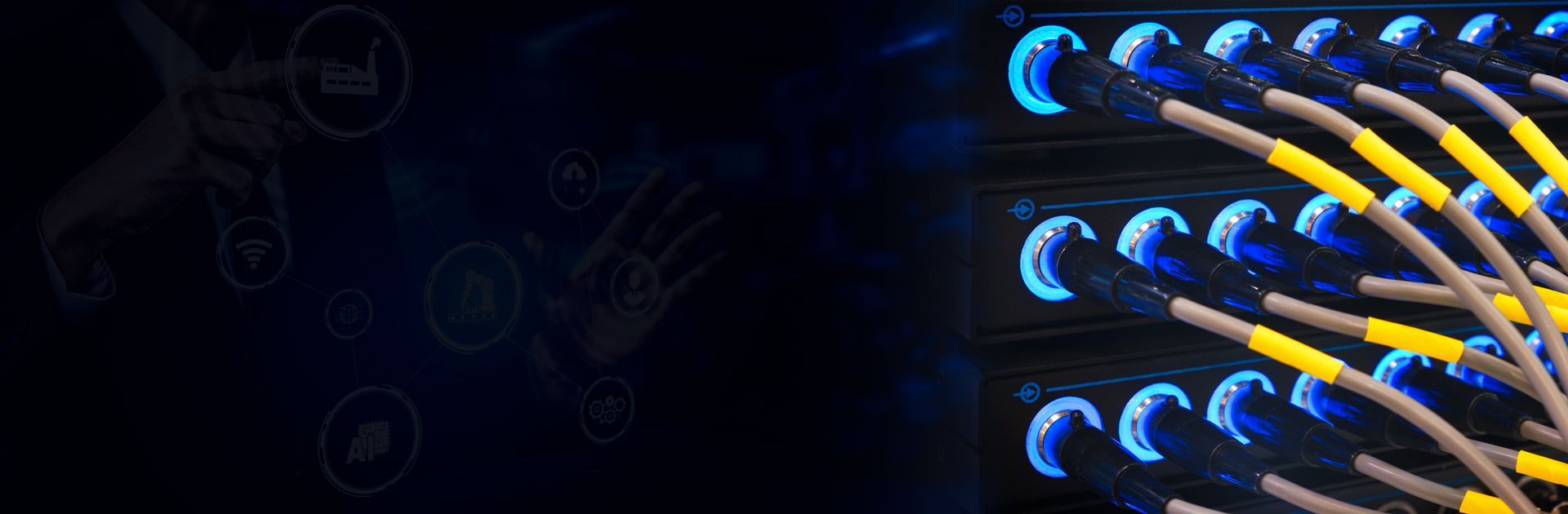
Design for Industrial Networks
Industrial Network Design Solutions
Our industrial network design solutions are built to transfer large amounts of data in real time between devices placed far apart from one another. These systems are applicable across various domains, including power management, industrial automation, and smart buildings.
We develop software and hardware to help our clients implement their industrial network projects successfully. Our services include creating fieldbus solutions, protection and control systems, data acquisition and analysis tools, network controllers, and sensors.
