Universal Nvidia Robotics Platform with Industrial Networking Support
Project in Nutshell: Promwad initiated the development of the first-of-its-kind universal platform for robotics based on Nvidia Jetson / Orin with the support of popular protocols for industrial networks, such as EtherCAT, PROFINET, and EtherNet/IP.
With this platform powered by the Hilscher netX communication controller, manufacturers can use popular modules and ready-made servo drives with all kinds of industrial and consumer robots without any additional solutions.
Challenge
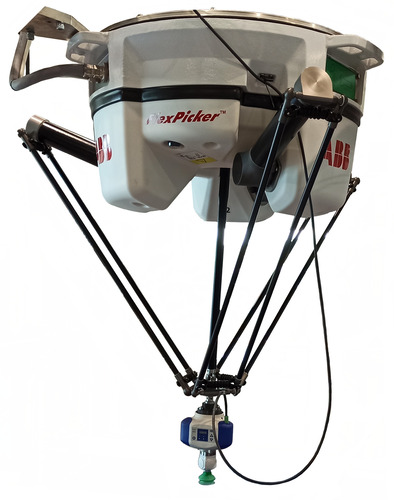
Delta robot FlexPicker by ABB. A similar custom solution can be built on the universal platform created by Promwad. Source: Marc Auledas, Wikipedia, CC BY-SA 4.0
Solution
We employ a two-fold strategy in our design project: simulation precedes real hardware testing. Our focus lies in creating a universal platform tailored for autonomous robotics development.
Nvidia Jetson Nano & Isaac ROS
The Nvidia robotics platform is engineered to harness accelerated computing for robot operating system 2 (ROS 2). Its reliability is underpinned by validation through Open Navigation, ensuring seamless integration with Navigation Stack 2 (Nav2).
