How to Design Embedded Systems for Harsh Environments: IP Ratings, Conformal Coatings, and Beyond
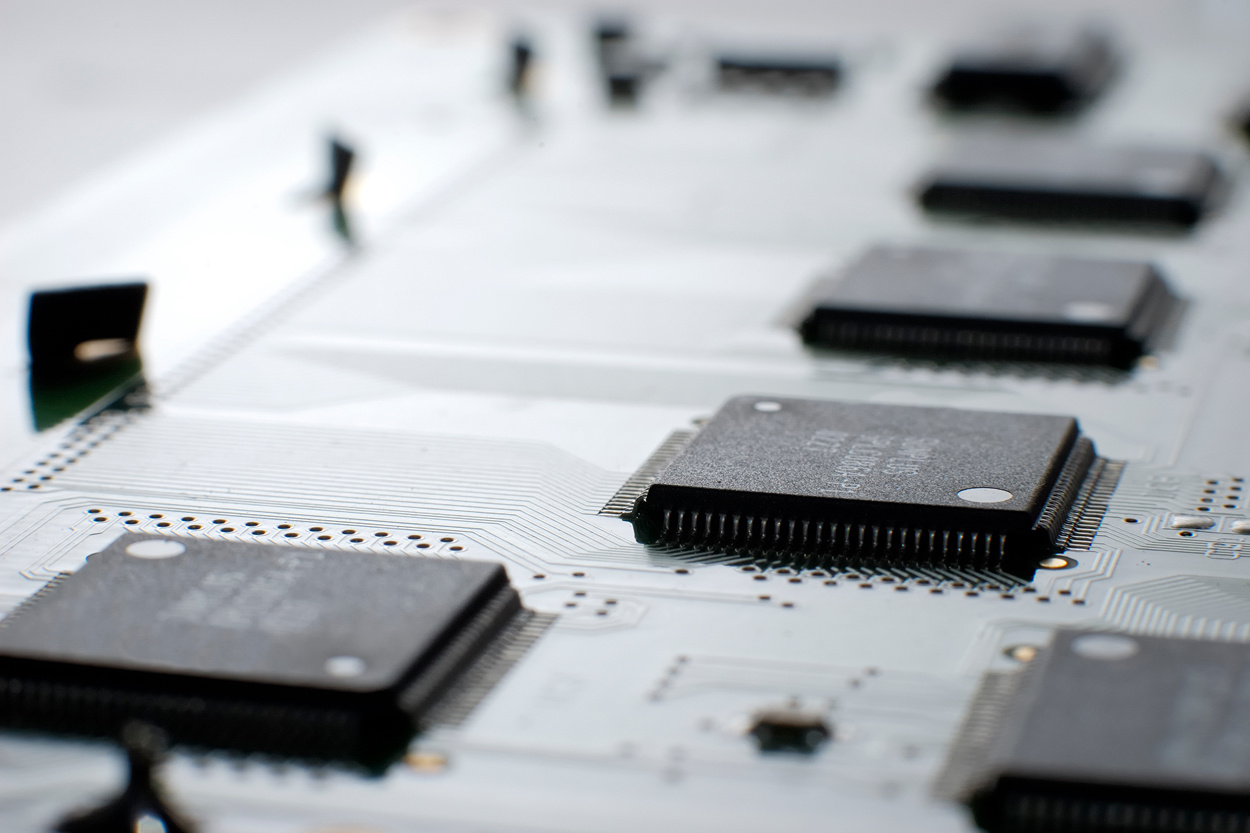
Not all embedded devices live in climate-controlled offices or server rooms. Many operate outdoors in snow or desert heat, inside vibrating heavy machinery, or exposed to chemicals and moisture. Whether it’s a smart sensor on a wind turbine, an ECU in a harvester, or a gateway mounted on an oil rig, designing for harsh environments requires special engineering practices.
In this article, we cover the critical elements of rugged embedded design — from enclosure sealing and conformal coatings to shock, vibration, and thermal management. You’ll learn how to protect electronics so they operate reliably, extend lifecycle costs, and pass demanding qualification tests.
