. Integration PROFINET into embedded devices provides real-time communication, improved diagnostics and the flexibility to scale operations, making it a cornerstone of industrial automation strategies.

PROFIBUS Protocol
PROFIBUS is a network protocol that provides data exchange at the field level (between controller and sensors) and higher-level communication systems. We use two variants of this protocol for different industrial applications:
- PROFIBUS DP (Distributed Periphery) is a protocol for data exchange with peripheral devices. It is used where high data transfer rates are required.
- PROFIBUS PA (Process Automation) is a protocol connecting field devices and control systems. It is used in hazardous areas.
PROFIBUS can be implemented for distributed I/O applications, providing high performance and efficiency.
One PROFIBUS DP cable can connect up to 126 input/output devices, each connecting to tens and hundreds of connection points. It allows for optimal and efficient operation of a single controller.
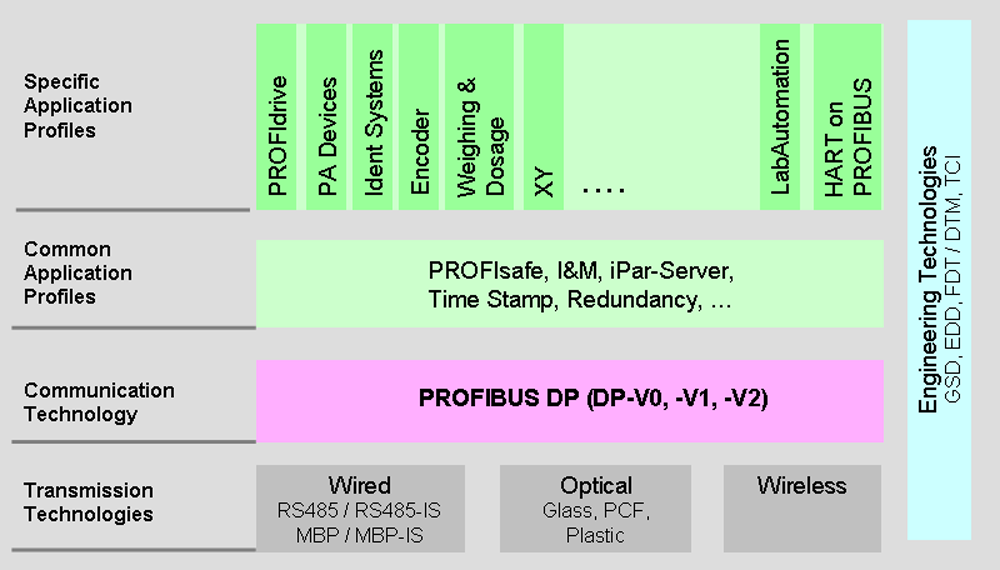
PROFIBUS building blocks. Source: profibus.com
With this standard, we realise proactive equipment management when new devices are introduced without stopping work. It is made possible by PROFIBUS Profile v 3.02, which allows new devices to adopt the functionality of previous versions temporarily.
The protocol can be used in various industries for reliable and efficient data exchange between devices and control systems. The main areas of application include industrial and process automation, energy management, building automation, transport and logistics, the food and beverage industry, and the automotive field.
PROFIBUS Software Design
PROFIBUS software design is an important aspect of industrial automation that involves developing software solutions for communication and control systems using the PROFIBUS protocol.
As, among other things, a PROFIBUS software company, Promwad specialise in efficient software development for better data exchange between various industrial devices, such as sensors, actuators, and controllers. PROFIBUS is known for its reliability and real-time capabilities, which makes it a perfect choice for manufacturing, process automation, and material handling.
In addition to development, our PROFIBUS software consulting services provide clients with expert guidance on implementing and optimising PROFIBUS solutions in their existing systems. We offer end-to-end support, from the initial design phase to deployment and maintenance, ensuring that the software is tailored to meet specific operational requirements.
