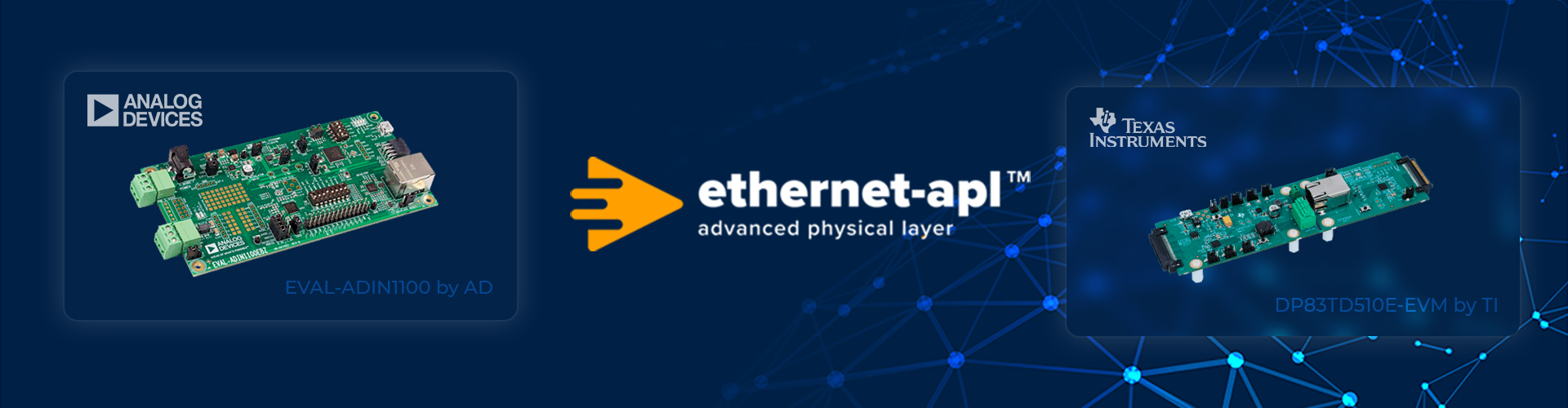
Promwad Implements Ethernet-APL in Client Devices for the Industrial Automation Market
What is Ethernet APL? Ethernet Advanced Physical Layer (Ethernet-APL) is a cutting-edge technology that has quickly become the new standard for building scalable industrial networks. Following major global manufacturers of industrial automation solutions, Promwad implements this technology in new products designed for our customers.
Ethernet-APL can be deployed over distances of up to one kilometre and in hazardous areas. ABB, Siemens, Yokogawa, and other market leaders are beginning to use it in their products. Now device manufacturers can follow this trend with the engineering support of Promwad.
Deploying industrial Ethernet networking solutions in industrial environments brings some challenges: insufficient data transfer rates, distance limitations, and restricted use in hazardous areas. We are helping our customers to overcome these challenges by developing Ethernet-APL-enabled solutions.
Ethernet APL embedded development involves integrating Ethernet-APL technology into embedded systems, specifically for industrial automation and process control. The process includes designing and programming microcontrollers, processors, and other embedded devices to support Ethernet APL.
This integration enables real-time data exchange, device management, and seamless communication within industrial networks. By leveraging Ethernet APL, companies can achieve reliable communication between field devices and control systems, which is essential for maintaining efficient operations in industries such as oil and gas, chemical processing, and manufacturing.
In this article, we describe the features and benefits of the Ethernet-APL technology for industrial networks, which our engineers implement on such evaluation boards as EVAL-ADIN1110 and EVAL-ADIN1100 by Analog Device and DP83TD510E-EVM by Texas Instruments.
Ethernet-APL business benefits
The world's major vendors consider Ethernet-APL to be a new and notable step in process automation. Endress+Hauser, Krohne, Phoenix Contact, Rockwell Automation, SAMSON, Stahl, and Vega are already using this technology in their solutions. By incorporating Ethernet APL software services into their strategy, these companies create more unified and adaptable projects for manufacturing sites, buildings, and even entire smart cities.