Why Harsh Environment Design is Critical
Failures in the field are costly. They lead to:
- Unplanned downtime in industrial operations
- Expensive on-site repairs or returns
- Safety hazards in automotive or energy systems
- Loss of trust for mission-critical devices
Building for rugged use upfront reduces total cost of ownership, warranty claims, and reputational risks.
Typical Environmental Stress Factors
Temperature Extremes
Devices might see -40°C cold starts or operate above +85°C near engines. Thermal cycles cause material fatigue and stress on solder joints.
Moisture and Corrosive Atmospheres
Outdoor installations face rain, humidity, and salt spray. Chemical plants expose electronics to aggressive gases.
Dust and Particulates
Mining and agriculture generate fine dust that can clog cooling paths or cause conductive bridging on PCBs.
Vibration and Mechanical Shock
Mobile equipment or robotic arms impose constant vibration. Shocks from drops or collisions threaten fragile components.
IP Ratings: Ingress Protection Explained
Code | Solids | Liquids |
IP6X | Dust-tight | |
IPX7 | Immersion to 1m | |
IPX9K | High-pressure wash |
Typical rugged systems target IP65 or higher. This means dust-tight and protected against water jets.
Conformal Coatings and Encapsulation
Conformal Coatings
Thin polymer films (100-300μm) applied over PCBs protect against humidity, salt, and minor contamination.
- Acrylic (AR): Easy to rework, general protection.
- Silicone (SR): Wider temperature, good for outdoor.
- Polyurethane (UR): Resistant to solvents and abrasion.
Potting / Encapsulation
Fully encasing electronics in resin (epoxy, silicone) for maximum protection.
- Improves vibration resistance.
- Blocks moisture completely.
- Harder to inspect or repair.
Thermal Management in Harsh Environments
Conduction Cooling
Use thick metal housings as heat sinks. Mount power components directly on walls.
Forced Convection
Fans or blowers work indoors but often fail outdoors due to dust ingress.
Heat Pipes and Phase Change Materials
Move heat from hotspots to larger surfaces for passive dissipation.
Mechanical Design: Vibration and Shock
PCB Layout Tips
- Keep heavy components low and center.
- Use multiple mounting screws with standoffs.
Potting or Gel-Fill
Dampens vibrations on connectors and solder joints.
Connector Locking
Use positive-locking connectors and strain reliefs to avoid cables shaking loose.
PCB-Level Design for Harsh Conditions
Surface Finishes
ENIG or ENEPIG offer good corrosion resistance compared to bare copper or HASL.
Coating Under Components
Use edge sealing or underfill on BGA to prevent capillary action drawing in moisture.
Wide Trace and Spacing
Reduces risk of conductive dendrite growth under humidity.
