How Vibration and Shock Simulation Reduces Iterations in Hardware Design
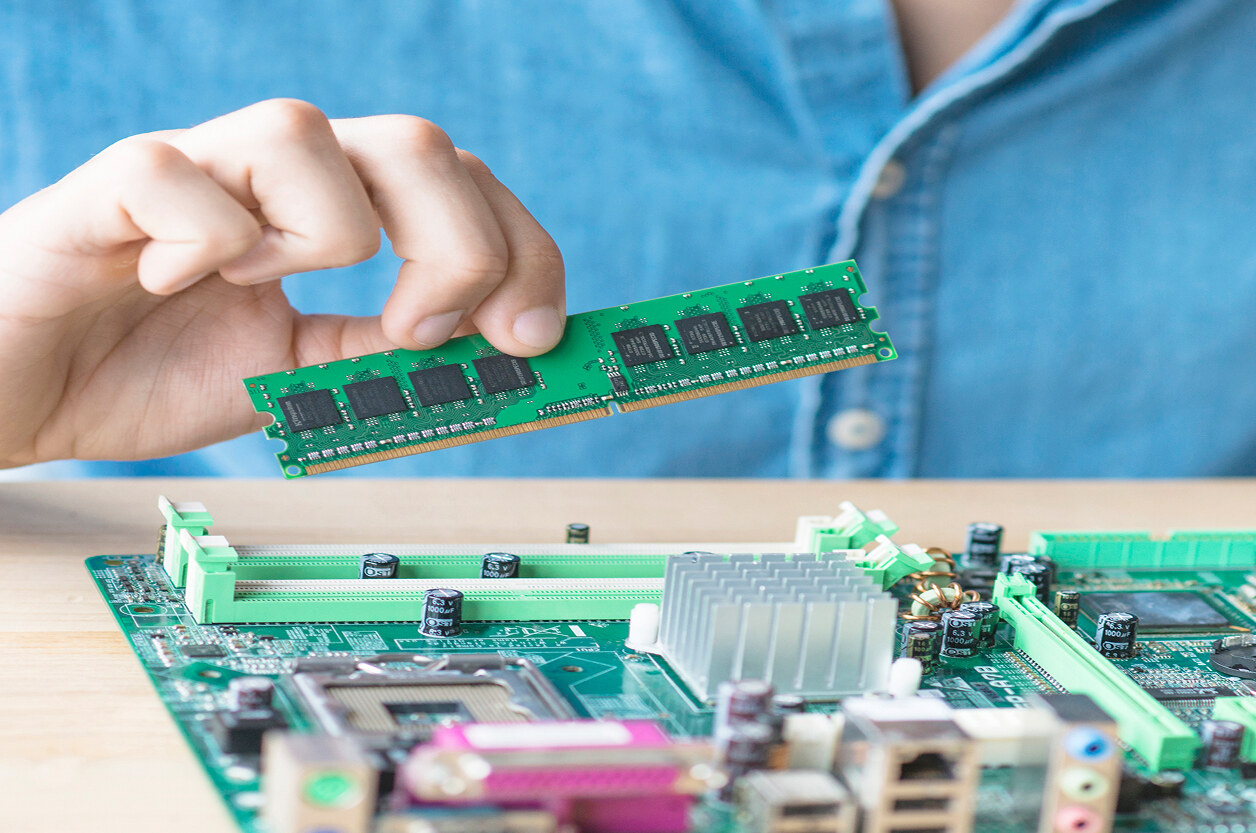
Why Simulating Mechanical Stress Saves Time and Money
In the development of industrial, automotive, and aerospace electronics, mechanical durability is not optional. Devices are exposed to drops, vibrations, impacts, and harsh motion — and failing a qualification test late in development often means costly redesigns and missed launch dates.
That's where vibration and shock simulations come in. These virtual tests replicate real-world mechanical stress, helping teams identify design weaknesses before they commit to physical prototypes. In this article, we’ll explain how they work, where they fit in the development cycle, and how they reduce the number of iterations required to reach a robust design.
What Are Vibration and Shock Simulations?
These simulations are part of finite element analysis (FEA) techniques that use CAD models to predict how an enclosure, PCB, or mechanical assembly will behave under mechanical stress.