The world's major manufacturers consider Ethernet-APL to be a new and important step in process automation. Endress+Hauser, Krohne, Phoenix Contact, Rockwell Automation, SAMSON, Stahl, and Vega are already using this technology in their solutions.
Ethernet-APL is a more unified and scalable automation solution for buildings, manufacturing sites, and entire smart cities, which brings the following benefits to business:
- fieldbus installations that already exist can be deployed again;
- merging with Ethernet-APL eliminates the need for complex and energy-intensive gateways;
- the Ethernet-APL can be used for large mechanisms in spark-dangerous areas and compact spaces;
- automation of processes connected to cloud storage is allowed;
- it is possible to work with a large data set and its analytics.
What is Ethernet-APL
An Ethernet technology's two-wire physical layer is called Ethernet-APL. It is designed for a field level: for industrial process automation systems, direct device and sensor connectivity in dangerous environments. This technology is suitable for industrial Ethernet networks: EtherNet/IP, HART-IP, OPC UA, and PROFINET. They can be used to organise the operation of flow metres, actuators, pressure, and temperature transducers.
Ethernet-APL is an extended Single Pair Ethernet (SPE) specification based on the 10BASE T1L standard and can support higher-bit Ethernet protocols. The advantages of Ethernet-APL versus SPE are detailed in the table below:
| Single Pair Ethernet (SPE) | Ethernet Advanced Physical Layer (Ethernet-APL) |
IEEE Standards supported | 1000BASE T1L, 100BASE T1L,10BASE T1S,10BASE T1L | 10BASE T1L |
Auto-negotiation |
|
|
Energy Efficient Ethernet (EEE) |
|
|
Power over Data Lines (PoDL) |
|
|
Power for Devices | 6 … 60 V, 100 … 1360 mA, max. 60 W | Trunk: typ. 48 V, 92 W |
Cables | IEC 61156 | IEC 61158-2 |
Connectors | IEC 63171 | RJ45, M8, M12, terminals |
Explosion protection concept |
|
|
Source: controlglobal.com
Ethernet-APL technology provides the following features:
- the combined operation of devices from different manufacturers;
- flexible and scalable network topology;
- laying of networks over long distances – up to 1,000 m, and branch lines – up to 200 m;
- amplitude modes: 2.4 V peak for cables up to 1000 meters and 1 V peak for shorter distance cables;
- use in hazardous areas;
- connection of up to 50 field devices — of up to 500 mW each;
- high bandwidth: 10 Mbit/sec;
- data transmission and power supply of the device via the same cable.
Several systems and technologies are directly related to Ethernet-APL and are already in use in industrial automation.
HART-IP in embedded systems is an innovation in industrial communications, combining the traditional HART protocol with modern IP-based networks. These systems enable real-time data exchange between field devices and control applications over a standard Ethernet infrastructure.
Using HART-IP, embedded systems can support higher data rates and longer communication distances. In addition, HART-IP embedded systems offer improved safety features, reliable data transmission, and easy integration into existing networks.
PROFINET in embedded systems are designed for real-time data exchange and control in industrial automation environments. Using the capabilities of Ethernet-based PROFINET technology, these systems provide high-speed, deterministic communication between devices, ensuring synchronisation and reliability of critical operations.
PROFINET is used in many applications, from small factory networks to large, complex industrial plants. It also provides reliable support for motion control, safety, and diagnostics, essential in industrial environments. In addition, PROFINET's compatibility with existing PROFIBUS systems enables simple integration into legacy systems, allowing companies to modernise their production facilities without significant overhauls.
EtherNet/IP embedded technology provides the reliable, high-speed communication required to maintain synchronised operations in complex industrial environments. It supports a wide range of applications, from simple sensor networks to advanced motion control and safety systems, and enables interoperability between devices from different manufacturers through compliance with the CIP (common industrial protocol).
EtherNet/IP's scalability and flexibility make it suitable for new installations and upgrades of existing systems. It supports advanced diagnostics and network management functions, helping to reduce downtime and improve overall system efficiency.
