Zonal Architecture in Modern Vehicle Electronics: The Shift from Domain-Based to Zonal ECUs
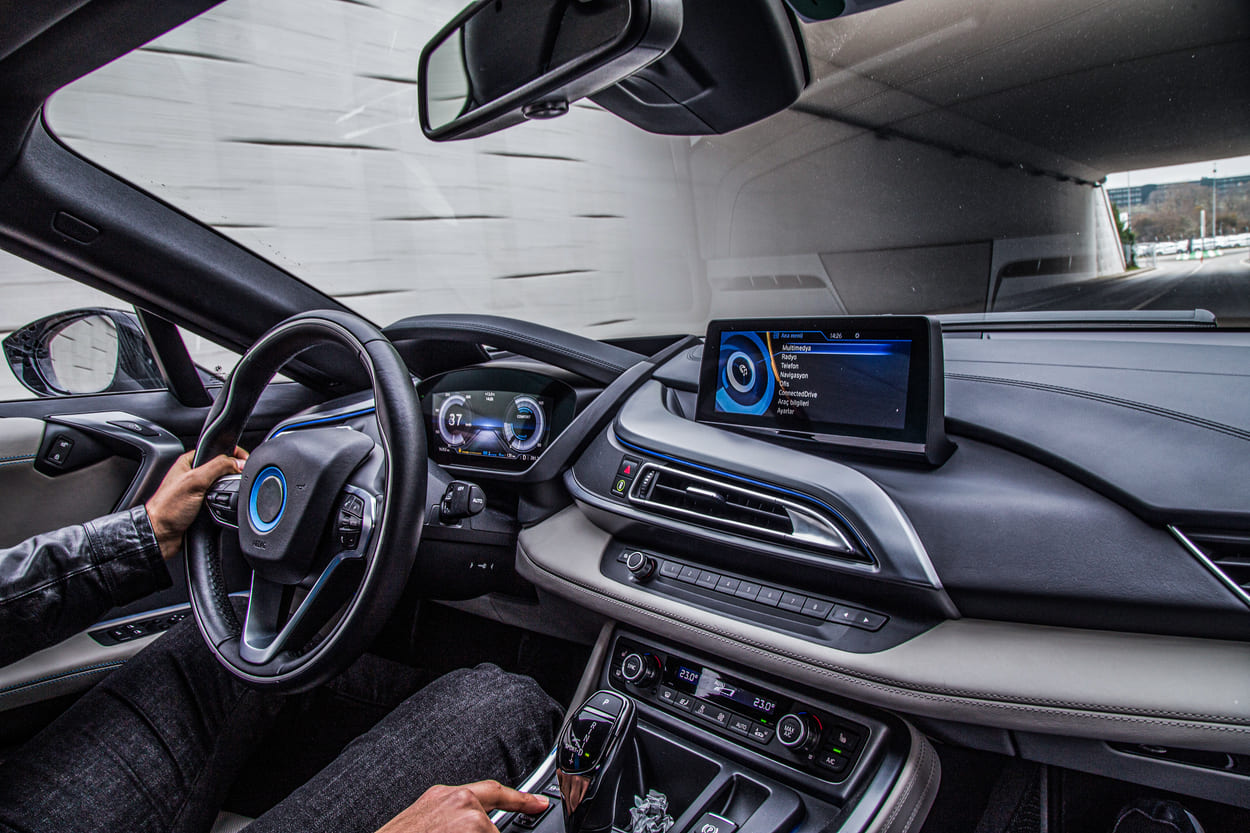
Modern vehicles are transforming from traditional mechanical machines into sophisticated, software-defined systems. With this evolution comes a need for more efficient electronic architectures. Enter zonal architecture — a concept revolutionizing the design of electrical and electronic systems in vehicles. Unlike the traditional domain-based approach, zonal architecture offers substantial benefits in wiring complexity, weight reduction, software scalability, and cost-efficiency.
This article explores what zonal architecture is, why it’s becoming a new standard, the implications for embedded development, and how it compares to legacy domain-based systems.
Understanding Vehicle E/E Architecture Evolution
Traditionally, vehicle electronic/electrical (E/E) systems have followed a domain-based architecture, where functionality is grouped by domain: powertrain, body, infotainment, chassis, and ADAS. Each domain has a central ECU (Electronic Control Unit) and communicates with sensors and actuators over separate CAN or LIN networks.
However, the growing complexity of in-vehicle functions, particularly for ADAS and autonomous driving, has driven up the number of ECUs and the weight of wiring harnesses, which now rival that of a compact passenger.
According to McKinsey, premium cars today may house over 150 ECUs and up to 5 kilometers of wiring, adding more than 50 kg to vehicle weight.