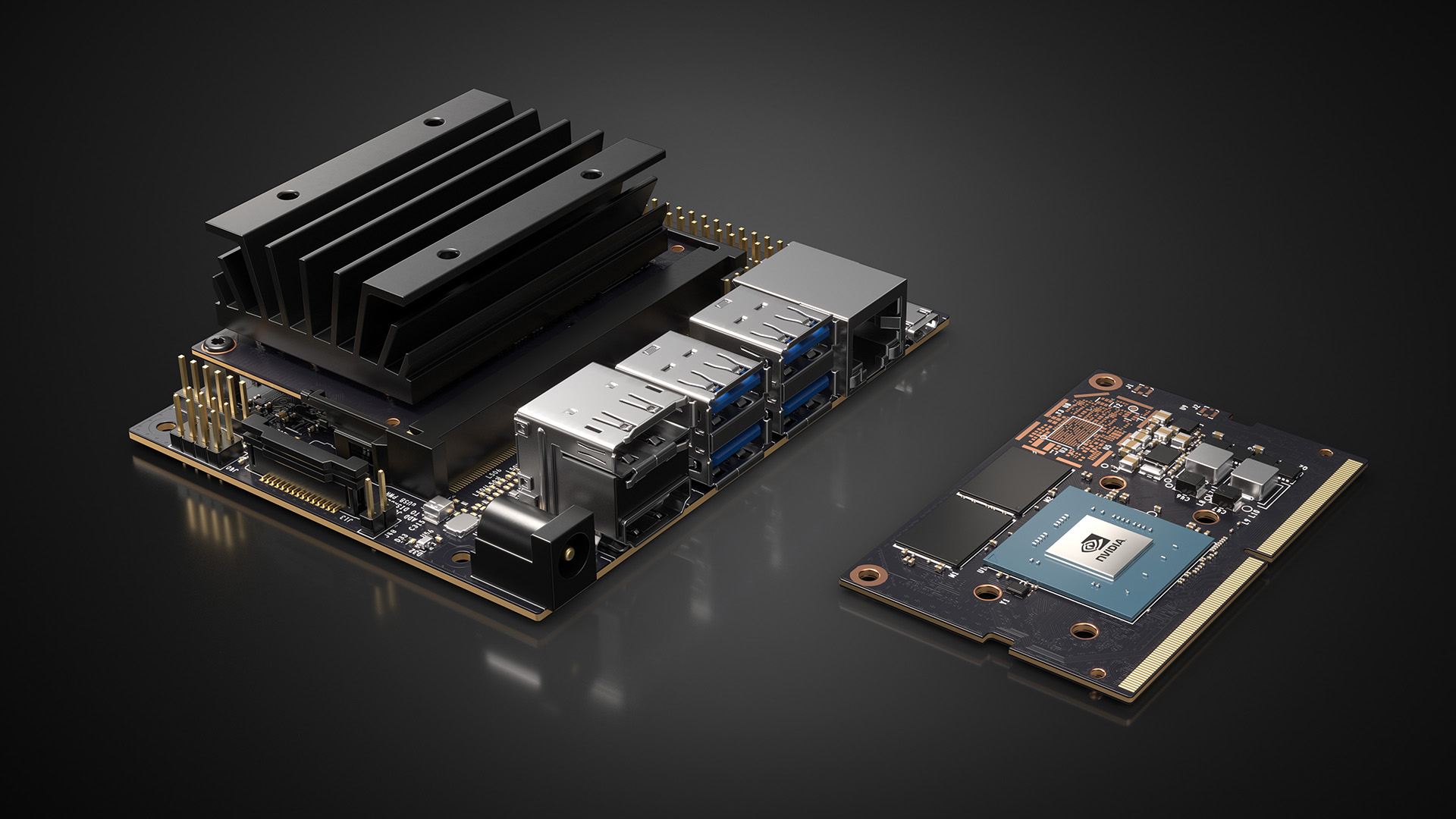
Jetson Nano Developer Kit we used to design the universal robotics platform. Source: nvidia.com
Teleoperation, environmental mapping, and navigation functions are provided by Nvidia's Isaac Robot Operating System (ROS). With these capabilities, robots navigate environments with agility and precision.
Our solution can simultaneously capture data from multiple cameras with a 100-microsecond delay from a single hardware trigger. With a recording rate of up to 4GB per second, ROSbags can capture sensor data quickly and reliably.
Hilscher netX Network Controllers
Our solution is based on the Hilscher netX controllers’ family, which provides connectivity to the industrial network and platform adaptability.
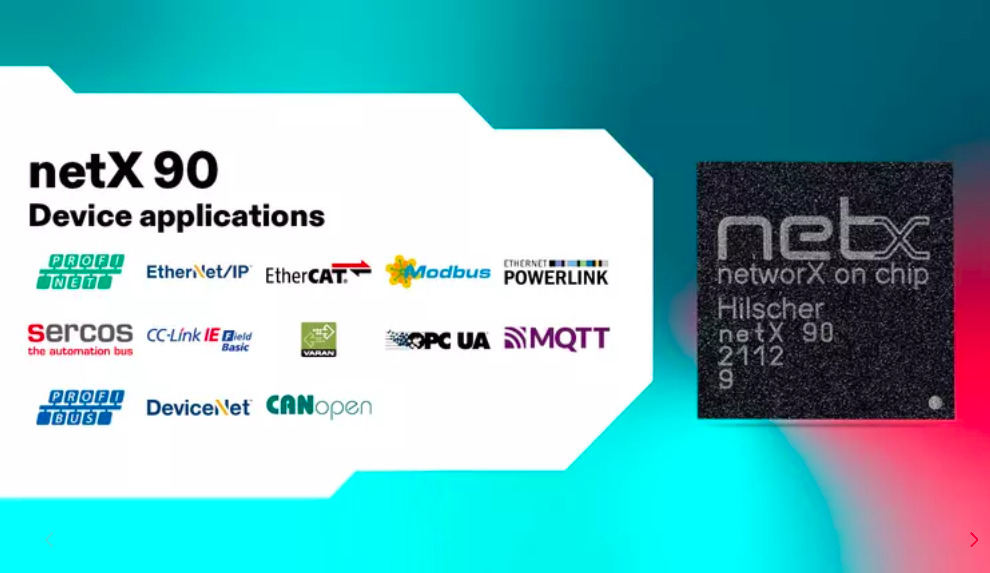
The netX network controller with all industrial communications that we integrated with our Nvidia robotics platform. Image by Hilscher
The Hilscher netX technology enables the realisation of all real-time Ethernet protocols with a single hardware solution, with the flexibility to switch communication protocols by loading different firmware, ensuring adaptability to evolving needs.
