Wireless Charging for Embedded Devices: Coil Design, Power Management, and Thermal Constraints
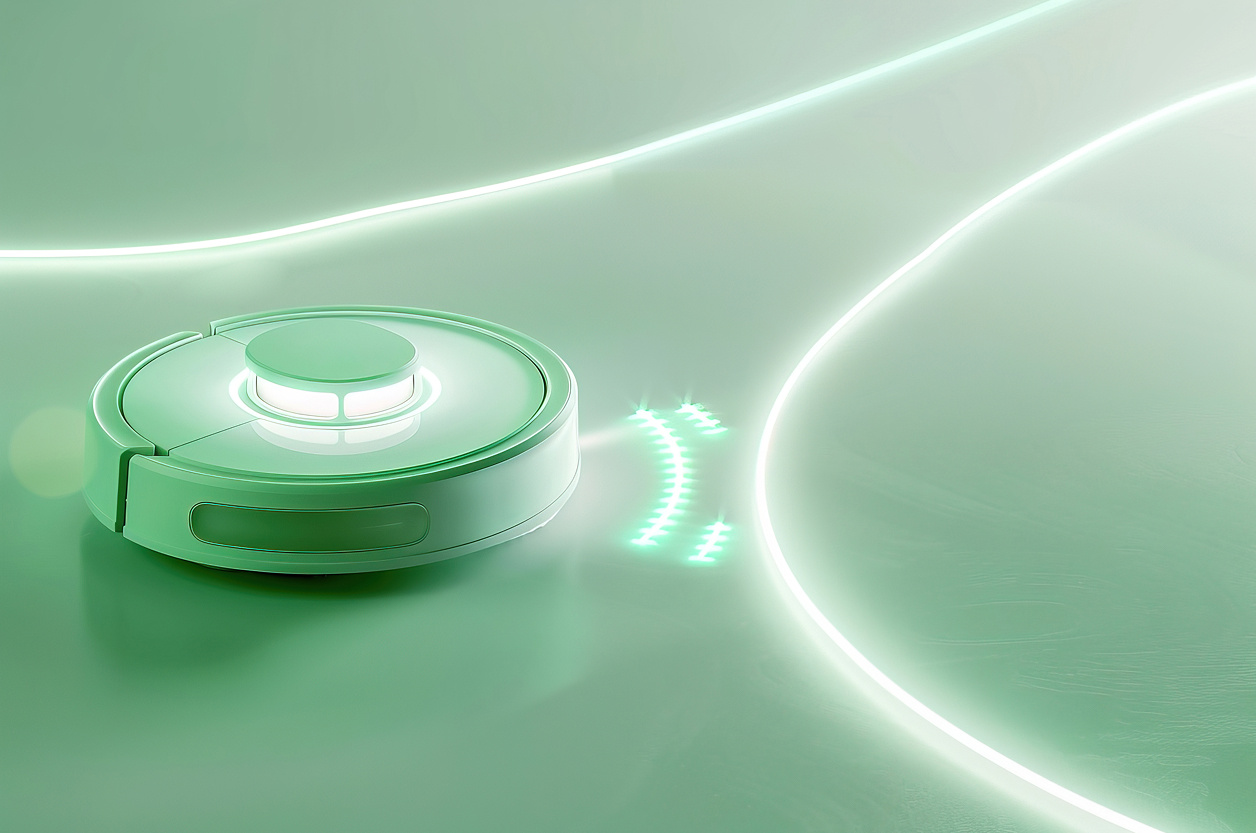
Wireless charging is no longer reserved for flagship smartphones. Today, it’s increasingly found in embedded systems — from industrial sensors and medical implants to consumer wearables and drones. Eliminating physical connectors not only enables sleeker designs but also improves reliability in harsh or moving environments by avoiding contact wear and exposure to dust or water.
However, integrating wireless power into embedded products is far from straightforward. Engineers must carefully balance coil geometry, frequency tuning, power transfer efficiency, and thermal effects, all under tight space constraints.
This article dives deep into how to design wireless charging systems for embedded devices, covering key trade-offs, practical engineering approaches, and future trends.
Why Embedded Products Are Moving to Wireless Power
Mechanical Reliability
Connectors are common failure points. In vibrating or rotating systems, maintaining good electrical contact is difficult. Wireless power completely sidesteps connector fatigue.
