How to Reduce Time-to-Market in Hardware Projects: From Design to Mass Production
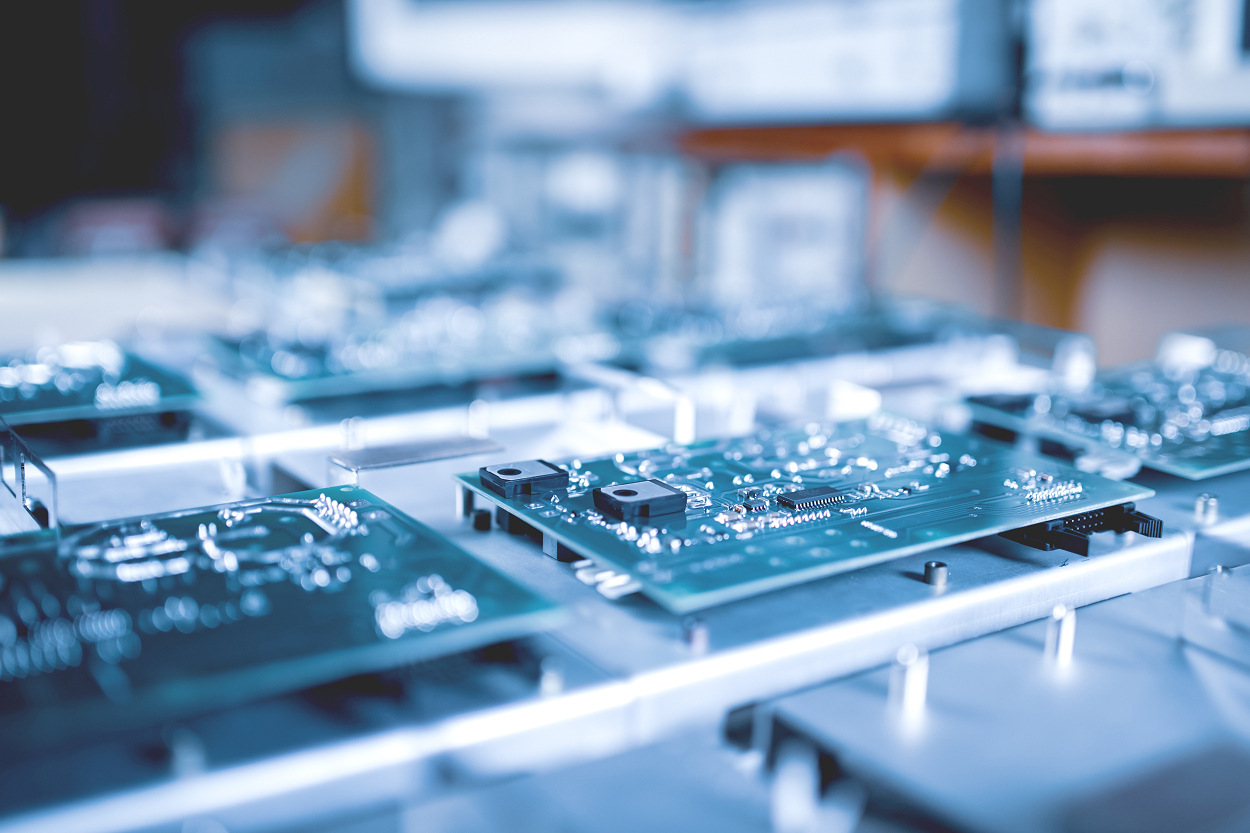
Why Time-to-Market Matters in Hardware
In fast-moving industries, speed is a competitive advantage. Getting your electronics product to market faster means:
- Capturing customer demand before competitors
- Responding to regulatory or seasonal windows
- Iterating based on user feedback faster
- Securing early revenue and investor confidence
Yet in hardware development, time-to-market is often delayed by fragmented processes, poor planning, and supply chain bottlenecks. This guide shows how to compress lead times at every stage, from concept to full production.
1. Align Design with Manufacturing from Day One
The earlier you consider manufacturing constraints in your product design, the fewer redesigns you'll need later. This is where Design for Manufacturing (DFM), Design for Assembly (DFA), and Design for Testability (DFT) come in.