Enhanced with industrial network support, additional NVRAM or SRAM, and an extended temperature range, our platform offers a multitude of hardware options, ensuring optimal performance tailored to different robotics applications.
How the Platform Works
The universal robotics platform serves as the standardised benchmark, accommodating all real-time Ethernet and fieldbus systems for Nvidia-based automation boards.
The protocol stack operates independently on the Hilscher platform, facilitating seamless data exchange with the host through Dual-Port Memory or DMA. Thanks to the unified Hilscher platform strategy, our platform utilises consistent drivers and tools across protocols, ensuring its flexibility and adaptability.
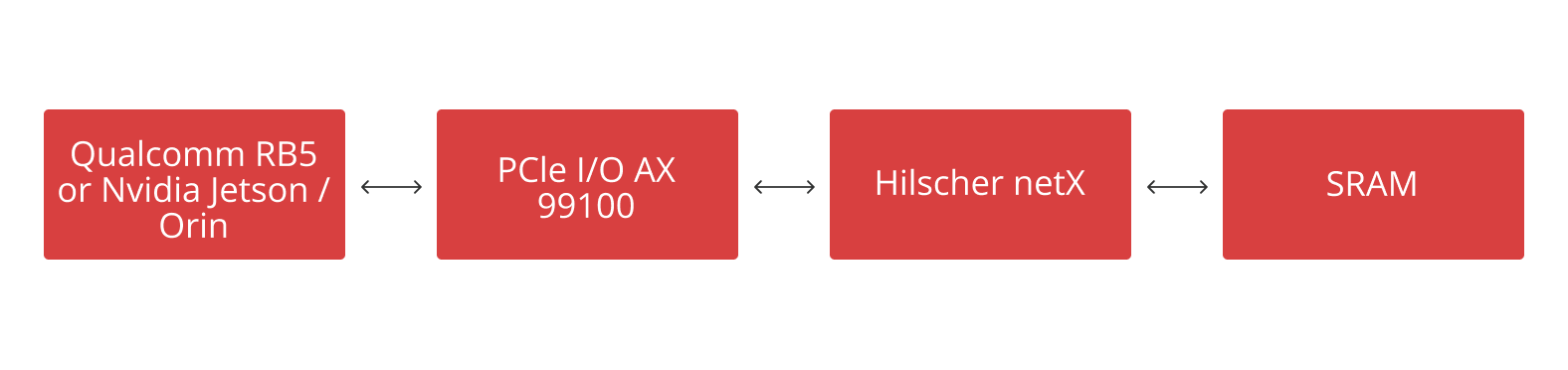
Block diagram of the universal platform for robotics by Promwad, equipped with ROS, Nvidia Jetson Nano, and Hilscher netX
The exchange of data with Nvidia Jetson/Orin is facilitated through PCIe connectivity, facilitated by the AX99100 PCIe bridge on the Hilscher part of the platform.
The carrier board boasts a range of features:
- a streamlined user interface across all protocols;
- support for universal real-time Ethernet as Master or Slave;
- simplified integration via a wide array of drivers;
- flexible data access via dual-port memory or direct memory access;
- a simple configuration is provided by assigning a unique slot number using a rotary switch.
Our solution receives data from the environment using FPD Link III cameras and LiDARs.
