Top 7 Mistakes in Hardware Product Scaling — and How to Avoid Them
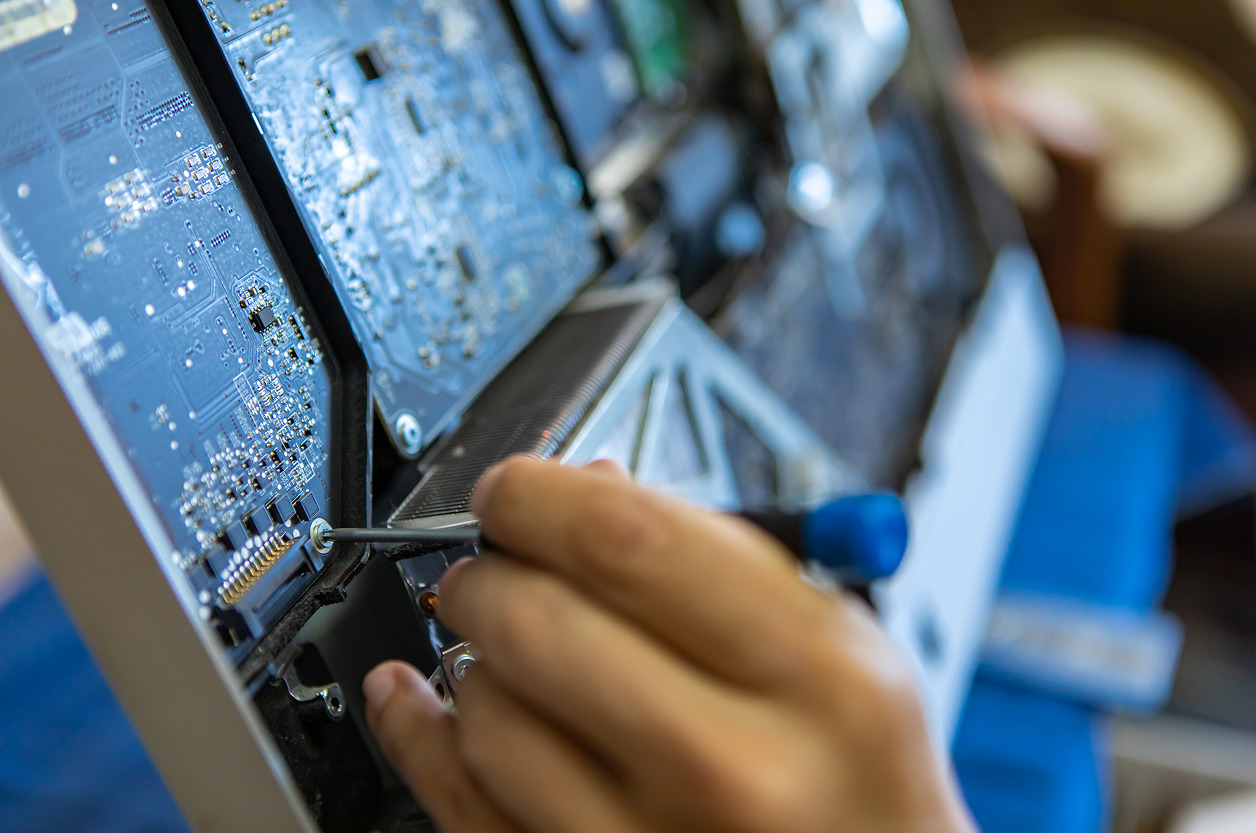
Getting Started: Why Scaling Hardware Is Harder Than It Looks
Scaling a hardware product from prototype to mass production isn’t just about increasing volume — it’s about rethinking processes, partnerships, compliance, and risk. Many companies underestimate the complexity, and even small oversights at the scaling stage can lead to huge delays, quality issues, or missed market opportunities.
In this guide, we highlight seven of the most common mistakes companies make when scaling hardware — and how you can avoid them to ensure your product evolves into a reliable, manufacturable, and competitive solution.
Mistake 1: Skipping DFM and DFT Reviews
The Problem:
Companies move from working prototypes to production without validating for manufacturability (DFM) and testability (DFT).
