Sealing Electronics Enclosures Part 2: Polymer and Metal Welding
We continue our journey in exploring technologies for the production of sealed electronics enclosures. This time, we will focus on gluing and welding, which are methods used to produce power supply units, headphones, USB flash drives, and other devices that aren’t meant to be taken apart and require water and dust protection.
Let's take a closer look at five types of welding: hot plate, electromagnetic induction, vibration, ultrasound, and laser. Engineers and technologists aren’t the only ones who might find this information interesting. :-)
If you’ve read part one of this article, you may remember that we used examples of our engineering projects to explain how the most popular sealing methods work: sealants and injection molding (multicomponent and over-molding). At the end of this part, there will be a table with an overview of all the methods that we described in both parts of the article. This table should help readers choose an optimal production technology for their particular hardware project.
Contents
- Introduction
- Joining an enclosure using vibration welding
- Ultrasonic welding of enclosures
- Laser welding enclosures
- Joining housing components with adhesives
Disclaimer. The intention of our blog is to share our experience in the development and production of electronics components. We are not in the business of selling or advertising any equipment. The specific examples of welding equipment and technologies are shown solely for educational purposes.
Naturally, welding is a great way to produce sealed metal housings and enclosures, but the main focus of this article is the welding of various types of thermoplastics, which are special polymers that melt when heated and then become solid again when they cool down.
1. Hot plate welding
This method involves putting the enclosure in contact with a hot, non-stick, hydrophobic plate (PTFE), commonly known under the brand name Teflon.
A plate welding machine from Suzhou Youwoly Machinery Equipment Co., Ltd. (Shanghai, China) and samples of manufactured products Photo source: made-in-china.com
Hot plate welding is used to quickly assemble robust, permanent, and sealed polymer electronics enclosures.
How it works: two molded enclosure components are connected using a heated plate.
A diagram of the process is shown below:
Stages of hot plate welding for polymer products
- Two parts of the product – the enclosure components – are set at a distance from one another.
- A hot plate of a specific temperature is inserted between them. Due to the contact or proximity to the surface of the hot plate, the enclosure components are heated at the planned connection points.
The spacers on the hot plate and the structural elements that hold the components (limiters) determine the depth of the initial melt. The holding time determines the depth of the secondary softening of the polymer. - When the connection areas reach the required temperature, the fixtures separate.
- The heating plate is withdrawn.
- Then the fixtures compress the components together. The spacers on the fixtures determine the amount of seam material displaced during the welding process.
- In this state, the enclosure components are held under slight pressure for a short time until the molten layer cools, creating a weld between the two joint surfaces.
When the cooling is complete, a gripper in one of the fixtures releases the finished enclosure.
Samples of products that were produced with the hot plate welding method using equipment from Suzhou Youwoly Machinery Equipment Co., Ltd. (Shanghai, China). Photo source: made-in-china.com
2. Welding the enclosure using electromagnetic induction
Electromagnetic welding is a simple, fast, and reliable method for the assembly of structural and hermetic seals. It is suitable for most thermoplastic materials and creates seals that can withstand high pressures. This technology also has the added benefit of being able to weld dissimilar types of thermoplastics together, as well as paper or aluminum with thermoplastics (reinforced and unreinforced).
A diagram of the process is shown below:
How it works:
The embedded element for this welding method consists of a dispersion of micron-sized metal powders, such as iron, stainless steel graphite, or ferrite, which allows the material to heat up under the influence of an electromagnetic field.