Environmental Protection
Enclosed, sealed devices become easier to achieve high IP ratings (IP67+), crucial for outdoor sensors or industrial applications.
User Experience and Miniaturization
In wearables or consumer gadgets, removing charging ports allows thinner enclosures and waterproofing without extra seals.
Basic Principles of Wireless Power Transfer
Wireless charging relies on inductive coupling. A transmitter (Tx) coil in the charging pad creates an alternating magnetic field. A receiver (Rx) coil in the device captures this field, inducing current.
Most systems operate at 100-300 kHz for short-range power (Qi standard). For implanted or specialized industrial applications, lower MHz frequencies are sometimes used.
A resonant circuit on both Tx and Rx sides maximizes energy transfer by matching the coil’s natural frequency to the driving frequency.
Coil Design for Embedded Devices
Coil Shape and Size
Flat spiral coils are common for slim designs like wearables. Solenoid-style coils can be used in cylindrical sensors. Coil diameter and number of turns dictate coupling efficiency. More turns increase inductance but also height.
Litz Wire vs. Solid Wire
Litz wire minimizes skin effect losses at high frequencies, improving efficiency especially above 100 kHz.
Shielding and Ferrites
Metal parts nearby can cause eddy current losses. Ferrite sheets under coils focus magnetic fields, reduce EMI into neighboring circuits, and improve coupling factor (k).
Power Electronics and Regulation
AC to DC Rectification
The Rx coil produces AC voltage. It’s rectified (often by synchronous rectifiers for better efficiency) and regulated to a stable DC voltage. Typical embedded designs use DC-DC converters after rectification to supply internal rails (3.3V, 1.8V).
Feedback and Communication
Most systems use low-speed communication from Rx to Tx to adjust power levels (modulation by load variation or dedicated protocols like Qi BPSK).
Power Range
- Wearables: 0.1 - 1 W
- IoT sensors: 1 - 5 W
- Light industrial tools: up to 20 W
Thermal Constraints: The Hidden Challenge
Heat from Eddy Currents
Metal chassis or battery packs under coils can absorb magnetic energy, heating up. Design must minimize metal directly behind Rx coils or use ferrites.
Losses in Rectifiers
At low loads, diode forward voltage is a significant percentage of total voltage, causing heat. Synchronous FET rectifiers help.
Overall Thermal Design
Use copper pours under charging ICs to spread heat. Model heat rise in CFD tools when placing Rx near batteries.
Long-Tail Technical Questions and Engineering Answers
How do you size the coil for a 5W wireless charger?
It typically needs an Rx coil around 25-35 mm in diameter. Number of turns balances inductance (~6-10 uH) with coil resistance. Use a simulation tool to tune for your target frequency and coupling distance.
Can you do wireless charging through metal?
Not directly. Metal blocks magnetic fields. Some solutions use clever flux-guiding slots or very thin aluminum to allow partial coupling, but efficiency drops significantly.
What’s the typical efficiency of wireless charging vs wired?
Wired charging might be 90-95%. Well-designed wireless links achieve 75-85% at short distances, dropping sharply with misalignment.
How do you prevent EMI affecting nearby circuits?
Use ferrites to contain fields. Implement frequency hopping or spread-spectrum driving to reduce peaks. Place sensitive analog circuits away from Rx coils.
Can low-frequency (LF) systems reduce heating?
Yes — 125 kHz systems generate less eddy current heating than MHz systems, but at the cost of needing larger coils for the same power.