Consequences:
- Assembly issues on SMT lines
- Low test coverage, hard-to-detect defects
- Increased NPI costs and yield loss
How to Avoid It:
- Involve EMS experts early for DFM/DFT reviews
- Use PCB design rules for production lines
- Design test points and functional diagnostics into early revisions
Mistake 2: Underestimating the Need for Pre-Certification Testing
The Problem:
Teams assume that compliance testing (EMC, safety, RF) will be a final step that “just works.”
Consequences:
- Failed certification tests
- Costly redesigns and time-to-market delays
- Lost confidence from investors or customers
How to Avoid It:
- Plan for pre-compliance testing as part of your MVP phase
- Work with labs that offer pre-scan or advisory sessions
- Design with regional requirements in mind (CE, FCC, IC, UKCA, etc.)
Mistake 3: BOM Optimization Is an Afterthought
The Problem:
The bill of materials (BOM) that works for 100 prototypes may not scale to 10,000 units.
Consequences:
- Long lead times and component shortages
- Price fluctuations due to poor sourcing
- Supply chain fragility
How to Avoid It:
- Create a sourcing strategy for scale (multi-vendor, LTB monitoring, parametric matching)
- Approve alternates for critical parts
- Use lifecycle and availability databases like SiliconExpert or Octopart
Mistake 4: No Clear Transition Plan Between Prototyping and EMS
The Problem:
Engineering teams hand off late-stage designs to EMS providers without documentation, validation plans, or production expectations.
Consequences:
- Friction during onboarding
- Conflicting assumptions about testing and QA
- Delays in production ramp-up
How to Avoid It:
- Build a complete transfer package (BOM, CAD, test plans, firmware, mechanicals)
- Pilot builds with supervision and fixture validation
- Assign a project owner for EMS coordination
Mistake 5: Poor Test Strategy for Scaling
The Problem:
Relying on manual testing or incomplete test coverage doesn’t scale with volume.
Consequences:
- Bottlenecks during production
- Low first-pass yield rates
- Inconsistent quality across units
How to Avoid It:
- Design automated functional and end-of-line test setups
- Align test protocols with expected batch sizes and geographies
- Plan fixture development early with EMS partners
Mistake 6: Ignoring Field Service and OTA Infrastructure
The Problem:
Product teams focus on launch but neglect what happens after deployment.
Consequences:
- Expensive field recalls or returns
- Inability to fix bugs or update security
- Reduced product lifetime and ROI
How to Avoid It:
- Implement OTA-ready firmware architecture
- Design secure boot and firmware rollback mechanisms
- Include diagnostics and remote logging options from the start
Mistake 7: Not Thinking Globally from the Start
The Problem:
Products are designed for a single market and then rushed into new regions without adaptation.
Consequences:
- Compliance gaps (voltage, RF bands, documentation)
- Logistics inefficiencies and packaging problems
- Lost opportunities in international scaling
How to Avoid It:
- Design for modularity and localization
- Create a roadmap for global certifications and label formats
- Involve international partners early in product testing and feedback
Mistake | Consequences | Prevention Strategy |
Skipping DFM/DFT | Yield loss, rework | Early design reviews with EMS |
No pre-certification testing | Redesign delays | EMC/RF pre-testing and design reviews |
BOM not optimized for scale | Supply chain risk | Multi-vendor sourcing strategy |
Poor EMS transition planning | Delays, miscommunication | Full transfer packages and pilot builds |
Incomplete test strategy | Low quality, bottlenecks | Scalable, automated test development |
No OTA or diagnostics | Post-launch failures | Firmware infrastructure from day one |
Lack of global readiness | Compliance gaps, market limitations | Modular, compliant, internationally tested design |
Promwad’s Role in Scalable Hardware Development
At Promwad, we help companies grow from idea to global production through:
- EMS onboarding and BOM lifecycle strategy
- DFM/DFT reviews and transfer package preparation
- Certification planning and lab partnerships
- Embedded software with OTA and diagnostics
- Scalable test fixture development
We don’t just help you launch — we help you scale right.