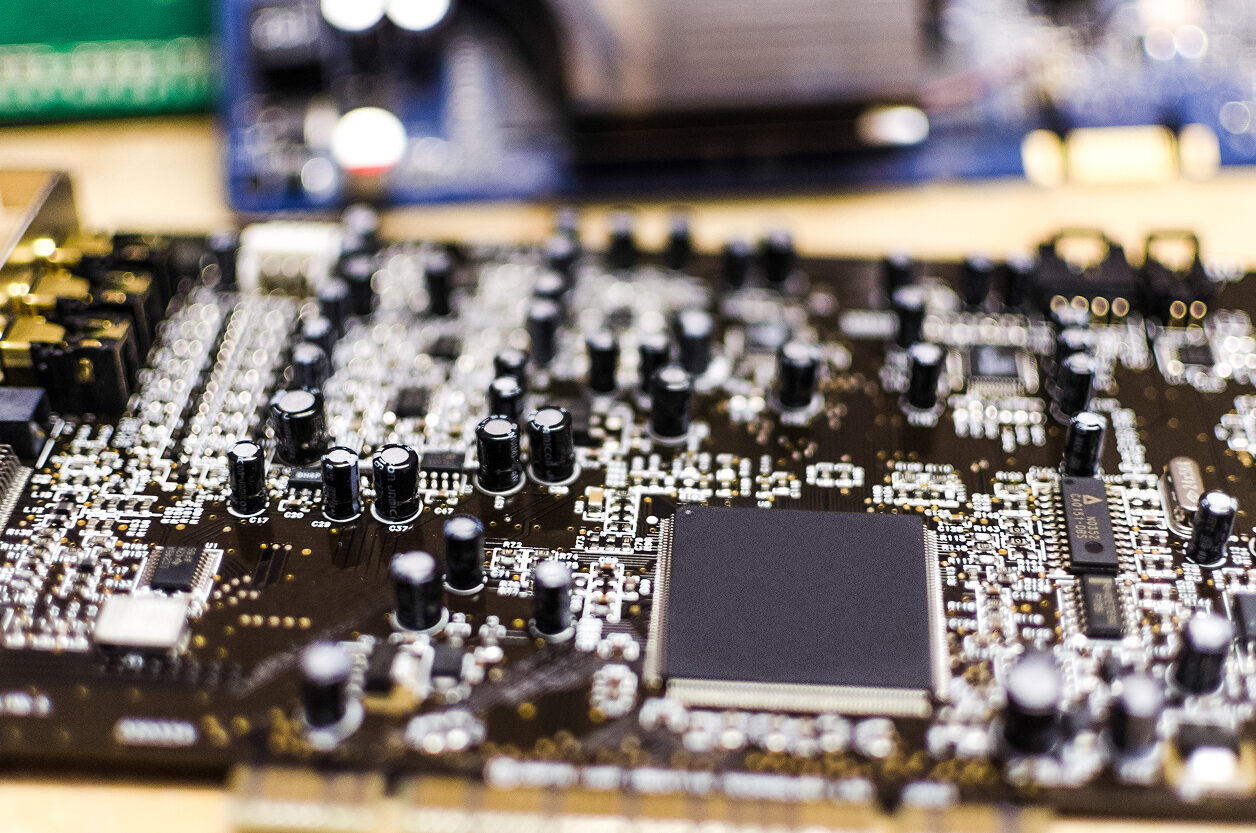
Long-Tail Technical Questions and Answers
What is the difference between IP67 and IP68?
Both are dust-tight (6).
IP67 is protected against immersion up to 1 meter for 30 min.
IP68 allows immersion beyond 1m under conditions specified by the manufacturer.
How does conformal coating protect PCBs?
It forms a moisture barrier, preventing corrosion, short circuits from condensation, and protecting against light chemical exposure.
Can you design for both high vibration and thermal extremes?
Yes, by combining potting for vibration damping with robust thermal paths — like potting compounds with good thermal conductivity.
What testing standards apply?
IEC 60068 for thermal cycling, vibration, and humidity. MIL-STD-810 for military ruggedness tests.
Should you always use potting?
Not necessarily. Potting makes repairs difficult and adds weight. Use it when needed for shock/vibration or full moisture immersion.
Future Trends in Harsh Environment Design
- Nanocoatings: Ultra-thin hydrophobic layers protect PCBs without impacting heat dissipation or weight.
- Smart Monitoring: Embedded sensors tracking internal humidity or strain can predict failures before they occur.
- Advanced materials: Thermally conductive plastics allow lighter enclosures while maintaining heat spreading.
Conclusion: Building Embedded Systems That Last
Designing for harsh environments isn’t just about rugged boxes. It demands an integrated approach:
- Selecting IP-rated enclosures and connectors
- Applying conformal coatings or potting where needed
- Planning robust thermal management
- Choosing materials and PCB finishes that withstand corrosion and stress
At Promwad, we engineer embedded systems that thrive in challenging conditions — from PCB design and thermal modeling to vibration qualification and IP testing. Whether your product needs to survive the tundra, the factory floor, or a combine harvester, we’re ready to help build electronics that last.
Our Case Studies