Here are examples of using induction welding to join two parts:
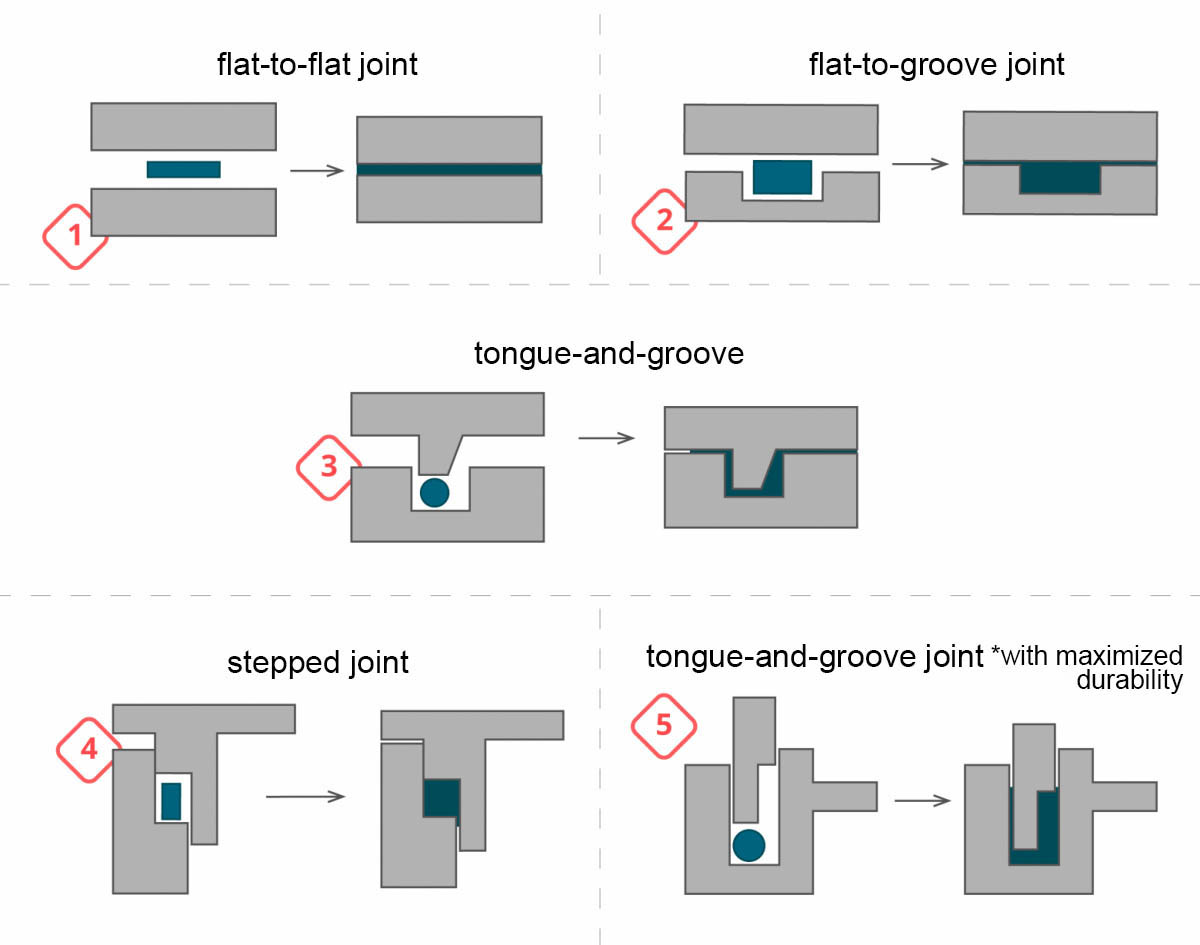
Types of induction welding joints used to connect two thermoplastic parts
- A flat-to-flat joint is well suited for welding long seams. It is often used in solar panels.
- A flat-to-groove joint is often used in the production of car dashboards.
- Tongue-and-groove joints create very strong connections. This method is excellent for connections that need to withstand extreme loads and require airtight seals.
- Stepped joint. Used for joining plastic parts that need to withstand vibration.
- Tongue-and-groove joint with maximized durability. Used for high-pressure seals.
Let's take a closer look at some of the advantages and disadvantages of this method:
The advantages of electromagnetic (induction) welding:
- All thermoplastic materials, both crystalline and amorphous, can be used for this method.
- The thickness of the product is preserved, and the weld seams can be hidden because the material is melted from the inside of the welding joint.
- Minimal contact pressure and fast welding cycles.
- Can be automated for high volume production.
- Easy implementation of structural, hermetic, and high-pressure seals.
- The physical and chemical properties of the welded section are similar to that of the materials being joined.
- Large range of sizes for the welding joints: from a tiny spot to 3 m.
- Long shelf life of the electromagnetic bonding material.
- No pre-treatment is required for the joint areas.
- Clean and quiet assembly.
Disadvantages of electromagnetic (induction) welding:
- Not suitable for encapsulating electrical devices in thermoplastics, i.e. winding coils, magnets, printed circuit boards, sensors, etc.
- Prototype welding is required when assembling new products since the electromagnetic seam depends on the welding coil and the ability to calculate the complex geometry of the parts’ joint surfaces.
- High cost of welding equipment.
- Electromagnetic welding coils tend to get overloaded and overheat.