Key actions:
- Run DFM checks before finalizing the PCB layout
- Involve EMS partners or manufacturing experts during schematic design
- Validate component availability and obsolescence status
- Prepare test points and diagnostic access in early revisions
2. Use Modular and Reusable Design Blocks
Reusing verified modules—such as power management, RF, or sensor subsystems—can eliminate design cycles and reduce risk.
Advantages:
- Shorter development time
- Fewer unknowns in integration and certification
- Easier updates and future versions
3. Prototype Quickly — and Intelligently
Rapid prototyping is essential but should be goal-driven. Instead of building full-featured prototypes too early, focus on validating critical functions.
Best practices:
- Use evaluation boards for early firmware development
- Employ 3D-printed enclosures to test form factor and ergonomics
- Conduct parallel hardware and firmware iterations
4. Streamline Component Sourcing Early
Component shortages can derail entire project timelines. Engage with EMS providers or supply chain consultants early to forecast risks and plan mitigation strategies.
Tips:
- Use real-time databases to check lead times and lifecycle status
- Approve alternates for key components
- Choose EMS partners with strong sourcing networks
5. Choose the Right EMS Partner
A contract manufacturer who is involved early can reduce onboarding friction, validate manufacturability, and accelerate ramp-up.
Look for:
- NPI (New Product Introduction) experience
- Engineering support, not just assembly
- Flexibility to scale from small batches to mass production
6. Automate Testing and Validation
Manual testing slows down production and introduces inconsistencies. Automated test setups speed up time-to-market and improve quality.
Include in your plan:
- Boundary scan testing or JTAG for complex boards
- Functional testers tailored to your application
- End-of-line testing strategies for production
7. Run a Pilot Build Before Mass Production
A pilot run helps identify real-world manufacturing issues in a controlled, lower-volume setting.
Pilot build benefits:
- Catch yield problems early
- Validate test procedures and logistics
- Fine-tune manufacturing documentation
Timeline Optimization Table
Development Stage | Typical Duration | With Optimizations |
Concept & Architecture | 2–4 weeks | 1–2 weeks |
Schematic + PCB Layout | 4–6 weeks | 2–4 weeks with DFM |
Prototype & Testing | 6–8 weeks | 3–5 weeks (iterative) |
Sourcing & EMS Onboarding | 4–6 weeks | 2–3 weeks with support |
Pilot Build | 3–4 weeks | 2 weeks |
Mass Production Launch | 4+ weeks | 2–3 weeks ramp-up |
8. Leverage Digital Twins and Simulation Tools
Digital prototyping is gaining popularity as a way to detect issues before the first board is manufactured. Tools such as Siemens PADS, Altium Designer, and Ansys allow early-stage simulation of thermal, electrical, and mechanical performance.
Benefits:
- Reduce the number of physical prototypes
- Shorten design cycles with virtual testing
- Improve reliability before production
9. Integrate Agile Methodologies in Hardware Projects
While agile practices originated in software, they are now being adapted for hardware development. Agile hardware means faster iteration, smaller releases, and closer collaboration between engineering and manufacturing.
Key points:
- Use sprints to structure prototyping cycles
- Employ Kanban boards to track sourcing and design tasks
- Maintain a backlog of feature requests and validation issues
10. Track Project Health with Real-Time Dashboards
Modern product development tools like Jira, Monday, or even dedicated PLM systems offer dashboard views that help stakeholders monitor timelines, risks, and resource allocation.