What is Zonal Architecture?
Zonal architecture restructures the vehicle's E/E system based on physical location (zone) rather than function. Each vehicle zone — front-left, rear-right, center, etc. — contains a zonal controller that manages local sensors and actuators, aggregates data, and communicates with a central vehicle computer over high-speed Ethernet.
Key Concepts:
- Zonal ECUs handle local I/O and preprocessing.
- Central computer processes complex logic (e.g., fusion, ADAS, diagnostics).
- Backbone Ethernet connects zonal ECUs with the central unit.
- Software-defined functionality moves from the periphery to the center.
This change allows for modular designs, scalability, and centralized software updates.
Zonal vs. Domain Architecture: Key Differences
Feature | Domain-Based Architecture | Zonal Architecture |
Structure | Function-oriented (e.g., infotainment, powertrain) | Location-oriented (e.g., front-left, rear-right) |
ECU Distribution | Central ECUs per domain | Local ECUs per zone |
Wiring | Point-to-point, extensive harnessing | Simplified with backbone Ethernet |
Software Deployment | Distributed across ECUs | Centralized, abstracted from hardware |
Scalability | Low, tight coupling between hardware & software | High, modular zones and central intelligence |
Benefits of Zonal Architecture
- Wiring Reduction and Weight Savings
- Up to 40% less cabling and 20-30% weight reduction.
- Simpler harnessing lowers manufacturing costs and assembly errors.
- Lower Power Consumption
- Fewer ECUs and shorter wiring reduce parasitic losses.
- Optimized power delivery paths with intelligent zonal control.
- Faster Software Updates
- OTA (over-the-air) updates via centralized management.
- Easier validation and cybersecurity compliance.
- Cost Efficiency
- Lower component count, simplified manufacturing, reduced maintenance.
- Future Readiness
- Supports software-defined vehicles, autonomous systems, and AI-driven apps.
- Supports software-defined vehicles, autonomous systems, and AI-driven apps.
Challenges in Adopting Zonal Architecture
- High Initial Investment
- Requires redesign of E/E platforms, validation cycles, and new tools.
- Legacy Integration
- Need to bridge zonal networks with legacy CAN/LIN systems during transition.
- Real-Time Constraints
- Requires deterministic communication for safety-critical applications (e.g., braking).
- Security and Functional Safety
- Centralized systems increase risk; must enforce strong security models (e.g., Zero Trust).
- Standardization
- Still an evolving field; OEMs like VW, GM, and BMW are driving their own standards.
- Still an evolving field; OEMs like VW, GM, and BMW are driving their own standards.
Implications for Embedded Development
The shift to zonal architecture significantly impacts both embedded hardware and software engineering:
Hardware:
- Design of modular, multi-functional zonal ECUs.
- Use of automotive-grade microcontrollers (e.g., NXP S32Z/E, TI Jacinto, Infineon AURIX).
- Integration of Ethernet TSN, CAN-FD, and LIN in a single board.
- Redundancy and isolation for safety compliance (ASIL-B/D).
Software:
- Centralized logic with middleware abstraction layers (AUTOSAR Adaptive, ROS2).
- Real-time operating systems (RTOS) for zonal ECUs.
- Increased reliance on containerization, hypervisors, and microservices.
- Centralized diagnostics, OTA infrastructure, cybersecurity agents.
Real-World Examples
- Volkswagen SSP Platform: SSP (Scalable Systems Platform) will adopt full zonal architecture by 2026, reducing ECUs by over 50% and wiring by 40%.
- GM Ultifi Software Platform: Combines zonal hardware with centralized vehicle OS and OTA delivery.
- Tesla Model Y: Already integrates zonal principles with fewer ECUs and central computing modules.
- Mercedes-Benz MB.OS: Centralized software stack compatible with zonal hardware to enable personalized driver experiences and ADAS updates.
Zonal ECUs: Key Design Considerations
Component | Considerations |
MCU/SoC | High-speed processing, ASIL-compliant, Ethernet + CAN support |
Network Interfaces | Ethernet TSN, CAN-FD, LIN |
Memory | Flash for OTA, secure boot, HSM support |
I/O | GPIO, ADC/DAC, PWM for local sensors & actuators |
Power Management | Intelligent power gating, isolation, load balancing |
Security | Secure boot, secure storage, firewalls, anomaly detection |
Software Stack Alignment
- AUTOSAR Adaptive Platform for central units
- Classic AUTOSAR or custom RTOS for zonal ECUs
- DoIP (Diagnostics over IP) for in-vehicle diagnostics
- TLS, MACsec, and IPsec for secure communications
Market Outlook & Industry Trends
According to IHS Markit, the zonal ECU market is expected to reach $12 billion by 2030, driven by electric vehicle demand and software-defined vehicle strategies.