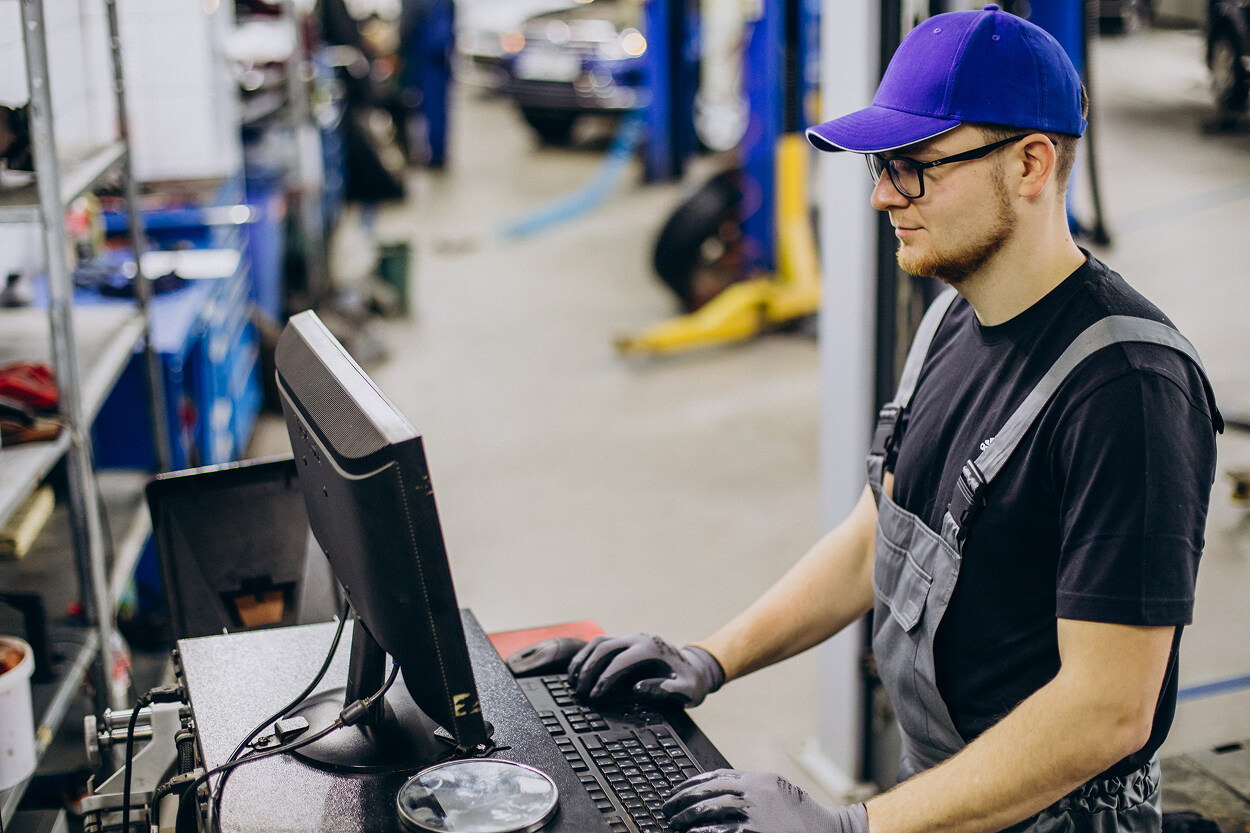
Real-World Case Study: Scaling an Industrial Sensor Platform
A German industrial automation company partnered with Promwad to scale their predictive maintenance sensor platform from pilot installations to full-scale deployment across three continents.
Challenges:
- Multiple SKU variants for different voltage and communication standards (LoRa, NB-IoT, Zigbee)
- Compliance with EU, North American, and APAC regulations
- Component shortages and long lead times during scaling
Promwad’s Approach:
- Performed DFM/DFT reviews to align PCBA design with EMS partner in Lithuania
- Implemented OTA update support for firmware upgrades and diagnostic logging
- Developed a universal test fixture with interchangeable modules for different regional variants
- Introduced BOM lifecycle tracking with automated alerts for EOL components
Outcomes:
- Time-to-market reduced by 28% despite supply chain disruptions
- First-pass yield stabilized at 98.3% after pilot run refinements
- All three regional product versions passed EMC and safety certifications on the first attempt
Final Thoughts: Scaling Is a Discipline, Not a Leap
Avoiding common scaling mistakes isn’t about perfection — it’s about foresight. The companies that grow best in 2025 are those that treat scaling as a process, not just a goal.
With the right strategy, the right partners, and the right tools, your prototype can become a product line — fast, repeatable, and reliable.
Our Case Studies in Hardware Design