3. Joining an enclosure using vibration welding
Vibration welding of thermoplastic materials is based on the principle of friction welding. The heat that melts the thermoplastic is generated when two workpieces are pressed against one another and vibrated. The small relative displacement of the joint causes friction and the surfaces are heated as a result. The heat melts the thermoplastic at the contact points. When the vibration stops, the parts are automatically aligned.
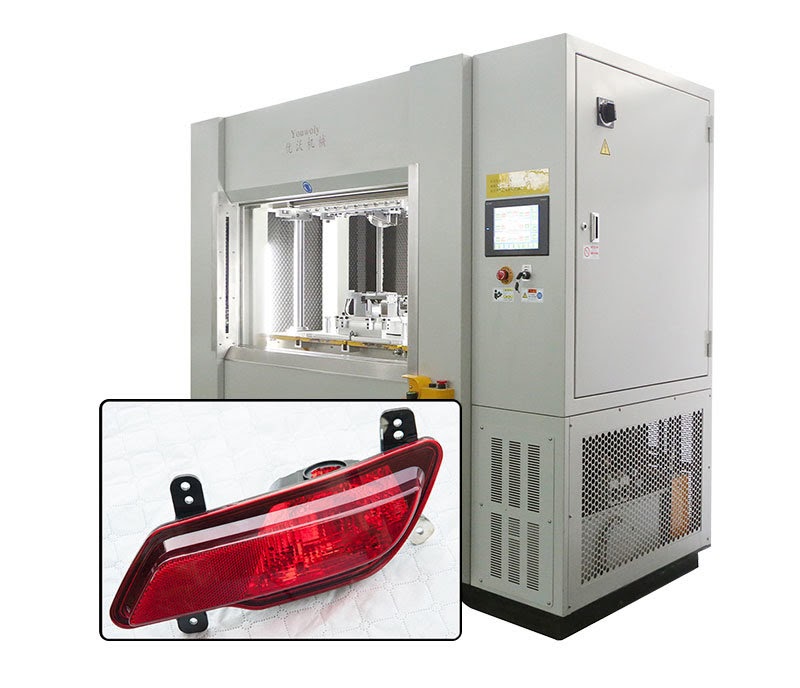
Vibration welding machine from Suzhou Youwoly Machinery Equipment Co., Ltd. (Shanghai, China). Photo source: made-in-china.com
It usually takes about 2-3 seconds for the materials to melt during vibration welding. The total cycle time ranges from 6 to 15 seconds on average, including the loading and unloading of the components.
Vibration welding is widely used in the manufacturing of automotive parts.
4. Ultrasonic welding of enclosures
Ultrasonic welding is a fast, clean, and efficient method for joining rigid, injection-molded thermoplastic components. This method is used in all manufacturing segments where it is necessary to join two plastics or to join plastic parts with non-plastic materials.
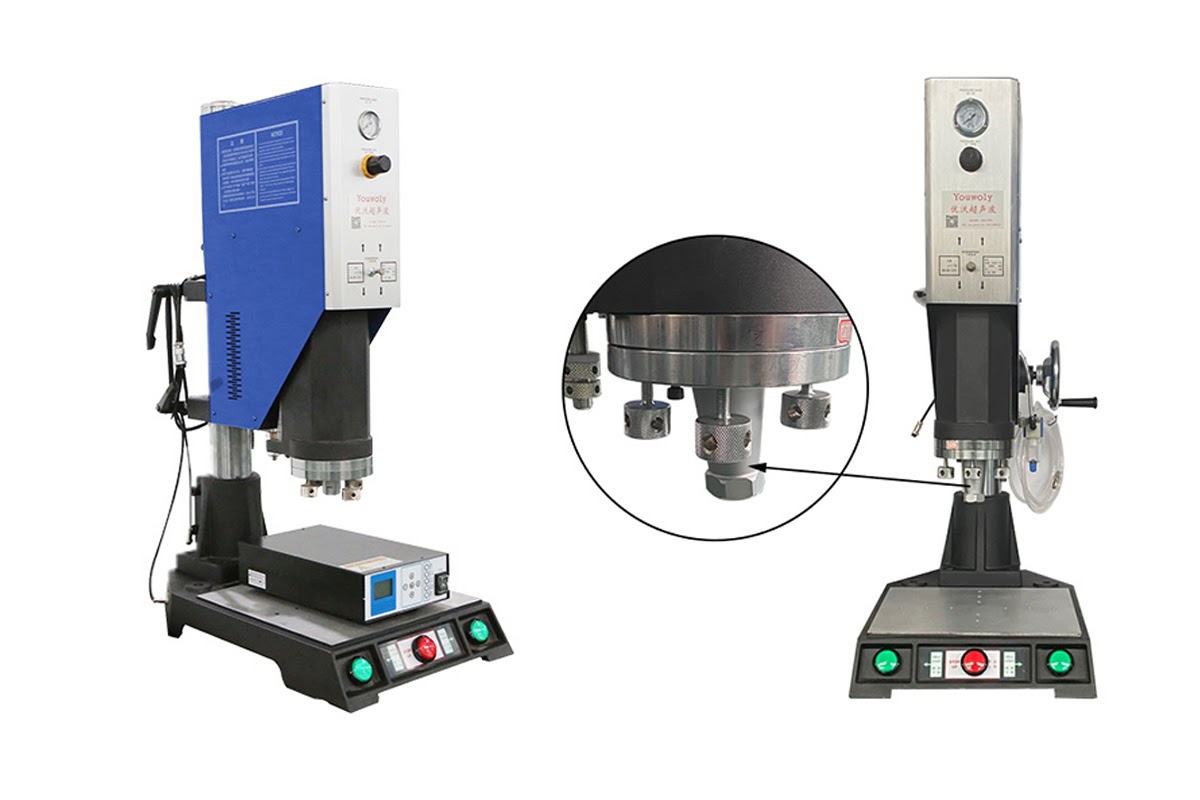
Ultrasonic welding machine from Suzhou Youwoly Machinery Equipment Co., Ltd. (Shanghai, China) Photo source: made-in-china.com
Parts that can be welded by ultrasonic or vibration welding are more cost-effective. With ultrasonic welding, a finished product can be obtained in 0.1–3 seconds, and the equipment costs are also quite low. For example, the machine pictured above can be bought for 2–3 thousand US dollars, while the prices for the other equipment shown in this article start from 15-18 thousand USD. However, vibration welding can be used to weld larger and more complex parts.
Typical examples of products that made with ultrasonic welding