What We Do for Industrial Communication Networks
Analysis and data acquisition (DAQ) systems
Automation and visualisation systems
Network controllers
HMIs and IPCs
Industrial Internet/
Industry 4.0 solutionsI/O systems and PLCs
PC cards
Sensors
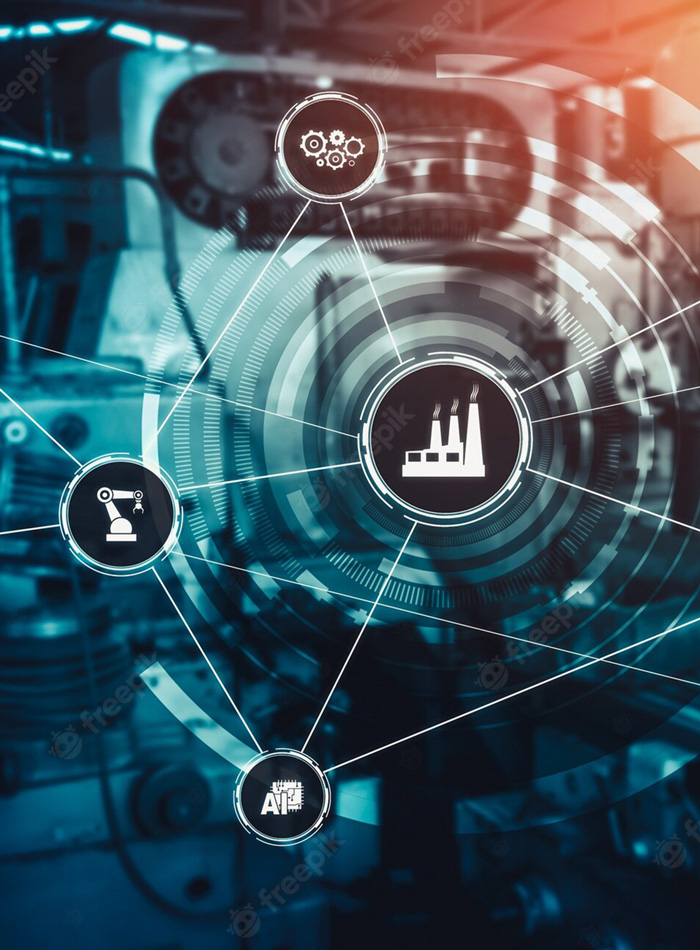
Our Tech Stack for Industrial Communication Networks
ODVA: EtherNet/IP, DeviceNet, ControlNet, CompoNet
OpENer (OpENer is an EtherNet/IP stack for I/O adapter devices), EtherNet/IP Client (asynchronous, non-blocking, EtherNet/IP client implementation for Java), EIPScanner, CIPster Ethernet/IP Stack in C++, EEIP.NET (Ethernet/IP compatible library for .NET implementations)
Modbus RTU/ASCII/TCP/Plus
libmodbus, PyModbus, EasyModbusTCP.NET, eModbus, tokio-modbus, freemodbus
PI
PROFIBUS, PROFINET, PROFINET RT, PROFINET IRT, PROFINET via TSN
FieldComm Group
HART, HART-IP, WirelessHART
POWERLINK
openPOWERLINK_V2
CC-Link
CC-Link, CC-Link IE
SERCOS
SERCOS III, SERCOS
netX – Scalable Industry 4.0 Communication Platform by Hilscher
We use netX to build cutting-edge solutions within the Industry 4.0 concept. This comprehensive software and hardware platform was designed by our partner, Hilscher. The multiprotocol netX chips support all the leading Ethernet standards, facilitating process and application deployment while ensuring communication for flexible industrial networking.
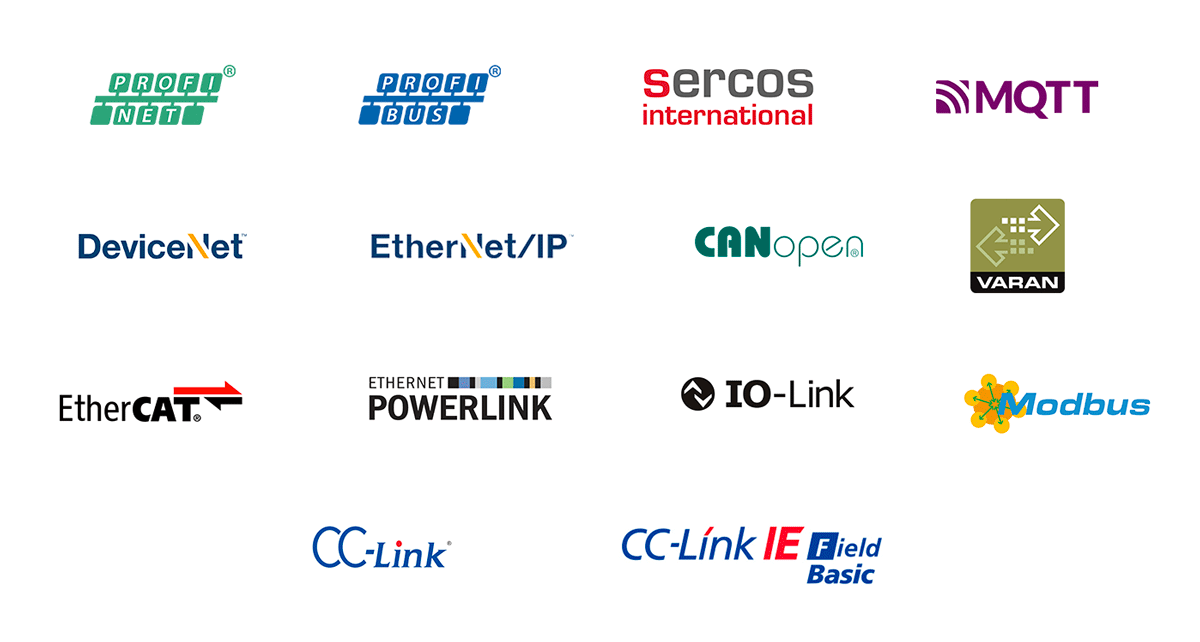
The benefits of the Hilscher netX solutions:
Flexibility: their SoC family connects all fieldbus systems and real-time Ethernet networks.