Why it matters:
- Identify bottlenecks before they escalate
- Improve communication across distributed teams
- Enable data-driven decision-making
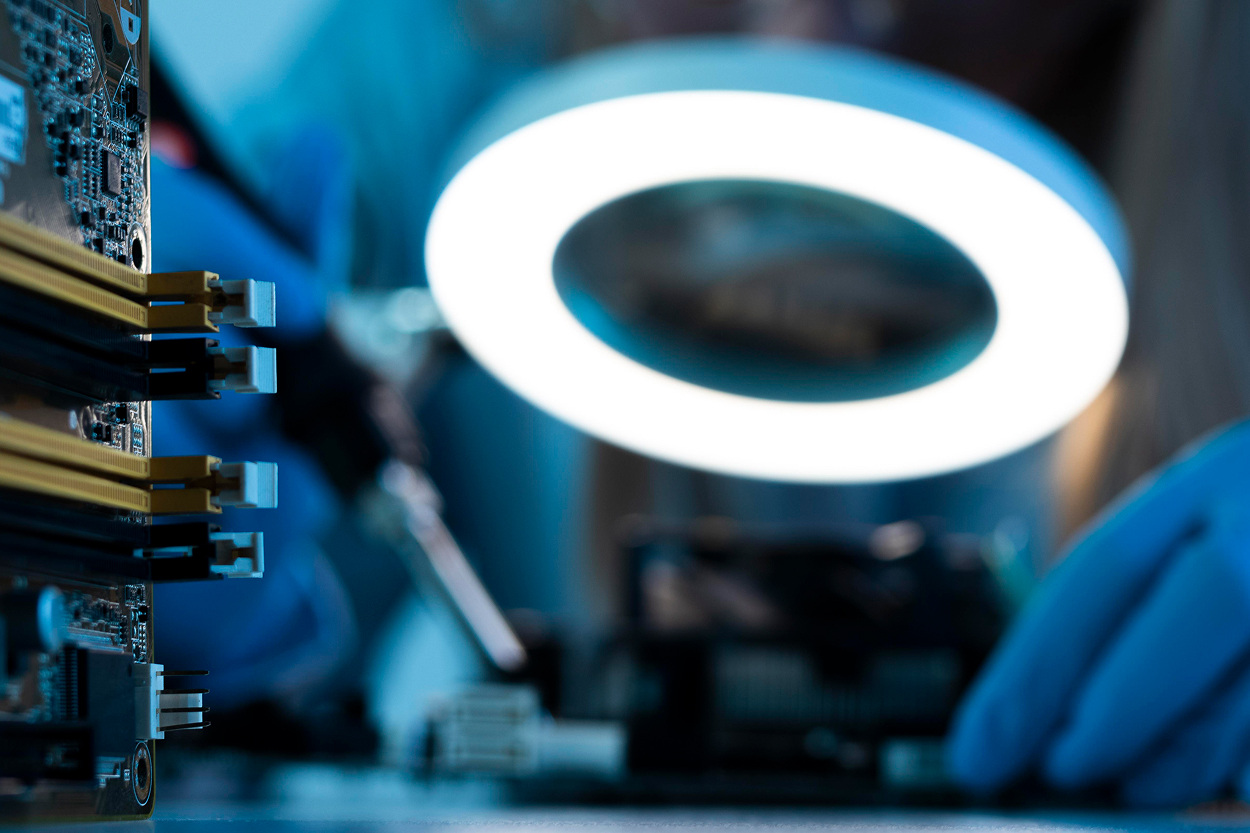
Promwad’s Role in Accelerating Time-to-Market
At Promwad, we help clients reduce development cycles through:
- DFM/DFT analysis from day one
- Reusable IP blocks and proven reference designs
- EMS onboarding and documentation handover
- Test system development and pilot supervision
Our cross-functional teams bridge design and production to keep your project moving — fast and smart.
Industry Outlook: Why Speed Will Define Winners in Hardware
According to a 2024 report by McKinsey, companies that lead in hardware innovation cycles are twice as likely to become market leaders within their niche. Time-to-market is increasingly correlated with customer retention, especially in consumer electronics, automotive, and smart devices.
Emerging technologies such as RISC-V SoCs, edge AI modules, and advanced wireless chipsets often have short adoption cycles — speed gives you the edge to be early.
Final Thoughts: Move Fast Without Breaking Things
Reducing time-to-market in electronics projects isn’t about rushing — it’s about removing friction. With the right approach to design, prototyping, sourcing, and manufacturing, you can deliver products faster while maintaining quality and scalability.
Let Promwad help you shorten the path from concept to production — without cutting corners.
Our Case Studies in Hardware Design