Ultrasonic welding is an excellent alternative to using glues, solvents, or mechanical fasteners to produce sealed enclosures that are not meant to be taken apart, such as power supply units, headphones, and chargers.
Advantages of ultrasonic welding:
- Energy efficiency and high performance at a lower cost than many other assembly methods.
- Does not require complex ventilation systems to remove smoke or heat from the work area.
- Convenient to integrate into an automated assembly line.
- Immediate start and stop without residual heat.
5. Laser welding enclosures
Laser welding technology is similar to IR welding, as it is also a method that does not require direct contact with a heating element. The appropriate heat energy is directed into the workpiece material via a laser beam, which is focused onto the workpiece surfaces to be welded.
How laser welding works
In some cases, the center of the joint zone can heat up more than the edge zones. Thus, there is an intense mixing of the melt in the joint zone during welding, which contributes to the extreme strength of the weld. The thermal expansion of the melt provides the welding force required to join the pre-clamped parts.
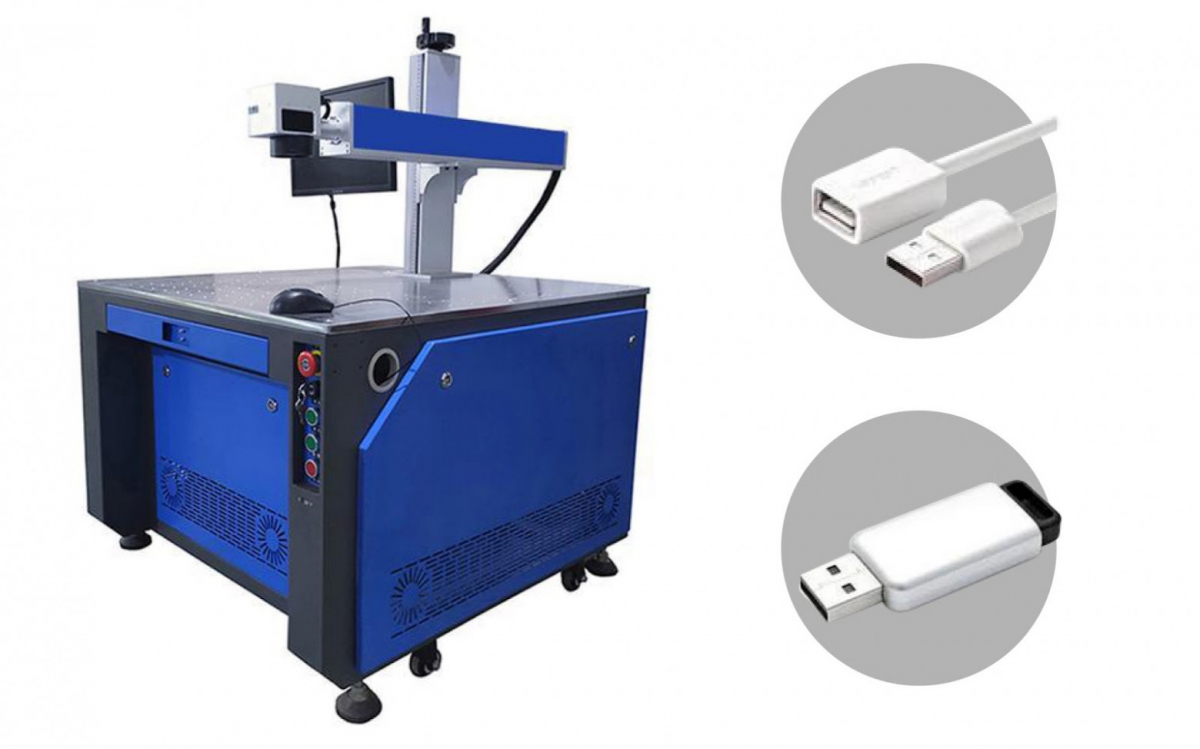
Intouch Laser Welding Machine from Taiyi Laser Technology Company Ltd. (Shenzhen, China) and some product examples. Photo source: made-in-china.com
Laser welding is a popular method for sealing a wide variety of electronics connectors.
6. Joining housing components with adhesives
Adhesive bonding is one of the most convenient assembly methods, especially when a thermoplastic needs to be joined with similar or different materials, including metals. The adhesive distributes stress over the entire area of the bonded surface and can ensure a good seal, if necessary.