Fast product launch enabled by a comprehensive software and hardware solution combined with an extensive ecosystem.
Easy integration due to continuous technical support and the development of necessary solutions.
Investment reliability: as a market leader, Hilscher guarantees long-term access to its products.
Learn more about our Hilscher-powered solutions
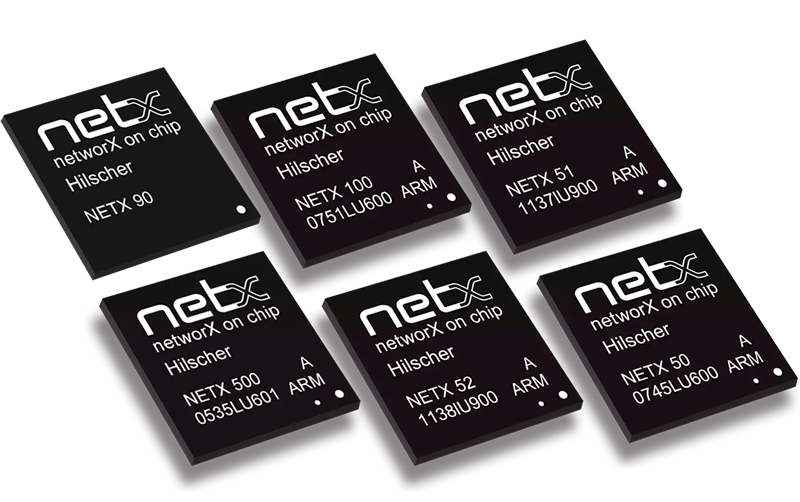
An Overview of Available SoCs from Hilscher
NETX 90
| NETX 51 | NETX 52 | NETX 100 | NETX 500 |
Smallest Multiprotocol SoC | Network controller for fieldbus and Real-Time Ethernet slaves with memory controller | Network controller for fieldbus and Real-Time Ethernet slaves | Network controller for Real-Time Ethernet and fieldbus master and slaves | Network controller for Real-Time Ethernet and fieldbus master and slaves with display controller |
|
|
|
|
|
Other Hardware Platforms for Industrial Networks
EtherCAT
Texas Instruments: AM335x, AM437x, AM57x, AMIC110, AMIC120, AM654x, AM64x.
Infineon Technologies: XMC4300, XMC4800.
Microchip Technology: LAN9254, LAN9253, LAN9252.
ASIX Electronics: AX58400, AX58200.
Beckhoff: ET1100.
FPGA: AMD (Xilinx), Intel (Altera), Lattice, GOWIN.
IO-Link
STMicroelectronics: L6360, L6362A, L6364.
Renesas Electronics: CCE4502, CCE4503, CCE4510, ZIOL2201, ZIOL2211, ZIOL2401, ZIOL2411.
Maxim Integrated: MAX22514, MAX14829, MAX22520, MAX22515, MAX22513, MAX14828, MAX14819, MAX14827A, MAX14838, MAX14839, MAX14836, MAX14826, MAX14832, MAX14820, MAX14824, MAX14821.
Profinet
Texas Instruments: AM335x, AM437x, AM57x, AMIC110, AMIC120.
FPGA: AMD (Xilinx), Intel (Altera), Lattice, GOWIN.
Siemens: ERTEC 200, ERTEC 200P.
Profibus Slave
Texas Instruments: AM335x, AM437x, AM57x, AMIC110, AMIC120.
FPGA: AMD (Xilinx), Intel (Altera), Lattice, GOWIN.