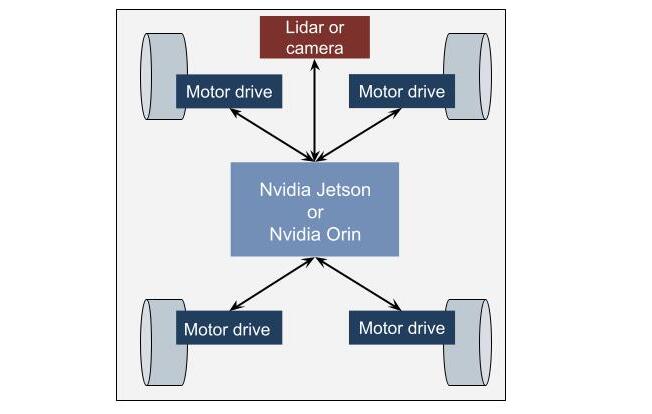
Block diagram of a mobile robot powered by Nvidia Jetson / Orin
We are now testing the solution on a mobile platform. Within this setup, each motor drive is seamlessly connected via EtherCAT and PROFINET to the main board. Our primary operating protocol is CiA 402, and we are also evaluating the effectiveness of this solution with the PROFIdrive profile.
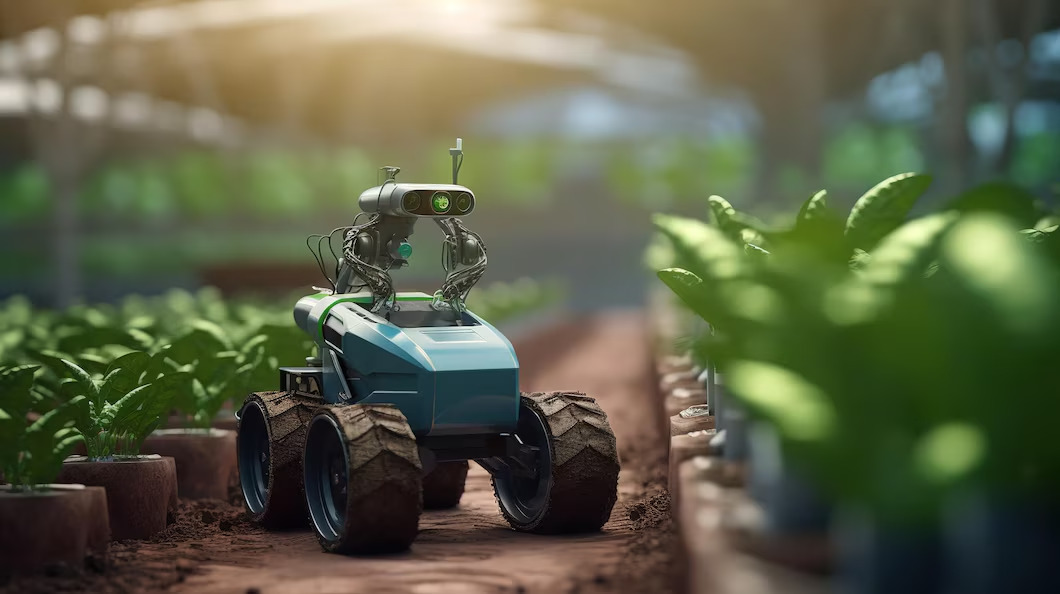
A mobile robot for greenhouses of agricultural complexes that can be based on the platform designed by Promwad and customised with robot programming software
RROS for Real-Time Task Processing
To optimise efficiency, we divided the platform into two areas based on the tasks to be performed: real-time tasks and those with less stringent real-time constraints. For real-time tasks, we implemented the Rust real-time operating system (RROS), a dual-core operating system that combines the Rust real-time kernel with a general-purpose Linux kernel.
The RROS architecture. Source: bupt-os.github.io
Here are the benefits the platform gets along with RROS:
- Hard real-time: RROS has better real-time performance than RT-Linux. This operating system contains an advanced task scheduler that reacts quickly to external events and reduces task switching and processing delays.
- Compatibility: RROS seamlessly integrates with nearly every Linux program, facilitating the smooth transition of intricate applications like TensorFlow and Kubernetes. Furthermore, it offers effortless adaptation of conventional Linux programs into real-time equivalents, enhancing versatility and flexibility.