Flexible adhesives allow some movement between the joined surfaces, which allows the joint to compensate for differences in the linear thermal expansion coefficients of the joining materials. Adhesives are also relatively inexpensive and do not require expensive specialized equipment.
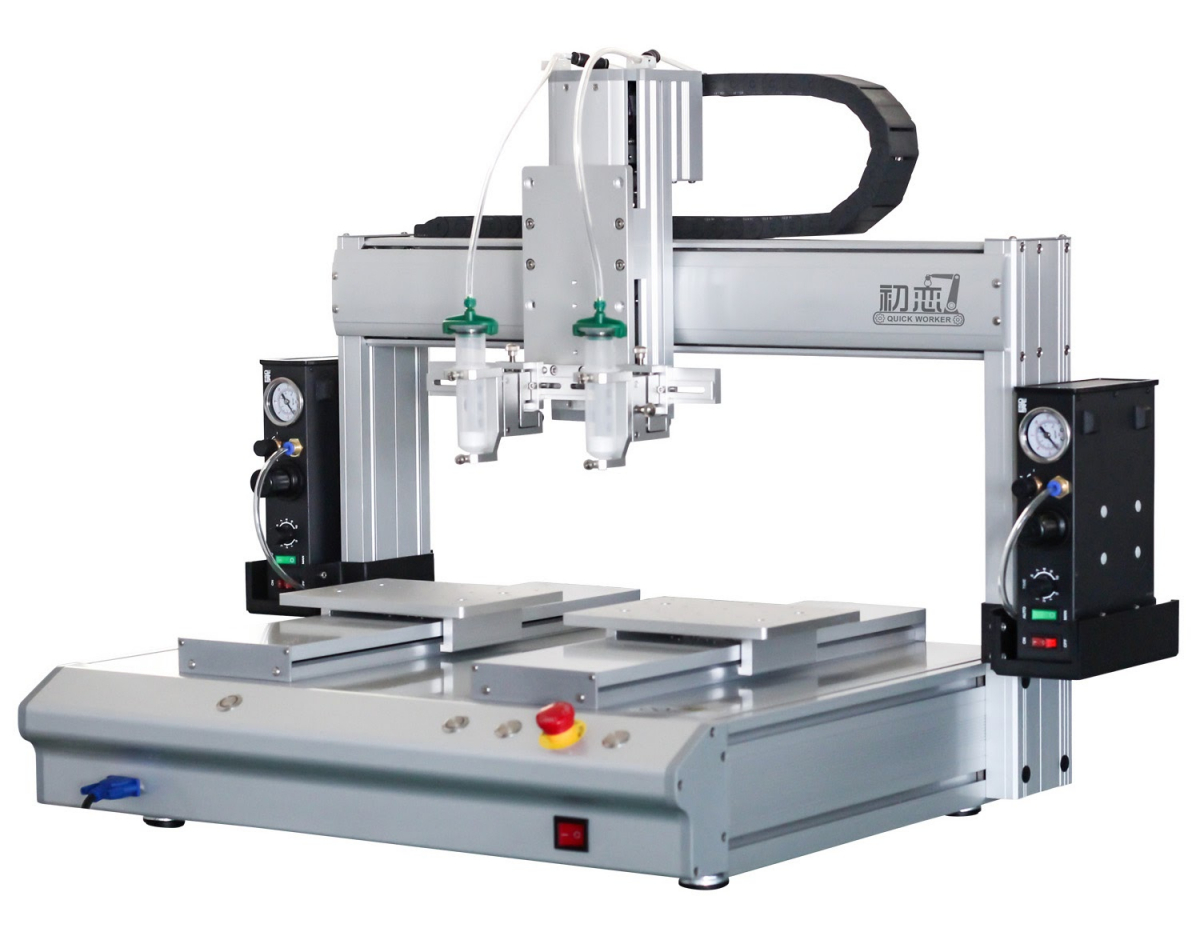
Automatic glue dispenser with a positioning system. Manufacturer: First love robot Co., Ltd. (Guangdong, China). Photo source: made-in-china.com
Advantages of using adhesives in electronics enclosure production:
- Low equipment costs. Easy to use with automated equipment.
- Dissimilar materials can be joined.
- Elasticity and a good seal.
- Low cost and ease of repair.
Conclusions
As you may have learned from part one of the article, which was about injection molding and sealants, several factors simultaneously affect the choice of an ideal method of sealing an enclosure for a particular device, including design requirements, production capabilities, batch size, budget, operating conditions, and others.
As promised, here’s a table with an overview of the characteristics for all the technologies that we discussed in the both parts of the article:
Injection molding and sealants from part 1
Sealing methods | Equipment | Advantages | Disadvantages |
Multi-component injection molding | Injection molding machine with two injection units and expensive set-up | Low cost for mass production, no extra costs for sealing | Ineffective for small batches Requires expensive equipment, set-up, and highly qualified personnel |
Over-molding | Injection molding machine and several sets of equipment | Can be used as an alternative to multi-component injection molding Due to simpler equipment set-up, the technology is more affordable for small batches | Manipulator or manual labor costs |
Use of a sealant | Not required | Low cost, no equipment needed | Additional operations during assembly (installation of sealants), fasteners are required in the seal area |