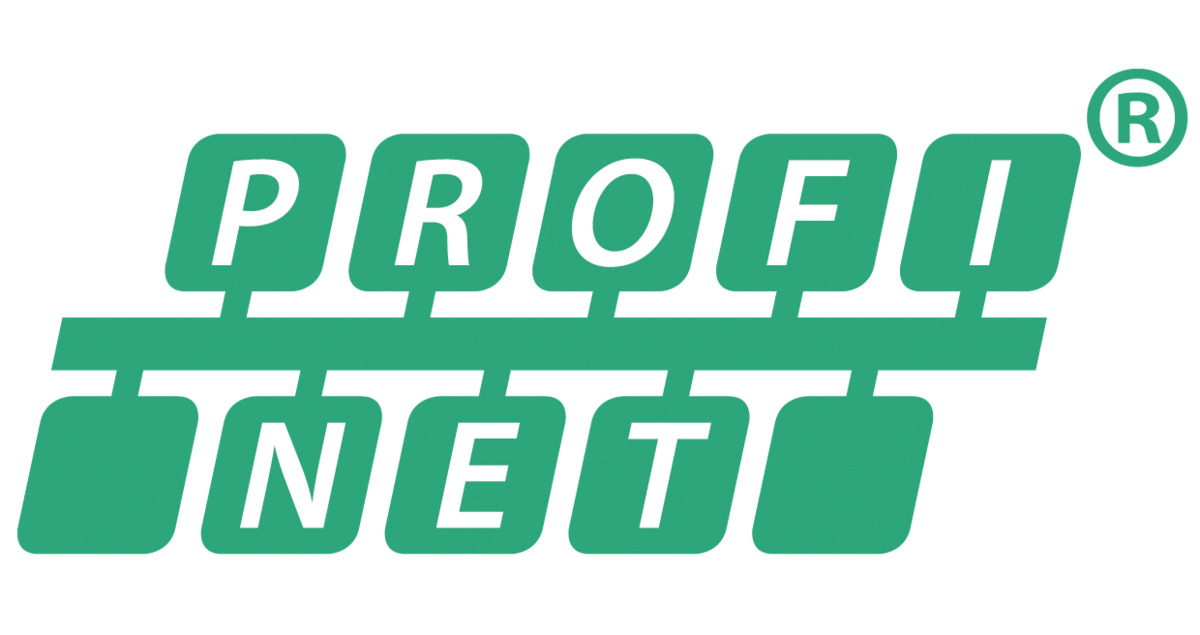
PROFINET Protocol
PROFINET is an Ethernet-based industrial communication protocol for real-time data transmission between devices, controllers, and control systems. It is used in Industry 4.0 and the automotive industry.
PROFINET application areas in industrial automation. Source: profibus.com
Supporting different network architectures – linear, ring or star – PROFINET can be easily adapted to specific enterprises' conditions and saves on standard solutions.
PROFINET Embedded Development
PROFINET embedded development is an area of industrial automation that integrates PROFINET capabilities into embedded systems such as sensors, actuators and controllers. It involves creating customised firmware and software that allows these devices to communicate effectively over PROFINET. By embedding PROFINET into devices, companies ensure deterministic communication for robotics applications, factory automation and process control.
In addition to software integration, developing PROFINET embedded systems often involves designing hardware components that support the PROFINET protocol. It includes selecting suitable microcontrollers, developing custom PCB, schematics, and ensuring that the hardware meets the stringent requirements of industrial environments, such as electromagnetic compatibility (EMC) and temperature tolerance.
IO-Link Protocol
IO-Link communication is a standardised IO technology that facilitates seamless communication between sensors, actuators, and the automation system. This protocol is designed to support different applications, from simple binary sensors to more complex devices that need extensive data exchange.
The IO-Link communication protocol allows for bidirectional data exchange, making configuring, diagnosing, and maintaining connected devices easier. It is an effective tool in industrial automation due to its capability to deliver complete device diagnostics and parameter data.
When integrating IO-Link with PROFINET, the IO-Link Master PROFINET module has an important function. This master module is the gateway, translating IO-Link data into a format the PROFINET network can understand. The PROFINET IO-Link Master provides communication between the field devices and the controller, resulting in accurate and real-time transfer of data.