- Easy to use: RROS simplifies the process of programming and debugging real-time applications. Leveraging the libevl interface to access real-time APIs, it enables seamless integration with debugging tools such as gdb, kgdb, and QEMU.
- Robustness: the real-time kernel of RROS is built in Rust, which increases its safety and robustness, particularly in addressing memory and concurrency concerns.
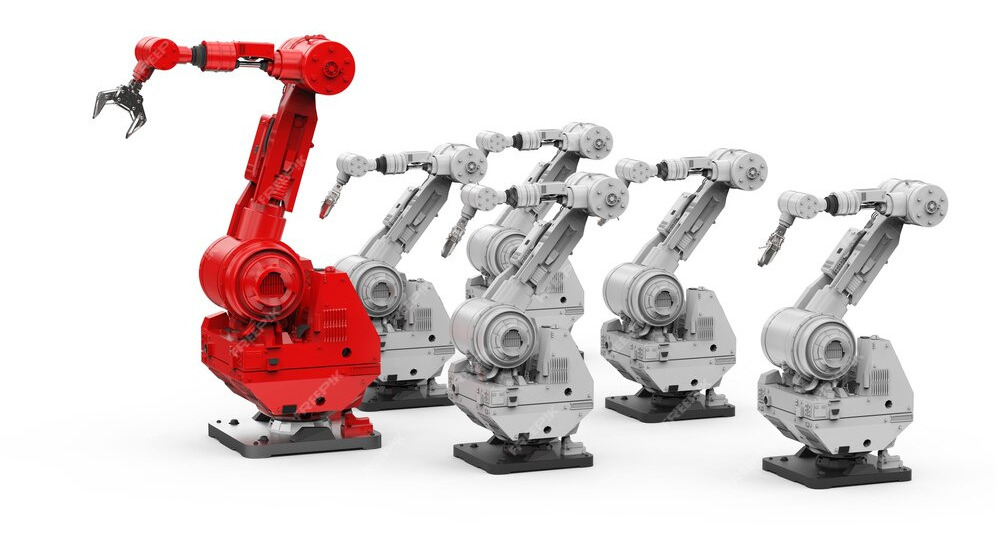
6-axis robots that used in machine assembly can be also based on the universal platform designed at Promwad
The platform retains its powerful capabilities while remaining compact and lightweight: its weight does not exceed 120 kg, even with a full payload. While the primary safety concern revolves around the potential impact of the robot itself, stringent design measures mitigate risks, ensuring that even in the event of a worst-case direct collision, harm remains moderate.
Business Value
By using our versatile platform in their robotic solutions, robot manufacturers can reap several benefits:
- Resource savings: the platform already supports industrial protocols, eliminating the need for additional integration solutions.
- Increased system reliability due to interoperability and seamless communication between different components of robotic systems.
- The versatility of the platform allows you to create a wide range of robotic systems based on a single solution, simplifying the development process.
Collaborative Opportunities
Get in touch with us, and we'll provide you with comprehensive details on three potential ways to collaborate:
- Tailoring the platform to your requirements: we'll customise the platform to fit your specific robotics solution, aligning with the needs of your industry.
- Joining the waiting list for upcoming releases: secure your place among the first to utilise our platform. With development set to conclude in 2025, signing up ensures you'll receive complete information on pricing and release dates as soon as they're ready.
- Investing in the platform development and partnering with us to introduce this groundbreaking platform to the market.
More of What We Do for Robotics
- Robotics Design Services: explore our robotics engineering profile, which covers a full range of services to design and manufacture your custom robot.
- NVIDIA for Robotics: learn about our experience with Nvidia platforms, the most popular embedded solutions for AI-powered robots.
- Work&Fun Interactive System: we developed a system with a set of unique inbuilt applications, an interactive screen and a robotic servo motor.
Media Coverage
This news story was covered by Chad Cox in Embedded Computing Design: Promwad Collaborates with Hilscher to Solve Compatibility Issues Within Robotics
This news story was covered in Robotics Tomorrow: The Compatibility Issue of Industrial Robotics Producers Finally To Be Solved