Electronic Unit for Wireless Charging Hub: Design & Manufacturing
Project in Nutshell: We designed and initiated the manufacturing of an electronic unit for a wireless charging device, carefully selecting cost-effective and high-performance components. BOM optimisation allowed our client to save up to 20% of their budget while ensuring a competitive product price without compromising on quality.
Client & Challenge
A supplier of technology for the automotive industry approached us to develop an electronic unit within a wireless charger for smartphones. The device is intended for use on compact transport modes—bicycles, scooters, and kick scooters—allowing users to charge their smartphones while on the move. In addition to the technical specifications, it was crucial for the client to optimise the cost of components as this directly impacted the profitability and competitiveness of the product.
Solution
To address this challenge, we compared and selected the necessary components, developed the hardware and embedded software, and organised the launch into mass production.
1. Hardware Development
We tackled this task by focusing on the client's main requirements: technical compliance and cost-effectiveness. For this, we examined controller options from leading manufacturers: NXP, Renesas, NuVolta, and Semtech.
Based on the technical and cost requirements, we chose the wireless power receiver P9242-R from our partner Renesas and a low-power microcontroller processor core Cortex-M0 from ARM.
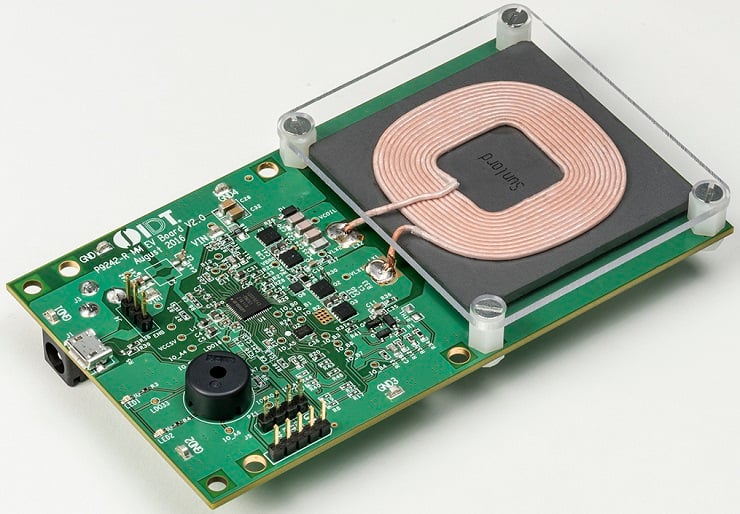
P9242-R-EVK Board from Renesas. Source: renesas.com
We also carefully selected other components, such as the wireless charging transmitter coil from Vishay, and optimised the device's enclosure for the electronic unit.
As a result, our choice of components achieved a balance between cost and performance, as well as a wide voltage input range of 4.25 to 21 V (this range is suitable for small automotive electronics and conditions with fluctuating input voltages).
2. Software Development
For firmware development, we selected a Real-Time Operating System (RTOS).
Our engineers ensured the device met the Qi power class 0 standard and provided an output power of up to 15 W. Additionally, we implemented several embedded features:
- device location detection;
- data exchange with the device about the charging current;
- transmitted power adjustment;
- shutdown at the end of charging;
- overheat protection;
- foreign object detection.
3. Manufacturing support
After developing the hardware and software components, we supported the production launch process. Our work at this stage included:
- prototype testing to check functionality and performance;
- design refinement based on feedback;
- collaboration with the client's manufacturing partner: control and consultancy support.
Our client received the first batch of low-cost wireless chargers compliant with the Qi wireless charging standard.
Business Value
By selecting cost-effective components for the design of the wireless charger, we helped our client save up to 20% in costs compared to the initial budget while maintaining a competitive pricing strategy without sacrificing quality.
More of What We Do for Charging Devices:
- Wireless EV Charging: our engineering profile on inductive charging that opens up new opportunities for fast wireless power transfer to electric vehicles.
Wireless Charging Benefits: an overview of the wireless charger market mentioning companies and products, challenges and forecasts. Switch Box Control Software: our case study on software development to redistribute power between an on-board vehicle charger and an induction charging station.