Key Drivers:
- Electric vehicle electrification
- Cloud-integrated vehicle functions
- Simplified service & maintenance
- AI and edge analytics at the zone level
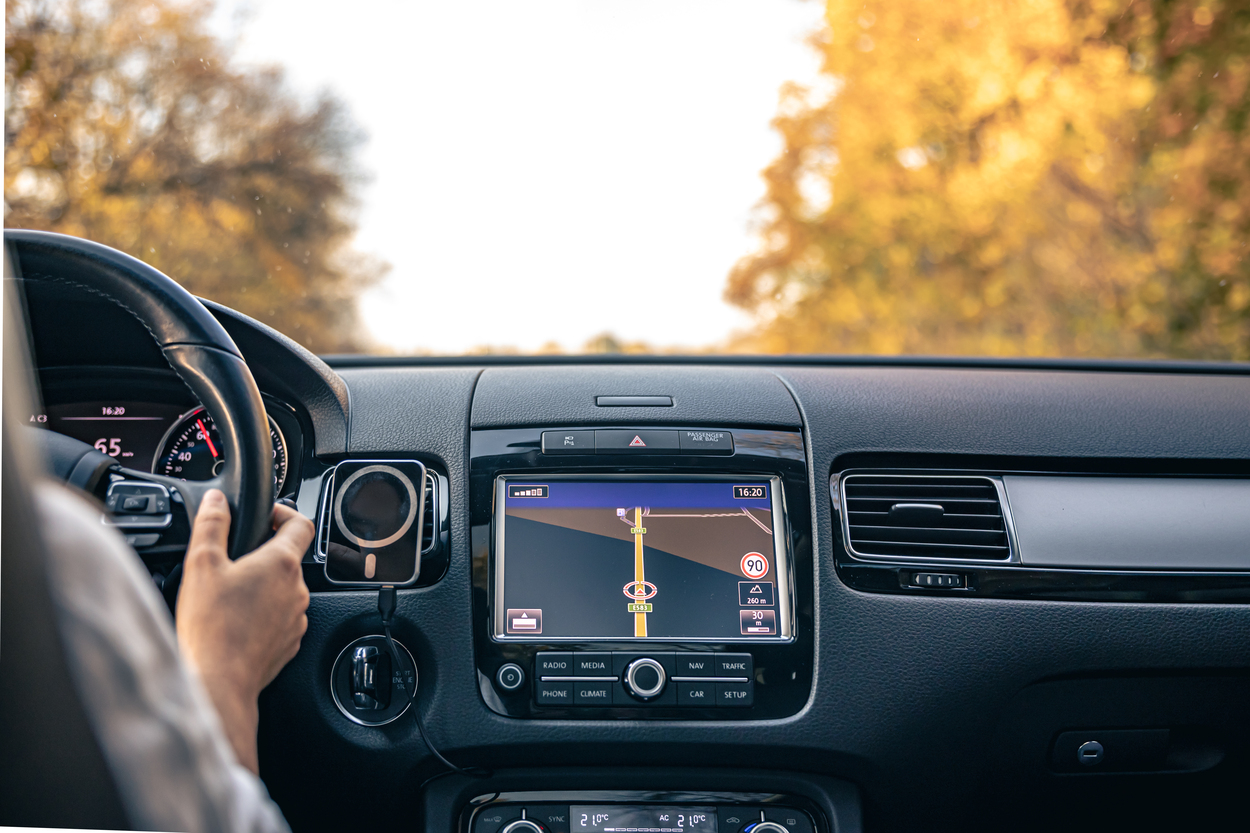
How Promwad Can Help
At Promwad, we support automotive clients transitioning to zonal architecture with:
- Custom ECU design for zonal and central computing platforms
- Integration of Ethernet TSN, AUTOSAR, and cybersecurity features
- Prototyping and compliance with ISO 26262 and ASPICE standards
- Firmware development and OTA infrastructure setup
Our engineering expertise enables automotive Tier 1s and OEMs to build next-generation vehicle architectures that are scalable, safe, and future-ready.
Conclusion
Zonal architecture is no longer a futuristic concept; it's becoming a core component of modern vehicle design. As the automotive industry shifts toward electrification, autonomy, and connectivity, zonal architecture offers the modularity and efficiency needed to scale and evolve.
For embedded developers and vehicle architects, this means rethinking ECU placement, system partitioning, and software design. Promwad is here to guide this transformation with deep engineering knowledge and hands-on experience in automotive innovation.