Profichip: PA002005 | VPCLS2, PALF2009 | VPC3+S, PALF2012 | VPC3+S, PALF2030 | VPC3+CLF, PALF2080 | VPC3+CLF3.
EtherNet/IP
Texas Instruments: AM335x, AM437x, AM57x, AMIC110, AMIC120.
FPGA: AMD (Xilinx), Intel (Altera), Lattice, GOWIN.
HART
ON Semiconductor: A5191HRT, NCN5192, NCN5193.
Analog Devices: AD74115HN, AD5700, AD5700-1.
Profibus Master
Texas Instruments: AM335x, AM57x.
FPGA: AMD (Xilinx), Intel (Altera), Lattice, GOWIN.
Our Case Studies in Industrial Automation
Our Cooperation Models
A flexible approach to suit your current needs
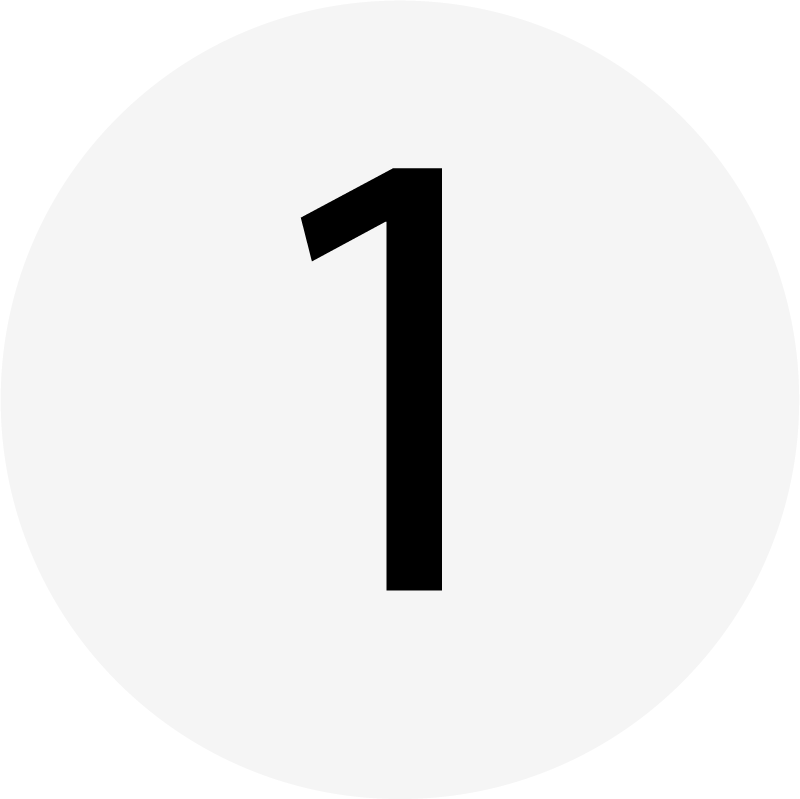
Dedicated Team
We will form a team to fit your specific engineering task. You are free to manage it and provide additional resources as needed.
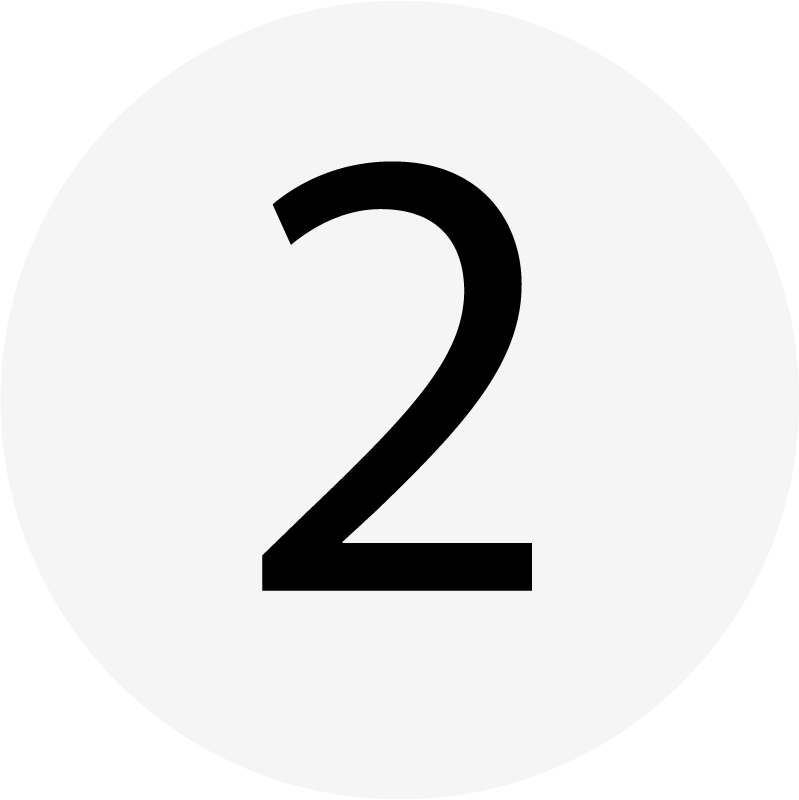
Project-Based
We can join you at any stage of the project or take it on in its entirety, including the management and risk control.