Sealing methods | Equipment | Advantages | Disadvantages |
Hot plate welding | Hot plate with thin PTFE (Teflon) layer, fixtures | Simplicity, strong connections for nearly all types of thermoplastics | Additional weld seam processing, long weld cycle, works on flat surfaces |
Electromagnetic (induction) welding | Induction welding equipment | Capable of joining dissimilar materials. Invisible seams/joints. Capable of welding complex profiles. Short welding cycle. Automation capability Easy to create high pressure seals | Expensive equipment, prototype welding required. Not suitable for welding electrical devices that are enclosed in thermoplastics (winding coils, magnets, printed circuit boards, sensors, etc.) |
Vibration welding | Vibration welding equipment | Short welding cycle | Flat welding surface. Risk of damaging electrical components with vibration. Only compatible thermoplastics can be joined. Possible misalignment of parts |
Ultrasonic welding | Ultrasonic welding machines, portable installations, or hand-held devices | Short welding cycle, energy efficiency, high production rate. Can be easily incorporated into an automatic assembly cycle. Invisible seam/joint. Environmentally friendly. Capable of joining dissimilar materials | Not suitable for joining parts with thick walls. Sensitive to moisture |
Laser welding | Laser welder | Short welding cycle, good appearance. Minimal temperature variations. Environmentally friendly. Capable of joining dissimilar materials | Expensive equipment |
Adhesive bonding | Fixtures | Simplicity, low cost. Uniform stress distribution: dissimilar materials can be joined, including those that might get destroyed during welding operations | Surface preparation required, long curing time. Toxicity. Low strength compared to welded joints |
We hope that you will find our experience in the development of sealed enclosures useful.
Our projects