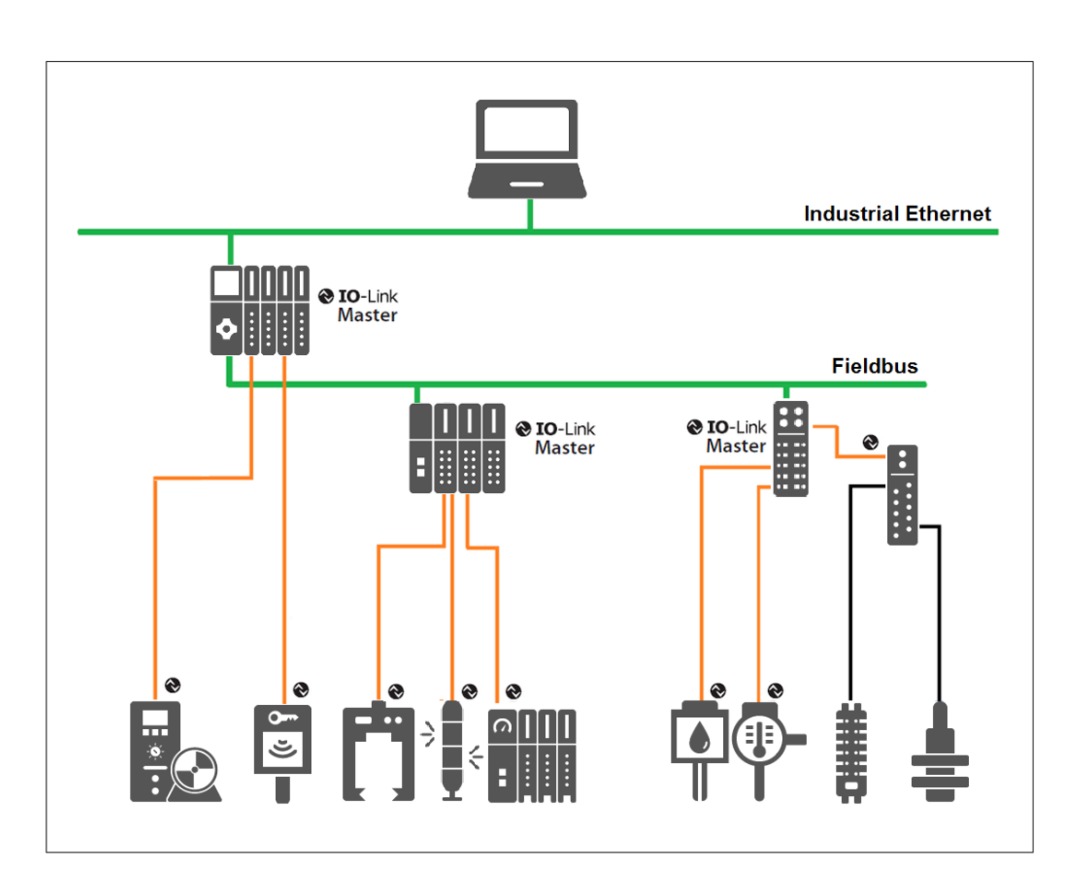
How the IO Link works. Source: profibus.com
Beyond PROFINET, IO-Link also extends its compatibility to other industrial Ethernet protocols, such as EtherNet/IP and EtherCAT. The Ethernet IP IO-Link Master and EtherCAT IO-Link Master allow IO-Link devices to be connected to EtherNet/IP and EtherCAT networks, respectively. This flexibility ensures that IO-Link can be used in various industrial settings, regardless of the preferred network protocol. It makes IO-Link an ideal solution for manufacturers who require versatile and scalable automation systems.
The adaptability of IO-Link to Ethernet IP is particularly noteworthy, as it enables the connection of IO-Link devices to Ethernet-based systems without losing any of the benefits of IO-Link communication. Users can keep a reliable connection across the various layers of the automation system – from the factory floor sensors and actuators to the higher-level control systems – by converting IO-Link data to Ethernet IP.
Overall, IO-Link communication enhances the efficiency of industrial automation by providing a standardised, flexible, and easy-to-integrate solution for connecting devices across different networks. Whether it's PROFINET, EtherNet/IP, or EtherCAT, IO-Link ensures that data is communicated effectively, enabling advanced diagnostics, simplified configuration, and improved overall system performance.
PROFIsafe & PROFIenergy Technologies
PROFIsafe is part of the PROFIBUS and PROFINET protocols and provides them with additional safety.
PROFIenergy is a profile for managing and optimising energy consumption in production and industrial environments, developed as part of the PROFINET and PROFIBUS communication protocols. This profile allows equipment to be put into energy-saving modes when not used.

Case Study: DC/AC Servo Drives
DC/AC servo drives is a project that Promwad engineers implemented by commission from a European manufacturer of industrial automation systems. We were responsible for developing hardware, software and enclosure design to launch servo drives into mass production.
During the development of these devices, we used PROFIBUS and PROFINET protocols, and provided support of advanced protective functions, including the certification for SIL 3 level. As a result, our client received a device with high fault tolerance and performance.
***
PROFIBUS and PROFINET simplify data exchange in automation and control systems. They enable real-time control, scalability, and integration with IT systems and support efficient production processes. These protocols play a key role in ensuring uninterrupted and reliable data transmission, which makes them indispensable tools for optimising industrial automation.
Our company specialises in PROFINET embedded services and PROFIBUS software development, offering comprehensive solutions for industrial automation. Promwad PROFINET services focus on integrating the high-speed, real-time communication capabilities of the PROFINET protocol directly into embedded systems for efficient data exchange across complex industrial environments.
For PROFIBUS, we deliver tailored software solutions that guarantee reliable communication between industrial devices using the PROFIBUS protocol. Our consulting services further enhance this offering by providing expert guidance on implementing and optimising PROFIBUS systems within your existing infrastructure.
Promwad's membership in PROFIBUS & PROFINET International gives us access to all necessary documentation and technical support, allowing us to develop industrial automation software and hardware for our clients. Contact us to discuss your project!