How Promwad uses Ethernet-APL to design client solutions
Ethernet APL embedded services by Promwad are focused on integrating APL of Ethernet into embedded systems to meet the requirements of industrial automation and process control environments. These services include developing and optimising firmware that allows microcontrollers and processors to support Ethernet APL's high-speed, two-wire communication standard.
Other parts of Ethernet APL embedded services include the design and development of IO systems, edge nodes, PLCs (programmable logic controllers), PACs (programmable automation controllers), and distributed IPCs. These steps are necessary to build cohesive, interconnected networks that are flexible to the challenging circumstances frequently seen in industrial settings.
We implement Ethernet-APL technology with single-port evaluation boards and modules from our partners, Analog Devices and Texas Instruments.
The EVAL-ADIN1110 evaluation board by AD
Functional block diagram ADIN1110. Source: analog.com
The EVAL-ADIN1110 is a single-port, low-power, 10BASE-T1L-based evaluation board with the support of IEEE 1588, designed by Analog Devices. It is used for industrial Ethernet applications and complies with the 802.3cg-2019 standard. It is made as the LFCSP chip, and the dimensions are 6 x 6 mm.
The ADIN1110 chip. Source: analog.com
The ADIN1110 has a built-in media access control interface (MAC) that allows you to connect to host controllers via Serial Peripheral Interface (SPI) and use processors with less power.
The board is suitable for intrinsically safe environments, it has a power supply voltage control and a reset system. It operates from a single 1.8V or 3.3V power bus.
The EVAL-ADIN1100 evaluation board by AD
Functional block diagram ADIN1100. Source: analog.com
The EVAL-ADIN1100 is a single-port, low-power (39 mW) evaluation board based on the 10BASE-T1L standard, designed by Analog Devices. It is used for industrial Ethernet applications, meets the 802.3cg-2019 standard, and supports the IEEE 1588 protocol.
The ADIN1100 chip. Source: analog.com
The ADIN1100 chip is integrated with the two-wire MDIO interface that communicates between the host processor/MAC and ADIN1100. The MDIO interface provides access to the following components and functions of the Ethernet PHY core integrated with ADIN1100:
- analogue circuits,
- buffering and control of the input and output clock pulses,
- interface control register, subsystem registers,
- MAC interface,
- clock pulse control,
- output configuration.
The operation of the chip can be provided by a single 1.8V or 3.3V power bus. The board has a built-in supply voltage monitoring and a resetting system to be suitable for use in intrinsically safe environments.
Where we use ADIN1110 & ADIN1100
We use the ADIN1110 and ADIN1100 chips in Ethernet APL firmware development to design IO-systems sensors, edge nodes, PLCs, PACs, distributed IPCs, DAQs, gas meters, and flow meters for our clients.
The DP83TD510E-EVM evaluation module by TI
Evaluation module DP83TD510E-EVM. Source: ti.com
The DP83TD510E-EVM is an evaluation module designed by Texas Instruments, compliant with 10Base-T1L IEEE 802.3cg. It has low power consumption and a long range. It supports 10BASE-TX Ethernet and ensures fast implementation thanks to the DP83822 chip.
The built-in USB-MDIO graphical user interface tools are responsible for the PHY register setup.
The DP83TD510E board is used for developing all kinds of sensors and actuators, such as shut-off valves, diaphragms, electric motors, etc.
+++
Ethernet-APL is an emerging technology that advances industrial automation technologies in the future. . It brings such advantages as high data transmission speed, intrinsic safety, range, and ease of deployment.
Promwad offers Ethernet APL embedded consulting and designs solutions based on this cutting-edge technology. Our expertise includes developing APL field switches, APL power switches with ADIN1110 and ADIN1100 by Analog Devices, and DP83TD510E by Texas Instruments.
If you need help in designing a device for industrial automation with the Ethernet-APL technology, don't hesitate to get in touch with us: we are ready to undertake turnkey development or individual engineering tasks in hardware design, software development, or production launch!
Our projects