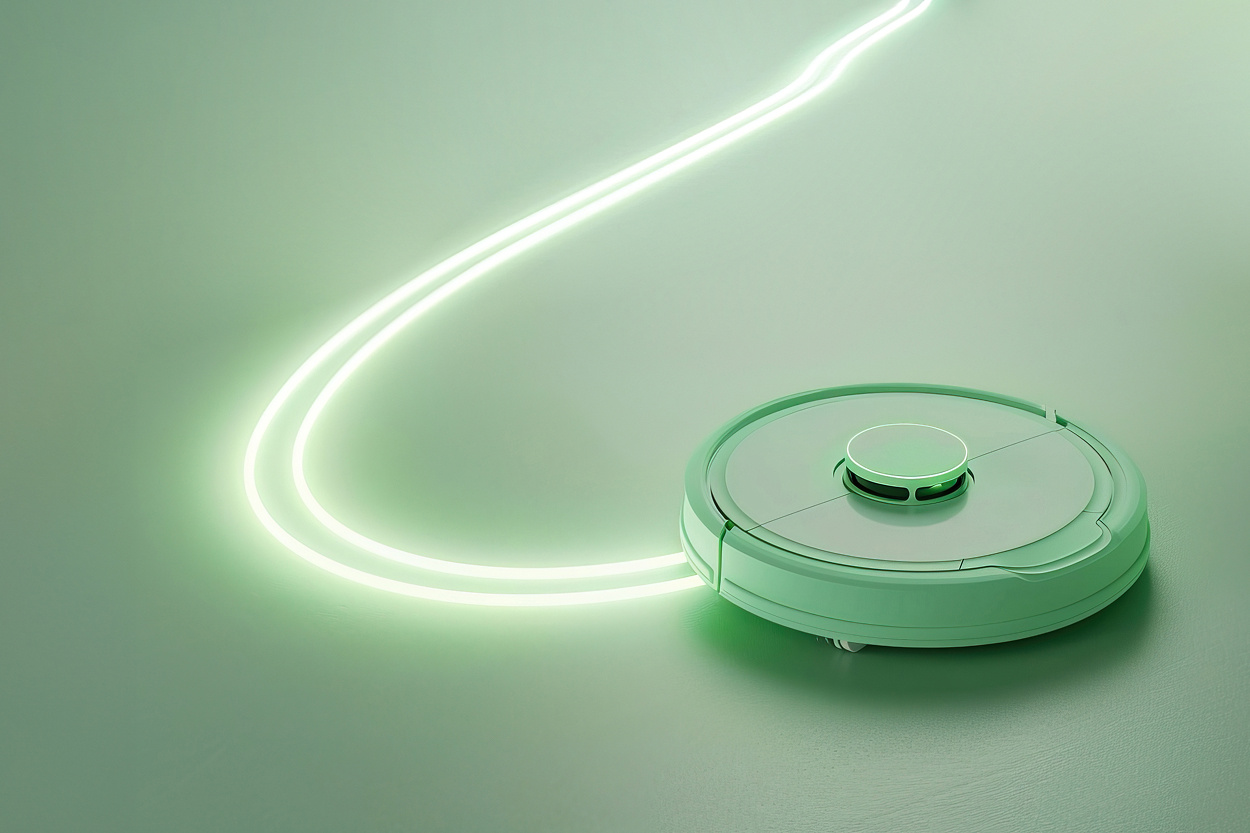
EMI and Regulatory Considerations
Wireless chargers emit strong magnetic fields. Designers must:
- Pass FCC / CE EMI standards (EN 55011, EN 55032).
- Implement sniffing or polling to avoid continuously driving power when no valid Rx is present.
- Ensure foreign object detection (FOD) to shut down if a stray metal piece causes unexpected heating.
Practical Example: A Rugged Sensor Node
Imagine retrofitting an industrial vibration sensor for wireless charging:
- Use a robust Rx coil glued inside a polymer casing, with a ferrite layer underneath.
- Place DC-DC after the bridge to regulate to 3.6V Li-Ion charging.
- Integrate a small MCU that negotiates power levels and periodically checks coil temperature via NTC.
This avoids connector failures from dust ingress on rotating shafts while allowing overnight charging during maintenance stops.
Future Directions in Wireless Power for Embedded
Resonant multi-coil systems: Improve misalignment tolerance, enabling free placement on charging pads.
Combining data and power: Inductive links can also carry serial data, eliminating the need for separate radios in very short-range setups.
Smarter charging ICs: Integrated FOD, thermal throttling, and dynamic frequency adjustments to adapt to nearby materials.
Conclusion: Integrating Wireless Power into Embedded Products
Wireless charging provides enormous benefits in mechanical reliability and design flexibility for embedded devices. But success depends on careful engineering across disciplines: coil design, power electronics, thermal analysis, and EMI control.
At Promwad, we help companies bring wireless power into embedded products — from coil geometry optimization to firmware-level negotiation protocols. If your next device needs to charge without wires, we’re ready to help engineer it from concept through to compliant production.
Our Case Studies