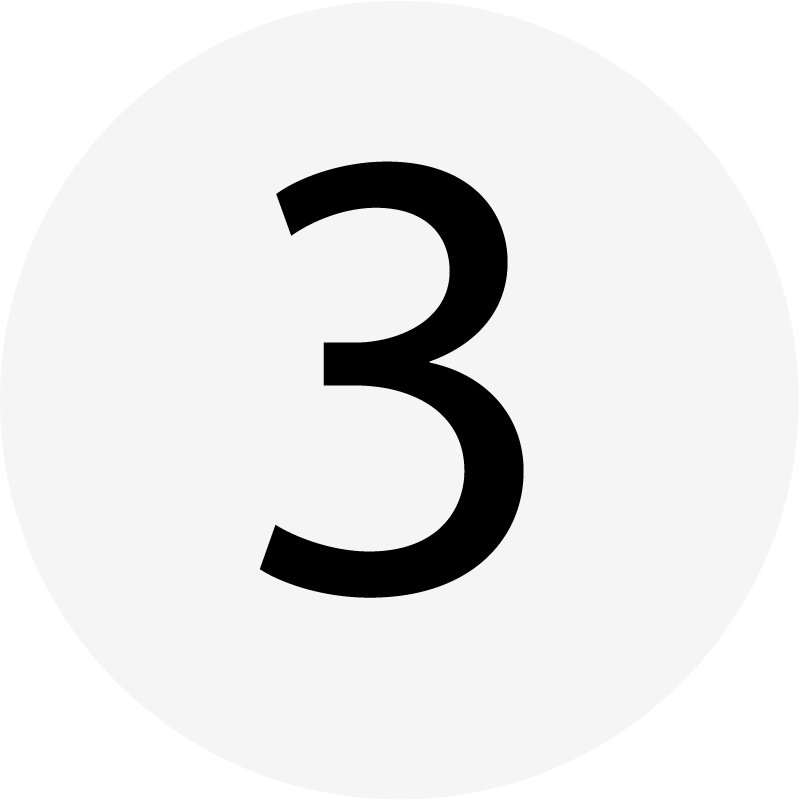
Fixed Price Model
This contract fixes the price so that it does not depend on resources used or time expended by our engineering team.
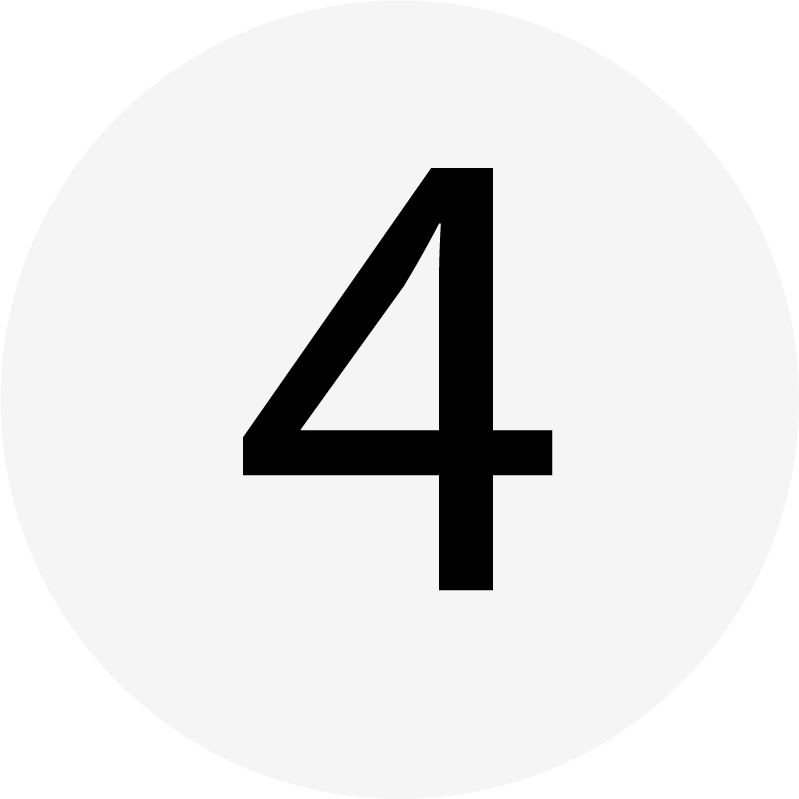
Time and Material
A T&M contract is the best option for a variable set of tasks that are difficult or impossible to establish and assess in advance.