Types of Simulations:
- Random Vibration – simulates road, flight, or machinery-induced motion
- Sine Sweep – for resonance detection and modal analysis
- Mechanical Shock – replicates drop tests or collision forces
- Combined Environmental Loads – vibration + thermal + pressure
They can be applied to:
- Enclosures and mounts
- PCB assemblies (rigid/flexible)
- Sockets, fasteners, and connectors
- Battery packs and internal brackets
Benefits of Simulation-Led Design
Benefit | Impact on Development |
Fewer physical prototypes | Less money spent on testing iterations |
Predict early failures | Identify weak joints, resonances |
Improve test pass rates | Higher chance of first-time qualification |
Reduce mass and material | Optimize without overengineering |
Accelerate compliance process | Confidence in MIL-STD, ISO, IEC standards |
Typical Simulation Workflow at Promwad
- Modeling and Material Definition: Import STEP/IGES files from CAD tools (SolidWorks, Fusion 360, Altium CoDesigner); define plastic, metal, rubber, and PCB stack-up properties
- Boundary Conditions and Constraints: Mounting points, clamp zones, screw torque, damping layers
- Load Profile Selection: Realistic profiles based on product usage (e.g., ISO 16750-3, MIL-STD-810G)
- Simulation Runs: Modal analysis, stress/strain contours, frequency sweeps, displacement graphs
- Interpretation and Redesign: Reinforce ribs, relocate mounting holes, add damping
Iterate before cutting prototypes
Simulation vs Physical Testing
Aspect | Simulation Only | Physical Only | Combined Approach (Best) |
Cost | Low per iteration | High (fixtures, samples, lab time) | Balanced |
Time | Hours to days | Days to weeks | Optimized |
Failure Insight | Visual data on weak points | Pass/fail with root cause analysis | Validation + optimization |
Certification Coverage | Early indicator only | Needed for compliance | Design confidence + documentation |
Real-World Use Cases
- Automotive Gateway
Problem: PCB cracked near mounting hole after vibration testing
Solution: FEA showed stress concentration → added fillet + isolation grommet
Result: Passed ISO 16750-3 on next test round - Ruggedized Sensor Node
Enclosure resonance near 250 Hz
Design modified to shift resonance above operational range
Avoided use of heavier materials
Common Standards Covered by Simulation
Standard | Application Domain |
ISO 16750 | Automotive electronics |
MIL-STD-810 | Military-grade equipment |
IEC 60068-2-27 | Shock tests for industrial hardware |
IEC 60068-2-64 | Random vibration |
ISTA / ASTM | Drop and transport packaging tests |
Simulations align with these standards to reduce surprises during lab testing.
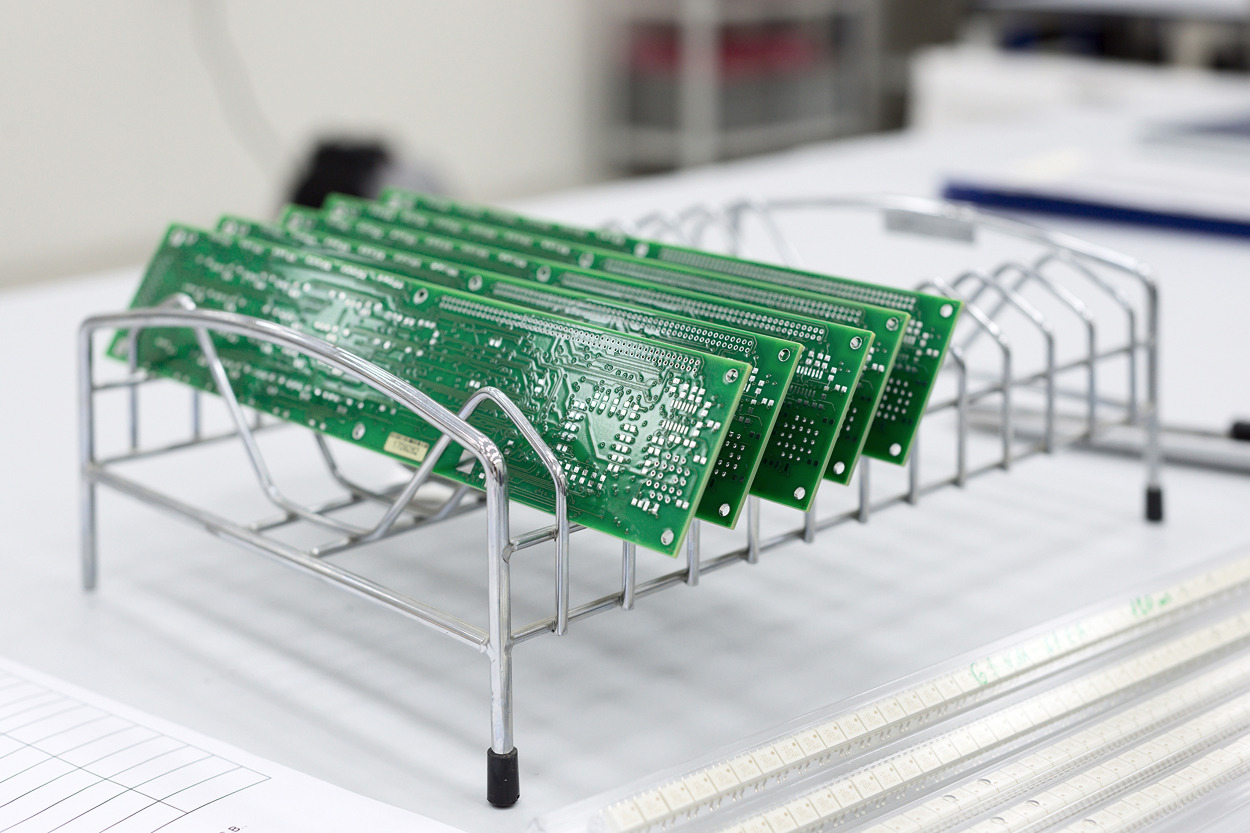
Design Tips for Better Vibration Tolerance
- Avoid mounting heavy components near unsupported PCB edges
- Use multiple mounting points to distribute load
- Isolate sensitive modules with rubber grommets or foam
- Simulate screw pull-out and torque-induced deformation
- Ensure cables and connectors don’t transmit vibration
Good mechanical design starts with an understanding of the environments the device will face.
Final Thoughts
You don’t need to wait for your product to fail in the lab (or in the field) to fix mechanical weaknesses. With simulation-driven hardware development, you can validate assumptions early, reduce physical prototyping costs, and pass certifications faster.
Promwad helps companies integrate FEA-based mechanical simulation into their electronics development workflows — so they build stronger, smarter, and safer products.
Let’s simulate your way to first-time-right hardware.
Our Case Studies in Hardware Design