Do you need software development or hardware design for industrial networks?
Drop us a line about your project! We will contact you today or the next business day. All submitted information will be kept confidential.
FAQ
What are the most common protocols used in industrial networks, and what are their advantages and disadvantages?
1) EtherNet/IP is a widely used, open standard that supports real-time control and data exchange.
- Advantages: high-speed, reliable, interoperable.
- Disadvantages: may not be suitable for low-latency applications.
2) Modbus is a widely used, simple and robust protocol.
- Advantages: widely supported, low cost.
- Disadvantages: limited functionality, may not be suitable for high-speed applications.
3) PROFINET is widely used in automation as a fast and reliable protocol.
- Advantages: high-speed, real-time capabilities, standardized.
- Disadvantages: it may be complex to implement; it may not be suitable for small systems.
4) CANbus is widely used in industrial and automotive applications.
- Advantages: low cost, low latency, and highly reliable.
- Disadvantages: limited data capacity, may not support high-speed communication.
5) EtherCAT is a real-time Ethernet-based industrial network protocol.
- Advantages: high-speed, real-time, low latency, flexible topology.
- Disadvantages: limited support compared to other industrial networks; it may be complex to implement.
6) SERCOS III is a real-time communication standard for industrial automation.
- Advantages: high-speed, real-time, deterministic, highly synchronized.
- Disadvantages: it may not be as widely supported as other industrial networks; it may have high implementation costs.
7) CANOpen is widely used as an open communication protocol for industrial automation.
- Advantages: low cost, simple to implement, widely supported, flexible.
- Disadvantages: limited data capacity, it may not support high-speed communication.
What are the challenges of integrating legacy systems into modern industrial networks?
- Compatibility issues between old and new systems.
- Difficulty in integrating diverse protocols and communication standards.
- Lack of real-time capabilities in legacy systems.
- Challenges in upgrading and maintaining old hardware and software.
- Data compatibility and integration issues.
- Cybersecurity risks associated with integrating outdated systems.
- Limited technical expertise and support for legacy systems.
What are the latest trends and developments in industrial network technology?
- Ethernet APL.
- Increased use of wireless and cloud-based data transfers.
- Development of real-time and deterministic industrial Ethernet protocols.
- Greater emphasis on cybersecurity and data privacy.
- Development of open-source and standardized industrial networks.
- Increased use of edge computing and fog computing in industrial automation.
- Adoption of Industry 4.0 and IoT technologies.
How can industrial networks be integrated with other enterprise systems, such as ERP and SCADA?
- Use of standardized communication protocols such as OPC-UA.
- Integration of MES (Manufacturing Execution System) and SCADA.
- Use of middleware and gateway solutions for data transfer and communication.
- Integration of cloud-based platforms and services.
- Use of APIs and web services for data exchange between systems.
- Adoption of open-source software and technologies.
- Implementation of data management and data integration strategies.
How can industrial network security be improved to protect against advanced persistent threats and cyber-attacks?
- Regular software updates and patches.
- External network access restrictions.
- Use of firewall and VPN solutions.
- Local area network of process control systems.
- A well-thought-out choice of wired solutions.
- Implementation of strong authentication and access control measures.
- Encryption of sensitive data and communications.
- Regular monitoring and testing of the network for vulnerabilities.
- Use of intrusion detection and prevention systems.
- Adoption of security best practices.